The hot-dip galvanizing of seamless steel pipes is to pickle the steel pipes first, in order to remove the iron oxide on the surface of the steel pipes. After pickling, it is cleaned in an ammonium chloride or zinc chloride aqueous solution or a mixed aqueous solution of ammonium chloride and zinc chloride, and then sent to a hot-dip coating tank. Hot-dip galvanized seamless pipe has the advantages of uniform coating, strong adhesion and long service life.
Standards and reasons for hot-dip galvanizing of seamless pipes
1. Adhesion amount:
Corrosion resistance is mainly determined by the thickness of the galvanized layer, so measuring the thickness is often the basis for judging the quality of the galvanized layer. The galvanized layer reacts differently due to the composition, structure and structure of the steel surface, and the angle and speed of entering and exiting the zinc solution also have a great influence.
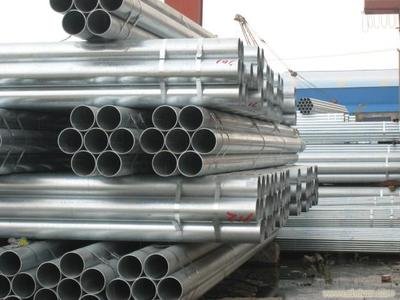
2. Uniformity:
The most rusty part of hot-dip galvanized steel is still the thinnest part of the zinc layer, so it is necessary to test whether the thinnest part meets the standard.
The uniformity test method generally uses copper sulfate test, but this method is very problematic for the test of the galvanized layer film composed of zinc layer and alloy layer. It is not very reasonable to judge the uniformity by the number of repetitions of a certain immersion time. Therefore, in the recent European and American standards and JIS, there is a tendency to abolish this test method, replace the uniformity with distribution, and use the film thickness gauge to check the distribution state when necessary.
3. Solidity:
The so-called solidity is the adhesion between the galvanized layer and the steel. It mainly requires that the galvanized components must not be peeled off during the arrangement, transportation, storage and use. The general inspection methods include hammering method, extrusion method, coiling method, etc. .
Adhesion, uniformity, and firmness are the items that define the quality inspection of hot-dip galvanizing in general specifications. It is also the standard for general formal inspection reports.
Standards and reasons for hot-dip galvanizing of seamless pipes
1. Adhesion amount:
Corrosion resistance is mainly determined by the thickness of the galvanized layer, so measuring the thickness is often the basis for judging the quality of the galvanized layer. The galvanized layer reacts differently due to the composition, structure and structure of the steel surface, and the angle and speed of entering and exiting the zinc solution also have a great influence.
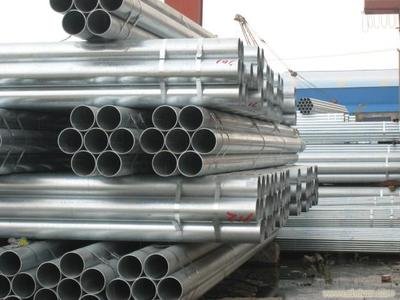
2. Uniformity:
The most rusty part of hot-dip galvanized steel is still the thinnest part of the zinc layer, so it is necessary to test whether the thinnest part meets the standard.
The uniformity test method generally uses copper sulfate test, but this method is very problematic for the test of the galvanized layer film composed of zinc layer and alloy layer. It is not very reasonable to judge the uniformity by the number of repetitions of a certain immersion time. Therefore, in the recent European and American standards and JIS, there is a tendency to abolish this test method, replace the uniformity with distribution, and use the film thickness gauge to check the distribution state when necessary.
3. Solidity:
The so-called solidity is the adhesion between the galvanized layer and the steel. It mainly requires that the galvanized components must not be peeled off during the arrangement, transportation, storage and use. The general inspection methods include hammering method, extrusion method, coiling method, etc. .
Adhesion, uniformity, and firmness are the items that define the quality inspection of hot-dip galvanizing in general specifications. It is also the standard for general formal inspection reports.