Submerged arc welding technology is the welding process of SSAW steel pipe and LSAW steel pipe. During the welding process, in addition to insufficient penetration, burn-through and poor formation caused by improper welding process parameters, there will also be pores, slag inclusions, cracks, etc. Defects. This article mainly introduces the main reasons and preventive measures for porosity in submerged arc welding seams.
(1) In the process of steel rolling or hot stamping and coiling, the oxide scale formed or fallen off, as well as the positioning welding slag shell, the carbon arc gas created flying slag, etc., are trapped in the flux, which will also cause pores in the weld. Preventive measures:
① The oxide skin that falls off during the process of coiling and bending should be cleaned or blown off with compressed air before assembly and welding to prevent it from being caught in the assembly gap or falling into the groove.
② The surrounding of the welding site should be clean to prevent oxide skin, slag shell, carbon arc, and gas-induced flying slag from mixing with the flux. In the flux that is recycled and reused, the content of these impurities is often high, so it is necessary to mix new flux into the flux that has been reused many times.
(2) When the flux layer is too thin, the welding voltage is too high or the network voltage fluctuates greatly, the arc may pass through the flux layer, causing the molten pool metal to be polluted by the outside air and causing pores; when the flux particle size is too coarse, the air will pass through The flux layer contaminates the molten pool; when the assembly gap exceeds 0.8 mm in the suspension welding, it will cause deep pores in the weld. Preventive measures:
① The thickness of the flux layer should be appropriate to suit the welding specification, and the particle size of the flux should not be too thick to ensure that the continuous arc light is not exposed during the welding process.
② Suspended welding, especially when the thickness of the weldment is less than 20 mm, the assembly gap should not exceed 0.8-1 mm.
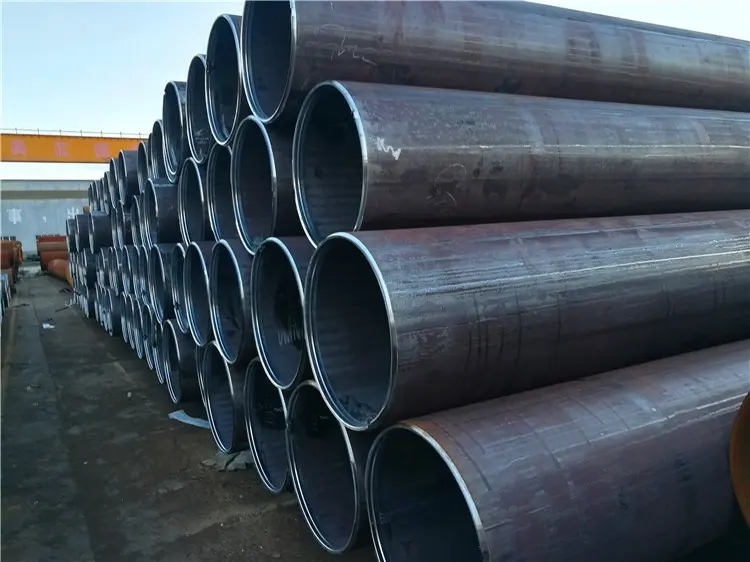
(3) The phenomenon of arc magnetic bias blowing often occurs in arc magnetic bias blowing welding, especially when DC welding is used. The porosity is more likely to appear in the closing area, the closer to the end of the weld, the more serious the porosity. The direction of magnetic deflection is affected by many factors, such as poor contact at the connection of the welding cable on the workpiece, and the secondary magnetic field caused by part of the welding cable wrapping around the joint, etc. Preventive measures:
① The fixture of the weldment is preferably made of non-magnetic conductive material.
② Leave a longer and thicker tack weld at the end
③ The connection position should be as far away as possible from the welding seam terminal.
④ Switch to alternating current.
(4) The rust, oil or other dirt around the welding groove of the workpiece is polluted, which will significantly increase the hydrogen content in the molten pool and cause pores. The method to prevent pores is to reduce the source of hydrogen and create Conditions for hydrogen to escape the molten pool:
① The flux should be dried strictly according to the regulations. If the weather is humid, the time it takes for the flux to be taken out of the oven to use should not be too long, and it is best to keep it warm at about 50 degrees for use. Recycled flux should avoid contamination by water, dust, etc.
② Strictly remove oil, rust and moisture within 20mm of both sides of welding wire and groove. The weldment should be assembled with the welding. If it is stained with water, the welding area should be baked and dried before welding.
③ The particle size of the flux should be appropriate, and the fine powder and ash should be screened out, so that the flux has a certain permeability and is conducive to the escape of gas.
(5) There are sulfur-rich layered segregation in the base metal, or there are delamination defects in the base metal, which will cause pores. When the base metal has high sulfur content and many sulfide inclusions, more gas will be generated during the welding process to form pores. Preventive measures:
① Control the welding specification and reduce the base metal fusion ratio. For example, use DC positive connection, small current or thick wire welding, and use multi-pass welding instead of single-pass welding.
② Appropriately reduce the welding speed and increase the time for the gas to escape from the molten pool.
③ Weld with welding wire with high manganese content, so that part of the sulfur forms manganese sulfide and is discharged into the slag.
④ If the original butt welding is without groove, it can be changed into V-groove welding, and the groove angle is larger than the commonly used groove angle.
