1. What is automotive steel sheet?
Carbon steel used for automotive body components can generally be divided into two categories:(1) Carbon steel with low carbon content and good plasticity, such as galvanized steel sheets. Components such as the fender, engine hood, trunk lid, and body side panels of the car body are made from this type of material.
(2)High-strength steel, which is used to manufacture internal panels and reinforcement plates of the car body.The functions of car body steel sheets include deep drawing performance, paint adhesion performance, bending performance, and rust prevention performance.
Thanks to technological advancements, especially after the 1990s, the application of laser texturing technology has greatly improved the deep drawing performance of steel sheets, making it possible to produce more aesthetically pleasing car bodies and also making the use of thinner steel sheets possible. The application of laser texturing technology has greatly improved the paint adhesion performance, making the car body more beautiful and durable.
The application of galvanized steel sheets, due to the principle of electrochemistry, significantly improves the lifespan of the steel sheets.
The bending performance of steel sheets requires a detailed explanation. According to common thinking, the thicker the steel sheet, the safer it is, but this is not the case. When a vehicle is hit, is it to protect the car or the person first? Thicker steel sheets are not easy to deform, and the impact energy is transferred to the personnel. Thinner steel sheets, when hit by energy, crumple and deform to absorb energy, so that as little energy as possible is transferred to the personnel.
Modern car design, the car body steel sheet is developing towards the direction of being thin. In the 1980s, it was more than 1MM, in the 1990s, it was 1-0.8MM, and now it is 0.8-0.6MM. In the past, the thick steel sheet of the car body also had the function of increasing the car's own weight, making the driving stable. Now it is considering increasing the weight of the chassis to make the center of gravity lower. For safety, the engine suspension is adopted in the design. When impacted, the steel sheet crumples and absorbs energy, and the engine decouples and falls to the ground. At the same time, anti-collision steel bars are installed inside to prevent external objects from injuring personnel when the steel sheet is punctured.
So do not judge the car and safety by the thickness of the steel sheet. FD, WL are thin steel sheets, and they have all passed the most stringent three-level safety tests. A whole car uses different steel materials and processes in different parts, including BP steel, BH steel, DP steel, BLa steel, TRIP steel, etc.
2. Types of automotive steel sheets
Boiling steel: 05F, 08F, 10F, 15F, 20F stamping parts, structural partsKilled steel: 05, 08, 10, 15, 20 stamping parts, structural parts
Special steel: 08Mn, 16Mn, 06Ti, 10Ti special for beams
Low carbon steel (ST) DC01, DC03, DC04, DC05, DC06 stamping parts
Stamping: BLC, BLD, BUSD, BUFD, BSUFD stamping parts
High strength: BP, BH, BLa, DP, TRIP stamping parts, structural parts
Hot rolled steel: SAPH (310, 370, 400, 440) structural parts
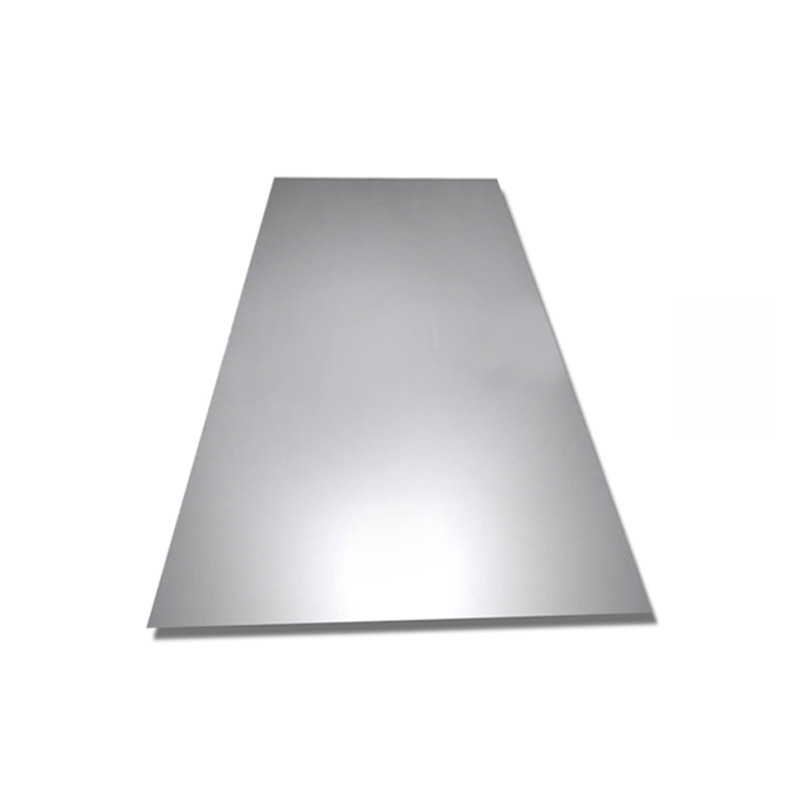
3. Ordinary low carbon steel sheet
At present, the most widely used in car production is ordinary low carbon steel sheet.Low carbon steel sheet has good plastic processing performance, strength and stiffness can also meet the requirements of the car body, but also can meet the requirements of the car body spot welding, so it is widely used in the car body.In order to meet the automotive industry's pursuit of lightweight requirements, steel enterprises have introduced a series of high-strength automotive steel plates. This high-strength steel plate is obtained by strengthening methods on the basis of low carbon steel plate, and the tensile strength has been greatly enhanced.
