UOE steel pipe forming process is one of the forming processes of LSAW steel pipe.The UOE production line adopts the Uing-Oing forming process. The formed steel pipe adopts five three-wire internal welding equipment and four three-wire external welding equipment.After welding, mechanical expansion or hydraulic expansion can be used to improve dimensional accuracy and remove internal stress according to user requirements.
The production process of UOE
Converter→refining→continuous casting→thick plate→steel plate loading→welding arc plate→rail edge→pre-bending→U forming→O forming→high pressure water washing→drying→pre-welding→internal welding→external welding→Removal of arc plate → ultrasonic inspection of weld seam and pipe end → X-ray inspection → steel pipe expansion → pipe end weld grinding → pipe end flat head → hydraulic test → ultrasonic inspection of weld seam and pipe end →X-ray inspection of weld seam and pipe end → chamfering → delamination of pipe end and magnetic particle inspection → residual magnetic demagnetization → factory inspection → weighing, length measurement → spray mark → upper protection ring → stacking and delivery.
The three main forming processes of UOE LSAW steel pipe forming process include: steel plate pre-bending, U forming and O forming. Each process uses a dedicated forming press to complete the three processes of steel plate edge pre-bending, U forming and 0 forming in turn, and deform the steel plate into a circular tube. Its advantages are: high degree of production automation, high productivity, excellent and stable product quality.
1. Steel plate edge pre-bending
The purpose of pre-bending the edge of the steel plate is to complete the pre-deformation of the two plate edges, so that the bending radius of the edge of the plate can reach or be close to the radius of the steel pipe specification produced, so as to ensure the geometric shape and dimensional accuracy of the welded seam area of the steel pipe.Avoid "pear-shaped" tube failure after O molding.
2.U molding
The steel plate with pre-bent edges enters the second forming process - U forming. After the steel plate is positioned on the U-forming press, the U-forming press moves down vertically with the die, and under the action of the lower support roller or the mold, the steel plate is bent and deformed into a U-shaped tube.
3. O molding
After the steel plate is deformed into a U-shaped tube, it enters the third main deformation process - O forming. In this process, the O-forming press is pressed down, and the deformation process of deforming the U-shaped tube into an O-shaped tube is completed. 0 The forming press is equipped with two bisected semi-cylindrical dies. After bending both sides of the U-shape, it is further deformed into an O-shape.A certain degree of compressive deformation is applied to control the elastic recovery while controlling the geometry after molding.
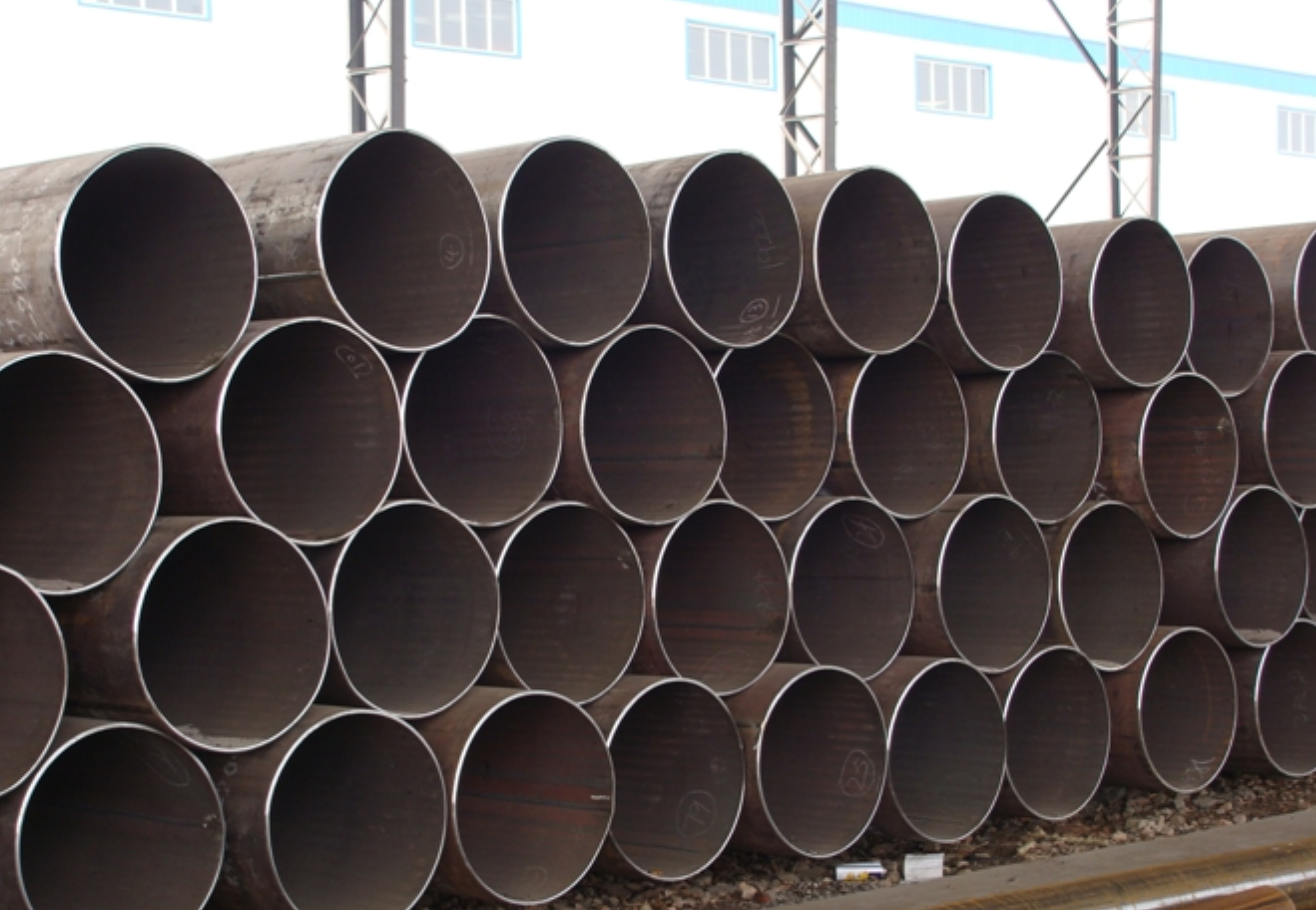
Production characteristics of UOE
