Boiler tubes are seamless steel tube or welded steel tubes used to manufacture tubes and other components in boiler systems. They can withstand high temperature and high pressure working environments and are widely used in the transportation of media in boiler systems to achieve effective heat transfer and energy conversion. Depending on the conveying medium and the operating temperature, boiler tubes can be carbon steel, alloy steel or stainless steel.
Classification of boiler tubes
1. Classification by manufacturing process
Seamless boiler tube: This is the most common type of boiler tube. Since there is no welding of steel pipes, the overall force is more uniform, and it is widely used in large boiler systems, especially equipment with high requirements for pipeline pressure and temperature.
Welded boiler tube: Usually made of explosive remnants of war. This process is relatively cheap and suitable for some boiler systems with low pressure requirements.
2. Classification by material
Carbon steel boiler tubes: the most common boiler tubes, usually used in low-pressure boiler systems, have good strength and toughness, but are easily oxidized and corroded, and are suitable for environments with low temperature and pressure.
Alloy steel boiler tubes: They have strong high temperature resistance and corrosion resistance, and are suitable for medium and high pressure boiler systems, especially in high temperature and harsh environments.
Stainless steel boiler tubes: They have excellent corrosion resistance, suitable for conveying corrosive media, and are usually used under harsh temperature and pressure conditions.
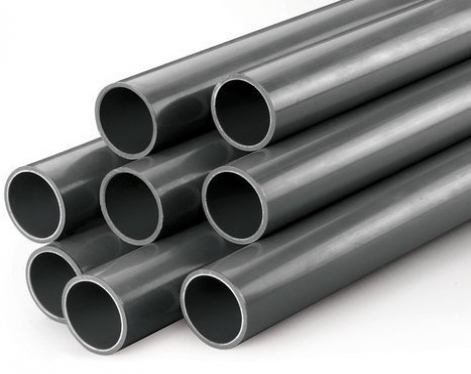
Advantages of boiler tubes
1. High pressure and high temperature performance
As a key component of the boiler, the boiler tube needs to work stably under extreme conditions of high temperature and high pressure. Common high-pressure boiler tubes such as 20G, 15CrMoG, 12Cr1MoVG, etc. have excellent pressure resistance and high temperature resistance.
2. Good corrosion resistance
During boiler operation, boiler tubes will be exposed to various corrosive media, such as sulfides and water vapor in high-temperature flue gas. However, boiler tubes have good corrosion resistance due to their special materials and surface treatment technology.
3. Recycling value and environmental advantages
Boiler tubes are mostly made of alloy materials and are recyclable. When boiler tubes reach the end of their service life, they can be processed through professional recycling processes and put back into production, which is in line with the current concept of environmental protection and conservation.
Disadvantages of boiler tubes
1. Defects caused by manufacturing process
Taking hot-rolled boiler tubes as an example, their manufacturing process has certain limitations. During the hot rolling process, non-metallic inclusions (such as sulfides, oxides and silicates) inside the steel are pressed into thin sheets, resulting in delamination, which greatly deteriorates the tensile performance of the boiler tube along the thickness direction, and may also cause interlayer tearing when the weld shrinks.
2. Corrosion problems during operation
Boiler tubes face multiple corrosion threats during operation. High-temperature sulfur corrosion is prone to occur in the water-cooled wall, mainly because the pyrite (FeS₂) in the coal powder melts in the furnace, and the incompletely burned part falls back to the surface of the water-cooled wall, decomposes under heat to produce free sulfur atoms, which react with the iron in the tube wall to form porous ferrous sulfide, causing corrosion to continue to extend to the inside of the tube wall, eventually leading to the explosion of the water-cooled wall.
3. Installation and processing defects
Problems are also prone to occur during the installation and processing of boiler tubes. In the welding process, due to improper operation of welders and poor quality of welding materials, the weld quality will be unqualified, and welding defects, pores, slag inclusions and other problems will occur, seriously affecting the sealing and reliability of the pipeline.
Read more: Advantages and Disadvantages of Seamless Boiler Tubes
Classification of boiler tubes
1. Classification by manufacturing process
Seamless boiler tube: This is the most common type of boiler tube. Since there is no welding of steel pipes, the overall force is more uniform, and it is widely used in large boiler systems, especially equipment with high requirements for pipeline pressure and temperature.
Welded boiler tube: Usually made of explosive remnants of war. This process is relatively cheap and suitable for some boiler systems with low pressure requirements.
2. Classification by material
Carbon steel boiler tubes: the most common boiler tubes, usually used in low-pressure boiler systems, have good strength and toughness, but are easily oxidized and corroded, and are suitable for environments with low temperature and pressure.
Alloy steel boiler tubes: They have strong high temperature resistance and corrosion resistance, and are suitable for medium and high pressure boiler systems, especially in high temperature and harsh environments.
Stainless steel boiler tubes: They have excellent corrosion resistance, suitable for conveying corrosive media, and are usually used under harsh temperature and pressure conditions.
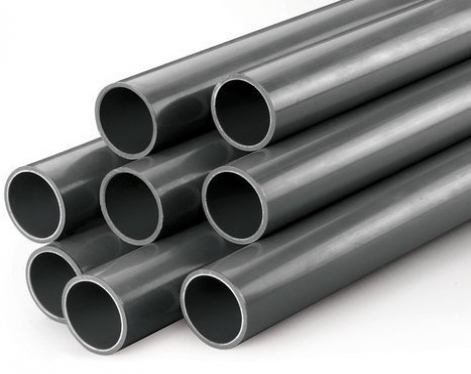
Advantages of boiler tubes
1. High pressure and high temperature performance
As a key component of the boiler, the boiler tube needs to work stably under extreme conditions of high temperature and high pressure. Common high-pressure boiler tubes such as 20G, 15CrMoG, 12Cr1MoVG, etc. have excellent pressure resistance and high temperature resistance.
2. Good corrosion resistance
During boiler operation, boiler tubes will be exposed to various corrosive media, such as sulfides and water vapor in high-temperature flue gas. However, boiler tubes have good corrosion resistance due to their special materials and surface treatment technology.
3. Recycling value and environmental advantages
Boiler tubes are mostly made of alloy materials and are recyclable. When boiler tubes reach the end of their service life, they can be processed through professional recycling processes and put back into production, which is in line with the current concept of environmental protection and conservation.
Disadvantages of boiler tubes
1. Defects caused by manufacturing process
Taking hot-rolled boiler tubes as an example, their manufacturing process has certain limitations. During the hot rolling process, non-metallic inclusions (such as sulfides, oxides and silicates) inside the steel are pressed into thin sheets, resulting in delamination, which greatly deteriorates the tensile performance of the boiler tube along the thickness direction, and may also cause interlayer tearing when the weld shrinks.
2. Corrosion problems during operation
Boiler tubes face multiple corrosion threats during operation. High-temperature sulfur corrosion is prone to occur in the water-cooled wall, mainly because the pyrite (FeS₂) in the coal powder melts in the furnace, and the incompletely burned part falls back to the surface of the water-cooled wall, decomposes under heat to produce free sulfur atoms, which react with the iron in the tube wall to form porous ferrous sulfide, causing corrosion to continue to extend to the inside of the tube wall, eventually leading to the explosion of the water-cooled wall.
3. Installation and processing defects
Problems are also prone to occur during the installation and processing of boiler tubes. In the welding process, due to improper operation of welders and poor quality of welding materials, the weld quality will be unqualified, and welding defects, pores, slag inclusions and other problems will occur, seriously affecting the sealing and reliability of the pipeline.
Read more: Advantages and Disadvantages of Seamless Boiler Tubes