Using high-strength characteristics, it is still possible to maintain the mechanical performance requirements of the car body while thinning the thickness, thereby reducing the weight of the car. For example, BH steel plate is made by stamping molding, then baking paint processing heat treatment to improve its tensile strength. In contrast, the steel plate with a strength of 440MPa produced in the past can be increased to 500MPa after adopting this processing technology. Originally, the side panel was made with a thickness of 1 millimeter of steel plate, and the high-strength steel plate only needs a thickness of 0.8 millimeters.
The use of high-strength steel plates can also effectively improve the impact resistance of the car body, prevent dents caused by flying sand and stones on the road during driving, and extend the service life of the car.
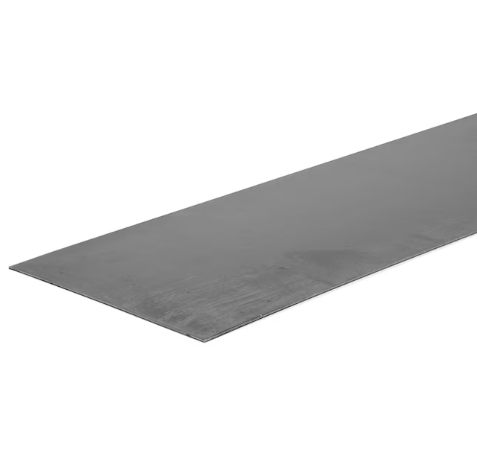
4. High-strength steel plates
The high-strength steel plates in the past, although the drawing strength is higher than that of low carbon steel plates, the elongation rate is only 50% of the latter, so they are only suitable for parts with simple shapes and small drawing depth.The current high-strength steel plates are made by adding appropriate trace elements to low carbon steel and rolling them through various treatments, with a tensile strength as high as 420N/mm2, which is 2 to 3 times that of ordinary low carbon steel plates.
Automotive high-strength steel plates should have the characteristics of high strength and good plasticity. At present, high-strength steels include BH steel (baked paint hardening steel), dual-phase DP steel, phase transformation induced plasticity steel (TRIP), micro-alloyed M steel, high-strength interstitial-free IF steel, etc.
They are generally used for parts that require high strength, high collision energy absorption, and strict forming requirements, such as wheels, reinforcement components, bumpers, and anti-collision bars. With the advancement of performance and forming technology, high-strength steel plates have been used for the inner and outer panels of cars, such as roof panels, door inner and outer panels, engine hoods, and trunk lids. Many mid-to-high-end cars now use high-strength steel plates.
High-strength steel plates have been developed and produced by developed countries for more than 20 years, and most of them have standardized and regular production series of products, and are widely used in the production of many car components.
The average usage rate of high-strength steel plates for Japanese cars was 25% in 1993 and 36% in 2000. The American Iron and Steel Institute (AISI) organized 13 steel companies worldwide to research and develop the "Ultra Light Steel Auto Body Research" (ULSAB), and in March 1998, they exhibited a high-strength steel body in Michigan, USA, which used about 86% high-strength steel, and its average weight was reduced by 25% compared to ordinary steel structure bodies, which is very attractive to car manufacturers.
Phosphorus-added high-strength steel refers to the addition of a certain amount of phosphorus to low carbon steel and ultra-low carbon steel, using the solid solution strengthening effect of phosphorus to improve the strength of steel. The use of this steel plate can appropriately reduce the thickness of car stamping parts, reduce the self-weight of the car, and obtain good economic benefits. It can be used to make outer panels, engine hoods, roof covers, etc., and can also be used to make reinforcement parts and structural parts such as beams and beams.
