In the modern industrial system, boiler tubes play an indispensable role and can be called the key "blood vessels" of the industry. Whether it is the core equipment boiler that converts thermal energy into electrical energy in a thermal power station, or the industrial boiler that provides thermal energy for the production process in the chemical, metallurgical, papermaking and other industries, they all rely on the support of boiler tubes. For this reason, it is necessary to have an in-depth understanding of the production and manufacturing methods and classification of boiler tubes, which will help us better select and use boiler tubes and ensure the smooth progress of industrial production.
Boiler tube production method
1. Material selection: Material selection is the cornerstone of boiler tube production and is related to product quality and performance. Common ones are seamless steel pipes and welded steel pipes, mostly made of carbon steel and alloy steel. When selecting materials, it is necessary to comprehensively consider factors such as the boiler's working pressure, temperature, and medium.
2. Molding process: The forming process determines the shape and size of boiler tubes. Common methods include hot rolling, cold drawing, extrusion, etc., among which hot rolling is the most commonly used.
3. Welding process (for welded steel pipes): Welding is a key link in the production of welded steel pipes, and the welding quality directly affects the use effect and safety of boiler tubes. Common welding methods include manual arc welding, submerged arc welding, etc.
4. Heat treatment effect: Heat treatment can eliminate residual stress inside the steel pipe and improve mechanical properties and corrosion resistance. Common heat treatment methods include normalizing, annealing, quenching, etc. Through proper heat treatment, the performance of boiler tubes can be optimized to better adapt to the working environment.
5. Strict testing process: Testing is the key to ensure product quality. During the production process, boiler tubes must be strictly tested, including appearance, size, mechanical properties, metallographic structure and other aspects. Appearance inspection mainly checks for defects such as cracks and sand holes; size inspection ensures compliance with standard requirements; mechanical property inspection tests tensile strength, yield strength, etc.; metallographic structure inspection analyzes whether the internal structure is normal. Only steel pipes that pass the inspection can leave the factory and enter the market.
6. Surface treatment finishing:Surface treatment is the last step in production. Through sandblasting, pickling and other methods, impurities such as oil and rust on the surface of the steel pipe can be removed to improve corrosion resistance and service life. Sandblasting uses the impact of high-speed sand flow to clean and roughen the surface; pickling removes scale and rust through chemical reaction. After surface treatment, the surface quality of the boiler tube is improved and can better resist external erosion.
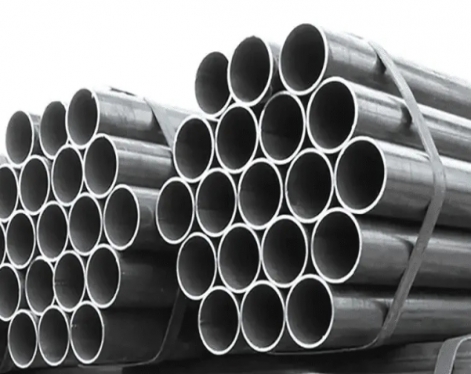
Classification of boiler tubes
1. According to the production method, boiler tubes can be divided into seamless steel tubes and welded steel tubes. The manufacturing process of welded steel pipes is relatively simple and the cost is low, but the weld is its weak point and its pressure resistance is inferior to that of seamless steel pipes. It is often used in situations where pressure and temperature requirements are not high.
2. Classification by cross-sectional shape: From the cross-sectional shape, boiler tubes are divided into round tubes and special-shaped tubes. Round tubes are the most common and are widely used in heating surface tubes, steam pipes, etc. of various boilers. Although the manufacturing process of special-shaped tubes such as square, rectangular, and hexagonal tubes is complicated, they can meet special structural and functional requirements.
3. Classification by operating temperature: According to the use temperature, boiler tubes can be divided into general boiler tubes and high-pressure boiler tubes. The general operating temperature of boiler tubes is below 350℃. They are usually made of No. 10 or No. 20 carbon steel. They are low in cost and can meet the requirements of general industrial boilers. High-pressure boiler tubes work under high temperature and high pressure environment and are often made of alloy steel. They are used in key parts such as superheater tubes and reheater tubes of high-pressure and ultra-high-pressure boilers.
