Galvanized angle steel is a carbon structural steel for construction. It is a simple cross-section steel material, mainly used for metal components and factory frames. It requires good weldability, plastic deformation performance and certain mechanical strength during use. The raw material billet for producing galvanized angle steel is low-carbon square billet, and the finished galvanized angle steel is delivered in hot-rolled, normalized or hot-rolled state. Galvanized angle steel is an important anti-corrosion upgrade product for steel materials and is widely used in the fields of construction, electricity, communications, etc. Its classification and quality directly affect the life and safety of the project.
Classification of galvanized angle steel
1. Classification by galvanizing process
Hot-dip galvanized angle steel: The angle steel is immersed in molten zinc liquid to form a zinc layer with a thickness of ≥85μm (GB/T 13912 standard), which has strong corrosion resistance and is suitable for long-term outdoor use.
Electro-galvanized angle steel: The zinc layer is deposited by electrolysis, the thickness is usually 8-15μm, the cost is low but the weather resistance is weak, and it is mostly used indoors or for short-term protection.
2. Classification by surface treatment
Passivated galvanized angle steel: The surface of the zinc layer is treated with chromate to form a rainbow or white passivation film, which can withstand salt spray for more than 72 hours (ASTM B633 standard).
Unpassivated galvanized angle steel: The zinc layer is directly exposed, easily oxidized and discolored, and requires coating protection.
3. Classification by purpose
For building structures: Q235B material, moderate strength, used for brackets and trusses.
For power towers: Q345B material, high strength, wind and earthquake resistance, must comply with GB/T 2694 standard.
Specially used for ships: Seawater corrosion resistant type, zinc layer thickness ≥110μm.
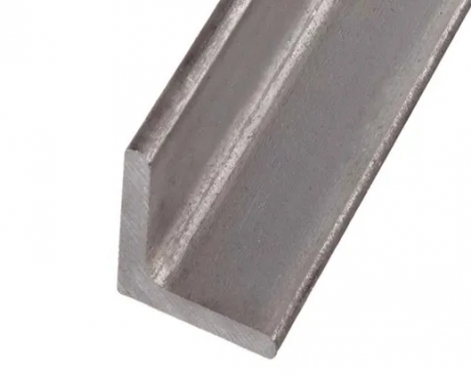
Five core indicators of quality control
1. Galvanized layer thickness
Hot-dip galvanizing: average zinc layer thickness ≥85μm (DN≤65mm), local minimum ≥70μm.
Electrogalvanizing: average zinc layer thickness ≥12μm, suitable for light corrosion environment.
2. Adhesion test
The cross-hatch test (ASTM D3359) is used, and the zinc layer is qualified if it does not peel off; or the bending test (GB/T 2976) is used, and the zinc layer does not fall off after 180° bending.
3. Appearance quality
The surface should be smooth without zinc nodules or missing plating, and slight color difference is allowed locally.
There should be no deformation that affects use, such as distortion ≤2mm/m.
4. Dimensional accuracy
Side width deviation: ±0.8mm (∠50×50×5 or less), ±1.2mm (∠100×100×10 or more).
Wall thickness deviation: ±10%.
5. Mechanical properties
Yield strength ≥ 235MPa (Q235B), tensile strength ≥ 375MPa, elongation after break ≥ 26% (GB/T 706 standard).
Conclusion
The classification and quality of galvanized angle steel directly affect the cost of the entire life cycle of the project. By accurately matching the process and strictly controlling the quality and mechanical properties of the zinc layer, it can be ensured that it can serve stably for more than 15 years in harsh environments. In the future, environmentally friendly galvanizing processes and intelligent detection technologies will become the development trend of the industry.
Read more: Advantages and Characteristics of Galvanized Angle Steel
Classification of galvanized angle steel
1. Classification by galvanizing process
Hot-dip galvanized angle steel: The angle steel is immersed in molten zinc liquid to form a zinc layer with a thickness of ≥85μm (GB/T 13912 standard), which has strong corrosion resistance and is suitable for long-term outdoor use.
Electro-galvanized angle steel: The zinc layer is deposited by electrolysis, the thickness is usually 8-15μm, the cost is low but the weather resistance is weak, and it is mostly used indoors or for short-term protection.
2. Classification by surface treatment
Passivated galvanized angle steel: The surface of the zinc layer is treated with chromate to form a rainbow or white passivation film, which can withstand salt spray for more than 72 hours (ASTM B633 standard).
Unpassivated galvanized angle steel: The zinc layer is directly exposed, easily oxidized and discolored, and requires coating protection.
3. Classification by purpose
For building structures: Q235B material, moderate strength, used for brackets and trusses.
For power towers: Q345B material, high strength, wind and earthquake resistance, must comply with GB/T 2694 standard.
Specially used for ships: Seawater corrosion resistant type, zinc layer thickness ≥110μm.
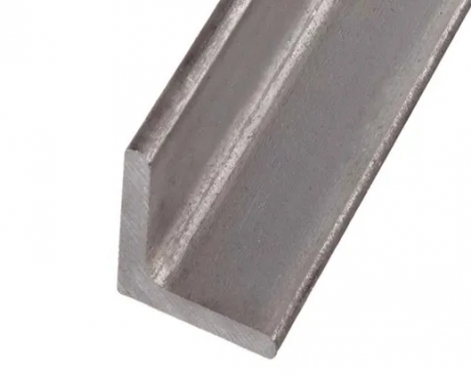
Five core indicators of quality control
1. Galvanized layer thickness
Hot-dip galvanizing: average zinc layer thickness ≥85μm (DN≤65mm), local minimum ≥70μm.
Electrogalvanizing: average zinc layer thickness ≥12μm, suitable for light corrosion environment.
2. Adhesion test
The cross-hatch test (ASTM D3359) is used, and the zinc layer is qualified if it does not peel off; or the bending test (GB/T 2976) is used, and the zinc layer does not fall off after 180° bending.
3. Appearance quality
The surface should be smooth without zinc nodules or missing plating, and slight color difference is allowed locally.
There should be no deformation that affects use, such as distortion ≤2mm/m.
4. Dimensional accuracy
Side width deviation: ±0.8mm (∠50×50×5 or less), ±1.2mm (∠100×100×10 or more).
Wall thickness deviation: ±10%.
5. Mechanical properties
Yield strength ≥ 235MPa (Q235B), tensile strength ≥ 375MPa, elongation after break ≥ 26% (GB/T 706 standard).
Conclusion
The classification and quality of galvanized angle steel directly affect the cost of the entire life cycle of the project. By accurately matching the process and strictly controlling the quality and mechanical properties of the zinc layer, it can be ensured that it can serve stably for more than 15 years in harsh environments. In the future, environmentally friendly galvanizing processes and intelligent detection technologies will become the development trend of the industry.
Read more: Advantages and Characteristics of Galvanized Angle Steel