ERW pipe, short for Electric Resistance Welded steel pipe, is known for its high production efficiency, cost-effectiveness, material conservation, and ease of automation. Due to these advantages, it finds widespread application across various industries, including aerospace, aviation, energy, electronics, automotive, and light manufacturing sectors.
SAW (Submerged Arc Welded) pipe is a steel pipe made using a welding process where the arc is submerged under a layer of flux. This method ensures deep weld penetration and high-quality seams. SAW pipes come in two main types: LSAW (longitudinal) and SSAW (spiral). Known for their strength, durability, and ability to handle large diameters, SAW pipes are widely used in oil and gas pipelines, water transmission, and structural applications. Their consistent weld quality makes them ideal for high-pressure, long-distance, and heavy-duty industrial projects.
ERW vs SAW Pipe: Key Differences
When choosing between ERW (Electric Resistance Welded) pipes and SAW (Submerged Arc Welded) pipes, understanding the key differences is crucial for ensuring performance, durability, and cost-efficiency. Here’s a breakdown of the main distinctions based on manufacturing, size, strength, and application suitability.
1. Manufacturing process:
ERW (Electric Resistance Welded) pipes are produced by joining the edges of a steel strip using high-frequency electrical current, creating a continuous weld along the seam. This method is highly efficient and results in a smooth, uniform surface. On the other hand, SAW (Submerged Arc Welded) pipes are manufactured using a welding process that occurs beneath a layer of flux, which shields the weld zone and ensures deep penetration. SAW pipes come in two main forms—LSAW (Longitudinal Submerged Arc Welded) and SSAW (Spiral Submerged Arc Welded)—making them ideal for applications requiring larger diameters and thicker walls.
2. Pipe Size & Wall Thickness
ERW pipes typically come in smaller diameters (up to 24 inches) with moderate wall thickness, making them suitable for structural use and low-pressure systems. In contrast, SAW pipes can reach diameters up to 100 inches with thicker walls, ideal for heavy-duty applications like offshore and long-distance pipelines.
3. Pressure Handling Capability
SAW pipes, particularly LSAW, provide superior pressure resistance thanks to their thicker walls and deeper welds. ERW pipes, on the other hand, are more suitable for low to medium pressure applications like water supply and scaffolding.
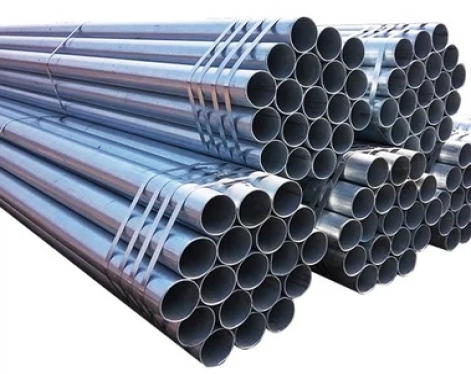
4. Cost and Efficiency
ERW pipes are more economical for small to medium projects, offering faster production and up to 20–30% lower material costs. SAW pipes, though more expensive, are essential for large-diameter, high-strength applications where durability is critical.
5. Weld Strength and Quality
SAW pipes offer greater weld strength and consistency due to their controlled welding process and deeper penetration. While ERW pipes have clean, uniform welds, they may not provide the same level of strength required for high-pressure or critical pipeline systems.
6. Surface Quality
ERW pipes offer a smoother, more uniform surface due to cold-forming and precise welding, making them ideal for visible or coated applications. SAW pipes, especially SSAW, may have a rougher finish with external weld beads, often requiring additional surface treatment for enhanced appearance or corrosion protection.
7. Weld Defect
ERW pipes may have minor weld defects like hook cracks or cold welds if not properly controlled, but modern techniques minimize these risks. SAW pipes, with deeper weld penetration and controlled conditions, generally have fewer internal defects, making them more reliable for high-pressure use.
Conclusion
When comparing ERW and SAW pipes, the right choice depends on your application needs. ERW pipes, made using high-frequency electric resistance welding, are ideal for small to medium diameters and low to medium pressure systems. They offer smooth surfaces, consistent seams, and are cost-effective for structural and general-purpose use. However, their weld strength may be limited for high-pressure demands.
SAW pipes—including LSAW and SSAW—are manufactured with submerged arc welding, enabling deeper welds and stronger joints. They support larger diameters and thicker walls, making them suitable for high-pressure, long-distance, and heavy-duty applications. Although more expensive and less smooth in surface finish, SAW pipes provide superior weld integrity and fewer defects.
