The branch where the author works is located on the coastline of the South China Sea. There are two wharfs for the transportation of raw materials and products. Both wharfs were built and put into use in 2005. There are 481 steel pipe piles as support. After a few years of use, some of the pipe piles have paint peeling and rust.
1.Cause Analysis
Since the salinity of seawater is between 32% and 37%, and the pH value is between 8 and 8.2, it is a natural strong electrolyte solution containing suspended sediment, dissolved gas, organisms, and corrupt organic matter. In addition, the steel pipe piles at the dock are long-term affected by tides, waves, marine organisms, ship berthing, oil booms, etc., impact and abrasion, etc., causing damage to the anti-corrosion coating in the splash zone of the pipe piling. Therefore, it is difficult for traditional anti-corrosion coatings to achieve the ideal anti-corrosion effect.
The environmental parameters of Haicheng are as follows
Tidal characteristics: The tidal characteristics of the area where this wharf is located are irregular semi-diurnal mixed tides, with an average annual tidal range of 1.02m, a maximum tidal range of 2.71m, a historical maximum water level of 3.92m, a minimum water level of -0.37m, and a wave direction of SSE.
The three peak areas of marine steel pipe pile corrosion are as follows.
(1) Splashing area - the splashing area above the average high tide line is the most serious area for steel structure corrosion
The corrosion rate is 0.2~0.5mm/Y. Reasons: seawater splashing, alternating dry and wet, sufficient oxygen; light and wave impact, destroying the metal protective film.
(2) Water level change area - the area 0.5-1.0m below the average low tide line, the corrosion rate is 0.1~0.3 mm/Y. Reasons: sufficient dissolved oxygen, large seawater flow rate, high water temperature, and rapid reproduction of marine organisms.
(3) Below the junction of seawater and sea mud.
Reason: Seawater and sea mud electrolyze the steel pipe piles, and the corrosion rate is 0.03-0.07mm/Y. Since the sacrificial anode protection method has been adopted for the protection of steel piles in the full immersion area of seawater, the anti-corrosion protection of the steel pipe piles in the splash area and the area 0.5~1.0m below the average low tide line should be the key parts of the steel pipe piles. Based on this situation, we started the maintenance plan for the steel pipe piles.
Because the paint peeling part of the pipe piles is located in the tidal range area and the wave splash area of the steel pipe piles, the anti-corrosion work must be carried out in a water environment. In this way, the traditional paint coating method cannot be used. Drawing on the maintenance experience at home and abroad, we chose the method of coating corrosion system protection.
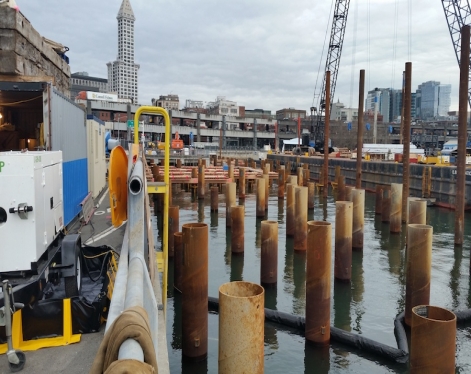
The anti-corrosion solutions for the atmospheric zone and splash zone of steel piles are as follows.
(1) Pretreatment of substrate
Cut the concrete along the rust ring on the top of the sea pile to the rust-free part [about 1~2 inches deep), and manually remove the rust of the substrate to Sa2~St3 level; for the atmospheric zone and splash zone that seem to be rust-free, the adhesion of the old paint film must be tested, and the old paint film that is not firmly attached should be polished and removed.
(2) Anti-corrosion coating design
Designed anti-corrosion life: 20-30 years; total dry film thickness: 600um; 500um is applied to the strong old paint film; coating passes: two coats of primer and topcoat in total; SP2170A primer, dark gray, one coat of 300um, including local reinforcement repair; 200um is applied to the strong old paint film; SP2170T topcoat, medium gray or various colors, one coat of 300um. The coating interval between primer and topcoat is greater than 8h. If the primer and topcoat need to be diluted, 5% thinner can be added.
(3) After the sea pile is painted, fill the top of the concrete with putty and apply SP2170T paint to seal it.
2. Anti-corrosion solution for tidal range and full immersion area
(1) Substrate pretreatment
Thoroughly remove rust and marine attachments on the surface of the sea pile; the old paint film in the rust-free area must be tested for adhesion, and the old paint film with weak adhesion should be polished and removed.
