The ERW pipe forming unit originally adopted the chain drawing method. Later, the United States created roll forming. The structure of the initial roll forming device is a cross arrangement of flat rolls and vertical rolls, which is mainly used to produce small-diameter ERW welded pipes. After continuous improvement, the forming arrangement changed to the form of flat, vertical roller + vertical roller group, the pipe diameter developed from small diameter to medium diameter, and high-frequency welding was adopted, which is generally called small and medium-sized roller forming welded pipe unit. After that, it was further developed into a row-roller type. The main production process layout and equipment composition of row-roll forming The row-roll forming machine is a major component of the welded steel tube production line. It is the core of production and the key equipment on the production line, which is responsible for bending flat steel strips into round tube billets.
According to the process requirements, the row-roll forming unit generally includes pinch rollers, pre-forming devices, rough forming devices, bending rollers, outer row rollers, upper deforming rollers, lower driving rollers, inner row rollers, fine forming racks, guide rollers , squeeze rollers, etc. Now it is described as follows.
1. Row-roll forming positioning method Most units adopt the center positioning method. The advantages of this center positioning method are:
1) When changing the specifications and sizes, the upper and lower rollers of the rough forming device are adjusted together, and the adjustment amount is relatively small; the four rollers of the fine forming device are adjusted up and down, left and right, and the adjustment amount is relatively small; the vertical rollers are positioned accurately.
2) The high-frequency transmission wire can be fixed in height.
3) The up and down adjustment amount of the medium frequency annealing sensor ultrasonic wave can be reduced by half.
2. Pinch roller
Generally, it is a two-roller type (no hole type), driven by a DC motor, and can be adjusted up and down. The purpose is to ensure that the line speeds of the rough forming and the finishing forming are consistent during the forming process of the strip steel, and the strip steel does not produce bending deformation in the frame, and starts to deform after leaving the frame. The pinch roller is very important to the centering of the strip steel, the vertical roller should be adjusted well, and it should be operated in conjunction with the downhill forming method.
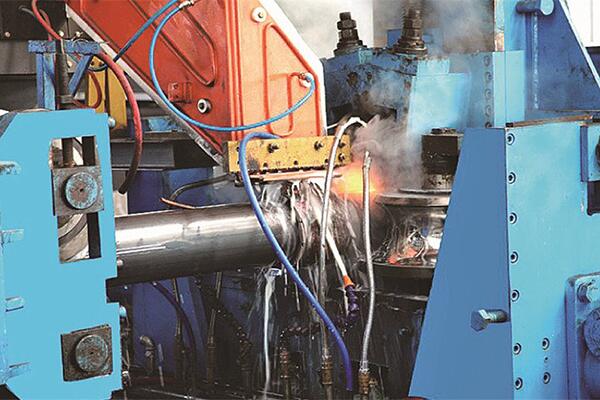
3. Preforming device
The strip steel is bent and deformed from the center (belongs to the central bending method), and its bending angle is fixed and does not change with the size of the pipe diameter. This section is the initial stage of row-roll forming, and its structure varies from unit to unit
4. Rough forming device (frame)
It is generally a two-roller type, driven by a DC motor, the upper and lower rolls are divided into 3 sections, and the middle drive ends freely slide. This kind of frame has 1 seat or 2 seats, but the upper and lower rollers have holes (concave-convex type) and the diameter is relatively large.
5. Bending Roller
The purpose is to bend the strip edges to the required dimensions, preventing the production of a "pear-shaped" finished tube. A pair of bending rollers can be adjusted together up and down, left and right, or individually. When changing product specifications, if 1 rough forming is used, most of the pass patterns will need to be replaced; if 2 rough forming is used, the bending rollers need to be replaced less, and only a few types can be replaced. On the whole, although the number of times to replace the bending rollers is more when using one rough forming frame, it is more economical than installing one more rough forming frame.
6. Outer row roller
The outer rollers are arranged symmetrically on both sides of the center line between the bending rollers and the finishing frame. Bending the strip steel into a 300°~330° open tube billet, so that it can easily enter the pass of the precision forming frame. The bending angle is related to the number of finely formed frames, as well as inner row rollers, lower support rollers, and deformed drive rollers. Its layout structure is designed into different structural forms according to the diameter of the formed steel pipe. When the diameter of the formed ERW pipe is 1120mm, a pass can be composed of two rolls, three rolls, four rolls or five rolls. When the diameter of the formed ERW pipe is 610mm, its pass pattern is basically composed of two rollers.
7. Inner row roller
Evenly arranged on the inner surface of the longitudinal tube blank. In the cross section of the pass, the number of rollers is determined according to the inner diameter of the welded pipe.
8. Deformation, drive roller
The upper roller is a deformed roller without driving, and the lower driving roller is driven by a DC motor. The lower driving roller is correspondingly arranged under the deforming roller, which increases the driving capacity of the strip and makes the deformation more uniform and reasonable.
9. Fine molding unit
Arranged behind the row of rollers, when the row of rollers bends and deforms the strip steel into a 330° open tube blank, two precision forming machines are used. When the row of rollers bends and deforms the strip steel into a 300° open tube blank, three precision forming machines are used. The precision forming passes are all closed passes, and the upper roller is equipped with guide sheets. The pass design adopts the vertical ellipse type, and the general machine base is the four-roller type, and the upper and lower rolls are driven by DC motors. There are also two types of racks: one is the archway of ordinary rolling mills; the other is the archway specially designed for row-rollers. The latter has good rigidity, and is convenient for changing rolls and adjusting. In order to ensure reliable deformation, the number of precision forming racks is 4 when producing general round pipes; if both round pipes and square rectangular pipes are produced, 5 racks are required.
