Cold-drawn pipe is a kind of steel pipe, that is, it is classified according to different production processes, which is different from hot-rolled (expanded) pipes. It is processed by multi-pass cold drawing in the process of expanding the diameter of the blank or raw tube, usually on a single-chain or double-chain cold drawing machine. Cold-rolled (dial) steel pipes are divided into general steel pipes (seamless pipes), low and medium pressure boiler steel pipes, high-pressure boiler steel pipes, alloy steel pipes, stainless steel pipes, petroleum cracking pipes, machining pipes, and thick-walled pipes,it also includes carbon thin-walled steel pipes, alloy thin-walled steel pipes, stainless steel thin-walled steel pipes, and special-shaped steel pipes.
Cold drawn tube specification
The outer diameter of the cold-drawn steel pipe can reach 6mm, the wall thickness can reach 0.25mm, the outer diameter of the thin-walled pipe can reach 5mm, the wall thickness is less than 0.25mm, and the precision and surface quality are obviously better than the hot-rolled (expanded) pipe. However, due to technical constraints, its caliber and length are limited to a certain extent.
Cold drawn steel pipe specifications
Cold-drawn steel is a processing technology for steel, which refers to various cold-drawn steel produced by cold-drawing method. The characteristics of cold drawn steel are: high precision and good surface quality. Cold drawing is mainly used for the production of steel wire, but also for the production of round steel and hexagonal steel with a diameter of less than 50mm, and steel pipes with a diameter of less than 76mm.
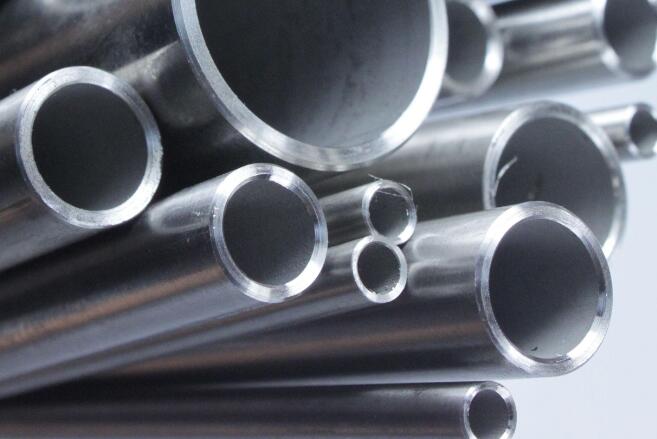
Basic process of cold drawn steel
① Raw materials should be inspected before cold drawing. For steel products with unknown steel grades or without factory certificates, samples should be taken for inspection. In case of oblate, barbed, hard and wet steel bars with irregular cross-sections, they should not be used for drawing, so as not to damage the drawing die and affect the quality. Steel bars must be rolled and derusted before cold drawing. The derusting device can use the wire drawing machine reel and the wire rod turret. Among them, there are 3 to 6 grooved shelling wheels that are staggered in one direction or staggered up and down. The steel bar can be derusted by repeatedly bending up and down, left and right. It is also possible to use a waste wire drawing die that is basically the same diameter as the steel bar to remove rust mechanically.
②In order to facilitate the steel bar to pass through the wire drawing die, the steel bar head should be rolled thinner (150~200 mm in length), and rolled to a diameter 0.5~0.8 mm smaller than the wire drawing die hole, so as to pass through the die hole smoothly. In order to reduce the number of rolling heads, the steel bars can be connected by butt welding, but the convex seam at the weld should be smoothed with a grinding wheel file to protect the equipment and the drawing die.
③Before operation, the equipment should be inspected and run once without load according to the routine. When installing the wire drawing die, it is necessary to distinguish the front and back. After installation, the fixing bolts should be tightened.
④ In order to reduce the wire drawing force and the loss of the wire drawing die hole, lubricant must be applied when drawing. Generally, a lubricating box is installed before the wire drawing die, so that the viscous lubricant of the steel bar enters the wire drawing die.
⑤ Wire drawing speed should be controlled at 50~70 m/min. The continuous drawing of the steel bar should not exceed 3 times. If it is necessary to pull out again, the internal stress of the steel bar should be eliminated, and the steel bar should be softened by low temperature (600 ℃ ~ 800 ℃) annealing treatment. After heating, take it out and bury it in the sand to make it cool slowly. The cooling rate should be controlled within 150°C/h.
⑥The finished wire drawing should be checked for defects such as sand holes, groove marks, and skin clips at any time, so as to replace the wire drawing die or adjust the speed at any time.
