Boiler tubes are key components in the boiler system. Their performance and use directly affect the operating efficiency, safety and service life of the boiler. Therefore, when using boiler tubes, relevant precautions must be strictly followed to ensure the normal operation of the boiler system and the safety of operators. The following are some aspects that need to be paid attention to during the use of boiler tubes summarized by Nansteel Manufacturing Co., Ltd:
Material selection and quality requirements
The material of boiler tubes must comply with national standards or industry specifications, and usually uses high-temperature resistant, corrosion-resistant, and high-strength steel, such as 20G, 15CrMo, 12Cr1MoV, etc. When selecting boiler tubes, the following points should be noted:
Material brand: Select the appropriate material brand according to the working pressure and temperature of the boiler.
Quality standards: Ensure that the production process, chemical composition, mechanical properties, etc. of boiler tubes meet relevant standards (such as GB/T 5310, ASME SA-106, etc.).
Appearance inspection: Check whether there are cracks, scratches, pits and other defects on the surface of the boiler tube to ensure that its surface is smooth and flawless.
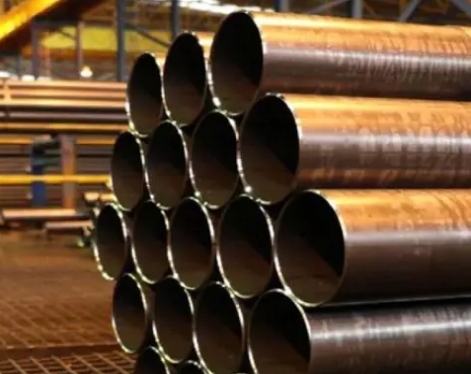
Installation and connection
The installation quality of boiler tubes directly affects their use effect and safety. During the installation process, pay attention to the following matters:
Pipeline layout: The layout of boiler tubes should be reasonable to avoid excessive elbows and joints to reduce flow resistance and stress concentration.
Welding quality: Welding is the main way to connect boiler tubes and must be performed by certified welders in accordance with specifications. Nondestructive testing (such as ultrasonic testing, radiographic testing, etc.) should be performed after welding to ensure the quality of the weld.
Support and fixation: Boiler tubes should be equipped with reasonable support and fixing devices to avoid deformation or damage of the tubes due to thermal expansion and contraction or vibration.
Monitoring and maintenance during operation
During the operation of the boiler, the working environment of the boiler tube is very harsh and is easily affected by factors such as high temperature, high pressure, and corrosion. Therefore, monitoring and maintenance must be strengthened:
Temperature control: The operating temperature of the boiler tube should be controlled within the design range to avoid over-temperature operation resulting in degradation of material properties or tube burst accidents.
Pressure monitoring: Regularly check the pressure of the boiler tubes to ensure that it operates within the allowable range.
Water quality management: Impurities and dissolved oxygen in boiler water can cause scaling or corrosion on the inner wall of boiler tubes, so water quality must be strictly controlled and water treatment must be performed regularly.
Regular inspection: Regularly inspect the appearance, measure the wall thickness and clean the inside of the boiler tubes to detect and deal with problems in a timely manner.
Prevent corrosion and scaling
Corrosion and scaling are one of the main causes of boiler tube damage, and effective measures must be taken to prevent them:
Chemical cleaning: Regularly perform chemical cleaning on boiler tubes to remove scale and corrosion products on the inner wall.
Anti-corrosion coating: Anti-corrosion coating is applied to the outer wall of the boiler tube to resist environmental corrosion.
Deoxygenation treatment: Oxygen dissolved in boiler water will accelerate corrosion, so deoxygenation equipment should be installed or deoxidizer should be added.
Prevent overpressure and overtemperature
Overpressure and overtemperature are the main causes of boiler tube damage and tube burst. The following measures must be taken:
Safety valve setting: Install a safety valve in the boiler system to automatically release pressure when the pressure exceeds the set value.
Temperature alarm device: Install temperature sensors and alarm devices to promptly sound the alarm and take measures when the temperature is abnormal.
Operating procedures: Operate the boiler strictly in accordance with the operating procedures to avoid overpressure or overtemperature caused by human operating errors.
Regular maintenance and replacement
Boiler tubes will age, wear or corrode after long-term use and must be inspected and replaced regularly:
Maintenance plan: Develop a detailed maintenance plan and conduct a comprehensive inspection of boiler tubes regularly.
Replacement standard: When the wall thickness of the boiler tube is reduced beyond the allowable value, or when severe corrosion or cracks occur, it should be replaced in time.
Record management: Establish maintenance and replacement records for boiler tubes to facilitate tracking and management.
Operator training
The correct use and maintenance of boiler tubes cannot be separated from the professional knowledge and skills of operators, so training must be strengthened:
Safety knowledge: Operators should be familiar with the safe operating procedures and emergency plans of boiler tubes.
Skill training: Regularly conduct skill training for operators to improve their installation, maintenance and overhaul capabilities.
Responsibility awareness: Strengthen the responsibility awareness of operators to ensure that they strictly follow the specifications.
Conclusion
The precautions for the use of boiler tubes cover many aspects such as material selection, installation, operation, maintenance, and overhaul. Only by strictly following these precautions can we ensure the safe and efficient operation of boiler tubes, extend their service life, and at the same time ensure the safety of operators and the sustainable development of the environment. In actual operation, detailed management systems and operating procedures should be formulated in combination with specific circumstances, and regular inspections and training should be carried out to ensure that boiler tubes are always in good working condition.