(1) UOE has high production efficiency and large production capacity, and the replacement mold cycle is long, which is more suitable for the production of large batches and single specification products;
(2) UOE can produce a small range of product diameters and thicknesses.
(3) UOE line pipe has small residual stress, high dimensional accuracy and small yield-strength ratio.
(4) The one-time investment of the UOE production line is high, about 3 billion yuan.
Note: Due to the high cost of UOE production process, small production batch and poor flexibility. Nowadays, many LSAW manufacturers use JCOE production process instead of UOE.
The production process of UOE
Converter→refining→continuous casting→thick plate→steel plate loading→welding arc plate→rail edge→pre-bending→U forming→O forming→high pressure water washing→drying→pre-welding→internal welding→external welding→Removal of arc plate → ultrasonic inspection of weld seam and pipe end → X-ray inspection → steel pipe expansion → pipe end weld grinding → pipe end flat head → hydraulic test → ultrasonic inspection of weld seam and pipe end →X-ray inspection of weld seam and pipe end → chamfering → delamination of pipe end and magnetic particle inspection → residual magnetic demagnetization → factory inspection → weighing, length measurement → spray mark → upper protection ring → stacking and delivery.
The three main forming processes of UOE LSAW steel pipe forming process include: steel plate pre-bending, U forming and O forming. Each process uses a dedicated forming press to complete the three processes of steel plate edge pre-bending, U forming and 0 forming in turn, and deform the steel plate into a circular tube. Its advantages are: high degree of production automation, high productivity, excellent and stable product quality.
1. Steel plate edge pre-bending
The purpose of pre-bending the edge of the steel plate is to complete the pre-deformation of the two plate edges, so that the bending radius of the edge of the plate can reach or be close to the radius of the steel pipe specification produced, so as to ensure the geometric shape and dimensional accuracy of the welded seam area of the steel pipe.Avoid "pear-shaped" tube failure after O molding.
2.U molding
The steel plate with pre-bent edges enters the second forming process - U forming. After the steel plate is positioned on the U-forming press, the U-forming press moves down vertically with the die, and under the action of the lower support roller or the mold, the steel plate is bent and deformed into a U-shaped tube.
3. O molding
After the steel plate is deformed into a U-shaped tube, it enters the third main deformation process - O forming. In this process, the O-forming press is pressed down, and the deformation process of deforming the U-shaped tube into an O-shaped tube is completed. 0 The forming press is equipped with two bisected semi-cylindrical dies. After bending both sides of the U-shape, it is further deformed into an O-shape.A certain degree of compressive deformation is applied to control the elastic recovery while controlling the geometry after molding.
