ERW pipes are produced from hot-rolled or cold-rolled flat coils according to ASTM A 513 specifications; Drawn Over Mandrel (DOM) tubes are produced from fully annealed ERW pipes through a cold drawing process.
1. Selection of internal high-pressure formed ERW pipes
ERW pipe is produced from hot-rolled or cold-rolled flat coils according to ASTM A 513 specifications; in order to achieve hydroformed surface quality, the coils should be free of scale, pickled and oiled.
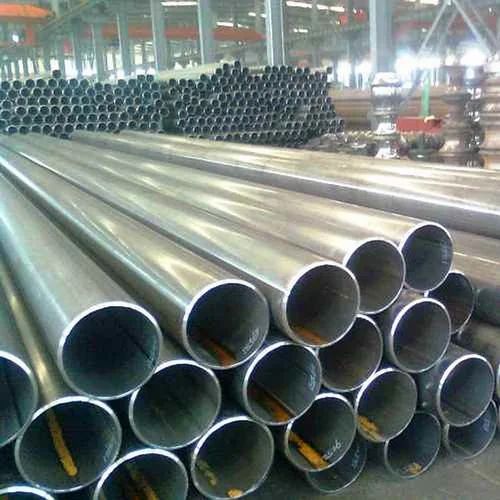
On the pipe rolling mill, the steel coil is cut to a certain size, and then the plate is fed into several forming rollers, welding stations, final sizes, and then cut to a certain length in a continuous high-speed process, as shown in Fingure 9-1.
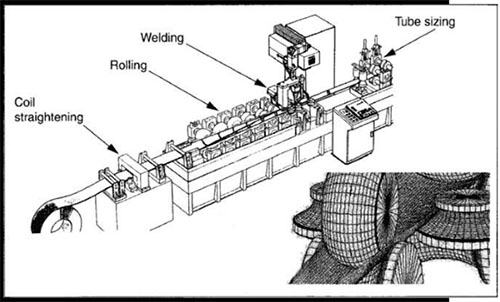
Fingure 9-1
To facilitate uninterrupted production and achieve consistent quality, many coil ends are welded together; ERW pipe rolling mill speeds typically range from 150 to 500 ft/min (46 to 152 m/min).
There are various layouts for the tube roll forming stage, with some older mills using fewer roll sets, often more aggressively in hardening the material.
However, most modern rolling mills are designed to better control strain hardening during the forming phase, using gentler forming methods.
A typical cross-section of a tube during roll forming is shown in Fingure 9-2.
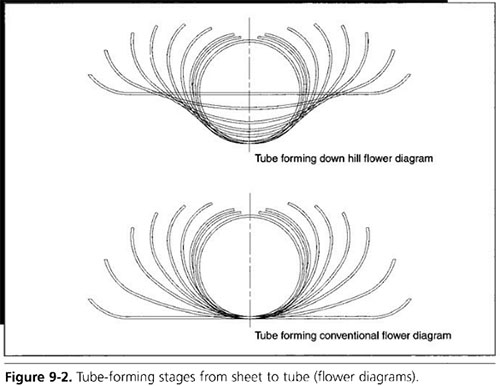
The pattern showing the forming stages from sheet to round tube is called a forming pattern, and the degree of strain hardening during tube rolling depends largely on the pattern used.
Tensile testing of specimens cut from different positions in the longitudinal direction and circumference of the pipe usually shows varying degrees of strain hardening. Figure 9-4 shows the three positions described in Figure 9-3 (the welding position, 90 degrees from the weld). degree, 180 degrees to the weld) tensile test results.
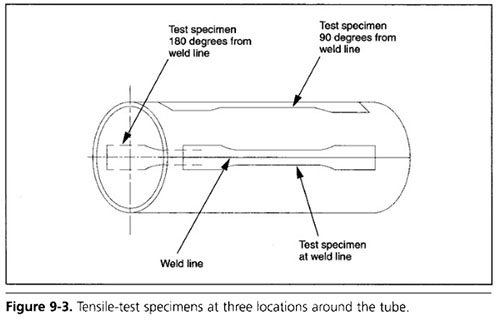
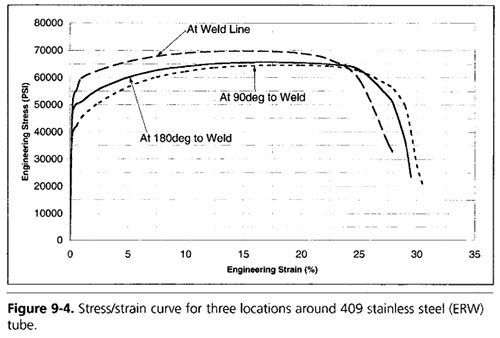
The results vary significantly, with changes in performance depending on the mill design and setup parameters. Figure 9-5 shows a comparison of the yield stress of sheet metal and pipe.
