In the industrial field, black carbon steel pipe is a common and important material. However, steel pipes can be affected by corrosion, reducing their service life. In order to protect black carbon steel pipe from corrosion, appropriate anti-corrosion measures need to be taken.
Methods for external anti-corrosion of black carbon steel pipe
Using cathodic protection alone is uneconomical because it consumes too much power. Therefore, the combination of anti-corrosion layer and cathodic protection, which concentrates cathodic protection on the exposed metal surface at defects in the anti-corrosion layer, is the best and most economical form of protection. "Combined protection" is a protection method in which "the anti-corrosion layer is mainly used and cathodic protection is supplemented".
2. Internal anti-corrosion treatment of black carbon steel pipe
Main anti-corrosion measures: anti-corrosion layer and cathodic protection. The anti-corrosion layer plays an isolation role in controlling metal corrosion. The exposed metal at the defect and the part covered by the anti-corrosion layer form a local corrosion battery of small anode and large cathode, which in turn will accelerate the corrosion rate of the exposed metal. Therefore, the effect of using anti-corrosion layer protection alone is not ideal. Therefore, a combination of anti-corrosion layer and cathodic protection should be used.
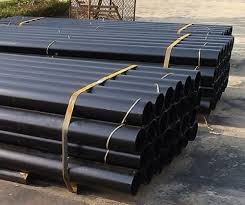
3.Black carbon steel pipe external anti-corrosion material
Pipeline anti-corrosion materials are materials that inhibit chemical corrosion and electrochemical corrosion in pipelines. Pipeline anti-corrosion materials are divided into pipeline body anti-corrosion materials and their corresponding patching materials. The main body anti-corrosion mainly includes petroleum asphalt, epoxy coal tar, adhesive tape, epoxy powder, PE coating, and PP coating. Commonly used patching methods include petroleum asphalt patching, epoxy coal pitch patching, adhesive tape patching, epoxy powder patching, and PE heat shrink material patching.
4. Surface treatment
(1) Anti-corrosion coating surface treatment of steel pipes
Usually there will be dust, oil, oxide scale, rust layer, pollutants, salt or old paint film on the surface of the steel pipe. Among them, oxide scale is a common but most easily ignored part. Oxide scale is a dense oxide layer produced when steel is forged and formed at high temperatures. It is usually relatively firmly attached, but is more brittle than the steel itself and acts as a cathode, which accelerates metal corrosion. If these substances are not removed and applied directly, the adhesion and anti-corrosion capabilities of the entire coating will inevitably be affected. According to statistics, more than 70% of paint problems are caused by improper surface preparation. Therefore, for the performance of a metal anti-corrosion coating paint system, suitable surface treatment is crucial.
(2) Steel pipe anti-corrosion surface cleaning level
There are two representative international standards for surface cleaning levels: one is "SSPC-" formulated by the United States in 1985; the second is "Sa-" formulated by Sweden in 1976, which is divided into four levels: Sa1, Sa2, Sa2.5, Sa3 are common international standards.
The details are as follows:
Sa1 level - equivalent to the US SSPC-SP7 level. Using the generally simple manual brushing and emery cloth polishing methods, this is the lowest level among the four cleanliness levels, and the protection of the coating is only slightly better than that of untreated workpieces. Technical standards for Sa1 level treatment: oil, grease, residual oxide scale, rust spots, residual paint and other contaminants should not be visible on the surface of the workpiece. Sa1 level is also called manual brushing and cleaning level.
Sa2 level - equivalent to the US SSPC-SP6 level. Use sandblasting cleaning method, which is the lowest level in sandblasting treatment, that is, the general requirement, but the protection of the coating is much higher than manual brushing and cleaning. Technical standards for Sa2 level treatment: The surface of the workpiece should be free from visible greasy, dirt, oxide scale, rust scale, paint, oxides, corrosives, and other foreign substances (except defects), but the defects are limited to no more than 100% per square meter of surface 33%, which may include slight shading; a small amount of slight discoloration caused by defects and rust; scale and paint defects. If the original surface of the workpiece is dented, slight rust and paint may remain at the bottom of the dent. Sa2 level is also called commodity cleaning level (or industrial level).
Sa2.5 level - is a level commonly used in industry and can be used as acceptance technical requirements and standards. Sa2.5 level is also called near-white cleaning level (near-white level or white-out level). Technical standards for Sa2.5 level treatment: The same as the first half of the Sa2 requirements, but defects are limited to no more than 5% of the surface per square meter, which may include slight shadows; a small amount of slight discoloration caused by defects and rust; scale and paint defects .
Sa3 level is equivalent to the US SSPC-SP5 level. It is the highest treatment level in the industry and is also called white cleaning level (or white level). The technical standards of Sa3 level treatment are the same as Sa2.5 level but 5% of shadows, defects, rust, etc. are no longer present.