Read more: Pressure Bearing Capacity of Boiler Tubes
Boiler tube production method
1. Material selection: Material selection is the cornerstone of boiler tube production and is related to product quality and performance. Common ones are seamless steel pipes and welded steel pipes, mostly made of carbon steel and alloy steel. When selecting materials, it is necessary to comprehensively consider factors such as the boiler's working pressure, temperature, and medium.
2. Molding process: The forming process determines the shape and size of boiler tubes. Common methods include hot rolling, cold drawing, extrusion, etc., among which hot rolling is the most commonly used.
3. Welding process (for welded steel pipes): Welding is a key link in the production of welded steel pipes, and the welding quality directly affects the use effect and safety of boiler tubes. Common welding methods include manual arc welding, submerged arc welding, etc.
4. Heat treatment effect: Heat treatment can eliminate residual stress inside the steel pipe and improve mechanical properties and corrosion resistance. Common heat treatment methods include normalizing, annealing, quenching, etc. Through proper heat treatment, the performance of boiler tubes can be optimized to better adapt to the working environment.
5. Strict testing process: Testing is the key to ensure product quality. During the production process, boiler tubes must be strictly tested, including appearance, size, mechanical properties, metallographic structure and other aspects. Appearance inspection mainly checks for defects such as cracks and sand holes; size inspection ensures compliance with standard requirements; mechanical property inspection tests tensile strength, yield strength, etc.; metallographic structure inspection analyzes whether the internal structure is normal. Only steel pipes that pass the inspection can leave the factory and enter the market.
6. Surface treatment finishing:Surface treatment is the last step in production. Through sandblasting, pickling and other methods, impurities such as oil and rust on the surface of the steel pipe can be removed to improve corrosion resistance and service life. Sandblasting uses the impact of high-speed sand flow to clean and roughen the surface; pickling removes scale and rust through chemical reaction. After surface treatment, the surface quality of the boiler tube is improved and can better resist external erosion.
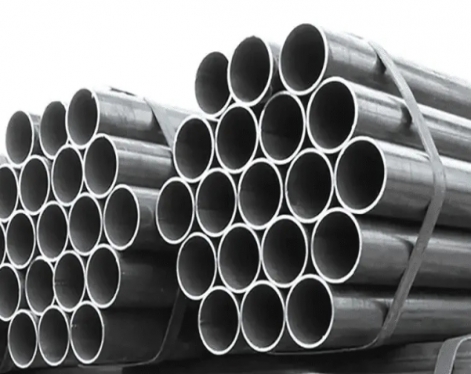
Classification of boiler tubes
1. According to the production method, boiler tubes can be divided into seamless steel tubes and welded steel tubes. The manufacturing process of welded steel pipes is relatively simple and the cost is low, but the weld is its weak point and its pressure resistance is inferior to that of seamless steel pipes. It is often used in situations where pressure and temperature requirements are not high.
2. Classification by cross-sectional shape: From the cross-sectional shape, boiler tubes are divided into round tubes and special-shaped tubes. Round tubes are the most common and are widely used in heating surface tubes, steam pipes, etc. of various boilers. Although the manufacturing process of special-shaped tubes such as square, rectangular, and hexagonal tubes is complicated, they can meet special structural and functional requirements.
3. Classification by operating temperature: According to the use temperature, boiler tubes can be divided into general boiler tubes and high-pressure boiler tubes. The general operating temperature of boiler tubes is below 350℃. They are usually made of No. 10 or No. 20 carbon steel. They are low in cost and can meet the requirements of general industrial boilers. High-pressure boiler tubes work under high temperature and high pressure environment and are often made of alloy steel. They are used in key parts such as superheater tubes and reheater tubes of high-pressure and ultra-high-pressure boilers.
Read more: Pressure Bearing Capacity of Boiler Tubes