Boiler tube burst refers to the combined action of various reasons such as overheating, wear and corrosion of water-cooled wall tubes, convection tubes, and economizer tubes in the heat exchange surface of the boiler during operation. Pipeline bursts and high-temperature boiler water leakage will occur. , causing the boiler to fail to operate normally. Through years of theoretical accumulation and field practice, it has been found that boiler pipeline bursts are mainly caused by thirteen reasons.
(1) Water treatment quality issues
The boiler feed water quality is poor, there is no water treatment or the water treatment method is incorrect, and the sewage treatment is not carried out according to relevant regulations, causing scaling or corrosion on the inner wall of the pipeline. The main reason for this is that some boiler water is taken from the ground. The hardness is as high as 5mmol/L, which is high hardness water, and contains high sulfur and high iron content. Once the water is not treated properly, pipe bursts will easily occur and the boiler will be forced to shut down for emergency repairs, which will have a great impact on production and life.
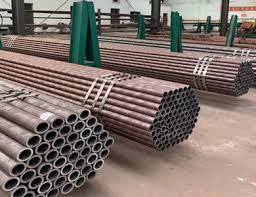
(2) Boiler tube performance issues
During the manufacturing, installation and maintenance process of boiler pipelines, stress concentration and mechanical performance degradation will occur at the welding joints. Pipeline bursts will occur in these key parts where stress concentration and mechanical performance degradation occur, which will also cause the boiler to collapse. Failure occurs and it is difficult to supply production and daily needs.
(3) Impurity problem
During the installation or maintenance of the boiler, impurities fall into the tubes, causing blockage in the tubes, resulting in poor water circulation or complete damage. The scale in the pipes falls off the inner wall and "bridges" the water circulation in a poor state.
(4) Boiler water level is too low
If the water level of the boiler is too low during operation, poor water circulation will also occur. When such a situation occurs, the temperature of the local pipeline will be too high, deforming until it bursts.
(5)Nozzle angle problem
For oil boilers, gas boilers or coal boilers, some boiler pipelines may overheat because the angle of the nozzle is not adjusted correctly during design and installation.
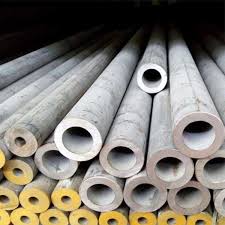
(6) Operational issues
Incorrect operation of starting and stopping the furnace causes the furnace tube to be blown by cold wind, causing the tube to expand and contract too quickly or too frequently, resulting in harmful stress.
(7) Pipeline heat concentration
The flue and firewall of the combustion chamber are damaged, causing the flue gas to short-circuit and cause heat concentration in the local furnace tube to burn out the furnace tube.
(8)Pipeline corrosion
Pipe corrosion and equipment aging lead to steel pipe explosions. Generally, it occurs in the economizer pipe on the rear heating surface. The reason is acid corrosion caused by too low exhaust gas temperature or too low feed water temperature.
(9) Local smoke speed is too fast
When installing and repairing the heating surface pipes, the pitch of the heating surface pipes and the distance between the heating surface pipe rows and the furnace wall do not meet the design requirements. Partial flue gas corridors, or partial pipes out of line, cause dust accumulation and bridging on the heating surface pipes, causing local smoke velocity to be too high, thereby increasing the wear and overheating of the pipes in this part.
(10) Pipe leakage
Due to careless construction, the sealing of the furnace wall was not strictly sealed in accordance with the construction requirements, causing eddy currents to form in the air leakage area. In this case, the pipeline will also be partially overheated or heated unevenly, and the air leakage will also increase the flow rate of the flue gas behind it. Increase, harming the tail heating surface.
(11)High temperature
The high-temperature operation of the pipe is also an important reason for boiler pipe explosion. Overheating and over-temperature pipe explosion are due to the decrease in mechanical properties of the pipe under overtemperature conditions, and the plastic deformation of the pipe under the action of pressure, that is, creep cracks and even pipe explosion.
