1. Overview of casing threads
(1)DefinitionSteel casing pipe threads are an important part of connecting casing and are used to seal and connect the casing.
(2)Function
Threads can ensure the sealing and connection strength of oil casing in harsh environments such as high pressure and high temperature, ensuring the safety and stability of the oil extraction process.
(3) steel casing thread type
①API round thread
API round thread is the most widely used thread type in petroleum casing connections. It has the advantages of simple structure, easy processing and detection.
②API partial trapezoidal thread
API partial trapezoidal thread is a high-performance oil casing connection thread with higher connection strength and sealing performance.
③Special thread
Special threads are oil casing connection threads designed for specific needs, such as casing connections with special requirements such as high anti-extrusion and high air tightness.
(4) Oil casing thread standards
①API standard
The thread of oil casing should comply with the relevant standards of API (American Petroleum Institute), such as API SPEC 5CT, etc.
②ISO standard
ISO (International Organization for Standardization) has also formulated corresponding oil casing thread standards, which are similar to API standards, but differ in some details.
③Other national standards
Different countries have also formulated corresponding Shibo casing thread standards based on their actual conditions and needs, such as the Russian GOST standard, the German DIN standard, etc.
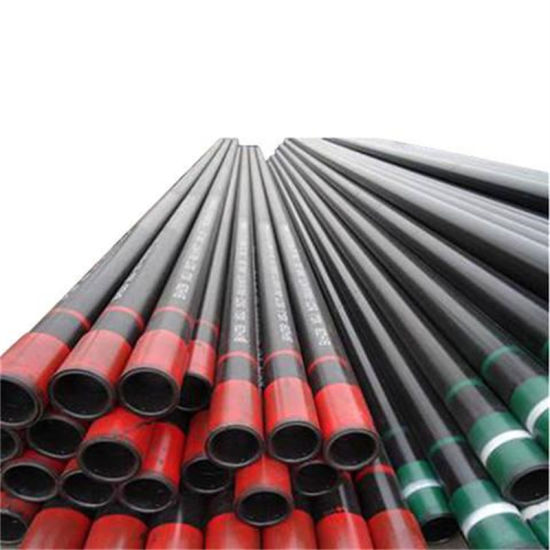
2. Casing thread structure and technical parameters
(1) Casing pipe thread structure①Tooth shape
Adopt V-shaped or trapezoidal tooth form to ensure connection strength and sealing.
② Pitch
Select the appropriate pitch according to the casing specifications and strength requirements.
③Tooth height
The tooth height affects the connection strength and sealing performance and needs to be determined according to the standard.
④ Taper
The taper is used to ensure concentricity and sealing after the casing is connected.
(2)Steel casing thread connection method
①Butt connection
Align the threads of the two sleeves and connect them by rotating them.
②Torque control
Use a special tightening tool to tightly connect the casing threads together.
③Buckle connection
Torque needs to be controlled during the connection process to ensure connection strength and sealing.
④Inspection and acceptance
After the connection is completed, inspection and acceptance are required to ensure that the connection quality meets the requirements.
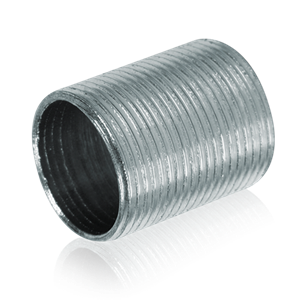
3. Steel casing thread processing technology and equipment
(1)Processing process flow①Preparation of raw materials
Select high-quality steel billets and conduct chemical composition and mechanical performance testing to ensure that the raw materials meet the standards.
②Heat treatment
The steel billet is heated, kept and cooled to improve its internal structure and mechanical properties.
③Turning processing
Use a lathe to turn the outer circle and inner hole of the heat-treated steel billet to achieve the specified dimensional accuracy and surface roughness.
④Thread processing
A special threading machine tool is used to thread the turned casing, including cutting, trimming and inspection.
⑤ Cleaning and rust prevention
Clean the processed casing to remove surface oil and impurities, and then apply anti-rust oil to prevent rust.
(2) Introduction to processing equipment
①Lathe
Used for turning the outer circle and inner hole of casing to ensure dimensional accuracy and surface quality.
