Anti-corrosion measures and procedures are as follows:
It is one of the basic methods for pipeline anticorrosion to evenly and densely coat the surface of the rust-removed metal pipeline with paint to isolate it from various corrosive media.
1. When coating the anti-corrosion layer of steel casing pipe, it is necessary to pay attention to the environmental factors such as temperature and humidity at the coating site, which directly affect the coating effect. When the steel casing pipe is coated with anti-corrosion coating indoors, the temperature should be controlled at 20-25 degrees Celsius, and the relative humidity varies depending on the material of the casing, generally about 65%.
2. When constructing outdoors, there should be no wind, sand and drizzle. The temperature should not be lower than 5 degrees Celsius, and the relative humidity should not be greater than 85%. The drying and curing temperatures of various anti-corrosion coatings used in steel casing pipe vary greatly. Generally, epoxy resin coatings cure very slowly below 10 degrees Celsius, so it is not suitable for winter construction.
In order to prevent corrosion in the pipe, reduce frictional resistance, and increase throughput, it is a film applied to the inner wall of the pipe. Commonly used coatings include amine-cured epoxy resin and polyamide epoxy resin, and the coating thickness is 0.038 to 0.2 mm. In order to ensure that the coating is firmly bonded to the pipe wall, surface treatment must be carried out on the inner wall of the pipe.
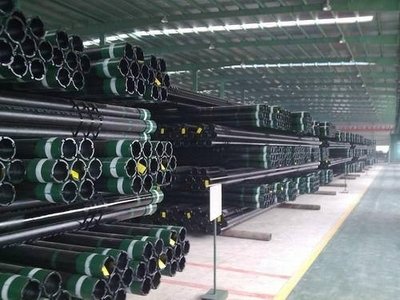
The main problems in casing anticorrosion engineering are:
1. Leakage: The settlement of the building structure will cause the waterproof casing to deform and leak water.
2. Aging: The long-term thermal expansion and contraction of the pipeline after installation will cause the expansion and contraction of the pipeline and cause the waterproof casing to not be used normally.
3. Unqualified installation:
(1) The welding does not meet the requirements (incomplete penetration of the weld, pores, slag inclusions, etc.);
(2) There is water leakage at the joint during the installation process;
4. Insufficient communication and coordination between the on-site installation personnel and the construction unit. The connection between pipe fittings is welding and bolting. Weld penetration and slag inclusions in the connection between pipes and fittings; porosity and slag inclusions when welding between unqualified pipe fittings; oil stains or paint on the surface of pipes. After the pipeline is installed, it will be affected by thermal expansion and contraction, corrosion and other factors for a long time, which may cause problems in the construction quality.
It is one of the basic methods for pipeline anticorrosion to evenly and densely coat the surface of the rust-removed metal pipeline with paint to isolate it from various corrosive media.
1. When coating the anti-corrosion layer of steel casing pipe, it is necessary to pay attention to the environmental factors such as temperature and humidity at the coating site, which directly affect the coating effect. When the steel casing pipe is coated with anti-corrosion coating indoors, the temperature should be controlled at 20-25 degrees Celsius, and the relative humidity varies depending on the material of the casing, generally about 65%.
2. When constructing outdoors, there should be no wind, sand and drizzle. The temperature should not be lower than 5 degrees Celsius, and the relative humidity should not be greater than 85%. The drying and curing temperatures of various anti-corrosion coatings used in steel casing pipe vary greatly. Generally, epoxy resin coatings cure very slowly below 10 degrees Celsius, so it is not suitable for winter construction.
In order to prevent corrosion in the pipe, reduce frictional resistance, and increase throughput, it is a film applied to the inner wall of the pipe. Commonly used coatings include amine-cured epoxy resin and polyamide epoxy resin, and the coating thickness is 0.038 to 0.2 mm. In order to ensure that the coating is firmly bonded to the pipe wall, surface treatment must be carried out on the inner wall of the pipe.
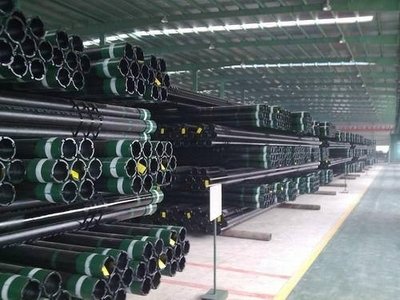
The main problems in casing anticorrosion engineering are:
1. Leakage: The settlement of the building structure will cause the waterproof casing to deform and leak water.
2. Aging: The long-term thermal expansion and contraction of the pipeline after installation will cause the expansion and contraction of the pipeline and cause the waterproof casing to not be used normally.
3. Unqualified installation:
(1) The welding does not meet the requirements (incomplete penetration of the weld, pores, slag inclusions, etc.);
(2) There is water leakage at the joint during the installation process;
4. Insufficient communication and coordination between the on-site installation personnel and the construction unit. The connection between pipe fittings is welding and bolting. Weld penetration and slag inclusions in the connection between pipes and fittings; porosity and slag inclusions when welding between unqualified pipe fittings; oil stains or paint on the surface of pipes. After the pipeline is installed, it will be affected by thermal expansion and contraction, corrosion and other factors for a long time, which may cause problems in the construction quality.