(12)Pipeline environment
The influence of the operating environment can also cause the furnace tube to rupture, such as frequent starts and stops of the boiler, drastic changes in load, improper adjustment of the center of the flame, primary and secondary air erosion of the water-cooled wall tube, and the impact of rapid cooling due to shutdown of the furnace. Burst boiler tubes leave hidden dangers.
(13)Carbon dioxide problem
There is carbon dioxide corrosion or oxygen corrosion in the boiler heating system pipe network, or the steam condensate water pipe network. When oxygen and carbon dioxide are present in the boiler return water system at the same time, the corrosion of the system pipe network steel will be more serious. Carbon dioxide makes the water slightly acidic and damages the pipelines. Protective film, as the oxygen content increases, the carbon steel equipment and pipe network of the heating system will appear in a state of large or small ulcers, accelerating corrosion. As a result, the color of the return water or condensed water will turn yellow, red, or even soy sauce color. , The iron ion content is large, and the steel pipe is perforated. This is the reason why common steam pipes and condensate pipes corrode, perforate, and leak. This is also the reason why the service life of some newly built boiler carbon steel pipes is only 4-5 years, that is, the condensate pipes need to be replaced every 4-5 years.
The iron content in the boiler return water exceeding the standard will not only cause the "red water" phenomenon of the boiler water, but also cause corrosion under the iron oxide scale. It will also lead to the rapid formation of phosphate scale in the boiler. The thermal conductivity of iron oxide scale is very poor. The heat transfer efficiency of the iron oxide scale layer is very different from that of the furnace tube, which seriously hinders heat transfer and causes heat transfer. The local temperature on the surface is too high, so that the metal strength decreases, endangering the safety of the boiler, causing deformation of the furnace tube and causing tube explosion.
In order to reduce and eliminate the occurrence of pipe explosions and ensure the needs of production and life, seven measures to prevent boiler pipe explosions are as follows:
(1)Water quality management
The management of water treatment and water quality monitoring has been strengthened, oxygen removal and iron removal equipment have been added, and primary softening has been changed to secondary softening, so that the boiler water reaches the national standard and ensures the safe and economical operation of the boiler.
(2) Regular maintenance
Make full use of hiring someone to perform maintenance after the boiler is shut down, and ask authoritative organizations such as the Municipal Boiler Inspection Institute to conduct comprehensive internal and external inspections of the boiler to discover and deal with problems in a timely manner to ensure healthy operation of the boiler. After shutting down the furnace, promptly descale and clean the smoke pipe, and do maintenance and repairs.
(3) Combustion management
Strengthen management during operation, adjust combustion, organize reasonable combustion conditions and appropriate flame center, prevent cold air from blowing the furnace tube, improve measures to prevent wear and corrosion, and conduct reasonable sewage discharge.
(4) Increase the exhaust gas temperature
Appropriately increase the exhaust gas temperature to 180-200 degrees to prevent the generation of condensation water at the tail.
(5) Anti-corrosion and descaling
Adding high-efficiency boiler anti-corrosion and scale inhibitor BF-30a, BF-30a has the dual protection function of putting the metal of the boiler body in a passivation state and inhibiting the cathodic reaction during the metal corrosion process, effectively preventing the metal body from being in the running state and the shutdown state. Oxygen corrosion under the environment; at the same time, due to the strong chelating effect of BF-30a, after being added to the boiler water, it forms a stable water-soluble chelate with the hardness ions in the water, which increases the solubility of the hardness ions in the water and greatly inhibits the formation of scale. At the same time, it can produce the effect of slowly dissolving the original scale; because BF-30a has strong lattice distortion and dispersion, the lattice distortion function causes the calcium carbonate crystals to break during the growth process, forming small crystals with irregular appearance and dispersed The agent is adsorbed on small crystals and metal surfaces to form a double electric layer. Under the action of static electricity, the small crystals and the small crystals and the metal surface of the boiler repel each other, avoiding the deposition and generation of scale on the metal surface of the boiler in water with higher hardness.