②Threading machine tools
Specially used for processing oil casing threads, it has the characteristics of high precision, high efficiency and high stability.
③Heat treatment equipment
Including heating furnaces, heating furnaces and cooling equipment, etc., used to improve the internal structure and mechanical properties of steel billets.
④Testing equipment
Including dimensional measuring instruments, hardness testers, metallographic microscopes, etc., used to detect various performance indicators of casing.
(3) Precautions during processing
①Safe operation
Strictly abide by the machine tool operating procedures and wear protective equipment to ensure personal safety.
②Equipment maintenance
Carry out regular maintenance and upkeep on processing equipment to ensure that the equipment is in good condition and to maximize processing accuracy and efficiency.
③Quality control
Strengthen the quality inspection and control of raw materials, semi-finished products and finished products to ensure that product quality meets standard requirements.
④Environmental protection requirements
Pay attention to reducing the emission of noise, dust, waste liquid and other pollutants during processing to protect the environment.
4. Petroleum casing pipe thread detection methods and standards
(1)Detection methods and procedures①Appearance inspection
Use visual inspection or a magnifying glass to observe whether there are cracks, rust, burrs and other defects on the thread surface.
②Dimensional inspection
Use measuring tools such as calipers and micrometers to detect key dimensions such as the major diameter, minor diameter, and pitch of the thread.
③Tightness test
Use special tools such as plug gauges or ring gauges to check the tightness of the threads to ensure a secure connection.
④Torque detection
During the connection process, use a torque wrench to check whether the connection torque meets the requirements.
(2) Testing standards and specifications
①API standard
The thread of oil casing should comply with the relevant standards of API (American Petroleum Institute), such as API SPEC 5CT, etc.
②ISO standard
The International Organization for Standardization (ISO) has also formulated relevant standards for oil casing threads, such as ISO 11960.
③National standards
Countries have also formulated corresponding national standards, such as China's GB/T 9253, etc.
④Corporate standards
Some large petroleum companies will also formulate their own corporate standards to guide production and testing.
(2)Common problems and solutions
① Thread damage
Thread damage may occur due to improper handling during processing or transportation. Solutions include increased protection during processing and transportation, as well as repair or replacement of damaged threads.
②The size is out of tolerance
Due to insufficient accuracy of processing equipment or improper operation, solutions for thread size deviations may include improving the accuracy of processing equipment, strengthening operator training, and strengthening dimensional inspection.
③Insufficient tightness
Insufficient tightness may occur due to insufficient thread machining accuracy or improper operation during the connection process. Solutions include improving processing accuracy, strengthening monitoring and adjustment during the connection process, and using high-quality sealing materials.
④The torque is too large or too small
Due to improper operation or equipment failure during the connection process, the torque may be too large or too small. Solutions include enhanced operator training, regular maintenance and calibration of torque wrenches, and the use of high-quality joining materials.
(3) Oil casing thread maintenance and upkeep
①Keep the threads clean
Regularly remove impurities and oil on the thread surface to prevent adverse effects on sealing performance.
② Check the thread tightening
Regularly check whether the threaded connection is loose and ensure the connection is tight and reliable.
③Lubrication and maintenance
According to the usage environment and requirements, regularly lubricate and maintain the threads to reduce wear and prevent corrosion.
(4)Fault diagnosis and troubleshooting methods
①Oil leakage fault diagnosis
Observe whether there is oil leakage from the threaded connection. If there is, it may be a poor seal or the thread is damaged. The seal needs to be replaced or the thread repaired in time.
②Loose fault diagnosis
Check whether the threaded connection is loose. If it is loose, it may cause leakage and safety hazards, and it needs to be tightened in time.
③Wear fault diagnosis
By observing and measuring the wear on the thread surface, it is determined whether the sleeve needs to be replaced or other repair measures are taken.
(5) Suggestions for improving service life
①Choose high-quality materials
High-quality petroleum casing and thread materials are selected to improve their wear resistance and corrosion resistance.
②Standardize installation operations
During the installation process, the operation must be strictly followed to ensure the tightness and reliability of the threaded connection.
③Strengthen maintenance
Perform regular maintenance on oil casing threads to detect and deal with potential problems in a timely manner to extend their service life.
④Avoid overload use
During use, avoid overloading the oil casing to reduce the risk of wear and damage.