What is a seamless tube?
Seamless tubes and boiler tubes play a vital role in industrial production. Although they are similar in appearance, they have significant differences in use, production process and technical requirements. This article will deeply analyze the differences between the two and the differences in production process from multiple dimensions. Seamless steel tube is a steel tube without seams along the perimeter of its cross section. It is widely used in many fields such as petroleum geological drilling, petrochemical, boiler manufacturing, bearing manufacturing, and aerospace due to its hollow cross-section, high bending and torsional strength, and light weight.
Production process of seamless steel tube
The production of seamless tubes mainly goes through the following key steps:
1. Tube preparation: Select standard steel ingots or solid tubes as raw materials.
2. Heating: Heat the tube to an appropriate temperature to improve its plasticity for subsequent processing.
3. Punching: The heated tube blank is punched into a rough tube by a punching machine to form a preliminary hollow structure.
4. Rolling/Extrusion/Cold Drawing: Depending on the production process, the rough tube is hot rolled, cold rolled, cold drawn or extruded to achieve the required size and shape. Hot rolled seamless steel tubes are rolled through a rolling mill at high temperature, with high production efficiency and low cost; cold rolled and cold drawn seamless steel tubes are processed at room temperature, with higher precision and smoother surface.
5. Heat treatment: Through normalizing, annealing, quenching and other heat treatment methods, the residual stress inside the steel pipe can be eliminated and its organizational properties can be improved.
6. Finishing and inspection: Finishing work such as straightening, head cutting, tail cutting, surface treatment, etc. is carried out on the finished steel pipes, and strict quality inspection is carried out to ensure that the products meet the standards.
What is a boiler tube?
Boiler tubes are steel tubes specially used to manufacture boiler heating surface tubes. They work in harsh environments and need to withstand high temperatures, high pressures, and corrosive media. Therefore, boiler tubes have extremely strict requirements on materials, production processes, and quality control. Boiler tubes are mostly made of seamless steel tubes or welded steel tubes, and are mostly made of carbon steel, alloy steel, etc.
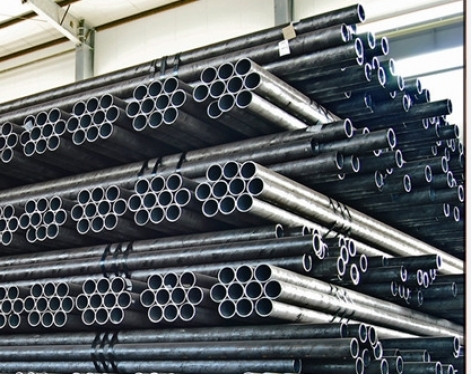
Boiler tube production process
The production process of boiler tubes is similar to that of seamless tubes, but it also has its own unique features:
1. Material selection: The selection of materials for boiler tubes must take into account the working environment and usage requirements to ensure that the material has sufficient strength, toughness, high temperature resistance and corrosion resistance.
2. Forming: Similar to seamless tubes, boiler tubes can also be formed by hot rolling, cold drawing, extrusion, etc. However, boiler tubes have higher requirements for dimensional accuracy and surface quality, so various parameters must be strictly controlled during the forming process.
3. Welding: Welding is required during the production process of boiler tubes. The quality of welding directly affects the use effect and safety of boiler tubes. Common welding methods include manual arc welding, submerged arc welding, TIG welding, etc. Appropriate welding materials and processes must be selected to ensure the quality of the weld.
4. Heat treatment: Like seamless tubes, boiler tubes also need to undergo heat treatment to eliminate residual stress and improve mechanical properties and corrosion resistance.
5. Inspection and surface treatment: Boiler tubes must undergo strict appearance inspection, size inspection, mechanical property inspection and metallographic structure inspection to ensure product quality. At the same time, surface treatment is also required to remove impurities such as oil and rust on the surface to improve corrosion resistance and service life.
Summary of the differences
1. Different uses: Seamless tubes are widely used in many industrial fields, while boiler tubes are dedicated to boiler manufacturing and have a special working environment.
2. Different technical requirements: Boiler tubes have harsh working environments and therefore have higher requirements on material, dimensional accuracy, surface quality and mechanical properties.
3. The production process focuses on different aspects: the production of seamless steel tubes focuses on improving production efficiency and reducing costs; while the production of boiler tubes pays more attention to quality control and safety performance.
In summary, there are significant differences between seamless tubes and boiler tubes in terms of use, technical requirements and production processes. Understanding these differences will help us better select and use these two types of steel pipe products to ensure their effective application in their respective fields.
