1. Introduction to H beam platform welding process
(1)DefinitionThe H beam platform welding process is a process that connects H-shaped steel (a steel with a cross-sectional shape similar to the English letter H) through welding technology. Common H beam classifications include hot-rolled and welded H beam.
(2)Features
It has the advantages of high structural strength, good stability, strong load-bearing capacity, and convenient construction. It is widely used in bridges, buildings, ships, machinery manufacturing and other fields.
(3)Application fields
①Bridge construction
H-shaped steel platform welding technology is widely used in bridge construction, such as bridge decks, piers and other parts of large bridges.
②Building structure
The beams, columns and other parts of high-rise buildings, long-span structures and other buildings often use H -shaped steel platform welding technology.
③Ship manufacturing
The hull structure, deck and other parts of the ship need to bear large loads, and the H beam platform welding process can provide sufficient structural strength and stability.
④Machinery manufacturing
In the manufacturing of large mechanical equipment, the H-shaped steel platform welding process is often used in the support structure, frame and other parts of the equipment.
(4)The importance of welding process
①Improve structural strength and stability
The H-shaped steel platform welding process can effectively connect multiple H-shaped steels together to form a whole, thereby improving the strength and stability of the structure.
②Ensure construction quality
The accuracy of the welding process and construction quality directly affect the quality and safety of the entire project. Therefore, the use of advanced welding technology and strict construction management is the key to ensuring construction quality.
③Reduce costs
The H-shaped steel platform welding process can realize batch production and standardized production, thereby reducing production costs and improving production efficiency.
④Improve safety
The welding process can ensure the structural safety and stability of the H-shaped steel platform, thus improving the safety of the entire project.
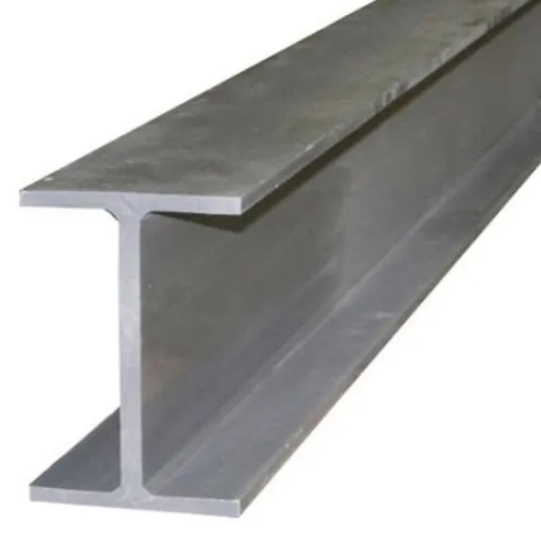
2.H beam welding process flow
(1) Preparation before welding①Material preparation
Ensure that the quality and specifications of H-shaped steel materials meet the requirements, and check whether the appearance and size of the materials meet the standards.
②Equipment inspection
Conduct a comprehensive inspection of welding equipment to ensure good performance, including welding machines, welding wires, flux, etc.
③Environmental requirements
Make sure the welding environment is clean, dry and free of oil and dust to reduce welding defects.
(2)Welding operation steps
① Positioning and fixing
Place and fix the H-shaped steel as required to ensure that it is operated in accordance with the prescribed welding sequence and that no movement occurs during the welding process.
②Welding sequence
Carry out the operation according to the prescribed welding sequence, weld the web plate first, and then weld the flange plate to ensure the welding quality.
③Welding parameter control
According to the material and thickness of H-shaped steel, select the appropriate welding current, voltage and welding speed to ensure welding quality.
④Weld quality inspection
During the welding process and after the welding is completed, the appearance and quality of the welds are inspected to detect and deal with problems in a timely manner.
(3) Treatment after welding
①Weld grinding
Polish the weld to remove welding slag and burrs to make the weld surface smooth.
②Weld inspection
Non-destructive testing technology is used to detect welds to ensure that the quality of welds meets requirements.
③ Anti-corrosion treatment
Preserve welds to improve their durability.
④Quality acceptance
Conduct quality inspection on the welded H-shaped steel platform in accordance with relevant standards and specifications to ensure compliance with requirements.
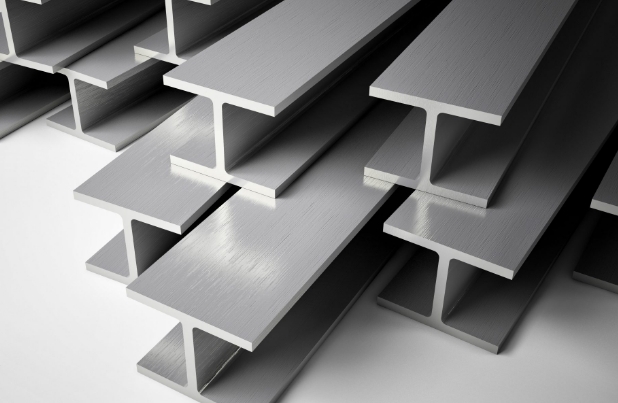
3. Key points of H beam welding process
(1) Selection of welding materials① Matchability of steel materials
Select welding materials that match the base metal to ensure the mechanical properties and corrosion resistance of the welded joint.
②Strength requirements of welds
According to the design requirements, select welding materials that can meet the weld strength requirements.
③Welding process
Consider the operability, melting point, thermal conductivity, etc. of the welding material to ensure the stability and reliability of the welding process.
(1) Determination of welding method
①Welding quality
Consider the quality requirements of the welded joints and choose a welding method that can ensure stable welding quality.
②Welding efficiency
Choose a welding method that can improve welding efficiency to shorten the production cycle.
③Difficulty of operation
Consider the skill level of the welder and the difficulty of the operation to select a suitable welding method.
(2) Control of welding quality
①Welding process parameters
According to the welding method and material characteristics, select appropriate welding current, voltage, welding speed and other process parameters.
②Preparation before welding
Ensure the cleanliness and flatness of the base material, as well as reasonable assembly gaps, to reduce the occurrence of welding defects.
③Post-weld inspection
Conduct visual inspection, non-destructive testing and mechanical property testing on welded joints to ensure that the welding quality meets the requirements.
4. Problems and solutions in H-shaped steel welding process
(1) The occurrence and prevention of welding cracks①Welding cracks
During the welding process, cracks may occur due to thermal stress, material properties and other factors.
②Preventive measures
Select appropriate welding materials, control welding parameters, preheat the base metal, reduce heat input, etc.
(2) Control of welding deformation
①Welding deformation
During the welding process, structural deformation may occur due to uneven thermal expansion and cooling contraction.
②Control method
Adopt reasonable welding sequence, control welding parameters, use anti-deformation method, etc.
(3) Detection and repair of welding defects
①Welding defects
Defects such as pores, slag inclusions, and lack of fusion may occur during the welding process.
②Detection method
X-ray testing, ultrasonic testing, magnetic particle testing, etc.
③Repair measures
Grinding, repair welding, machining, etc.