Boiler tubes are an important part of the boiler system, mainly used to transport high-temperature and high-pressure steam or hot water. Their service life is affected by many factors, including material quality, working environment, operating conditions, maintenance, etc. The following will analyze the service life of boiler tubes and its influencing factors in detail from different angles.
Basic Overview of Boiler Tubes
Boiler tubes are usually made of carbon steel, alloy steel or stainless steel. According to their use and working conditions, they can be divided into seamless steel tubes and welded steel tubes. The main function of boiler tubes is to withstand high temperature and high pressure to ensure the safe transportation of steam or hot water. Due to the particularity of its working environment, boiler tubes must have good heat resistance, corrosion resistance and mechanical strength.
Service life of boiler tubes
Boiler tubes typically last 10 to 30 years, but this varies depending on the following factors:
1. Material quality
The material of the boiler tube directly affects its service life. High-quality alloy steel or stainless steel tubes have better heat resistance and corrosion resistance and longer service life. Low-quality carbon steel tubes are prone to oxidation, corrosion and deformation under high temperature and high pressure environments, resulting in a shortened service life.
2. Working environment
The working environment of boiler tubes has a significant impact on their lifespan. For example, boiler tubes working in high temperature, high pressure, high humidity or corrosive media (such as acidic or alkaline water) will have their service life greatly shortened. In addition, boiler tubes are also prone to fatigue damage under conditions of frequent start-stop or load fluctuations, resulting in a shortened lifespan.
3. Operating conditions
Improper operation will accelerate the aging of boiler tubes. For example, over-temperature and over-pressure operation will cause creep or embrittlement of boiler tube materials; poor water quality (such as high hardness and high oxygen content) will cause scaling or corrosion on the inner wall of boiler tubes, thus shortening their service life.
4. Maintenance
Regular maintenance and care are the key to extending the service life of boiler tubes. Through regular cleaning, descaling, anti-corrosion treatment and inspection, potential problems can be discovered and dealt with in a timely manner, avoiding boiler tube failure due to corrosion, cracks or deformation.
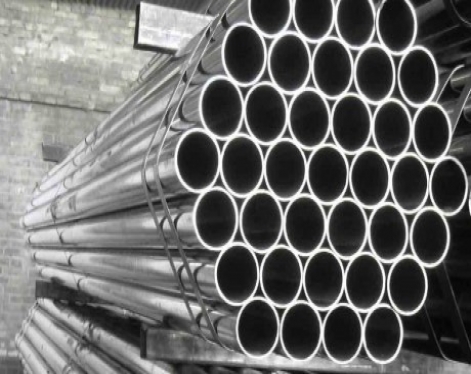
Main issues affecting boiler tube life
1. Corrosion
Corrosion is the most common failure mode of boiler tubes. Corrosion can be divided into internal corrosion and external corrosion: internal corrosion is mainly caused by poor water quality or corrosive media; external corrosion is caused by environmental humidity, temperature or chemicals. Corrosion will cause the wall thickness of boiler tubes to decrease, the strength to decrease, and eventually leakage or bursting of the tubes.
2. Scaling
Scaling on the inner wall of boiler tubes will reduce heat transfer efficiency, cause the tube wall temperature to rise, and accelerate material aging and failure. In addition, scaling can also cause local overheating, causing deformation or rupture of boiler tubes.
3. Fatigue damage
Boiler tubes are prone to fatigue cracks under conditions of frequent start-stop or load fluctuations. These cracks will gradually expand and eventually lead to boiler tube failure.
4. Creep
Under high temperature and high pressure environment, the boiler tube material will creep, that is, the material slowly deforms under stress. Creep will cause the boiler tube wall thickness to decrease, the strength to decrease, and eventually fail.
Measures to prolong the service life of boiler tubes
1. Choose high-quality materials
Choose appropriate boiler tube materials according to working conditions. For example, in high temperature and high pressure environments, alloy steel or stainless steel tubes with better heat resistance and corrosion resistance should be selected.
2. Optimize operating conditions
Avoid over-temperature and over-pressure operation, control boiler load fluctuations, and reduce frequent start-stop to reduce fatigue damage and creep risks of boiler tubes.
3. Improve water quality
Pre-treat boiler water to reduce hardness and oxygen content to prevent scaling and corrosion. Regularly test and treat water quality to ensure that water quality meets standards.
4. Regular maintenance and inspection
Develop and implement a maintenance plan for boiler tubes, including cleaning, descaling, anti-corrosion treatment and non-destructive testing. Through regular inspections, potential problems can be discovered and dealt with in a timely manner to avoid accidents.
5. Use advanced technology
Use modern technology, such as online monitoring systems and non-destructive testing technology, to monitor the status of boiler tubes in real time and warn of potential risks in advance.
Boiler tube replacement standards
When the boiler tube has the following conditions, it should be replaced in time:
1. The wall thickness is reduced beyond the allowable range;
2. Severe corrosion, cracks or deformation occurs;
3. The heat transfer efficiency is significantly reduced and cannot meet the operating requirements;
4. The design service life is reached and it is uated that it can no longer be used safely.
Conclusion
The service life of boiler tubes is affected by many factors and is usually between 10 and 30 years. By selecting high-quality materials, optimizing operating conditions, improving water quality, regular maintenance and adopting advanced technology, the service life of boiler tubes can be effectively extended to ensure the safe and stable operation of the boiler system. At the same time, a boiler tube replacement plan should be formulated according to actual conditions to avoid accidents caused by aging or failure.