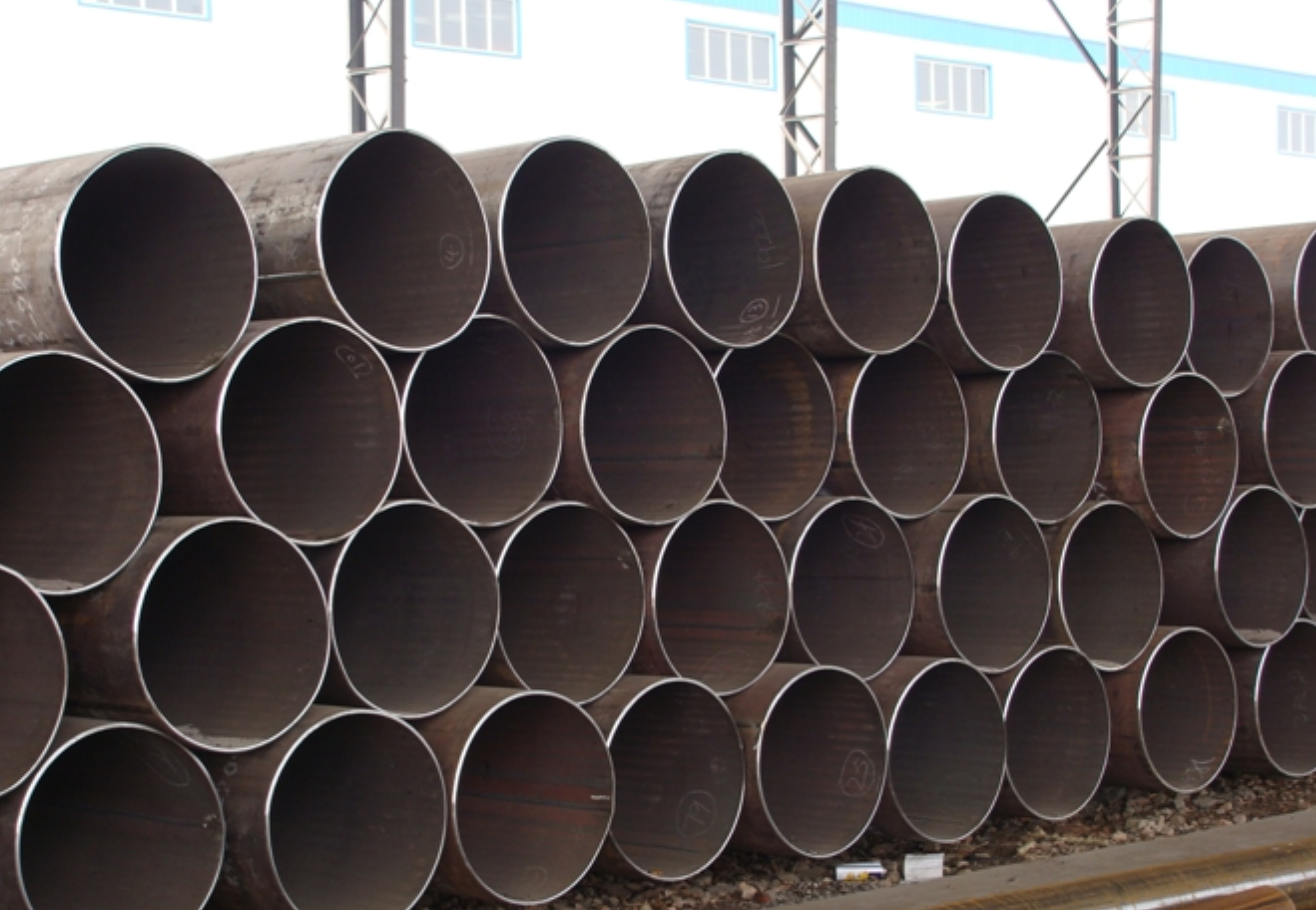
Production characteristics of UOE
(1) UOE has high production efficiency and large production capacity, and the replacement mold cycle is long, which is more suitable for the production of large batches and single specification products;
(2) UOE can produce a small range of product diameters and thicknesses.
(3) UOE line pipe has small residual stress, high dimensional accuracy and small yield-strength ratio.
(4) The one-time investment of the UOE production line is high, about 3 billion yuan.
Note: Due to the high cost of UOE production process, small production batch and poor flexibility. Nowadays, many LSAW manufacturers use JCOE production process instead of UOE.