The welded pipe is a steel pipe made of steel plate or strip steel after being crimped and welded, generally with a length of 6 meters. The production process of welded steel pipe is simple, the production efficiency is high, there are many varieties and specifications, and the investment in equipment is small, but the general strength is lower than that of seamless pipe. Welded pipes are widely used in construction, furniture, automobiles and other fields. As a kind of metal material, welded pipe has a crucial impact on its quality in the process of its production and manufacturing, the selection and implementation of the surface treatment method.
1. Surface treatment methods and common techniques
The surface treatment methods of steel are mainly divided into two categories: mechanical treatment and chemical treatment. Among them, mechanical treatment includes grinding wheel polishing, wire drawing, polishing and other methods; chemical treatment includes pickling, electroplating, spraying and other methods. One of the most common surface treatments for welded pipe is galvanizing. In addition, there are some other surface treatment methods, such as painting, spraying and so on.
2. The effect of surface treatment on the quality of welded pipes
(1) Anti-corrosion performance: The surface treatment method of the welded pipe has a direct impact on its anti-corrosion performance. Galvanized welded pipe has extremely strong corrosion resistance, which can effectively prolong its service life and maintenance cycle; while untreated welded pipe is susceptible to oxidation and corrosion due to its surface, resulting in damage and aging of the material.
(2) Appearance effect: The surface treatment method will also have a certain impact on the appearance effect of the welded pipe. For example, spraying and plastic spraying can decorate the welded pipe with various colors and patterns, so that it can better meet the needs of different environments and scenes.
(3) Processing performance: The surface treatment method will affect the processing performance of the welded pipe. For example, the surface of untreated welded pipes is prone to problems such as burrs and defects, which is very unfavorable for the component manufacturing industry that requires high-precision processing.
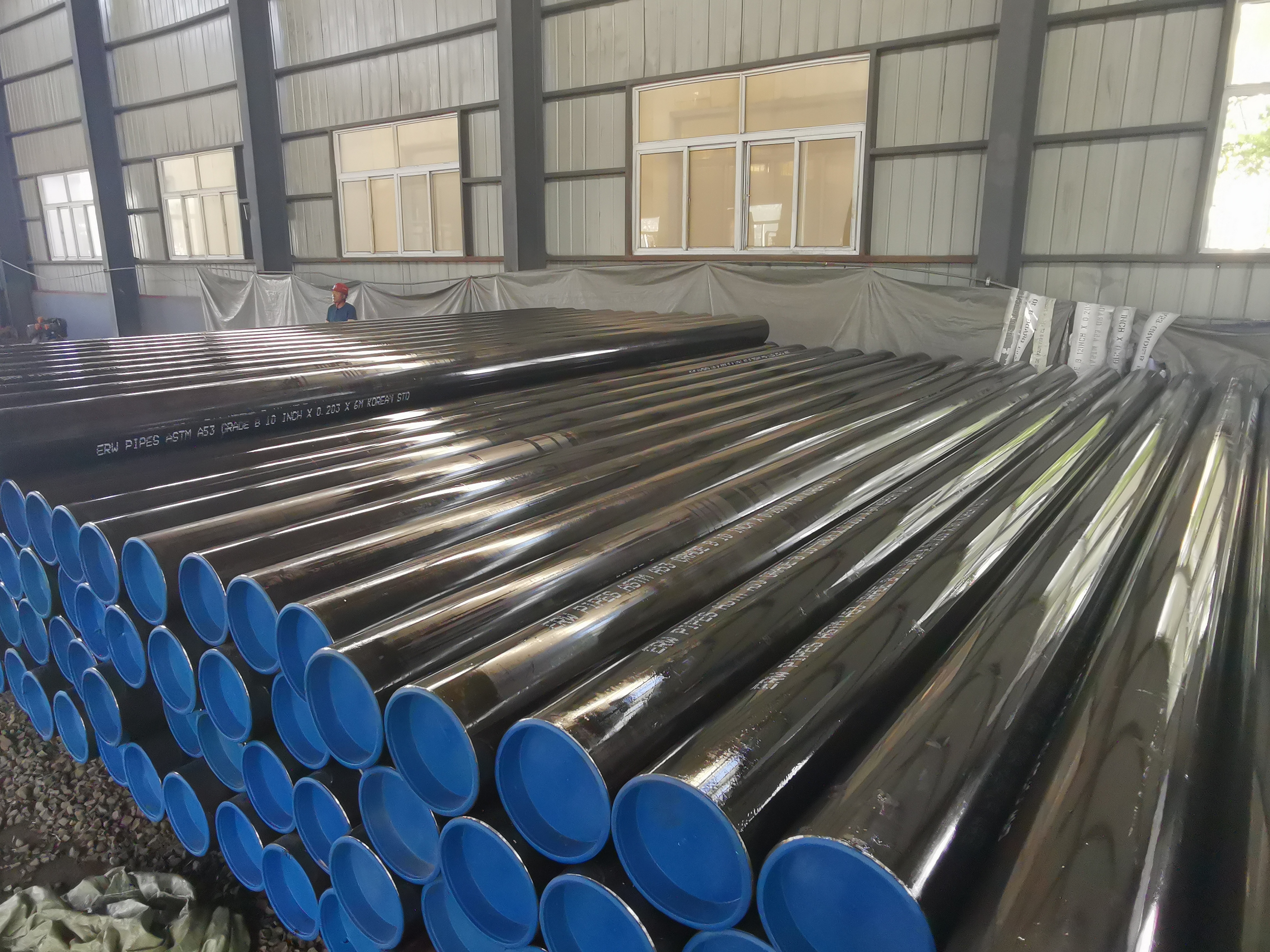
3. How to choose the appropriate surface treatment method
According to the specific application scenarios and usage requirements of welded pipes, it is very important to choose a suitable surface treatment method. The following points are factors to consider when choosing a surface treatment method:
(1) Anti-corrosion performance requirements of materials;
(2) Appearance effect requirements, including color, gloss, etc.;
(3) Processing performance requirements, such as flatness, surface quality, etc.
4. Conclusion
In short, the selection and implementation of welded pipe surface treatment methods have a direct impact on its quality. According to different application scenarios and usage requirements, choosing an appropriate surface treatment method can improve the anti-corrosion performance, aesthetics and processing performance of the welded pipe, thereby avoiding a series of problems. Therefore, in the production and manufacturing process of welded pipes, attention should be paid to the selection and implementation of surface treatment methods to ensure the stability and reliability of welded pipe quality.
1. Surface treatment methods and common techniques
The surface treatment methods of steel are mainly divided into two categories: mechanical treatment and chemical treatment. Among them, mechanical treatment includes grinding wheel polishing, wire drawing, polishing and other methods; chemical treatment includes pickling, electroplating, spraying and other methods. One of the most common surface treatments for welded pipe is galvanizing. In addition, there are some other surface treatment methods, such as painting, spraying and so on.
2. The effect of surface treatment on the quality of welded pipes
(1) Anti-corrosion performance: The surface treatment method of the welded pipe has a direct impact on its anti-corrosion performance. Galvanized welded pipe has extremely strong corrosion resistance, which can effectively prolong its service life and maintenance cycle; while untreated welded pipe is susceptible to oxidation and corrosion due to its surface, resulting in damage and aging of the material.
(2) Appearance effect: The surface treatment method will also have a certain impact on the appearance effect of the welded pipe. For example, spraying and plastic spraying can decorate the welded pipe with various colors and patterns, so that it can better meet the needs of different environments and scenes.
(3) Processing performance: The surface treatment method will affect the processing performance of the welded pipe. For example, the surface of untreated welded pipes is prone to problems such as burrs and defects, which is very unfavorable for the component manufacturing industry that requires high-precision processing.