Methods for external anti-corrosion of black carbon steel pipe
Using cathodic protection alone is uneconomical because it consumes too much power. Therefore, the combination of anti-corrosion layer and cathodic protection, which concentrates cathodic protection on the exposed metal surface at defects in the anti-corrosion layer, is the best and most economical form of protection. "Combined protection" is a protection method in which "the anti-corrosion layer is mainly used and cathodic protection is supplemented".
2. Internal anti-corrosion treatment of black carbon steel pipe
Main anti-corrosion measures: anti-corrosion layer and cathodic protection. The anti-corrosion layer plays an isolation role in controlling metal corrosion. The exposed metal at the defect and the part covered by the anti-corrosion layer form a local corrosion battery of small anode and large cathode, which in turn will accelerate the corrosion rate of the exposed metal. Therefore, the effect of using anti-corrosion layer protection alone is not ideal. Therefore, a combination of anti-corrosion layer and cathodic protection should be used.
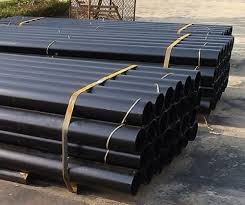
3.Black carbon steel pipe external anti-corrosion material
Pipeline anti-corrosion materials are materials that inhibit chemical corrosion and electrochemical corrosion in pipelines. Pipeline anti-corrosion materials are divided into pipeline body anti-corrosion materials and their corresponding patching materials. The main body anti-corrosion mainly includes petroleum asphalt, epoxy coal tar, adhesive tape, epoxy powder, PE coating, and PP coating. Commonly used patching methods include petroleum asphalt patching, epoxy coal pitch patching, adhesive tape patching, epoxy powder patching, and PE heat shrink material patching.
4. Surface treatment
(1) Anti-corrosion coating surface treatment of steel pipes
Usually there will be dust, oil, oxide scale, rust layer, pollutants, salt or old paint film on the surface of the steel pipe. Among them, oxide scale is a common but most easily ignored part. Oxide scale is a dense oxide layer produced when steel is forged and formed at high temperatures. It is usually relatively firmly attached, but is more brittle than the steel itself and acts as a cathode, which accelerates metal corrosion. If these substances are not removed and applied directly, the adhesion and anti-corrosion capabilities of the entire coating will inevitably be affected. According to statistics, more than 70% of paint problems are caused by improper surface preparation. Therefore, for the performance of a metal anti-corrosion coating paint system, suitable surface treatment is crucial.
(2) Steel pipe anti-corrosion surface cleaning level
There are two representative international standards for surface cleaning levels: one is "SSPC-" formulated by the United States in 1985; the second is "Sa-" formulated by Sweden in 1976, which is divided into four levels: Sa1, Sa2, Sa2.5, Sa3 are common international standards.
The details are as follows:
Sa1 level - equivalent to the US SSPC-SP7 level. Using the generally simple manual brushing and emery cloth polishing methods, this is the lowest level among the four cleanliness levels, and the protection of the coating is only slightly better than that of untreated workpieces. Technical standards for Sa1 level treatment: oil, grease, residual oxide scale, rust spots, residual paint and other contaminants should not be visible on the surface of the workpiece. Sa1 level is also called manual brushing and cleaning level.
Sa2 level - equivalent to the US SSPC-SP6 level. Use sandblasting cleaning method, which is the lowest level in sandblasting treatment, that is, the general requirement, but the protection of the coating is much higher than manual brushing and cleaning. Technical standards for Sa2 level treatment: The surface of the workpiece should be free from visible greasy, dirt, oxide scale, rust scale, paint, oxides, corrosives, and other foreign substances (except defects), but the defects are limited to no more than 100% per square meter of surface 33%, which may include slight shading; a small amount of slight discoloration caused by defects and rust; scale and paint defects. If the original surface of the workpiece is dented, slight rust and paint may remain at the bottom of the dent. Sa2 level is also called commodity cleaning level (or industrial level).
Sa2.5 level - is a level commonly used in industry and can be used as acceptance technical requirements and standards. Sa2.5 level is also called near-white cleaning level (near-white level or white-out level). Technical standards for Sa2.5 level treatment: The same as the first half of the Sa2 requirements, but defects are limited to no more than 5% of the surface per square meter, which may include slight shadows; a small amount of slight discoloration caused by defects and rust; scale and paint defects .
Sa3 level is equivalent to the US SSPC-SP5 level. It is the highest treatment level in the industry and is also called white cleaning level (or white level). The technical standards of Sa3 level treatment are the same as Sa2.5 level but 5% of shadows, defects, rust, etc. are no longer present.
Previous:Heat treatment for octg casing