In summary, choose ERW for budget-friendly, light-duty needs and SAW for robust, high-performance projects.
Read more: ERW Pipe VS. CEW Pipe
SAW (Submerged Arc Welded) pipe is a steel pipe made using a welding process where the arc is submerged under a layer of flux. This method ensures deep weld penetration and high-quality seams. SAW pipes come in two main types: LSAW (longitudinal) and SSAW (spiral). Known for their strength, durability, and ability to handle large diameters, SAW pipes are widely used in oil and gas pipelines, water transmission, and structural applications. Their consistent weld quality makes them ideal for high-pressure, long-distance, and heavy-duty industrial projects.
ERW vs SAW Pipe: Key Differences
When choosing between ERW (Electric Resistance Welded) pipes and SAW (Submerged Arc Welded) pipes, understanding the key differences is crucial for ensuring performance, durability, and cost-efficiency. Here’s a breakdown of the main distinctions based on manufacturing, size, strength, and application suitability.
1. Manufacturing process:
ERW (Electric Resistance Welded) pipes are produced by joining the edges of a steel strip using high-frequency electrical current, creating a continuous weld along the seam. This method is highly efficient and results in a smooth, uniform surface. On the other hand, SAW (Submerged Arc Welded) pipes are manufactured using a welding process that occurs beneath a layer of flux, which shields the weld zone and ensures deep penetration. SAW pipes come in two main forms—LSAW (Longitudinal Submerged Arc Welded) and SSAW (Spiral Submerged Arc Welded)—making them ideal for applications requiring larger diameters and thicker walls.
2. Pipe Size & Wall Thickness
ERW pipes typically come in smaller diameters (up to 24 inches) with moderate wall thickness, making them suitable for structural use and low-pressure systems. In contrast, SAW pipes can reach diameters up to 100 inches with thicker walls, ideal for heavy-duty applications like offshore and long-distance pipelines.
3. Pressure Handling Capability
SAW pipes, particularly LSAW, provide superior pressure resistance thanks to their thicker walls and deeper welds. ERW pipes, on the other hand, are more suitable for low to medium pressure applications like water supply and scaffolding.
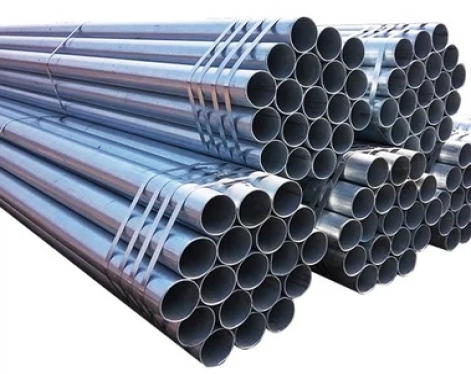
4. Cost and Efficiency
ERW pipes are more economical for small to medium projects, offering faster production and up to 20–30% lower material costs. SAW pipes, though more expensive, are essential for large-diameter, high-strength applications where durability is critical.
5. Weld Strength and Quality
SAW pipes offer greater weld strength and consistency due to their controlled welding process and deeper penetration. While ERW pipes have clean, uniform welds, they may not provide the same level of strength required for high-pressure or critical pipeline systems.
6. Surface Quality
ERW pipes offer a smoother, more uniform surface due to cold-forming and precise welding, making them ideal for visible or coated applications. SAW pipes, especially SSAW, may have a rougher finish with external weld beads, often requiring additional surface treatment for enhanced appearance or corrosion protection.
7. Weld Defect
ERW pipes may have minor weld defects like hook cracks or cold welds if not properly controlled, but modern techniques minimize these risks. SAW pipes, with deeper weld penetration and controlled conditions, generally have fewer internal defects, making them more reliable for high-pressure use.
Conclusion
When comparing ERW and SAW pipes, the right choice depends on your application needs. ERW pipes, made using high-frequency electric resistance welding, are ideal for small to medium diameters and low to medium pressure systems. They offer smooth surfaces, consistent seams, and are cost-effective for structural and general-purpose use. However, their weld strength may be limited for high-pressure demands.
SAW pipes—including LSAW and SSAW—are manufactured with submerged arc welding, enabling deeper welds and stronger joints. They support larger diameters and thicker walls, making them suitable for high-pressure, long-distance, and heavy-duty applications. Although more expensive and less smooth in surface finish, SAW pipes provide superior weld integrity and fewer defects.
In summary, choose ERW for budget-friendly, light-duty needs and SAW for robust, high-performance projects.
Read more: ERW Pipe VS. CEW Pipe