Baking hard high-strength steel refers to the use of specific chemical components and production processes to make the steel plate contain a certain amount of carbon atoms, and the steel plate has a lower yield strength in the delivery state, and the yield strength increases after stamping molding and painting baking. It is a high-efficiency steel used for cars. It can improve the anti-dent performance of the car's outer panel while maintaining good forming performance. It is widely used on the outer panels of car doors, engine hoods, and other outer coverings.
Dual-phase high-strength steel is a phase transformation strengthening high-strength steel, which has a low yield strength ratio, no yield extension, a high strain strengthening index, and good collision performance, and can achieve weight reduction while improving safety. It is an advanced high-strength steel that has been developed in recent years and has been used in large quantities in developed countries in the automotive industry. It is mainly used for car wheels, bumpers, suspension systems, and reinforcement parts, and can also be used for the inner and outer panels of cars.
Low-alloy high-strength steel is added with a small amount of niobium and/or titanium alloy elements in low carbon steel, which form carbides and nitrides with carbon, nitrogen, and other elements and precipitate on the ferrite to improve the strength of steel. This steel plate has good formability and higher strength, mainly used for structural parts such as car seats and beams.
Phase transformation induced plasticity steel (TRIP700 formability is equivalent to ST14) is mainly used for high-strength, complex forming parts, such as crumple zones, A-pillar, B-pillar, floor beams, cross beams, etc. See Figure 5 for the development and use forecast of high-strength steel in Japan before 2014.
5.Galvanized thin steel plate
Galvanized thin steel plates are widely used in cars because of their good corrosion resistance.In the early years, people found in experiments that when iron and zinc are placed in salt water, and there is no connection between the two, both iron and zinc will rust, iron produces red rust, and zinc produces "white rust"; if there is a connection between the two, iron will not rust and zinc produces "white rust", and zinc protects iron. This phenomenon is called sacrificial anode protection.
After research, when the galvanized amount is 350 grams per square meter (single-sided), the service life of galvanized steel plates outdoors (red rust) is about 15-18 years in rural areas and about 3-5 years in industrial areas, which is several times or even more than ten times longer than ordinary steel plates.
Since the 1970s, car body steel plates have used galvanized thin steel plates, and during assembly, the galvanized side is placed on the inside of the car to improve the corrosion resistance of the car body, and the non-galvanized side is placed on the outside of the car for painting.
To meet the various requirements of cars for galvanized steel plates, some manufacturers carry out special treatments such as diffusion annealing on the galvanizing production line to form a "zinc-iron" alloy coating on the surface of the steel plate. Its characteristic is that the welding and corrosion resistance after painting are better than pure zinc-coated plates. Later, there were also alloy hot-dip galvanized steel plates such as "zinc-aluminum-silicon" and "zinc-aluminum-rhenium", which greatly improved the corrosion resistance of hot-dip galvanized steel plates and the binding performance with paint is stable for a long time.
At present, cars have widely used galvanized steel plates, with galvanized steel plate thickness ranging from 0.5 to 3.0 millimeters, of which the body covering parts mostly use galvanized steel plates of 0.6 to 0.8 millimeters.
The body parts of German Audi cars are mostly made of galvanized steel plates (some use aluminum alloy plates), more than 80% of the steel plates used by American Buick cars are double-sided hot-dip galvanized steel plates, and the outer covering parts of Shanghai Passat cars use electro-galvanizing process, and the inner covering parts use hot-dip galvanizing process, which can make the car body anti-rust warranty period up to 11 years.
Materials are an important factor affecting the quality of cars. In modern cars, body materials account for a large part of the whole car materials. In order to improve the economy of car driving, reducing the weight of the car is the goal of major car manufacturers around the world, and in recent years, more and more aluminum or plastic and other non-steel materials have been used to make body parts, such as Audi A2 all-aluminum body, Nissan SUV "Qijun" using plastic for the front fender, and more passenger car bumpers are made of plastic.
In the situation where non-steel materials are increasingly used to make body parts, steel enterprises that are highly dependent on the automotive industry will face a direct threat. Therefore, the research and development of lightweight, high-strength automotive steel plates have become a hot topic for steel enterprises for many years.
