Scope of application
Submerged arc welding is one of the mechanized welding methods with high production efficiency today. Its full name is submerged arc automatic welding, also known as automatic arc welding under flux layer. It is a welding method in which an arc burns under a flux layer. Its inherent advantages such as stable welding quality, high welding productivity, no arc light and little smoke make it the main welding method in the manufacture of important steel structures such as pressure vessels, pipe section manufacturing, and box-shaped beams and columns.
Argon arc welding technology is based on the principle of ordinary arc welding, using argon to protect the metal welding material, and through high current to melt the welding material into a liquid state on the base material to be welded to form a molten pool. A welding technique that achieves a metallurgical combination of the metal to be welded and the welding material. Since the argon gas is continuously supplied during high-temperature fusion welding, the welding material cannot be in contact with the oxygen in the air, thus preventing the oxidation of the welding material, so it can weld stainless steel and ferrous metals.
Tips: Because of its characteristics, submerged arc welding technology is often used in the manufacture of pipe sections. The welded steel tubes produced by submerged arc welding technology mainly include LSAW pipes and SSAW pipes.
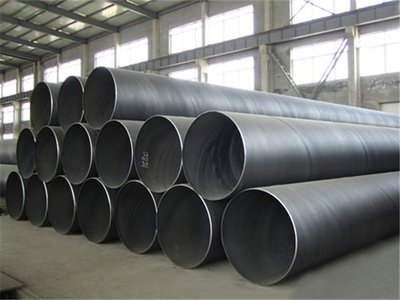
Features
1. Submerged arc welding
(1) High production efficiency
On the one hand, the conductive length of the welding wire is shortened, and the current and current density are increased, so the penetration depth of the arc and the deposition efficiency of the welding wire are greatly improved. On the other hand, due to the heat insulation effect of flux and slag, there is basically no heat radiation loss on the arc, and there is less spatter. Although the heat loss for melting flux increases, the overall thermal efficiency is still greatly increased.
(2) High weld quality
The slag has a good protective effect in insulating the air, the welding parameters can be kept stable through automatic adjustment, the technical level of the welder is not high, the weld composition is stable, and the mechanical properties are relatively good.
(3) Good working conditions
In addition to reducing the labor intensity of manual welding operations, it has no arc radiation, which is a unique advantage of submerged arc welding.
2. Argon arc welding
(1) Argon protection can isolate the adverse effects of oxygen, nitrogen, hydrogen, etc. in the air on the arc and molten pool, reduce the burning loss of alloying elements, and obtain dense, spatter-free, high-quality welded joints;
(2) The arc combustion of argon arc welding is stable, the heat is concentrated, the arc column temperature is high, the welding production efficiency is high, the heat affected zone is narrow, and the stress, deformation and crack tendency of the welded parts are small;
(3) Argon arc welding is open arc welding, which is convenient for operation and observation;
(4) The electrode loss is small, the arc length is easy to maintain, and there is no flux or coating layer during welding, so it is easy to realize mechanization and automation;
(5) Argon arc welding can weld almost all metals, especially some refractory metals and easily oxidized metals, such as magnesium, titanium, molybdenum, zirconium, aluminum, etc. and their alloys;
(6) It is not limited by the position of the weldment, and can be welded in all positions.
Disadvantages of argon arc welding
(1) Argon arc welding has a large heat-affected zone. After the pipe is repaired, it often causes defects such as deformation, hardness reduction, trachoma, local annealing, cracking, pinholes, wear, scratches, undercut, or insufficient bonding force and internal stress damage. Especially in the process of repairing small defects of precision steel pipes, it is prominent on the surface. In the field of repairing defects of precision steel pipes, cold welding machines can be used instead of argon arc welding. Due to the small heat release of cold welding machines, the shortcomings of argon arc welding are better overcome, and the repairing problems of precision castings are made up for.
(2) Argon arc welding is more harmful to human body. The current density of argon arc welding is high, and the light emitted is relatively strong. The ultraviolet radiation generated by its arc is about 5 to 30 times that of ordinary electrode arc welding, and the infrared radiation is about 1 to 1.5 times that of electrode arc welding. The ozone content generated during welding is relatively high, so try to choose a place with better air circulation for construction, otherwise it will cause great harm to the body.
(3) For metals with low melting point and easy evaporation (such as lead, tin, zinc), welding is more difficult.