(2) Anti-corrosion coating design for tidal range and full immersion area
In the most corrosive area several meters above and below the ocean waterline, the paint film performance is targeted. In order to achieve durable protection benefits, the thickness of the coating here is generally required to be 2 to 3 times the thickness of the area above the splash zone. Design anti-corrosion life: 20-30 years. SP2170A primer, dark gray, one coat of 1000um, including local reinforcement repair. Then wrap the non-woven fabric dipped in heavy anti-corrosion paint and match it with a sheath. The interval between primer and wrapping non-woven fabric is greater than 6 hours.
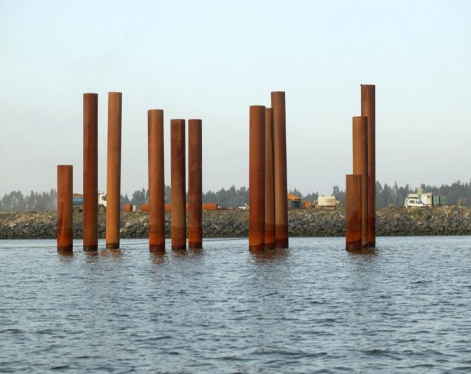
3.The specific steps of anti-corrosion solutions for piling pipes
Step 1: the surface treatment of steel pipe piles.
(1) Purpose. In order to ensure that the anti-corrosion paste can fully combine with the steel surface and achieve the best protection effect, the steel surface must be treated.
(2) Treatment requirements. The surface treatment of the steel structure in the construction area must meet the ISOSt2 standard or above, without obvious bubbles and floating rust; the attached marine organisms in the tidal range area and other marine organism attachment zones should be removed as much as possible, and the surface protrusions should not have sharp angles, generally not higher than 5mm, and the maximum not higher than 10mm.
(3) Treatment methods.
1) Remove marine organisms. Use a spatula and a high-pressure water gun to remove attached marine organisms. For firmly attached shellfish, the residue should not be higher than 10mm.
2) Manual rust removal.
① Use inspection pliers to knock on the bubbling area to detect whether there is a rust layer under the paint film.
② Use a rust removal spatula to gently scrape the raised part of the steel pipe to remove all the floating rust and bubbles.
③ Use a steel sand brush to remove floating rust and oxide scale, and use iron sandpaper to grind and remove rust.
3) Sandblasting. Generally, sandblasting is not required. However, if the surface rust layer is very serious, sandblasting can be used to remove the loose rust and make the surface finish of the steel structure meet the requirements.
Step 2 : apply anti-corrosion paste.
(1) Application method: squeeze a little anti-corrosion paste in the middle of the palm and apply it. Repeat 5 to 10 times to make the anti-corrosion paste evenly distributed on the surface of the steel structure.
(2) Amount of anti-corrosion paste. For smooth surfaces, about 300g/m²; for areas with particularly severe rust, about 400 to 500 g/m².
(3) When applying anti-corrosion paste near the average sea level, it should be done at low tide.
(4) The pits and gaps on the surface of the steel pile should be filled with anti-corrosion paste. The rusted areas need to be smoothed. A layer of anti-corrosion paste should also be applied to the surface of the protrusions so that the anti-corrosion paste is evenly distributed on the surface of the steel structure to form a complete protective film.
Step 3: wrap the anti-corrosion tape.
(1) Wrapping method. When wrapping on the straight pipe, first wrap two layers at the beginning, and then overlap 1/2 in sequence. When wrapping, tighten and flatten the anti-corrosion tape with a little force to squeeze out the air inside. It must be ensured that at least two layers are wrapped at each location. For vertical structures, winding is generally carried out from bottom to top.
(2) Requirements. After applying the anti-corrosion paste, the anti-corrosion tape should be wrapped immediately, especially near the average sea level, to prevent the anti-corrosion paste from being washed off by seawater. When wrapping, tighten and flatten the anti-corrosion tape by hand to ensure that no bubbles appear in the wrapped area. Ensure that the steel pile is covered with more than two layers of anti-corrosion tape at each location.
Step 4: Install the anti-corrosion shield.
(1) Install the anti-corrosion shield.
Install the anti-corrosion shield vertically. The steel structure at the regular location can pre-process the shield shell. During on-site construction, fasten the two anti-corrosion shields with stainless steel bolts.
(2) Sealing the ends of the anti-corrosion shield.
The two ends are sealed with water-curing epoxy resin.
