Mild steel plate is a carbon steel plate with a carbon content of ≤0.25%. It has good plasticity, toughness and weldability, is easy to form by cold working, but has low strength and hardness and moderate cost. It is widely used in automobile bodies, building steel structures, home appliance shells and other fields. The production process directly affects its quality: improper hot rolling temperature control will lead to uneven structure; excessive cold rolling reduction rate will easily cause work hardening; deviation in annealing process parameters will affect toughness. Surface treatment such as galvanizing process will reduce corrosion resistance if the coating is uneven. Only by strictly controlling the process of each link can the performance of the steel plate be stable and meet the needs of different scenarios.
The production process of mild steel plate mainly includes the following steps:
1. Raw material preparation: Low-carbon steel billet (carbon content ≤ 0.25%) is used as raw material, and after removing surface impurities, it is heated to 1100-1250℃ to soften it.
2. Hot rolling: The heated steel billet is rolled to a certain thickness by a rough rolling mill, and then rolled multiple times by a finishing mill, and the final rolling temperature is controlled (usually 800-900℃) to form a hot-rolled steel plate with a thickness of generally 2-20mm.
3. Cooling and coiling: After hot rolling, it is quickly cooled (such as laminar cooling), the cooling speed is controlled, and then it is rolled into a steel coil to improve the performance stability of the steel plate.
4. Cold rolling (optional): further rolling of hot-rolled plates, direct cold rolling without heating, thickness can be reduced to 0.1-3mm, improving surface finish and dimensional accuracy.
5. Heat treatment: annealing is required after cold rolling to eliminate stress and improve plasticity. Surface treatment such as cold rolling annealing or galvanizing can be selected according to needs.
6. Finishing: including straightening, trimming, inspection, and finally forming a mild steel plate that meets the standards.
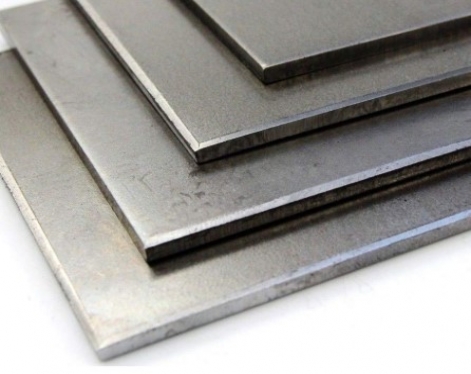
Matters needing attention in the production process of mild steel plates
1. Raw material control: Strictly screen raw materials such as iron ore and scrap steel to avoid excessive impurities and ensure that the carbon content is accurately controlled below 0.25%, which directly affects the plasticity and weldability of the steel plate.
2. Temperature control: Hot rolling requires precise control of the heating temperature (1100-1250℃) and the final rolling temperature (800-900℃). Uneven temperatures can easily lead to structural defects; the annealing temperature before cold rolling needs to match the material to prevent overburning or abnormal hardness.
3. Rolling parameters: The hot rolling reduction rate must be uniform to avoid local stress concentration; the cold rolling speed and reduction amount must be adapted to prevent poor plate shape or surface scratches.
4. Cooling specifications: The cooling rate after hot rolling must be stable to prevent coarse grains; slow cooling after cold rolling to avoid excessive internal stress and affect subsequent processing.
5. Surface treatment: Pickling must thoroughly remove the oxide scale, and ensure the surface is clean before galvanizing/painting to avoid coating shedding or corrosion hazards.
Does the production process of mild steel plates have a big impact on the environment?
From the perspective of the links, high-temperature heating (such as hot rolling and annealing) relies on fossil energy and will emit a large amount of carbon dioxide; pickling uses strong acid to produce wastewater containing heavy metals, which will pollute the water and soil if not properly treated; rolling equipment operation and raw material transportation produce noise and dust. Under traditional processes, these links release pollutants in a concentrated manner, which has a significant impact on the local environment.