Submerged arc welding is one of the mechanized welding methods with high production efficiency today. Its full name is submerged arc automatic welding, also known as automatic arc welding under flux layer. It is a welding method in which an arc burns under a flux layer. Its inherent advantages such as stable welding quality, high welding productivity, no arc light and little smoke make it the main welding method in the manufacture of important steel structures such as pressure vessels, pipe section manufacturing, and box-shaped beams and columns.
Argon arc welding technology is based on the principle of ordinary arc welding, using argon to protect the metal welding material, and through high current to melt the welding material into a liquid state on the base material to be welded to form a molten pool. A welding technique that achieves a metallurgical combination of the metal to be welded and the welding material. Since the argon gas is continuously supplied during high-temperature fusion welding, the welding material cannot be in contact with the oxygen in the air, thus preventing the oxidation of the welding material, so it can weld stainless steel and ferrous metals.
Tips: Because of its characteristics, submerged arc welding technology is often used in the manufacture of pipe sections. The welded steel tubes produced by submerged arc welding technology mainly include LSAW pipes and SSAW pipes.
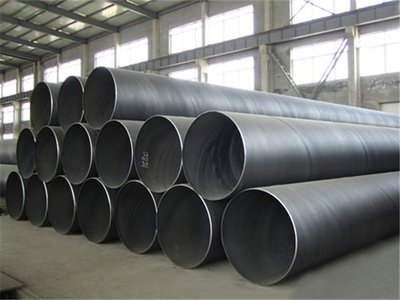
Features
1. Submerged arc welding
(1) High production efficiency
On the one hand, the conductive length of the welding wire is shortened, and the current and current density are increased, so the penetration depth of the arc and the deposition efficiency of the welding wire are greatly improved. On the other hand, due to the heat insulation effect of flux and slag, there is basically no heat radiation loss on the arc, and there is less spatter. Although the heat loss for melting flux increases, the overall thermal efficiency is still greatly increased.
(2) High weld quality
The slag has a good protective effect in insulating the air, the welding parameters can be kept stable through automatic adjustment, the technical level of the welder is not high, the weld composition is stable, and the mechanical properties are relatively good.
(3) Good working conditions
In addition to reducing the labor intensity of manual welding operations, it has no arc radiation, which is a unique advantage of submerged arc welding.
2. Argon arc welding
(1) Argon protection can isolate the adverse effects of oxygen, nitrogen, hydrogen, etc. in the air on the arc and molten pool, reduce the burning loss of alloying elements, and obtain dense, spatter-free, high-quality welded joints;
(2) The arc combustion of argon arc welding is stable, the heat is concentrated, the arc column temperature is high, the welding production efficiency is high, the heat affected zone is narrow, and the stress, deformation and crack tendency of the welded parts are small;
(3) Argon arc welding is open arc welding, which is convenient for operation and observation;
(4) The electrode loss is small, the arc length is easy to maintain, and there is no flux or coating layer during welding, so it is easy to realize mechanization and automation;
(5) Argon arc welding can weld almost all metals, especially some refractory metals and easily oxidized metals, such as magnesium, titanium, molybdenum, zirconium, aluminum, etc. and their alloys;
(6) It is not limited by the position of the weldment, and can be welded in all positions.
Disadvantages of argon arc welding
(1) Argon arc welding has a large heat-affected zone. After the pipe is repaired, it often causes defects such as deformation, hardness reduction, trachoma, local annealing, cracking, pinholes, wear, scratches, undercut, or insufficient bonding force and internal stress damage. Especially in the process of repairing small defects of precision steel pipes, it is prominent on the surface. In the field of repairing defects of precision steel pipes, cold welding machines can be used instead of argon arc welding. Due to the small heat release of cold welding machines, the shortcomings of argon arc welding are better overcome, and the repairing problems of precision castings are made up for.
(2) Argon arc welding is more harmful to human body. The current density of argon arc welding is high, and the light emitted is relatively strong. The ultraviolet radiation generated by its arc is about 5 to 30 times that of ordinary electrode arc welding, and the infrared radiation is about 1 to 1.5 times that of electrode arc welding. The ozone content generated during welding is relatively high, so try to choose a place with better air circulation for construction, otherwise it will cause great harm to the body.
(3) For metals with low melting point and easy evaporation (such as lead, tin, zinc), welding is more difficult.