6.Hot-formed steel plate
The strength of a car body depends on the design of the car body and the strength of the steel plate, so the strength of the steel plate in important protective parts of the car body is very important, and hot-formed steel plate is undoubtedly the best among all kinds of high-strength plates.Hot-formed steel plate technology refers to the steel plate after 950°C high-temperature heating, one-time forming, and then quickly cooling, which comprehensively improves the strength of the steel plate, with a yield of up to 1000Mpa, each square centimeter can withstand more than 10 tons of pressure, using this material on the car body, in the case of almost no change in the weight of the car body, the bearing capacity is increased by 30%, making the car's rigidity reach a new level, and in the European NCAP collision test to achieve a five-star standard.
7.Spot welding steel plate
In recent years, a "spot welding" technology has become popular, which is a steel plate made by cutting and spot welding steel plates of different thicknesses and different properties, and this spot welding steel plate can be stamped and processed.Using spot welding steel plates can correspond to different plates according to different parts of the car, and better play its role, such as using thicker high-strength steel plates in places with high load, and using thinner high-strength steel plates in other parts.
The application of spot welding steel plates simplifies the production process, improves the performance of components, and reduces weight. The parts on the car components that use "spot welding" are often side frames, inner door panels, car bottom plates, side crossbars, windshield window frames, central pillars, etc. Therefore, there are also high requirements for the welding of high-strength steel plates.
Coating is an important process in the car manufacturing process, including galvanized steel plates.
At present, the white body of mid-to-high-end cars generally uses galvanized plates, and galvanized plates can ensure that the car body will not rust for 10 years. However, the surface roughness and cleanliness of the car steel plates produced by steel mills during the rolling process will directly affect the adhesion of the zinc layer of galvanizing.
At the same time, the control of the steel plate thickness accuracy will also affect the accuracy of the modern car production line, because the modern car production line is spot welding with robots, and the large thickness error of the plate will lead to virtual welding.
Note: The car body skin plate, door, roof, bottom plate and other covering parts are all cold-rolled plates, and the main beam, beam, bumper and other parts are hot-rolled plates.
8.Car body steel plate safety
In fact, the thickness of the car body steel plate is not the only determining factor for the safety of the vehicle. To measure the safety of a car, there are mainly two aspects, one is the rigidity of the car body, and the other is the absorption of energy.The rigidity of the car body includes the overall rigidity of the car body and chassis, the handling rigidity of the car body and other indicators. Maybe you have such a feeling, some vehicles have a feeling of falling apart when driving at high speed, and you must hold the steering wheel firmly with both hands. This is because the impact of the road surface, air resistance and other factors will cause the car body to deform, thereby affecting the control of the vehicle. A good car body must have high rigidity and not easy to deform.
The second aspect of safety is collision safety. At present, the European NCAP new car impact test represents the world's most stringent collision safety standards. It not only requires the car body to effectively absorb the energy generated during the collision when it occurs in the front, side, front offset collision, and rollover, etc., to maximize the protection of the personnel in the car from injury and no injury, but also has a more humanized indicator, which is the protection of pedestrians.
To meet the above requirements, different car manufacturers have different solutions and have formed different design styles. European and American cars, especially German cars, are integrated into the rigorous and excellent style of the Germans in the design concept, and at the same time, to adapt to the requirements of many roads in Germany with unlimited speed, the thickness and strength of the car body steel plates are relatively high, and the vehicle's own weight is larger, therefore, it also brings higher overall rigidity and stability when driving at high speed.
Japanese and Korean cars focus on the economy and agility of the vehicle in the design, the car body steel plates are thin, the self-weight is lighter, although the economy is fuel-efficient, and the power is not inferior, but the stability when driving at high speed is worse than that of German cars. However, in various safety collision experiments, both European and American and Japanese and Korean cars have scored high.
So, why do cars with thin steel plates easily give people an impression of being unsafe? This still has to be attributed to the differences in the concept of collision safety. German cars with thicker steel plates, when a collision occurs, the deformation of the whole car is relatively small, and minor collisions in daily life are often unharmed, but when the collision energy reaches a certain level, the energy-absorbing area begins to work to protect the safety of the passenger compartment.
Japanese and Korean cars have thinner steel plates and often use composite car bodies, and they have worked hard on energy absorption. For example, the rigidity of the front engine compartment and the rear trunk is appropriately reduced, and when impacted, the front and rear will absorb the impact force to avoid being transmitted to the passenger compartment, and the result is naturally that the car body is a mess.
It seems that judging the safety of the car by who has thicker steel plates, stronger resistance to smashing, and less damage in the collision is still not comprehensive enough. However, the higher safety of German cars has formed a reputation in the industry and in the minds of consumers after all, and consumers still need to make comprehensive judgments when choosing.
Previous:ASTM A333 vs A106 Seamless Pipe
Next:Advantages of H-pile