Read more: Service Life of Boiler Tubes
Material selection and quality requirements
The material of boiler tubes must comply with national standards or industry specifications, and usually uses high-temperature resistant, corrosion-resistant, and high-strength steel, such as 20G, 15CrMo, 12Cr1MoV, etc. When selecting boiler tubes, the following points should be noted:
Material brand: Select the appropriate material brand according to the working pressure and temperature of the boiler.
Quality standards: Ensure that the production process, chemical composition, mechanical properties, etc. of boiler tubes meet relevant standards (such as GB/T 5310, ASME SA-106, etc.).
Appearance inspection: Check whether there are cracks, scratches, pits and other defects on the surface of the boiler tube to ensure that its surface is smooth and flawless.
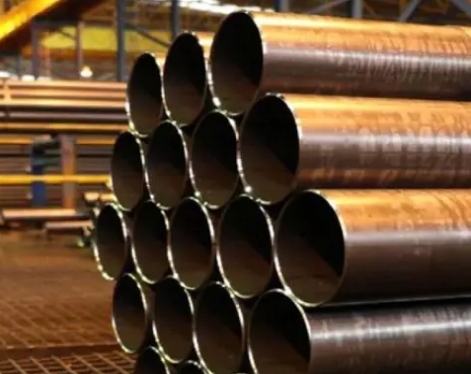
Installation and connection
The installation quality of boiler tubes directly affects their use effect and safety. During the installation process, pay attention to the following matters:
Pipeline layout: The layout of boiler tubes should be reasonable to avoid excessive elbows and joints to reduce flow resistance and stress concentration.
Welding quality: Welding is the main way to connect boiler tubes and must be performed by certified welders in accordance with specifications. Nondestructive testing (such as ultrasonic testing, radiographic testing, etc.) should be performed after welding to ensure the quality of the weld.
Support and fixation: Boiler tubes should be equipped with reasonable support and fixing devices to avoid deformation or damage of the tubes due to thermal expansion and contraction or vibration.
Monitoring and maintenance during operation
During the operation of the boiler, the working environment of the boiler tube is very harsh and is easily affected by factors such as high temperature, high pressure, and corrosion. Therefore, monitoring and maintenance must be strengthened:
Temperature control: The operating temperature of the boiler tube should be controlled within the design range to avoid over-temperature operation resulting in degradation of material properties or tube burst accidents.
Pressure monitoring: Regularly check the pressure of the boiler tubes to ensure that it operates within the allowable range.
Water quality management: Impurities and dissolved oxygen in boiler water can cause scaling or corrosion on the inner wall of boiler tubes, so water quality must be strictly controlled and water treatment must be performed regularly.
Regular inspection: Regularly inspect the appearance, measure the wall thickness and clean the inside of the boiler tubes to detect and deal with problems in a timely manner.
Prevent corrosion and scaling
Corrosion and scaling are one of the main causes of boiler tube damage, and effective measures must be taken to prevent them:
Chemical cleaning: Regularly perform chemical cleaning on boiler tubes to remove scale and corrosion products on the inner wall.
Anti-corrosion coating: Anti-corrosion coating is applied to the outer wall of the boiler tube to resist environmental corrosion.
Deoxygenation treatment: Oxygen dissolved in boiler water will accelerate corrosion, so deoxygenation equipment should be installed or deoxidizer should be added.
Prevent overpressure and overtemperature
Overpressure and overtemperature are the main causes of boiler tube damage and tube burst. The following measures must be taken:
Safety valve setting: Install a safety valve in the boiler system to automatically release pressure when the pressure exceeds the set value.
Temperature alarm device: Install temperature sensors and alarm devices to promptly sound the alarm and take measures when the temperature is abnormal.
Operating procedures: Operate the boiler strictly in accordance with the operating procedures to avoid overpressure or overtemperature caused by human operating errors.
Regular maintenance and replacement
Boiler tubes will age, wear or corrode after long-term use and must be inspected and replaced regularly:
Maintenance plan: Develop a detailed maintenance plan and conduct a comprehensive inspection of boiler tubes regularly.
Replacement standard: When the wall thickness of the boiler tube is reduced beyond the allowable value, or when severe corrosion or cracks occur, it should be replaced in time.
Record management: Establish maintenance and replacement records for boiler tubes to facilitate tracking and management.
Operator training
The correct use and maintenance of boiler tubes cannot be separated from the professional knowledge and skills of operators, so training must be strengthened:
Safety knowledge: Operators should be familiar with the safe operating procedures and emergency plans of boiler tubes.
Skill training: Regularly conduct skill training for operators to improve their installation, maintenance and overhaul capabilities.
Responsibility awareness: Strengthen the responsibility awareness of operators to ensure that they strictly follow the specifications.
Conclusion
The precautions for the use of boiler tubes cover many aspects such as material selection, installation, operation, maintenance, and overhaul. Only by strictly following these precautions can we ensure the safe and efficient operation of boiler tubes, extend their service life, and at the same time ensure the safety of operators and the sustainable development of the environment. In actual operation, detailed management systems and operating procedures should be formulated in combination with specific circumstances, and regular inspections and training should be carried out to ensure that boiler tubes are always in good working condition.
Read more: Service Life of Boiler Tubes