Read more: Production and Classification of Boiler Tubes
Seamless tubes and boiler tubes play a vital role in industrial production. Although they are similar in appearance, they have significant differences in use, production process and technical requirements. This article will deeply analyze the differences between the two and the differences in production process from multiple dimensions. Seamless steel tube is a steel tube without seams along the perimeter of its cross section. It is widely used in many fields such as petroleum geological drilling, petrochemical, boiler manufacturing, bearing manufacturing, and aerospace due to its hollow cross-section, high bending and torsional strength, and light weight.
Production process of seamless steel tube
The production of seamless tubes mainly goes through the following key steps:
1. Tube preparation: Select standard steel ingots or solid tubes as raw materials.
2. Heating: Heat the tube to an appropriate temperature to improve its plasticity for subsequent processing.
3. Punching: The heated tube blank is punched into a rough tube by a punching machine to form a preliminary hollow structure.
4. Rolling/Extrusion/Cold Drawing: Depending on the production process, the rough tube is hot rolled, cold rolled, cold drawn or extruded to achieve the required size and shape. Hot rolled seamless steel tubes are rolled through a rolling mill at high temperature, with high production efficiency and low cost; cold rolled and cold drawn seamless steel tubes are processed at room temperature, with higher precision and smoother surface.
5. Heat treatment: Through normalizing, annealing, quenching and other heat treatment methods, the residual stress inside the steel pipe can be eliminated and its organizational properties can be improved.
6. Finishing and inspection: Finishing work such as straightening, head cutting, tail cutting, surface treatment, etc. is carried out on the finished steel pipes, and strict quality inspection is carried out to ensure that the products meet the standards.
What is a boiler tube?
Boiler tubes are steel tubes specially used to manufacture boiler heating surface tubes. They work in harsh environments and need to withstand high temperatures, high pressures, and corrosive media. Therefore, boiler tubes have extremely strict requirements on materials, production processes, and quality control. Boiler tubes are mostly made of seamless steel tubes or welded steel tubes, and are mostly made of carbon steel, alloy steel, etc.
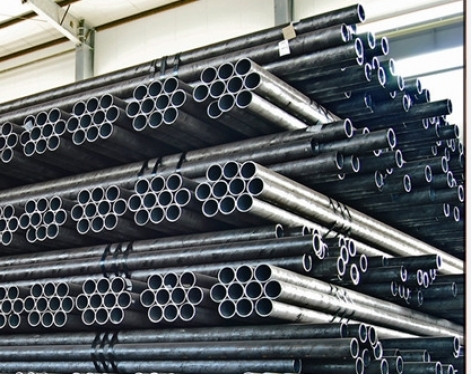
Boiler tube production process
The production process of boiler tubes is similar to that of seamless tubes, but it also has its own unique features:
1. Material selection: The selection of materials for boiler tubes must take into account the working environment and usage requirements to ensure that the material has sufficient strength, toughness, high temperature resistance and corrosion resistance.
2. Forming: Similar to seamless tubes, boiler tubes can also be formed by hot rolling, cold drawing, extrusion, etc. However, boiler tubes have higher requirements for dimensional accuracy and surface quality, so various parameters must be strictly controlled during the forming process.
3. Welding: Welding is required during the production process of boiler tubes. The quality of welding directly affects the use effect and safety of boiler tubes. Common welding methods include manual arc welding, submerged arc welding, TIG welding, etc. Appropriate welding materials and processes must be selected to ensure the quality of the weld.
4. Heat treatment: Like seamless tubes, boiler tubes also need to undergo heat treatment to eliminate residual stress and improve mechanical properties and corrosion resistance.
5. Inspection and surface treatment: Boiler tubes must undergo strict appearance inspection, size inspection, mechanical property inspection and metallographic structure inspection to ensure product quality. At the same time, surface treatment is also required to remove impurities such as oil and rust on the surface to improve corrosion resistance and service life.
Summary of the differences
1. Different uses: Seamless tubes are widely used in many industrial fields, while boiler tubes are dedicated to boiler manufacturing and have a special working environment.
2. Different technical requirements: Boiler tubes have harsh working environments and therefore have higher requirements on material, dimensional accuracy, surface quality and mechanical properties.
3. The production process focuses on different aspects: the production of seamless steel tubes focuses on improving production efficiency and reducing costs; while the production of boiler tubes pays more attention to quality control and safety performance.
In summary, there are significant differences between seamless tubes and boiler tubes in terms of use, technical requirements and production processes. Understanding these differences will help us better select and use these two types of steel pipe products to ensure their effective application in their respective fields.
Read more: Production and Classification of Boiler Tubes