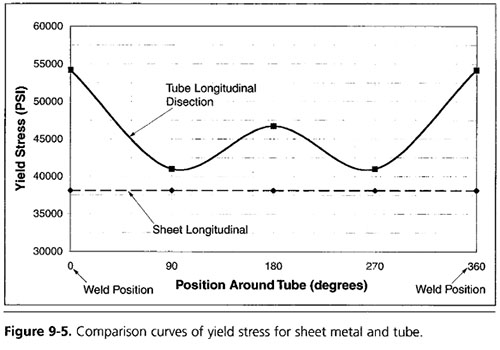
Please note that the yield stress of the pipe is high and varies greatly around it. Also note the W-shape of the pipe curve. For an ideal internal high-pressure formed pipe, the height of w should be minimized so that its position is close to the sheet material line. After the forming stage, the pipe enters the welding station.
To obtain a high-quality weld, the edges of the steel strip are resistively heated and pressed together using a set of special rollers. This butt welding method does not require any additional filler material. During the welding process, a certain amount of molten iron will protrude from the inside and outside of the pipe surface.
This is called welding flash and is usually removed immediately after a welding operation using a form tool. For most hydroforming applications, flash is removed or "scarred" from both surfaces.
In some applications, where the internal weld flash may be rolled or height-controlled to a specific size, laser welding may be used instead of resistance welding.
Laser welding is generally of higher quality than resistance welding, and for laser welded pipe components that require very high expansion rates, where the heat affected zone around the weld is significantly lower, there are often benefits to using laser welded pipe.
However, rolling speeds are limited to laser welding speeds, which range from 30 to 50 ft/min (10 to 15 m/min). After the welding phase, the pipe is allowed to cool before entering the sizing station.
Until now, the diameter of steel pipes has usually been slightly larger, with the focus being on welding quality and high forming speeds. At the sizing station, the size, diameter and ovality of the pipe have reached the required tolerances.
For tubes to be hydroformed, diameter reduction at this stage should be kept to a minimum to maintain the formability of the material. ERW pipe is typically available in diameters from 0.5 to 12.5 inches (12.7 to 317.5 mm) and with wall thickness factors from 5 to 100.Laser welded pipes can reach 125 WF. As wall factors increase, it becomes increasingly difficult and costly to produce oil pipes using this technology.
2. Selection of internal high-pressure forming core-pulling tubes
Drawn Over Mandrel (DOM) tubes are produced by a cold drawing process from fully annealed ERW tubes; the tube sheet is drawn through a mold with or without a mandrel inside the mold.
The tubes with mandrels inside are of very precise dimensions and have uniform material properties. After the cold drawing operation, the tubes are normalized or annealed to the required mechanical properties; DOM tubes are available in diameters from 0.375 to 12.5 inches (9.53 to 317.5 mm) and wall thicknesses Factors range from 10 to 50.
1. Selection of internal high-pressure formed ERW pipes
ERW pipe is produced from hot-rolled or cold-rolled flat coils according to ASTM A 513 specifications; in order to achieve hydroformed surface quality, the coils should be free of scale, pickled and oiled.
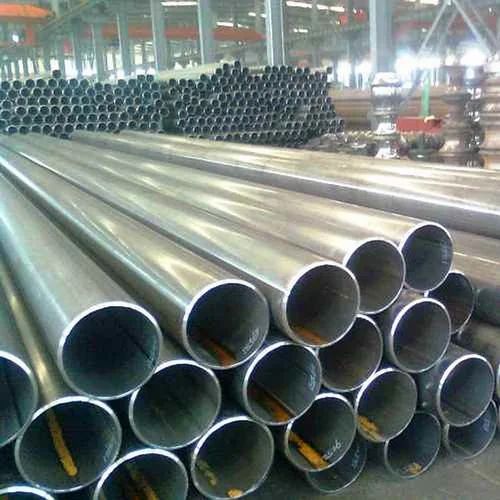
On the pipe rolling mill, the steel coil is cut to a certain size, and then the plate is fed into several forming rollers, welding stations, final sizes, and then cut to a certain length in a continuous high-speed process, as shown in Fingure 9-1.
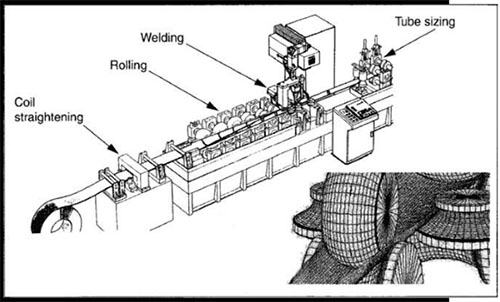
Fingure 9-1
To facilitate uninterrupted production and achieve consistent quality, many coil ends are welded together; ERW pipe rolling mill speeds typically range from 150 to 500 ft/min (46 to 152 m/min).
There are various layouts for the tube roll forming stage, with some older mills using fewer roll sets, often more aggressively in hardening the material.
However, most modern rolling mills are designed to better control strain hardening during the forming phase, using gentler forming methods.
A typical cross-section of a tube during roll forming is shown in Fingure 9-2.