(3) When tightening the bolts, care should be taken to ensure that the seal of the corrosion protection cover is evenly stressed to prevent deformation of the corrosion protection cover and rupture of the sealing edge due to excessive local stress.
1.Cause Analysis
Since the salinity of seawater is between 32% and 37%, and the pH value is between 8 and 8.2, it is a natural strong electrolyte solution containing suspended sediment, dissolved gas, organisms, and corrupt organic matter. In addition, the steel pipe piles at the dock are long-term affected by tides, waves, marine organisms, ship berthing, oil booms, etc., impact and abrasion, etc., causing damage to the anti-corrosion coating in the splash zone of the pipe piling. Therefore, it is difficult for traditional anti-corrosion coatings to achieve the ideal anti-corrosion effect.
The environmental parameters of Haicheng are as follows
Tidal characteristics: The tidal characteristics of the area where this wharf is located are irregular semi-diurnal mixed tides, with an average annual tidal range of 1.02m, a maximum tidal range of 2.71m, a historical maximum water level of 3.92m, a minimum water level of -0.37m, and a wave direction of SSE.
The three peak areas of marine steel pipe pile corrosion are as follows.
(1) Splashing area - the splashing area above the average high tide line is the most serious area for steel structure corrosion
The corrosion rate is 0.2~0.5mm/Y. Reasons: seawater splashing, alternating dry and wet, sufficient oxygen; light and wave impact, destroying the metal protective film.
(2) Water level change area - the area 0.5-1.0m below the average low tide line, the corrosion rate is 0.1~0.3 mm/Y. Reasons: sufficient dissolved oxygen, large seawater flow rate, high water temperature, and rapid reproduction of marine organisms.
(3) Below the junction of seawater and sea mud.
Reason: Seawater and sea mud electrolyze the steel pipe piles, and the corrosion rate is 0.03-0.07mm/Y. Since the sacrificial anode protection method has been adopted for the protection of steel piles in the full immersion area of seawater, the anti-corrosion protection of the steel pipe piles in the splash area and the area 0.5~1.0m below the average low tide line should be the key parts of the steel pipe piles. Based on this situation, we started the maintenance plan for the steel pipe piles.
Because the paint peeling part of the pipe piles is located in the tidal range area and the wave splash area of the steel pipe piles, the anti-corrosion work must be carried out in a water environment. In this way, the traditional paint coating method cannot be used. Drawing on the maintenance experience at home and abroad, we chose the method of coating corrosion system protection.
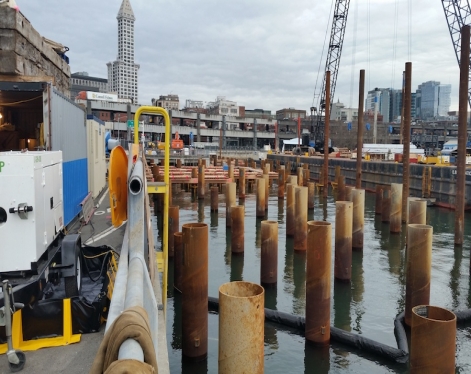
The anti-corrosion solutions for the atmospheric zone and splash zone of steel piles are as follows.
(1) Pretreatment of substrate
Cut the concrete along the rust ring on the top of the sea pile to the rust-free part [about 1~2 inches deep), and manually remove the rust of the substrate to Sa2~St3 level; for the atmospheric zone and splash zone that seem to be rust-free, the adhesion of the old paint film must be tested, and the old paint film that is not firmly attached should be polished and removed.
(2) Anti-corrosion coating design
Designed anti-corrosion life: 20-30 years; total dry film thickness: 600um; 500um is applied to the strong old paint film; coating passes: two coats of primer and topcoat in total; SP2170A primer, dark gray, one coat of 300um, including local reinforcement repair; 200um is applied to the strong old paint film; SP2170T topcoat, medium gray or various colors, one coat of 300um. The coating interval between primer and topcoat is greater than 8h. If the primer and topcoat need to be diluted, 5% thinner can be added.
(3) After the sea pile is painted, fill the top of the concrete with putty and apply SP2170T paint to seal it.
2. Anti-corrosion solution for tidal range and full immersion area
(1) Substrate pretreatment
Thoroughly remove rust and marine attachments on the surface of the sea pile; the old paint film in the rust-free area must be tested for adhesion, and the old paint film with weak adhesion should be polished and removed.
