The corrosion resistance of galvanized seamless steel pipe depends on many factors, the most critical of which are the quality of the zinc coating itself and the corrosive environment. In general, galvanizing provides a certain degree of corrosion protection, but its effect is far less than that of stainless steel or professional heavy-duty anti-corrosion coatings. Nansteel Manufacturing Co., Ltd carefully summarizes the corrosion resistance characteristics of galvanized seamless steel pipe and the factors that affect the corrosion resistance of galvanized seamless steel pipe.
The basic principle of galvanizing anti-corrosion
Galvanizing protects against corrosion primarily through two mechanisms:
Physical barrier protection: The zinc layer acts as a physical barrier between the steel pipe substrate and the corrosive medium, preventing oxygen, moisture and other corrosive substances from directly contacting the steel, thereby delaying corrosion.
Electrochemical sacrificial anode protection: Zinc is more active than iron. When the galvanized layer is scratched or damaged, the exposed steel and zinc will form a micro-battery. At this time, the zinc will corrode preferentially as a sacrificial anode, thereby protecting the steel substrate from rusting.
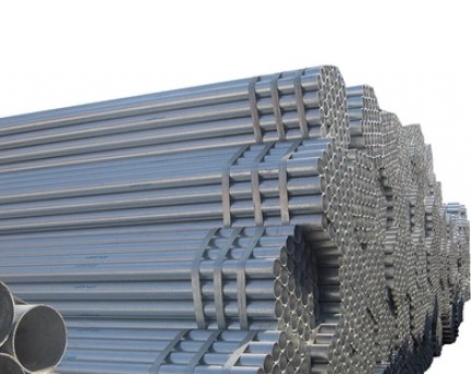
Corrosion resistance characteristics of galvanized seamless steel pipe
1. Hot-dip galvanized seamless steel pipe (more common and has good corrosion resistance)
Zinc layer thickness: Hot-dip galvanizing is formed by immersing the steel pipe in molten zinc liquid. The zinc layer thickness is usually thick (up to 60-600 g/m²) and forms a zinc-iron alloy layer with strong adhesion to the steel substrate.
Corrosion resistance: In the atmospheric environment, hot-dip galvanized seamless steel pipes have good corrosion resistance. The surface of the zinc layer will react with oxygen, carbon dioxide and water vapor in the air to form a dense and stable basic zinc carbonate protective film ("white rust"), which further prevents corrosion. In general industrial and urban atmospheric environments, its service life can reach several years or even decades.
limitation:
Strong acid and strong alkaline environment: The corrosion rate of zinc will be significantly accelerated in strong acid (pH < 6) or strong alkaline (pH > 12) environment, so it is not suitable.
Humid, oxygen-free, and closed environments: In a humid and poorly ventilated closed space, the zinc layer may undergo rapid "white rust" corrosion, resulting in the inability to form a protective film or its destruction.
High temperature environment: High temperature will accelerate the oxidation and volatilization of the zinc layer, reducing the anti-corrosion effect.
Wear: If the zinc layer falls off over a large area due to mechanical wear, the steel pipe substrate will lose protection.
Water quality: In certain water qualities (such as high chloride ion, high hardness, or oxygen-rich and slow-flowing water), the zinc coating may also accelerate corrosion.
2. Cold-dip galvanized seamless steel pipe (poor corrosion resistance, not commonly used)
Zinc layer thickness: The zinc layer of cold-dip galvanizing (electro-galvanizing) is very thin (usually 10-50 g/m²) and has relatively poor adhesion, and mainly serves an aesthetic purpose.
Corrosion resistance: Its anti-corrosion ability is very limited, and it will quickly fail in a corrosive environment, exposing the steel matrix and rusting. Many engineering specifications and standards have explicitly prohibited the use of cold-dip galvanized steel pipes in important anti-corrosion occasions.
Other factors affecting the corrosion resistance of galvanized seamless steel pipe
Environmental humidity and temperature: Corrosion is usually more severe in environments with high humidity and large temperature changes.
Air pollution: Areas with high levels of pollutants such as sulfur dioxide and chloride in the air are more corrosive.
Medium properties: The pH value, oxygen content, flow rate and impurity content of the conveying fluid will affect the corrosion rate.
Damage to the galvanized layer: Scratches and bumps during transportation and installation will damage the zinc layer and affect the anti-corrosion effect.
Conclusion
Galvanized seamless steel pipe (especially hot-dip galvanized) has a certain corrosion resistance in conventional atmospheric environment and neutral water, and can meet many general needs. However, it is not suitable for harsh corrosive environments such as strong acid, strong alkali, high temperature, high wear or high chloride ion. In these cases, it is necessary to choose a higher level of anti-corrosion solution, such as stainless steel seamless steel pipe, coating anti-corrosion (such as 3PE, epoxy resin) or lining anti-corrosion (such as plastic lining, rubber lining) seamless steel pipe.
