Stainless steel expanded plate is also known as stainless steel stretched expanded mesh, stainless steel expanded mesh, and stainless steel punched mesh. It is one of the steel plate stretched mesh products made of stainless steel plates. The mesh is uniform, the mesh surface is flat and the friction coefficient is high. It is strong and suitable for cutting and processing workpieces. Sturdy and durable, beautiful in appearance, saving material space, it is a good material for environmental protection and energy saving.
Stainless steel plate mesh refers to a grid plate made of stainless steel material for flat steel and connecting rods. There are various types of materials such as 304, 316L, etc. The production of stainless steel plate mesh is a process that requires strict development of welding construction technology. How to effectively avoid problems such as warping, unevenness, and poor welding through operational capabilities during the production management process is a significant issue. The deformation of the welding structure of stainless steel mesh plate severely affects the quality and usability of the welding work and has a certain complexity and diversity. Common deformations are mainly related to transverse shrinkage, longitudinal shrinkage, bending deformation, and buckling.
During the welding process of stainless steel plate mesh, we need to fully consider the impact of factors such as the material of different plates, geometric structure shape, size, and constraints, while also including traditional welding processes and welding parameters into the scope of social factor research management. Specifically, the resistance of stainless steel plates to resist instability deformation and the critical load they can withstand are mainly related to the selected plate material, geometric model shape, and other design-related quantities. The residual stress caused by the welding system instability is closely related to the welding method and parameters used.
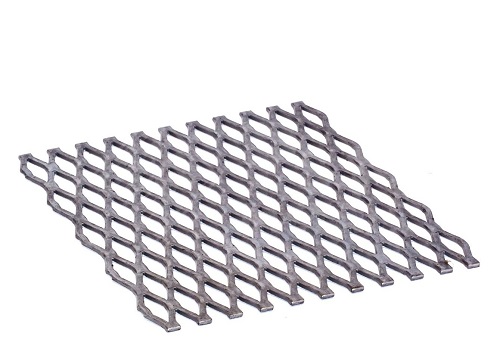
To avoid deformation during the manufacturing process of stainless steel grille plates, it is necessary to control from the selection of materials first. Choosing stainless steel mesh plates as materials is a good choice, but it is important to avoid purchasing poor-quality flat steel raw materials, especially those that may contain too many impurities. In addition, when choosing small manufacturers, it is also necessary to pay attention to their production quality.
In the manufacturing process, welding is an important link and needs to be strictly controlled to ensure the quality and shape of the grille plate. The quality of welding is a big test for the final performance and stability of the stainless steel grille plate. Therefore, the welding process must be given full attention and refined operation.
Secondly, it is necessary to master some research methods for the welding process of stainless steel mesh plates.
1. During the welding process of stainless steel grille plates, measures to reduce technical distortion are needed. There are two aspects to pay attention to during the welding process. On the one hand, minimizing the longitudinal force caused by the plastic pressure generated during the heating phase. The plastic pressure force longitudinally includes: pre-tension force (mechanical stretching and preset temperature), reducing heat input equivalent methods (using various cooling sides of welding fixtures and using heat-absorbing materials previously deposited), and uniformly cooling the preheating gradient method. On the other hand, cooling, where the temperature difference between the dynamic binding clamps includes stretching (with cold welding) and static temperature difference stretching, maximizing longitudinal plastic strain during the period.
2. Control measures for the deformation process of stainless steel plate mesh after welding. The most scientific method is to use the multi-point heating method to correct the convex and concave deformation problems of stainless steel mesh plates. Generally, the diameter of the heating point is not less than 15mm, and the distance between the heating points should be determined according to the size of the deformation of different plates, usually within the range of 50-100mm. Studies have shown that by using traditional welding and eliminating residual stress heat treatment methods after welding, it is possible to overcome the deformation of steel welded components. To better prevent the rebound deformation of stainless steel thin plates after welding, improve the size stability of the components, and through some slit samples, strip samples, and plate samples, without forced welding, and then perform post-weld heat treatment technology on the components, it is possible to effectively overcome the deformation of the plate welding.
Stainless steel plate mesh refers to a grid plate made of stainless steel material for flat steel and connecting rods. There are various types of materials such as 304, 316L, etc. The production of stainless steel plate mesh is a process that requires strict development of welding construction technology. How to effectively avoid problems such as warping, unevenness, and poor welding through operational capabilities during the production management process is a significant issue. The deformation of the welding structure of stainless steel mesh plate severely affects the quality and usability of the welding work and has a certain complexity and diversity. Common deformations are mainly related to transverse shrinkage, longitudinal shrinkage, bending deformation, and buckling.
During the welding process of stainless steel plate mesh, we need to fully consider the impact of factors such as the material of different plates, geometric structure shape, size, and constraints, while also including traditional welding processes and welding parameters into the scope of social factor research management. Specifically, the resistance of stainless steel plates to resist instability deformation and the critical load they can withstand are mainly related to the selected plate material, geometric model shape, and other design-related quantities. The residual stress caused by the welding system instability is closely related to the welding method and parameters used.
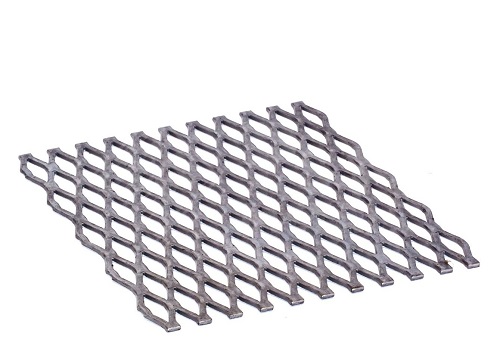
To avoid deformation during the manufacturing process of stainless steel grille plates, it is necessary to control from the selection of materials first. Choosing stainless steel mesh plates as materials is a good choice, but it is important to avoid purchasing poor-quality flat steel raw materials, especially those that may contain too many impurities. In addition, when choosing small manufacturers, it is also necessary to pay attention to their production quality.
In the manufacturing process, welding is an important link and needs to be strictly controlled to ensure the quality and shape of the grille plate. The quality of welding is a big test for the final performance and stability of the stainless steel grille plate. Therefore, the welding process must be given full attention and refined operation.
Secondly, it is necessary to master some research methods for the welding process of stainless steel mesh plates.
1. During the welding process of stainless steel grille plates, measures to reduce technical distortion are needed. There are two aspects to pay attention to during the welding process. On the one hand, minimizing the longitudinal force caused by the plastic pressure generated during the heating phase. The plastic pressure force longitudinally includes: pre-tension force (mechanical stretching and preset temperature), reducing heat input equivalent methods (using various cooling sides of welding fixtures and using heat-absorbing materials previously deposited), and uniformly cooling the preheating gradient method. On the other hand, cooling, where the temperature difference between the dynamic binding clamps includes stretching (with cold welding) and static temperature difference stretching, maximizing longitudinal plastic strain during the period.
2. Control measures for the deformation process of stainless steel plate mesh after welding. The most scientific method is to use the multi-point heating method to correct the convex and concave deformation problems of stainless steel mesh plates. Generally, the diameter of the heating point is not less than 15mm, and the distance between the heating points should be determined according to the size of the deformation of different plates, usually within the range of 50-100mm. Studies have shown that by using traditional welding and eliminating residual stress heat treatment methods after welding, it is possible to overcome the deformation of steel welded components. To better prevent the rebound deformation of stainless steel thin plates after welding, improve the size stability of the components, and through some slit samples, strip samples, and plate samples, without forced welding, and then perform post-weld heat treatment technology on the components, it is possible to effectively overcome the deformation of the plate welding.