However, in recent years, the industry has promoted clean energy (such as natural gas replacing coal), wastewater recycling treatment systems, dust collection devices, etc., and the popularization of short-process steelmaking (using electric furnaces to replace some converters), carbon emissions and pollutant emissions have dropped significantly. Overall, its environmental impact is controllable and continues to be optimized with the upgrading of environmental protection technologies.
Read more: Advantages and Disadvantages of Mild Steel Plates
The production process of mild steel plate mainly includes the following steps:
1. Raw material preparation: Low-carbon steel billet (carbon content ≤ 0.25%) is used as raw material, and after removing surface impurities, it is heated to 1100-1250℃ to soften it.
2. Hot rolling: The heated steel billet is rolled to a certain thickness by a rough rolling mill, and then rolled multiple times by a finishing mill, and the final rolling temperature is controlled (usually 800-900℃) to form a hot-rolled steel plate with a thickness of generally 2-20mm.
3. Cooling and coiling: After hot rolling, it is quickly cooled (such as laminar cooling), the cooling speed is controlled, and then it is rolled into a steel coil to improve the performance stability of the steel plate.
4. Cold rolling (optional): further rolling of hot-rolled plates, direct cold rolling without heating, thickness can be reduced to 0.1-3mm, improving surface finish and dimensional accuracy.
5. Heat treatment: annealing is required after cold rolling to eliminate stress and improve plasticity. Surface treatment such as cold rolling annealing or galvanizing can be selected according to needs.
6. Finishing: including straightening, trimming, inspection, and finally forming a mild steel plate that meets the standards.
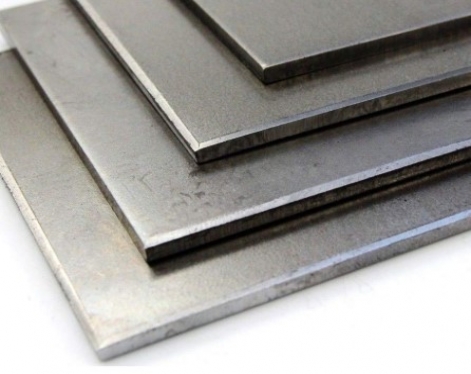
Matters needing attention in the production process of mild steel plates
1. Raw material control: Strictly screen raw materials such as iron ore and scrap steel to avoid excessive impurities and ensure that the carbon content is accurately controlled below 0.25%, which directly affects the plasticity and weldability of the steel plate.
2. Temperature control: Hot rolling requires precise control of the heating temperature (1100-1250℃) and the final rolling temperature (800-900℃). Uneven temperatures can easily lead to structural defects; the annealing temperature before cold rolling needs to match the material to prevent overburning or abnormal hardness.
3. Rolling parameters: The hot rolling reduction rate must be uniform to avoid local stress concentration; the cold rolling speed and reduction amount must be adapted to prevent poor plate shape or surface scratches.
4. Cooling specifications: The cooling rate after hot rolling must be stable to prevent coarse grains; slow cooling after cold rolling to avoid excessive internal stress and affect subsequent processing.
5. Surface treatment: Pickling must thoroughly remove the oxide scale, and ensure the surface is clean before galvanizing/painting to avoid coating shedding or corrosion hazards.
Does the production process of mild steel plates have a big impact on the environment?
From the perspective of the links, high-temperature heating (such as hot rolling and annealing) relies on fossil energy and will emit a large amount of carbon dioxide; pickling uses strong acid to produce wastewater containing heavy metals, which will pollute the water and soil if not properly treated; rolling equipment operation and raw material transportation produce noise and dust. Under traditional processes, these links release pollutants in a concentrated manner, which has a significant impact on the local environment.
However, in recent years, the industry has promoted clean energy (such as natural gas replacing coal), wastewater recycling treatment systems, dust collection devices, etc., and the popularization of short-process steelmaking (using electric furnaces to replace some converters), carbon emissions and pollutant emissions have dropped significantly. Overall, its environmental impact is controllable and continues to be optimized with the upgrading of environmental protection technologies.
Read more: Advantages and Disadvantages of Mild Steel Plates