When purchasing galvanized seamless steel pipes, be sure to clarify whether they are hot-dip galvanized or cold-dip galvanized, and uate whether their anti-corrosion ability meets the requirements based on the actual use environment.
Read more: Differences between Seamless Steel Pipes and Galvanized Pipes
The basic principle of galvanizing anti-corrosion
Galvanizing protects against corrosion primarily through two mechanisms:
Physical barrier protection: The zinc layer acts as a physical barrier between the steel pipe substrate and the corrosive medium, preventing oxygen, moisture and other corrosive substances from directly contacting the steel, thereby delaying corrosion.
Electrochemical sacrificial anode protection: Zinc is more active than iron. When the galvanized layer is scratched or damaged, the exposed steel and zinc will form a micro-battery. At this time, the zinc will corrode preferentially as a sacrificial anode, thereby protecting the steel substrate from rusting.
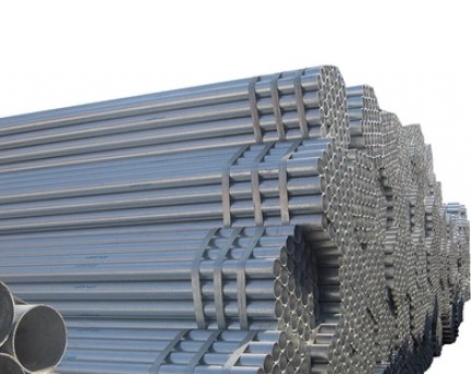
Corrosion resistance characteristics of galvanized seamless steel pipe
1. Hot-dip galvanized seamless steel pipe (more common and has good corrosion resistance)
Zinc layer thickness: Hot-dip galvanizing is formed by immersing the steel pipe in molten zinc liquid. The zinc layer thickness is usually thick (up to 60-600 g/m²) and forms a zinc-iron alloy layer with strong adhesion to the steel substrate.
Corrosion resistance: In the atmospheric environment, hot-dip galvanized seamless steel pipes have good corrosion resistance. The surface of the zinc layer will react with oxygen, carbon dioxide and water vapor in the air to form a dense and stable basic zinc carbonate protective film ("white rust"), which further prevents corrosion. In general industrial and urban atmospheric environments, its service life can reach several years or even decades.
limitation:
Strong acid and strong alkaline environment: The corrosion rate of zinc will be significantly accelerated in strong acid (pH < 6) or strong alkaline (pH > 12) environment, so it is not suitable.
Humid, oxygen-free, and closed environments: In a humid and poorly ventilated closed space, the zinc layer may undergo rapid "white rust" corrosion, resulting in the inability to form a protective film or its destruction.
High temperature environment: High temperature will accelerate the oxidation and volatilization of the zinc layer, reducing the anti-corrosion effect.
Wear: If the zinc layer falls off over a large area due to mechanical wear, the steel pipe substrate will lose protection.
Water quality: In certain water qualities (such as high chloride ion, high hardness, or oxygen-rich and slow-flowing water), the zinc coating may also accelerate corrosion.
2. Cold-dip galvanized seamless steel pipe (poor corrosion resistance, not commonly used)
Zinc layer thickness: The zinc layer of cold-dip galvanizing (electro-galvanizing) is very thin (usually 10-50 g/m²) and has relatively poor adhesion, and mainly serves an aesthetic purpose.
Corrosion resistance: Its anti-corrosion ability is very limited, and it will quickly fail in a corrosive environment, exposing the steel matrix and rusting. Many engineering specifications and standards have explicitly prohibited the use of cold-dip galvanized steel pipes in important anti-corrosion occasions.
Other factors affecting the corrosion resistance of galvanized seamless steel pipe
Environmental humidity and temperature: Corrosion is usually more severe in environments with high humidity and large temperature changes.
Air pollution: Areas with high levels of pollutants such as sulfur dioxide and chloride in the air are more corrosive.
Medium properties: The pH value, oxygen content, flow rate and impurity content of the conveying fluid will affect the corrosion rate.
Damage to the galvanized layer: Scratches and bumps during transportation and installation will damage the zinc layer and affect the anti-corrosion effect.
Conclusion
Galvanized seamless steel pipe (especially hot-dip galvanized) has a certain corrosion resistance in conventional atmospheric environment and neutral water, and can meet many general needs. However, it is not suitable for harsh corrosive environments such as strong acid, strong alkali, high temperature, high wear or high chloride ion. In these cases, it is necessary to choose a higher level of anti-corrosion solution, such as stainless steel seamless steel pipe, coating anti-corrosion (such as 3PE, epoxy resin) or lining anti-corrosion (such as plastic lining, rubber lining) seamless steel pipe.
When purchasing galvanized seamless steel pipes, be sure to clarify whether they are hot-dip galvanized or cold-dip galvanized, and uate whether their anti-corrosion ability meets the requirements based on the actual use environment.
Read more: Differences between Seamless Steel Pipes and Galvanized Pipes