Carbon steel ERW pipe refers to a steel pipe welded by carbon steel through resistance welding.
1.What is carbon steel pipe?
Carbon steel pipe can be used to describe various metal tubular items, and its main alloying element is 0.12%-2% carbon. In addition to carbon elements other than chromium, cobalt, molybdenum, nickel, niobium, titanium, and tungsten, vanadium and zirconium can be added to obtain their respective alloying effects. For example, compared to A106 Grade B pipe, which has low tensile strength, A333 Grade 6 pipe has high tensile strength and impact properties in cryogenic applications and is used at room temperature or higher. This is achieved by adding higher than 0.9% manganese, which is limited to 0.65% in A106 tubes.
Generally, when the maximum specified content of manganese is 1.65%, the silicon content is 0.6%, and the copper content 0.6% does not exceed the specified limits, the pipe is called a carbon steel pipe.
Carbon steel pipes are divided into four categories:
Low carbon steel pipe - Carbon content: 0.55-1.05%.
Medium carbon steel pipe - Carbon content: 0.25-10.6%.
High carbon steel pipe - carbon content: 0.9-2.5%.
Ultra-high carbon steel pipe - Carbon content: 2.5-3.0%.
As the carbon content increases, high carbon steel pipes can become harder and less ductile through quenching and tempering. If high carbon steel pipes are not heat treated, they may have low welding ability and low melting point. Large diameter pipes used for water transportation are generally made of carbon steel.
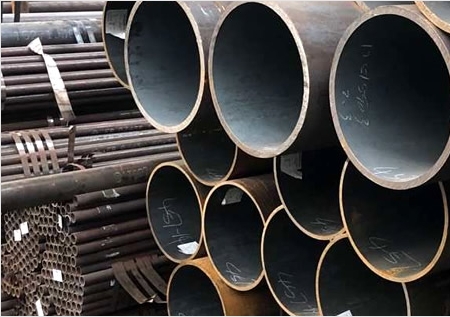
2.What is ERW steel pipe?
ERW is a general term for resistance welded steel pipes. Straight seam high-frequency resistance welding pipe (Electric Resistance Welding, referred to as ERW) ERW is the first letter of the corresponding English word. Resistance welded steel pipes are divided into two forms: AC welded steel pipes and DC welded steel pipes.
AC welding is divided into low frequency welding, medium frequency welding, super medium frequency welding and high frequency welding according to the frequency. High-frequency welding is mainly used for the production of thin-walled steel pipes or ordinary-walled steel pipes. High-frequency welding is divided into contact welding and induction welding. DC welding is generally used for small diameter steel pipes.
Therefore, in summary, high-frequency welded pipe is included in ERW welded pipe, which is a kind of ERW welded pipe produced by high-frequency welding process. ERW straight seam welded pipe is a steel pipe with advanced product performance, leading quality and relatively economical performance in the field of oil and gas storage and transportation.
3.Manufacturing process of carbon steel ERW pipes
The manufacturing process of carbon steel ERW pipes involves several key steps:
(1)Material Selection
High-quality carbon steel coils or strips are selected based on the required specifications.
(2)Forming
The flat steel strip is passed through a series of rollers to gradually form it into a cylindrical shape.
(3)Welding
The edges of the formed strip are heated to the welding temperature using a high-frequency current and then fused together under pressure to create a solid weld seam.
(4)Sizing
The welded pipe is passed through additional rolls to achieve the desired dimensions and roundness.
(4)Cutting and Finishing
The pipe is cut to the required lengths, and the ends are finished according to specific customer requirements.
4.Applications of carbon steel ERW pipes
Carbon steel ERW pipes are widely used in various industrial applications, including:
(1)Oil and Gas Industry
Transportation of oil, gas, and petroleum products due to their high-pressure bearing capacity and durability.
(2)Construction
Structural applications such as building frameworks, scaffolding, and support columns.
(3)Water Transmission
Distribution and transmission systems for water and other fluids due to their corrosion resistance.
(4)Industrial Processes
Conveying various fluids and gases in industrial processing plants.