(2) Anti-corrosion coating design for tidal range and full immersion area
In the most corrosive area several meters above and below the ocean waterline, the paint film performance is targeted. In order to achieve durable protection benefits, the thickness of the coating here is generally required to be 2 to 3 times the thickness of the area above the splash zone. Design anti-corrosion life: 20-30 years. SP2170A primer, dark gray, one coat of 1000um, including local reinforcement repair. Then wrap the non-woven fabric dipped in heavy anti-corrosion paint and match it with a sheath. The interval between primer and wrapping non-woven fabric is greater than 6 hours.
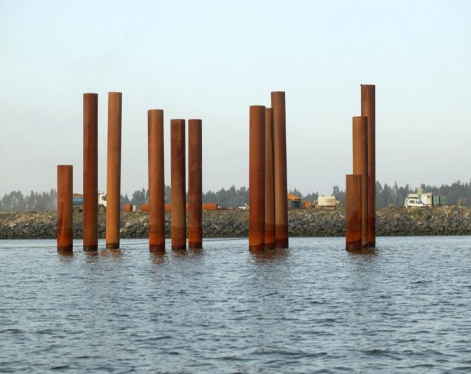
3.The specific steps of anti-corrosion solutions for piling pipes
Step 1: the surface treatment of steel pipe piles.
(1) Purpose. In order to ensure that the anti-corrosion paste can fully combine with the steel surface and achieve the best protection effect, the steel surface must be treated.
(2) Treatment requirements. The surface treatment of the steel structure in the construction area must meet the ISOSt2 standard or above, without obvious bubbles and floating rust; the attached marine organisms in the tidal range area and other marine organism attachment zones should be removed as much as possible, and the surface protrusions should not have sharp angles, generally not higher than 5mm, and the maximum not higher than 10mm.
(3) Treatment methods.
1) Remove marine organisms. Use a spatula and a high-pressure water gun to remove attached marine organisms. For firmly attached shellfish, the residue should not be higher than 10mm.
2) Manual rust removal.
① Use inspection pliers to knock on the bubbling area to detect whether there is a rust layer under the paint film.
② Use a rust removal spatula to gently scrape the raised part of the steel pipe to remove all the floating rust and bubbles.
③ Use a steel sand brush to remove floating rust and oxide scale, and use iron sandpaper to grind and remove rust.
3) Sandblasting. Generally, sandblasting is not required. However, if the surface rust layer is very serious, sandblasting can be used to remove the loose rust and make the surface finish of the steel structure meet the requirements.
Step 2 : apply anti-corrosion paste.
(1) Application method: squeeze a little anti-corrosion paste in the middle of the palm and apply it. Repeat 5 to 10 times to make the anti-corrosion paste evenly distributed on the surface of the steel structure.
(2) Amount of anti-corrosion paste. For smooth surfaces, about 300g/m²; for areas with particularly severe rust, about 400 to 500 g/m².
(3) When applying anti-corrosion paste near the average sea level, it should be done at low tide.
(4) The pits and gaps on the surface of the steel pile should be filled with anti-corrosion paste. The rusted areas need to be smoothed. A layer of anti-corrosion paste should also be applied to the surface of the protrusions so that the anti-corrosion paste is evenly distributed on the surface of the steel structure to form a complete protective film.
Step 3: wrap the anti-corrosion tape.
(1) Wrapping method. When wrapping on the straight pipe, first wrap two layers at the beginning, and then overlap 1/2 in sequence. When wrapping, tighten and flatten the anti-corrosion tape with a little force to squeeze out the air inside. It must be ensured that at least two layers are wrapped at each location. For vertical structures, winding is generally carried out from bottom to top.
(2) Requirements. After applying the anti-corrosion paste, the anti-corrosion tape should be wrapped immediately, especially near the average sea level, to prevent the anti-corrosion paste from being washed off by seawater. When wrapping, tighten and flatten the anti-corrosion tape by hand to ensure that no bubbles appear in the wrapped area. Ensure that the steel pile is covered with more than two layers of anti-corrosion tape at each location.
Step 4: Install the anti-corrosion shield.
(1) Install the anti-corrosion shield.
Install the anti-corrosion shield vertically. The steel structure at the regular location can pre-process the shield shell. During on-site construction, fasten the two anti-corrosion shields with stainless steel bolts.
(2) Sealing the ends of the anti-corrosion shield.
The two ends are sealed with water-curing epoxy resin.
(3) When tightening the bolts, care should be taken to ensure that the seal of the corrosion protection cover is evenly stressed to prevent deformation of the corrosion protection cover and rupture of the sealing edge due to excessive local stress.