10. Seam guide
The purpose is to control the opening angle of the weld seam between 3°~6° to ensure good welding. The welding seam guiding device itself has an insulation and adjustment mechanism to ensure the requirements of the welding angle.
11. Squeeze roller
Generally, the extrusion roller is four-roller or five-roller type, most of which are five-roller type.
According to the process requirements, the row-roll forming unit generally includes pinch rollers, pre-forming devices, rough forming devices, bending rollers, outer row rollers, upper deforming rollers, lower driving rollers, inner row rollers, fine forming racks, guide rollers , squeeze rollers, etc. Now it is described as follows.
1. Row-roll forming positioning method Most units adopt the center positioning method. The advantages of this center positioning method are:
1) When changing the specifications and sizes, the upper and lower rollers of the rough forming device are adjusted together, and the adjustment amount is relatively small; the four rollers of the fine forming device are adjusted up and down, left and right, and the adjustment amount is relatively small; the vertical rollers are positioned accurately.
2) The high-frequency transmission wire can be fixed in height.
3) The up and down adjustment amount of the medium frequency annealing sensor ultrasonic wave can be reduced by half.
2. Pinch roller
Generally, it is a two-roller type (no hole type), driven by a DC motor, and can be adjusted up and down. The purpose is to ensure that the line speeds of the rough forming and the finishing forming are consistent during the forming process of the strip steel, and the strip steel does not produce bending deformation in the frame, and starts to deform after leaving the frame. The pinch roller is very important to the centering of the strip steel, the vertical roller should be adjusted well, and it should be operated in conjunction with the downhill forming method.
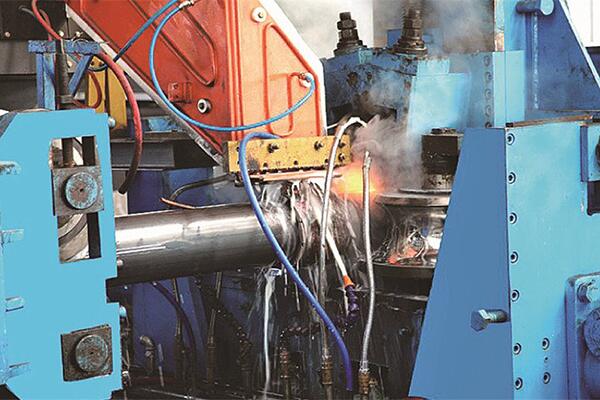
3. Preforming device
The strip steel is bent and deformed from the center (belongs to the central bending method), and its bending angle is fixed and does not change with the size of the pipe diameter. This section is the initial stage of row-roll forming, and its structure varies from unit to unit
4. Rough forming device (frame)
It is generally a two-roller type, driven by a DC motor, the upper and lower rolls are divided into 3 sections, and the middle drive ends freely slide. This kind of frame has 1 seat or 2 seats, but the upper and lower rollers have holes (concave-convex type) and the diameter is relatively large.
5. Bending Roller
The purpose is to bend the strip edges to the required dimensions, preventing the production of a "pear-shaped" finished tube. A pair of bending rollers can be adjusted together up and down, left and right, or individually. When changing product specifications, if 1 rough forming is used, most of the pass patterns will need to be replaced; if 2 rough forming is used, the bending rollers need to be replaced less, and only a few types can be replaced. On the whole, although the number of times to replace the bending rollers is more when using one rough forming frame, it is more economical than installing one more rough forming frame.
6. Outer row roller
The outer rollers are arranged symmetrically on both sides of the center line between the bending rollers and the finishing frame. Bending the strip steel into a 300°~330° open tube billet, so that it can easily enter the pass of the precision forming frame. The bending angle is related to the number of finely formed frames, as well as inner row rollers, lower support rollers, and deformed drive rollers. Its layout structure is designed into different structural forms according to the diameter of the formed steel pipe. When the diameter of the formed ERW pipe is 1120mm, a pass can be composed of two rolls, three rolls, four rolls or five rolls. When the diameter of the formed ERW pipe is 610mm, its pass pattern is basically composed of two rollers.
7. Inner row roller
Evenly arranged on the inner surface of the longitudinal tube blank. In the cross section of the pass, the number of rollers is determined according to the inner diameter of the welded pipe.
8. Deformation, drive roller
The upper roller is a deformed roller without driving, and the lower driving roller is driven by a DC motor. The lower driving roller is correspondingly arranged under the deforming roller, which increases the driving capacity of the strip and makes the deformation more uniform and reasonable.
9. Fine molding unit
Arranged behind the row of rollers, when the row of rollers bends and deforms the strip steel into a 330° open tube blank, two precision forming machines are used. When the row of rollers bends and deforms the strip steel into a 300° open tube blank, three precision forming machines are used. The precision forming passes are all closed passes, and the upper roller is equipped with guide sheets. The pass design adopts the vertical ellipse type, and the general machine base is the four-roller type, and the upper and lower rolls are driven by DC motors. There are also two types of racks: one is the archway of ordinary rolling mills; the other is the archway specially designed for row-rollers. The latter has good rigidity, and is convenient for changing rolls and adjusting. In order to ensure reliable deformation, the number of precision forming racks is 4 when producing general round pipes; if both round pipes and square rectangular pipes are produced, 5 racks are required.
10. Seam guide
The purpose is to control the opening angle of the weld seam between 3°~6° to ensure good welding. The welding seam guiding device itself has an insulation and adjustment mechanism to ensure the requirements of the welding angle.
11. Squeeze roller
Generally, the extrusion roller is four-roller or five-roller type, most of which are five-roller type.
Next:ASTM A519 gr 4130