Carbon steel welded tubes are integral components in various industrial sectors, serving critical roles in structural frameworks, mechanical systems, fluid transportation, and heat transfer applications. These tubes are manufactured through a welding process that joins flat or coiled carbon steel strips to form cylindrical tubes of varying dimensions and specifications. Understanding the characteristics, production methods, quality considerations, and diverse applications of carbon steel welded tubes is essential for engineers, manufacturers, and end-users across multiple industries.
1.Manufacturing Process
Carbon steel welded tubes are produced through a series of manufacturing steps:
(1)Raw Material Selection: The process begins with the selection of high-quality carbon steel coils or strips, which undergo inspection for chemical composition, mechanical properties, surface condition, and dimensional tolerances to ensure compliance with industry standards such as ASTM A513, ASTM A787, and EN 10305-3.
(2)Forming: The selected steel strips are shaped into a cylindrical form using specialized equipment such as roll forming mills, continuous forming machines, or high-frequency welding lines. The forming process ensures precise shaping of the strips into tubes with consistent dimensions and tight tolerances.
(3)Welding: Subsequent to forming, the edges of the steel strips are welded together using various welding techniques such as high-frequency induction welding, electric resistance welding (ERW), submerged arc welding, or laser welding. The welding process creates strong and durable joints, ensuring the integrity and strength of the tube structure.
(4)Sizing and Finishing: Once welded, the tubes undergo sizing and shaping operations to achieve the desired outside diameter, wall thickness, and length. Additional finishing processes may include straightening, cutting to specific lengths, deburring, and surface treatment to meet quality requirements.
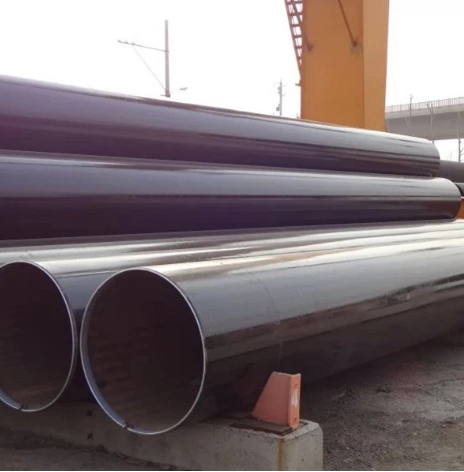
2.Characteristics of Carbon Steel Welded Tubes:
(1)Structural Integrity: Carbon steel welded tubes offer excellent structural integrity and load-bearing capacity, making them suitable for a wide range of construction, infrastructure, and industrial applications.
(2)Diverse Specifications: These tubes are available in various specifications, including round, square, rectangular, and oval shapes, with a wide range of dimensions, wall thicknesses, and surface finishes to meet specific application requirements.
(3)Corrosion Resistance: While carbon steel is susceptible to corrosion, proper surface treatment and coatings can enhance the corrosion resistance of welded tubes, making them suitable for applications where exposure to corrosive environments is a concern.
(4)Cost-Effectiveness: Carbon steel welded tubes are cost-effective solutions for structural and mechanical applications, offering a balance between strength, durability, and affordability.
3.Quality Considerations:
(1)Material Inspection: Strict material inspection and testing protocols ensure that the carbon steel used for welded tubes meets the required chemical composition, mechanical properties, and surface conditions as per industry standards.
(2)Welding Quality: The welding process is a critical aspect of quality control, requiring meticulous attention to welding parameters, joint preparation, and weld integrity to minimize defects and ensure strong, reliable welds.
(3)Dimensional Accuracy: Accurate dimensional control of outside diameter, wall thickness, straightness, and ovality is crucial to meet design specifications and structural requirements.
(4)Surface Finish and Coating: Surface finish and protective coatings play a significant role in enhancing the appearance and corrosion resistance of carbon steel welded tubes, especially for outdoor and exposed applications.
(5)Non-Destructive Testing (NDT): Non-destructive testing methods such as ultrasonic testing (UT), eddy current testing (ECT), and visual inspection are employed to detect internal and surface defects, ensuring the overall quality and integrity of the welded tubes.
3.Applications of Carbon Steel Welded Tubes:
(1)Structural Construction: These tubes are widely used in building construction, infrastructure projects, and steel structures for their strength, versatility, and cost-effectiveness.
(2)Mechanical Systems: Carbon steel welded tubes find applications in mechanical and industrial systems, including conveyors, material handling equipment, support structures, and machinery components.
(3)Fluid Transportation: They are utilized for conveying water, gas, steam, and other fluids in plumbing, HVAC systems, process piping, and general fluid transportation applications.
(4)Heat Transfer Equipment: Carbon steel welded tubes are employed in heat exchangers, boilers, and condensers for their thermal conductivity and compatibility with heating and cooling fluids.