1.What is carbon steel pipe?
Carbon steel pipe can be used to describe various metal tubular items, and its main alloying element is 0.12%-2% carbon. In addition to carbon elements other than chromium, cobalt, molybdenum, nickel, niobium, titanium, and tungsten, vanadium and zirconium can be added to obtain their respective alloying effects. For example, compared to A106 Grade B pipe, which has low tensile strength, A333 Grade 6 pipe has high tensile strength and impact properties in cryogenic applications and is used at room temperature or higher. This is achieved by adding higher than 0.9% manganese, which is limited to 0.65% in A106 tubes.
Generally, when the maximum specified content of manganese is 1.65%, the silicon content is 0.6%, and the copper content 0.6% does not exceed the specified limits, the pipe is called a carbon steel pipe.
Carbon steel pipes are divided into four categories:
Low carbon steel pipe - Carbon content: 0.55-1.05%.
Medium carbon steel pipe - Carbon content: 0.25-10.6%.
High carbon steel pipe - carbon content: 0.9-2.5%.
Ultra-high carbon steel pipe - Carbon content: 2.5-3.0%.
As the carbon content increases, high carbon steel pipes can become harder and less ductile through quenching and tempering. If high carbon steel pipes are not heat treated, they may have low welding ability and low melting point. Large diameter pipes used for water transportation are generally made of carbon steel.
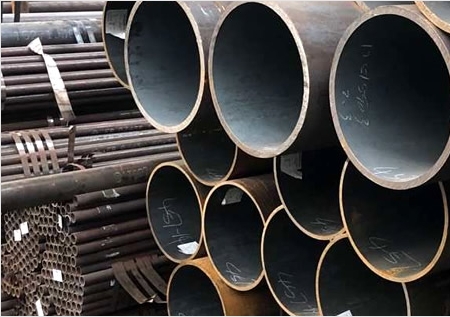
2.What is ERW steel pipe?
ERW is a general term for resistance welded steel pipes. Straight seam high-frequency resistance welding pipe (Electric Resistance Welding, referred to as ERW) ERW is the first letter of the corresponding English word. Resistance welded steel pipes are divided into two forms: AC welded steel pipes and DC welded steel pipes.
AC welding is divided into low frequency welding, medium frequency welding, super medium frequency welding and high frequency welding according to the frequency. High-frequency welding is mainly used for the production of thin-walled steel pipes or ordinary-walled steel pipes. High-frequency welding is divided into contact welding and induction welding. DC welding is generally used for small diameter steel pipes.
Therefore, in summary, high-frequency welded pipe is included in ERW welded pipe, which is a kind of ERW welded pipe produced by high-frequency welding process. ERW straight seam welded pipe is a steel pipe with advanced product performance, leading quality and relatively economical performance in the field of oil and gas storage and transportation.
3.Manufacturing process of carbon steel ERW pipes
The manufacturing process of carbon steel ERW pipes involves several key steps:
(1)Material Selection
High-quality carbon steel coils or strips are selected based on the required specifications.
(2)Forming
The flat steel strip is passed through a series of rollers to gradually form it into a cylindrical shape.
(3)Welding
The edges of the formed strip are heated to the welding temperature using a high-frequency current and then fused together under pressure to create a solid weld seam.
(4)Sizing
The welded pipe is passed through additional rolls to achieve the desired dimensions and roundness.
(4)Cutting and Finishing
The pipe is cut to the required lengths, and the ends are finished according to specific customer requirements.
4.Applications of carbon steel ERW pipes
Carbon steel ERW pipes are widely used in various industrial applications, including:
(1)Oil and Gas Industry
Transportation of oil, gas, and petroleum products due to their high-pressure bearing capacity and durability.
(2)Construction
Structural applications such as building frameworks, scaffolding, and support columns.
(3)Water Transmission
Distribution and transmission systems for water and other fluids due to their corrosion resistance.
(4)Industrial Processes
Conveying various fluids and gases in industrial processing plants.
Previous:ASTM A53 black steel pipe