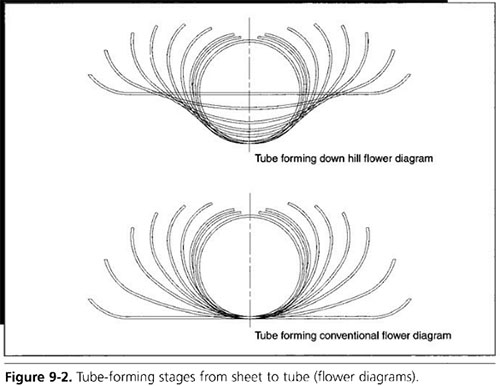
The pattern showing the forming stages from sheet to round tube is called a forming pattern, and the degree of strain hardening during tube rolling depends largely on the pattern used.
Tensile testing of specimens cut from different positions in the longitudinal direction and circumference of the pipe usually shows varying degrees of strain hardening. Figure 9-4 shows the three positions described in Figure 9-3 (the welding position, 90 degrees from the weld). degree, 180 degrees to the weld) tensile test results.
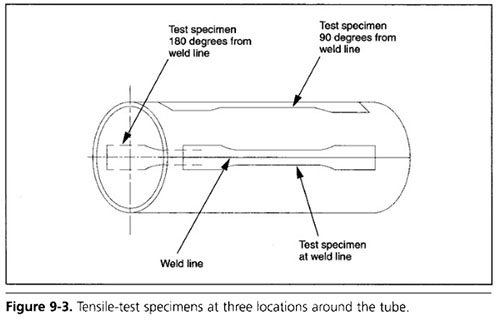
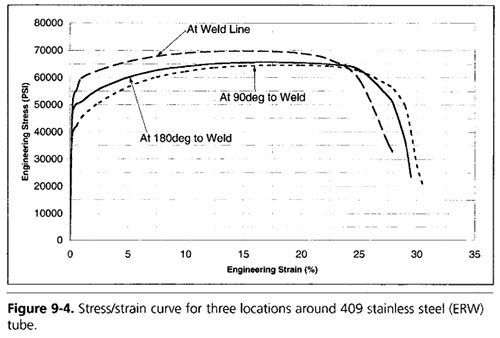
The results vary significantly, with changes in performance depending on the mill design and setup parameters. Figure 9-5 shows a comparison of the yield stress of sheet metal and pipe.
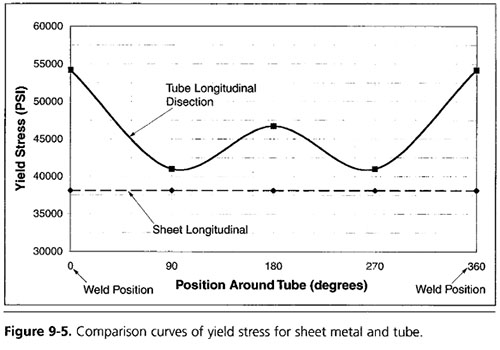
Please note that the yield stress of the pipe is high and varies greatly around it. Also note the W-shape of the pipe curve. For an ideal internal high-pressure formed pipe, the height of w should be minimized so that its position is close to the sheet material line. After the forming stage, the pipe enters the welding station.
To obtain a high-quality weld, the edges of the steel strip are resistively heated and pressed together using a set of special rollers. This butt welding method does not require any additional filler material. During the welding process, a certain amount of molten iron will protrude from the inside and outside of the pipe surface.
This is called welding flash and is usually removed immediately after a welding operation using a form tool. For most hydroforming applications, flash is removed or "scarred" from both surfaces.
In some applications, where the internal weld flash may be rolled or height-controlled to a specific size, laser welding may be used instead of resistance welding.
Laser welding is generally of higher quality than resistance welding, and for laser welded pipe components that require very high expansion rates, where the heat affected zone around the weld is significantly lower, there are often benefits to using laser welded pipe.
However, rolling speeds are limited to laser welding speeds, which range from 30 to 50 ft/min (10 to 15 m/min). After the welding phase, the pipe is allowed to cool before entering the sizing station.
Until now, the diameter of steel pipes has usually been slightly larger, with the focus being on welding quality and high forming speeds. At the sizing station, the size, diameter and ovality of the pipe have reached the required tolerances.
For tubes to be hydroformed, diameter reduction at this stage should be kept to a minimum to maintain the formability of the material. ERW pipe is typically available in diameters from 0.5 to 12.5 inches (12.7 to 317.5 mm) and with wall thickness factors from 5 to 100.Laser welded pipes can reach 125 WF. As wall factors increase, it becomes increasingly difficult and costly to produce oil pipes using this technology.
2. Selection of internal high-pressure forming core-pulling tubes
Drawn Over Mandrel (DOM) tubes are produced by a cold drawing process from fully annealed ERW tubes; the tube sheet is drawn through a mold with or without a mandrel inside the mold.
The tubes with mandrels inside are of very precise dimensions and have uniform material properties. After the cold drawing operation, the tubes are normalized or annealed to the required mechanical properties; DOM tubes are available in diameters from 0.375 to 12.5 inches (9.53 to 317.5 mm) and wall thicknesses Factors range from 10 to 50.