⑤ If the porosity is caused by the delamination of the base metal (a defect that occurs when rolling the steel plate), the delamination should generally be removed and then re-welded.
(1) In the process of steel rolling or hot stamping and coiling, the oxide scale formed or fallen off, as well as the positioning welding slag shell, the carbon arc gas created flying slag, etc., are trapped in the flux, which will also cause pores in the weld. Preventive measures:
① The oxide skin that falls off during the process of coiling and bending should be cleaned or blown off with compressed air before assembly and welding to prevent it from being caught in the assembly gap or falling into the groove.
② The surrounding of the welding site should be clean to prevent oxide skin, slag shell, carbon arc, and gas-induced flying slag from mixing with the flux. In the flux that is recycled and reused, the content of these impurities is often high, so it is necessary to mix new flux into the flux that has been reused many times.
(2) When the flux layer is too thin, the welding voltage is too high or the network voltage fluctuates greatly, the arc may pass through the flux layer, causing the molten pool metal to be polluted by the outside air and causing pores; when the flux particle size is too coarse, the air will pass through The flux layer contaminates the molten pool; when the assembly gap exceeds 0.8 mm in the suspension welding, it will cause deep pores in the weld. Preventive measures:
① The thickness of the flux layer should be appropriate to suit the welding specification, and the particle size of the flux should not be too thick to ensure that the continuous arc light is not exposed during the welding process.
② Suspended welding, especially when the thickness of the weldment is less than 20 mm, the assembly gap should not exceed 0.8-1 mm.
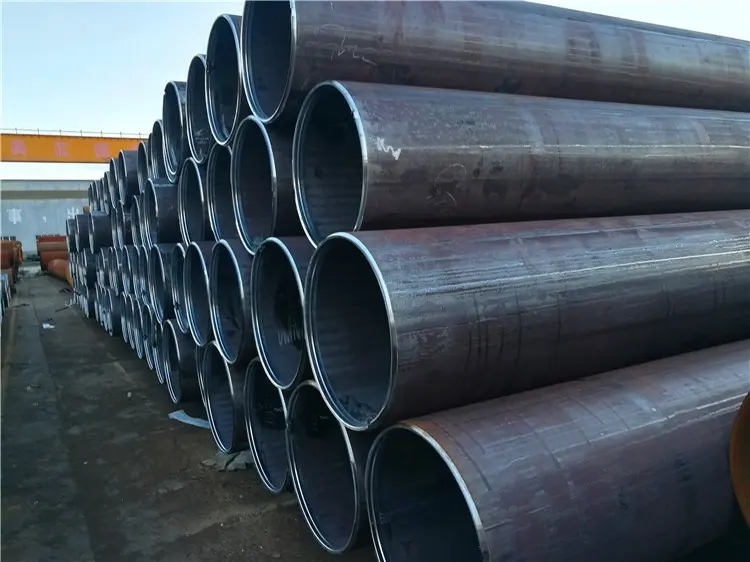
(3) The phenomenon of arc magnetic bias blowing often occurs in arc magnetic bias blowing welding, especially when DC welding is used. The porosity is more likely to appear in the closing area, the closer to the end of the weld, the more serious the porosity. The direction of magnetic deflection is affected by many factors, such as poor contact at the connection of the welding cable on the workpiece, and the secondary magnetic field caused by part of the welding cable wrapping around the joint, etc. Preventive measures:
① The fixture of the weldment is preferably made of non-magnetic conductive material.
② Leave a longer and thicker tack weld at the end
③ The connection position should be as far away as possible from the welding seam terminal.
④ Switch to alternating current.
(4) The rust, oil or other dirt around the welding groove of the workpiece is polluted, which will significantly increase the hydrogen content in the molten pool and cause pores. The method to prevent pores is to reduce the source of hydrogen and create Conditions for hydrogen to escape the molten pool:
① The flux should be dried strictly according to the regulations. If the weather is humid, the time it takes for the flux to be taken out of the oven to use should not be too long, and it is best to keep it warm at about 50 degrees for use. Recycled flux should avoid contamination by water, dust, etc.
② Strictly remove oil, rust and moisture within 20mm of both sides of welding wire and groove. The weldment should be assembled with the welding. If it is stained with water, the welding area should be baked and dried before welding.
③ The particle size of the flux should be appropriate, and the fine powder and ash should be screened out, so that the flux has a certain permeability and is conducive to the escape of gas.
(5) There are sulfur-rich layered segregation in the base metal, or there are delamination defects in the base metal, which will cause pores. When the base metal has high sulfur content and many sulfide inclusions, more gas will be generated during the welding process to form pores. Preventive measures:
① Control the welding specification and reduce the base metal fusion ratio. For example, use DC positive connection, small current or thick wire welding, and use multi-pass welding instead of single-pass welding.
② Appropriately reduce the welding speed and increase the time for the gas to escape from the molten pool.
③ Weld with welding wire with high manganese content, so that part of the sulfur forms manganese sulfide and is discharged into the slag.
④ If the original butt welding is without groove, it can be changed into V-groove welding, and the groove angle is larger than the commonly used groove angle.
⑤ If the porosity is caused by the delamination of the base metal (a defect that occurs when rolling the steel plate), the delamination should generally be removed and then re-welded.