1. Causes of boiler tube explosions
(1) Water treatment quality issuesThe boiler feed water quality is poor, there is no water treatment or the water treatment method is incorrect, and the sewage treatment is not carried out according to relevant regulations, causing scaling or corrosion on the inner wall of the pipeline. The main reason for this is that some boiler water is taken from the ground. The hardness is as high as 5mmol/L, which is high hardness water, and contains high sulfur and high iron content. Once the water is not treated properly, pipe bursts will easily occur and the boiler will be forced to shut down for emergency repairs, which will have a great impact on production and life.
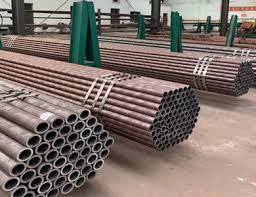
(2) Boiler tube performance issues
During the manufacturing, installation and maintenance process of boiler pipelines, stress concentration and mechanical performance degradation will occur at the welding joints. Pipeline bursts will occur in these key parts where stress concentration and mechanical performance degradation occur, which will also cause the boiler to collapse. Failure occurs and it is difficult to supply production and daily needs.
(3) Impurity problem
During the installation or maintenance of the boiler, impurities fall into the tubes, causing blockage in the tubes, resulting in poor water circulation or complete damage. The scale in the pipes falls off the inner wall and "bridges" the water circulation in a poor state.
(4) Boiler water level is too low
If the water level of the boiler is too low during operation, poor water circulation will also occur. When such a situation occurs, the temperature of the local pipeline will be too high, deforming until it bursts.
(5)Nozzle angle problem
For oil boilers, gas boilers or coal boilers, some boiler pipelines may overheat because the angle of the nozzle is not adjusted correctly during design and installation.
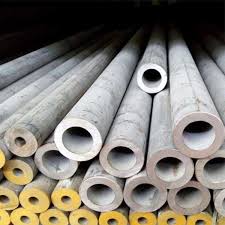
(6) Operational issues
Incorrect operation of starting and stopping the furnace causes the furnace tube to be blown by cold wind, causing the tube to expand and contract too quickly or too frequently, resulting in harmful stress.
(7) Pipeline heat concentration
The flue and firewall of the combustion chamber are damaged, causing the flue gas to short-circuit and cause heat concentration in the local furnace tube to burn out the furnace tube.
(8)Pipeline corrosion
Pipe corrosion and equipment aging lead to steel pipe explosions. Generally, it occurs in the economizer pipe on the rear heating surface. The reason is acid corrosion caused by too low exhaust gas temperature or too low feed water temperature.
(9) Local smoke speed is too fast
When installing and repairing the heating surface pipes, the pitch of the heating surface pipes and the distance between the heating surface pipe rows and the furnace wall do not meet the design requirements. Partial flue gas corridors, or partial pipes out of line, cause dust accumulation and bridging on the heating surface pipes, causing local smoke velocity to be too high, thereby increasing the wear and overheating of the pipes in this part.
(10) Pipe leakage
Due to careless construction, the sealing of the furnace wall was not strictly sealed in accordance with the construction requirements, causing eddy currents to form in the air leakage area. In this case, the pipeline will also be partially overheated or heated unevenly, and the air leakage will also increase the flow rate of the flue gas behind it. Increase, harming the tail heating surface.
(11)High temperature
The high-temperature operation of the pipe is also an important reason for boiler pipe explosion. Overheating and over-temperature pipe explosion are due to the decrease in mechanical properties of the pipe under overtemperature conditions, and the plastic deformation of the pipe under the action of pressure, that is, creep cracks and even pipe explosion.
