Large-diameter welded pipes are generally welded steel tubes that use double-sided submerged arc welding processes. According to their weld seams, they can be divided into large-diameter straight seam welded pipes and large-diameter spiral welded pipes.
The production process of large diameter longitudinal welded pipe is simple, the production efficiency is high, and the cost is low. The strength of the large-diameter spiral welded pipe is generally higher than that of the straight seam welded pipe. It can use a narrower billet to produce a welded pipe with a larger diameter. But the production efficiency is lower than that of seamless steel pipes.
Heat treatment process of large diameter welded pipe
1. During the heat treatment process, the cause of the change in the geometric shape of the large-diameter welded pipe is the heat treatment stress. Heat treatment stress is a relatively complicated issue. It is not only the cause of defects such as deformation and cracks, but also an important means to improve the fatigue strength and service life of workpieces.
2. Therefore, it is very important to understand the mechanism and change law of heat treatment stress and master the method of controlling internal stress. Heat treatment stress refers to the stress generated inside the welded pipe due to heat treatment factors (thermal process and tissue transformation process).
3. It is self-equilibrium in the whole or part of the volume of the welded pipe, so it is called internal stress. Heat treatment stress can be divided into tensile stress and compressive stress according to the nature of its action; it can be divided into instantaneous stress and residual stress according to its action time, and can be divided into thermal stress and tissue stress according to the cause of its formation.
4. For large-diameter welded pipes that do not change in composition and organizational state, when they are at different temperatures, as long as the linear expansion coefficient is not equal to zero, the specific volume will change. Therefore, during the heating or cooling process, mutual tension and compression internal stress will be generated between the surface centers of the workpiece. The greater the temperature difference generated in the workpiece, the greater the thermal stress.
5. Thermal stress is formed due to the different temperature changes of various parts in the welded pipe during the heating or cooling process. For example, for a solid workpiece, the surface always heats up faster than the core when heated, and the core cools slower than the surface when cooled, because heat is absorbed and dissipated through the surface.
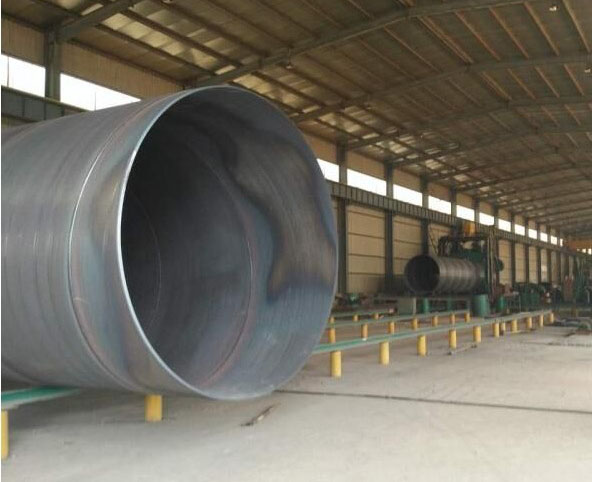
Which environments are large diameter welded pipes suitable for?
1. Structural categories: steel pipe pile curtains for wharves; steel pipes for high-rise buildings and bridge structures; structural steel pipes for offshore platforms.
2. Natural gas: submarine and onshore long-distance pipelines; gas pipelines at gas receiving stations; gas fields and urban natural gas pipeline networks.
3. Petrochemical: Crude oil, refined oil, petrochemical raw material and finished product delivery pipes and oilfield pipe network.
4. Coal: transportation of coal, coal water slurry, etc.
5. Other categories: tap water transportation; power plant intake and drainage pipelines and high-pressure pipelines.
The production process of large diameter longitudinal welded pipe is simple, the production efficiency is high, and the cost is low. The strength of the large-diameter spiral welded pipe is generally higher than that of the straight seam welded pipe. It can use a narrower billet to produce a welded pipe with a larger diameter. But the production efficiency is lower than that of seamless steel pipes.
Heat treatment process of large diameter welded pipe
1. During the heat treatment process, the cause of the change in the geometric shape of the large-diameter welded pipe is the heat treatment stress. Heat treatment stress is a relatively complicated issue. It is not only the cause of defects such as deformation and cracks, but also an important means to improve the fatigue strength and service life of workpieces.
2. Therefore, it is very important to understand the mechanism and change law of heat treatment stress and master the method of controlling internal stress. Heat treatment stress refers to the stress generated inside the welded pipe due to heat treatment factors (thermal process and tissue transformation process).
3. It is self-equilibrium in the whole or part of the volume of the welded pipe, so it is called internal stress. Heat treatment stress can be divided into tensile stress and compressive stress according to the nature of its action; it can be divided into instantaneous stress and residual stress according to its action time, and can be divided into thermal stress and tissue stress according to the cause of its formation.
4. For large-diameter welded pipes that do not change in composition and organizational state, when they are at different temperatures, as long as the linear expansion coefficient is not equal to zero, the specific volume will change. Therefore, during the heating or cooling process, mutual tension and compression internal stress will be generated between the surface centers of the workpiece. The greater the temperature difference generated in the workpiece, the greater the thermal stress.
5. Thermal stress is formed due to the different temperature changes of various parts in the welded pipe during the heating or cooling process. For example, for a solid workpiece, the surface always heats up faster than the core when heated, and the core cools slower than the surface when cooled, because heat is absorbed and dissipated through the surface.
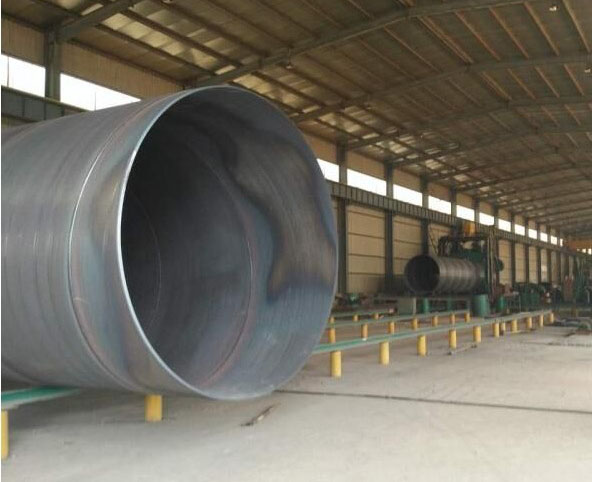
Which environments are large diameter welded pipes suitable for?
1. Structural categories: steel pipe pile curtains for wharves; steel pipes for high-rise buildings and bridge structures; structural steel pipes for offshore platforms.
2. Natural gas: submarine and onshore long-distance pipelines; gas pipelines at gas receiving stations; gas fields and urban natural gas pipeline networks.
3. Petrochemical: Crude oil, refined oil, petrochemical raw material and finished product delivery pipes and oilfield pipe network.
4. Coal: transportation of coal, coal water slurry, etc.
5. Other categories: tap water transportation; power plant intake and drainage pipelines and high-pressure pipelines.