In conclusion, carbon steel welded tubes are essential components in a wide array of industrial and commercial applications, providing structural support, fluid conveyance, and heat transfer capabilities. By adhering to stringent manufacturing processes, quality control measures, and compliance with industry standards, these welded tubes offer reliable performance, durability, and cost-effective solutions for diverse engineering and construction needs.
1.Manufacturing Process
Carbon steel welded tubes are produced through a series of manufacturing steps:
(1)Raw Material Selection: The process begins with the selection of high-quality carbon steel coils or strips, which undergo inspection for chemical composition, mechanical properties, surface condition, and dimensional tolerances to ensure compliance with industry standards such as ASTM A513, ASTM A787, and EN 10305-3.
(2)Forming: The selected steel strips are shaped into a cylindrical form using specialized equipment such as roll forming mills, continuous forming machines, or high-frequency welding lines. The forming process ensures precise shaping of the strips into tubes with consistent dimensions and tight tolerances.
(3)Welding: Subsequent to forming, the edges of the steel strips are welded together using various welding techniques such as high-frequency induction welding, electric resistance welding (ERW), submerged arc welding, or laser welding. The welding process creates strong and durable joints, ensuring the integrity and strength of the tube structure.
(4)Sizing and Finishing: Once welded, the tubes undergo sizing and shaping operations to achieve the desired outside diameter, wall thickness, and length. Additional finishing processes may include straightening, cutting to specific lengths, deburring, and surface treatment to meet quality requirements.
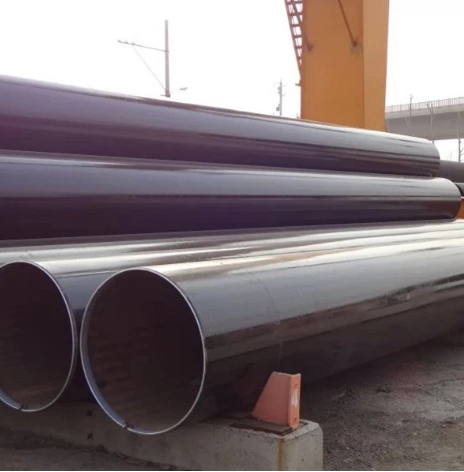
2.Characteristics of Carbon Steel Welded Tubes:
(1)Structural Integrity: Carbon steel welded tubes offer excellent structural integrity and load-bearing capacity, making them suitable for a wide range of construction, infrastructure, and industrial applications.
(2)Diverse Specifications: These tubes are available in various specifications, including round, square, rectangular, and oval shapes, with a wide range of dimensions, wall thicknesses, and surface finishes to meet specific application requirements.
(3)Corrosion Resistance: While carbon steel is susceptible to corrosion, proper surface treatment and coatings can enhance the corrosion resistance of welded tubes, making them suitable for applications where exposure to corrosive environments is a concern.
(4)Cost-Effectiveness: Carbon steel welded tubes are cost-effective solutions for structural and mechanical applications, offering a balance between strength, durability, and affordability.
3.Quality Considerations:
(1)Material Inspection: Strict material inspection and testing protocols ensure that the carbon steel used for welded tubes meets the required chemical composition, mechanical properties, and surface conditions as per industry standards.
(2)Welding Quality: The welding process is a critical aspect of quality control, requiring meticulous attention to welding parameters, joint preparation, and weld integrity to minimize defects and ensure strong, reliable welds.
(3)Dimensional Accuracy: Accurate dimensional control of outside diameter, wall thickness, straightness, and ovality is crucial to meet design specifications and structural requirements.
(4)Surface Finish and Coating: Surface finish and protective coatings play a significant role in enhancing the appearance and corrosion resistance of carbon steel welded tubes, especially for outdoor and exposed applications.
(5)Non-Destructive Testing (NDT): Non-destructive testing methods such as ultrasonic testing (UT), eddy current testing (ECT), and visual inspection are employed to detect internal and surface defects, ensuring the overall quality and integrity of the welded tubes.
3.Applications of Carbon Steel Welded Tubes:
(1)Structural Construction: These tubes are widely used in building construction, infrastructure projects, and steel structures for their strength, versatility, and cost-effectiveness.
(2)Mechanical Systems: Carbon steel welded tubes find applications in mechanical and industrial systems, including conveyors, material handling equipment, support structures, and machinery components.
(3)Fluid Transportation: They are utilized for conveying water, gas, steam, and other fluids in plumbing, HVAC systems, process piping, and general fluid transportation applications.
(4)Heat Transfer Equipment: Carbon steel welded tubes are employed in heat exchangers, boilers, and condensers for their thermal conductivity and compatibility with heating and cooling fluids.
In conclusion, carbon steel welded tubes are essential components in a wide array of industrial and commercial applications, providing structural support, fluid conveyance, and heat transfer capabilities. By adhering to stringent manufacturing processes, quality control measures, and compliance with industry standards, these welded tubes offer reliable performance, durability, and cost-effective solutions for diverse engineering and construction needs.
Previous:Steel well casing pipes