Read more: Production Methods and Precautions for Boiler Tubes
Basic Overview of Boiler Tubes
Boiler tubes are usually made of carbon steel, alloy steel or stainless steel. According to their use and working conditions, they can be divided into seamless steel tubes and welded steel tubes. The main function of boiler tubes is to withstand high temperature and high pressure to ensure the safe transportation of steam or hot water. Due to the particularity of its working environment, boiler tubes must have good heat resistance, corrosion resistance and mechanical strength.
Service life of boiler tubes
Boiler tubes typically last 10 to 30 years, but this varies depending on the following factors:
1. Material quality
The material of the boiler tube directly affects its service life. High-quality alloy steel or stainless steel tubes have better heat resistance and corrosion resistance and longer service life. Low-quality carbon steel tubes are prone to oxidation, corrosion and deformation under high temperature and high pressure environments, resulting in a shortened service life.
2. Working environment
The working environment of boiler tubes has a significant impact on their lifespan. For example, boiler tubes working in high temperature, high pressure, high humidity or corrosive media (such as acidic or alkaline water) will have their service life greatly shortened. In addition, boiler tubes are also prone to fatigue damage under conditions of frequent start-stop or load fluctuations, resulting in a shortened lifespan.
3. Operating conditions
Improper operation will accelerate the aging of boiler tubes. For example, over-temperature and over-pressure operation will cause creep or embrittlement of boiler tube materials; poor water quality (such as high hardness and high oxygen content) will cause scaling or corrosion on the inner wall of boiler tubes, thus shortening their service life.
4. Maintenance
Regular maintenance and care are the key to extending the service life of boiler tubes. Through regular cleaning, descaling, anti-corrosion treatment and inspection, potential problems can be discovered and dealt with in a timely manner, avoiding boiler tube failure due to corrosion, cracks or deformation.
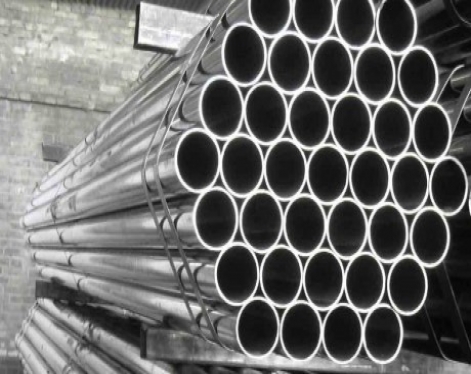
Main issues affecting boiler tube life
1. Corrosion
Corrosion is the most common failure mode of boiler tubes. Corrosion can be divided into internal corrosion and external corrosion: internal corrosion is mainly caused by poor water quality or corrosive media; external corrosion is caused by environmental humidity, temperature or chemicals. Corrosion will cause the wall thickness of boiler tubes to decrease, the strength to decrease, and eventually leakage or bursting of the tubes.
2. Scaling
Scaling on the inner wall of boiler tubes will reduce heat transfer efficiency, cause the tube wall temperature to rise, and accelerate material aging and failure. In addition, scaling can also cause local overheating, causing deformation or rupture of boiler tubes.
3. Fatigue damage
Boiler tubes are prone to fatigue cracks under conditions of frequent start-stop or load fluctuations. These cracks will gradually expand and eventually lead to boiler tube failure.
4. Creep
Under high temperature and high pressure environment, the boiler tube material will creep, that is, the material slowly deforms under stress. Creep will cause the boiler tube wall thickness to decrease, the strength to decrease, and eventually fail.
Measures to prolong the service life of boiler tubes
1. Choose high-quality materials
Choose appropriate boiler tube materials according to working conditions. For example, in high temperature and high pressure environments, alloy steel or stainless steel tubes with better heat resistance and corrosion resistance should be selected.
2. Optimize operating conditions
Avoid over-temperature and over-pressure operation, control boiler load fluctuations, and reduce frequent start-stop to reduce fatigue damage and creep risks of boiler tubes.
3. Improve water quality
Pre-treat boiler water to reduce hardness and oxygen content to prevent scaling and corrosion. Regularly test and treat water quality to ensure that water quality meets standards.
4. Regular maintenance and inspection
Develop and implement a maintenance plan for boiler tubes, including cleaning, descaling, anti-corrosion treatment and non-destructive testing. Through regular inspections, potential problems can be discovered and dealt with in a timely manner to avoid accidents.
5. Use advanced technology
Use modern technology, such as online monitoring systems and non-destructive testing technology, to monitor the status of boiler tubes in real time and warn of potential risks in advance.
Boiler tube replacement standards
When the boiler tube has the following conditions, it should be replaced in time:
1. The wall thickness is reduced beyond the allowable range;
2. Severe corrosion, cracks or deformation occurs;
3. The heat transfer efficiency is significantly reduced and cannot meet the operating requirements;
4. The design service life is reached and it is uated that it can no longer be used safely.
Conclusion
The service life of boiler tubes is affected by many factors and is usually between 10 and 30 years. By selecting high-quality materials, optimizing operating conditions, improving water quality, regular maintenance and adopting advanced technology, the service life of boiler tubes can be effectively extended to ensure the safe and stable operation of the boiler system. At the same time, a boiler tube replacement plan should be formulated according to actual conditions to avoid accidents caused by aging or failure.
Read more: Production Methods and Precautions for Boiler Tubes