When the geological conditions are not good and the bearing capacity of the foundation is small, the PHC pipe pile foundation must be selected, and the piles are driven into the ground one by one, and the components of the buildings above are transmitted through the pile foundation to the soil layer with high bearing capacity of the lower layer. If the soil layer with high bearing capacity of the lower layer is deep, the friction force between the pile foundation and the surrounding soil can also be used to support the component of the upper building. So how are PHC pipe piles generally constructed?
Construction operation of PHC pipe pile:
1) Measuring and laying out line
There shall be no less than 2 control piles and leveling points near the piling construction area, and their orientation shall be based on the principle of not being affected by piling (40m away from the operating address). The axis control pile should be set at 5~10m away from the external wall pile to control the axis and elevation of the pile foundation. The axis and elevation of the pile foundation have been measured. After inspection and review, the pre-inspection procedures should be processed and filed for inspection.
2) Measuring and placing pile position
Set the building axis and corner piles according to the control point, measure and place the pile position according to the pile position layout diagram, and mark the center of the pile position with steel bars or bamboo sticks. In order to prevent the pile driver from extruding the soil by its own weight when the pile driver is in place, the displacement of the measured pile should be checked before the pile driver is in place, and the pile positioning error should be controlled within 20mm. One level gauge controls the elevation of the pile top, and two orthogonal theodolites control the straightness of the pipe pile.
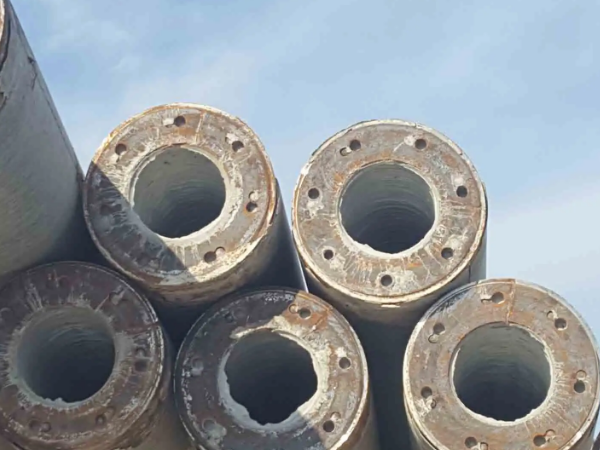
3) Vertical pile and pile insertion
According to the control point that has been set, use the Cartesian coordinate method to double check the pile position. After correct, lower the first section of the pile, and control the error between the center point of the first section of the pile tip and the pile position within 20mm.
4) Straightness control
When the pile tip enters the soil layer 500mm, use the theodolite to adjust the pile frame of the pile driver to be in a straight position, and then adjust the straightness of the first section of the pile (the theodolite is generally erected 15m away from the pile driver), so that the pile frame and the pile body are kept parallel. The accuracy error is less than 1% of the pile length (the straightness error of the first pipe pile when it is inserted into the ground should not exceed 0.5%), the pile can be pressed, and the tracking monitoring is carried out during the pile pressing process, and the pile frame is instructed to maintain its accuracy. If it is out of tolerance, it must be adjusted in time, but it is necessary to ensure that the pile body does not crack. If necessary, pull out and re-insert the pile body as much as possible, find out the cause, remove the fault, and backfill with sand before construction. The method is used to quickly rectify the deviation, and the pile body is pulled and broken.
5) Piling
Pile driving (hammer construction) Use the guide sliding fixture or pile hoop of the pile frame to embed the pile in the two guides of the pile frame, align the pile center directly, slowly lower it into the soil, and wait for the pile orientation and straightness to be corrected. The hammer can be pressed on the pile together with the pile cap, and a ruler should be set on the side of the pile or on the frame. And make a record before hitting the pile. If the pile head is unusual, use a sack or thick cardboard to level it, and it can also be smoothed with epoxy mortar first. At the beginning of piling, the hammer should be lightly pressed or hit several times. After checking that the pile body, pile frame, pile hammer, etc. are straight and consistent, it can be transferred to normal driving. After the pile is stabilized, it can be driven according to the required drop distance. Pile driving uses pile caps and elastic pads with appropriate pile head size to smooth the impact during piling and distribute the piling stress evenly, and extend the duration of the impact to facilitate the penetration of the pile. The pile cap is made of cast steel or steel plate, the hammer pad is mostly made of hardwood or white-brown rope ring, and the pile pad is mostly made of pine wood or paper pad or phenolic laminated plastic, synthetic rubber, etc.
The surface of the pile cap in contact with the pile must be flat and on the same line with the pile body to avoid deflection during piling. If the pile hammer has its own cap, it only needs to protect the top of the pile with a rope pad or wooden block. If the pile needs to go deep into the soil, use the delivery pile. The feeding pile is made of solid wood or steel, and the length and diameter are determined according to the needs. When using, place the feeding pile on the top of the pile so that it is on the same vertical line as the pile, hammer the feeding pile, and gradually drive the pile into the pile. in the soil. In the process of pile driving, always pay attention to whether the pile body has displacement and skew. If any problems are found, they should be corrected in time. When the pile will sink to the required depth or reach the hard soil layer, the height of the drop hammer should generally not be greater than 1m to avoid breaking the pile head. , During the pile driving process, record the pile driving construction. When it is close to the design requirements, you can observe the penetration level or the soil entry elevation until the design requirements are met, and then move the pile driver to the new pile position.
Go here if you want to learn about "How to repair fracture at the top of pipe pile?"