(12)Pipeline environment
The influence of the operating environment can also cause the furnace tube to rupture, such as frequent starts and stops of the boiler, drastic changes in load, improper adjustment of the center of the flame, primary and secondary air erosion of the water-cooled wall tube, and the impact of rapid cooling due to shutdown of the furnace. Burst boiler tubes leave hidden dangers.
(13)Carbon dioxide problem
There is carbon dioxide corrosion or oxygen corrosion in the boiler heating system pipe network, or the steam condensate water pipe network. When oxygen and carbon dioxide are present in the boiler return water system at the same time, the corrosion of the system pipe network steel will be more serious. Carbon dioxide makes the water slightly acidic and damages the pipelines. Protective film, as the oxygen content increases, the carbon steel equipment and pipe network of the heating system will appear in a state of large or small ulcers, accelerating corrosion. As a result, the color of the return water or condensed water will turn yellow, red, or even soy sauce color. , The iron ion content is large, and the steel pipe is perforated. This is the reason why common steam pipes and condensate pipes corrode, perforate, and leak. This is also the reason why the service life of some newly built boiler carbon steel pipes is only 4-5 years, that is, the condensate pipes need to be replaced every 4-5 years.
The iron content in the boiler return water exceeding the standard will not only cause the "red water" phenomenon of the boiler water, but also cause corrosion under the iron oxide scale. It will also lead to the rapid formation of phosphate scale in the boiler. The thermal conductivity of iron oxide scale is very poor. The heat transfer efficiency of the iron oxide scale layer is very different from that of the furnace tube, which seriously hinders heat transfer and causes heat transfer. The local temperature on the surface is too high, so that the metal strength decreases, endangering the safety of the boiler, causing deformation of the furnace tube and causing tube explosion.
2. Five measures to prevent boiler tube explosion
In order to reduce and eliminate the occurrence of pipe explosions and ensure the needs of production and life, seven measures to prevent boiler pipe explosions are as follows:(1)Water quality management
The management of water treatment and water quality monitoring has been strengthened, oxygen removal and iron removal equipment have been added, and primary softening has been changed to secondary softening, so that the boiler water reaches the national standard and ensures the safe and economical operation of the boiler.
(2) Regular maintenance
Make full use of hiring someone to perform maintenance after the boiler is shut down, and ask authoritative organizations such as the Municipal Boiler Inspection Institute to conduct comprehensive internal and external inspections of the boiler to discover and deal with problems in a timely manner to ensure healthy operation of the boiler. After shutting down the furnace, promptly descale and clean the smoke pipe, and do maintenance and repairs.
(3) Combustion management
Strengthen management during operation, adjust combustion, organize reasonable combustion conditions and appropriate flame center, prevent cold air from blowing the furnace tube, improve measures to prevent wear and corrosion, and conduct reasonable sewage discharge.
(4) Increase the exhaust gas temperature
Appropriately increase the exhaust gas temperature to 180-200 degrees to prevent the generation of condensation water at the tail.
(5) Anti-corrosion and descaling
Adding high-efficiency boiler anti-corrosion and scale inhibitor BF-30a, BF-30a has the dual protection function of putting the metal of the boiler body in a passivation state and inhibiting the cathodic reaction during the metal corrosion process, effectively preventing the metal body from being in the running state and the shutdown state. Oxygen corrosion under the environment; at the same time, due to the strong chelating effect of BF-30a, after being added to the boiler water, it forms a stable water-soluble chelate with the hardness ions in the water, which increases the solubility of the hardness ions in the water and greatly inhibits the formation of scale. At the same time, it can produce the effect of slowly dissolving the original scale; because BF-30a has strong lattice distortion and dispersion, the lattice distortion function causes the calcium carbonate crystals to break during the growth process, forming small crystals with irregular appearance and dispersed The agent is adsorbed on small crystals and metal surfaces to form a double electric layer. Under the action of static electricity, the small crystals and the small crystals and the metal surface of the boiler repel each other, avoiding the deposition and generation of scale on the metal surface of the boiler in water with higher hardness.