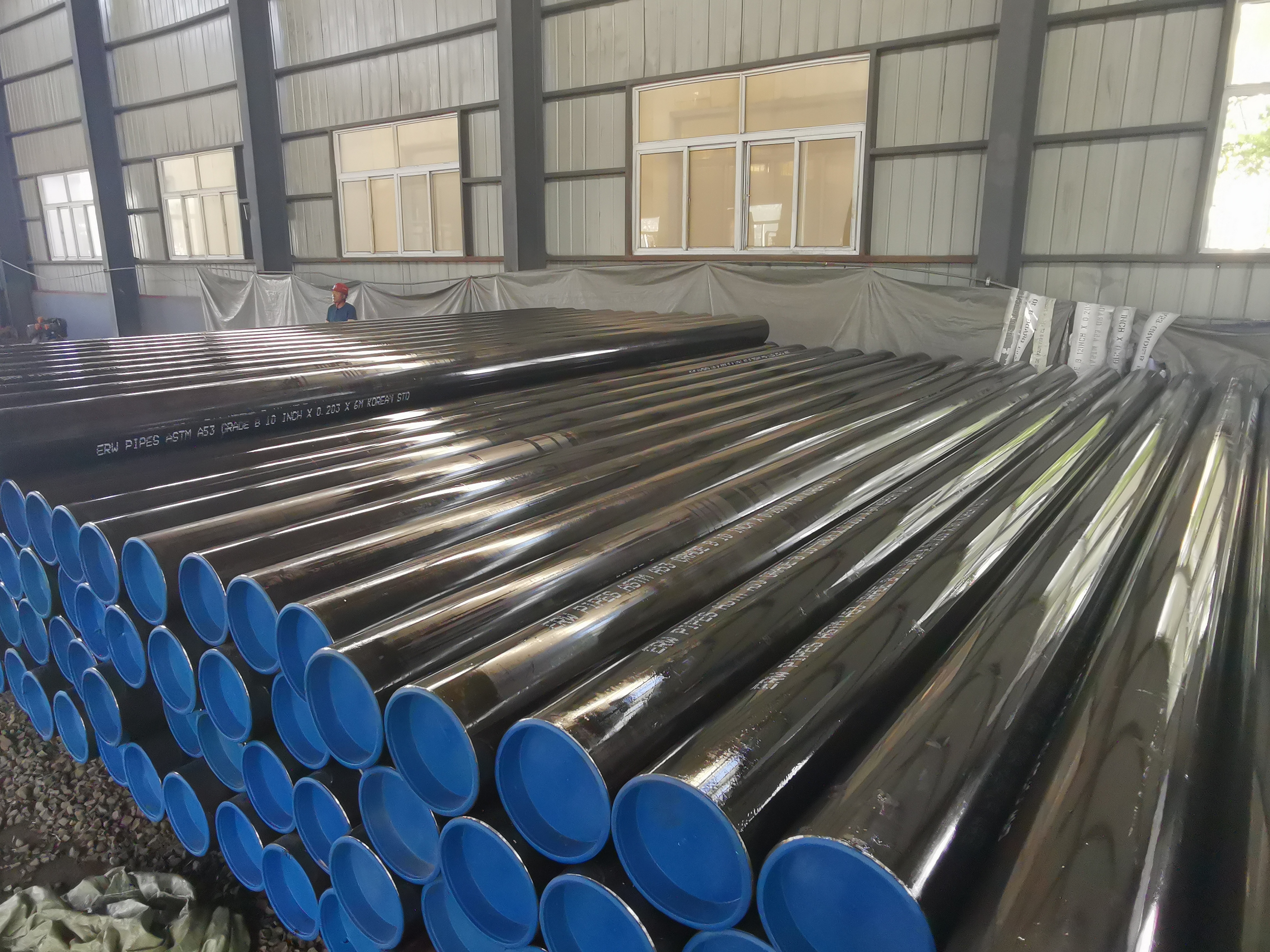
3. How to choose the appropriate surface treatment method
According to the specific application scenarios and usage requirements of welded pipes, it is very important to choose a suitable surface treatment method. The following points are factors to consider when choosing a surface treatment method:
(1) Anti-corrosion performance requirements of materials;
(2) Appearance effect requirements, including color, gloss, etc.;
(3) Processing performance requirements, such as flatness, surface quality, etc.
4. Conclusion
In short, the selection and implementation of welded pipe surface treatment methods have a direct impact on its quality. According to different application scenarios and usage requirements, choosing an appropriate surface treatment method can improve the anti-corrosion performance, aesthetics and processing performance of the welded pipe, thereby avoiding a series of problems. Therefore, in the production and manufacturing process of welded pipes, attention should be paid to the selection and implementation of surface treatment methods to ensure the stability and reliability of welded pipe quality.