The basic process of cold drawn tube
① Pipe material supply, the pipe materials used are hot-rolled finished pipes or semi-finished pipes, extruded pipes and welded pipes;
②Pipe material preparation, including inspection, bundling, pickling, cleaning, rinsing, neutralization, drying, lubricating, etc.;
③ cold working (cold rolling or cold drawing);
④Finishing of finished products includes heat treatment of finished products, straightening, sampling, head and tail cutting, inspection (manual inspection and various flaw detection), hydraulic test, oiling, packaging, warehousing, etc. Different products have different finishing contents.
The production feature of the cold-processed pipe unit is that the pipe material usually undergoes multiple cold deformations and produces work hardening from input to processing into finished products. Therefore, the entire production process is composed of multiple preparation processes and deformation processes, and has the characteristics of reciprocating cycles. Therefore, there are many processes, long production cycle, large metal consumption, low production efficiency, and generally small production scale.
Cold drawn tube specification
The outer diameter of the cold-drawn steel pipe can reach 6mm, the wall thickness can reach 0.25mm, the outer diameter of the thin-walled pipe can reach 5mm, the wall thickness is less than 0.25mm, and the precision and surface quality are obviously better than the hot-rolled (expanded) pipe. However, due to technical constraints, its caliber and length are limited to a certain extent.
Cold drawn steel pipe specifications
Cold-drawn steel is a processing technology for steel, which refers to various cold-drawn steel produced by cold-drawing method. The characteristics of cold drawn steel are: high precision and good surface quality. Cold drawing is mainly used for the production of steel wire, but also for the production of round steel and hexagonal steel with a diameter of less than 50mm, and steel pipes with a diameter of less than 76mm.
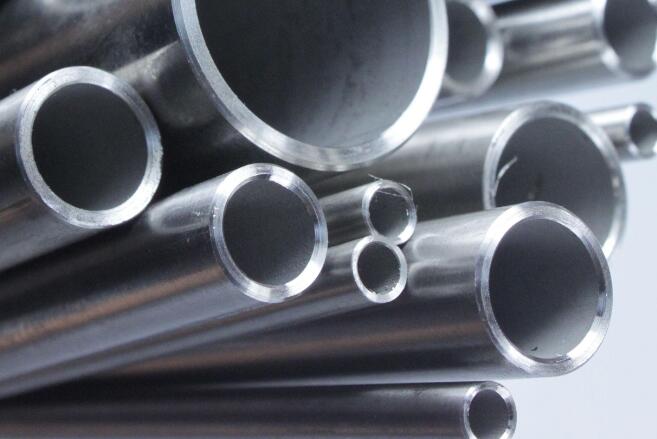
Basic process of cold drawn steel
① Raw materials should be inspected before cold drawing. For steel products with unknown steel grades or without factory certificates, samples should be taken for inspection. In case of oblate, barbed, hard and wet steel bars with irregular cross-sections, they should not be used for drawing, so as not to damage the drawing die and affect the quality. Steel bars must be rolled and derusted before cold drawing. The derusting device can use the wire drawing machine reel and the wire rod turret. Among them, there are 3 to 6 grooved shelling wheels that are staggered in one direction or staggered up and down. The steel bar can be derusted by repeatedly bending up and down, left and right. It is also possible to use a waste wire drawing die that is basically the same diameter as the steel bar to remove rust mechanically.
②In order to facilitate the steel bar to pass through the wire drawing die, the steel bar head should be rolled thinner (150~200 mm in length), and rolled to a diameter 0.5~0.8 mm smaller than the wire drawing die hole, so as to pass through the die hole smoothly. In order to reduce the number of rolling heads, the steel bars can be connected by butt welding, but the convex seam at the weld should be smoothed with a grinding wheel file to protect the equipment and the drawing die.
③Before operation, the equipment should be inspected and run once without load according to the routine. When installing the wire drawing die, it is necessary to distinguish the front and back. After installation, the fixing bolts should be tightened.
④ In order to reduce the wire drawing force and the loss of the wire drawing die hole, lubricant must be applied when drawing. Generally, a lubricating box is installed before the wire drawing die, so that the viscous lubricant of the steel bar enters the wire drawing die.
⑤ Wire drawing speed should be controlled at 50~70 m/min. The continuous drawing of the steel bar should not exceed 3 times. If it is necessary to pull out again, the internal stress of the steel bar should be eliminated, and the steel bar should be softened by low temperature (600 ℃ ~ 800 ℃) annealing treatment. After heating, take it out and bury it in the sand to make it cool slowly. The cooling rate should be controlled within 150°C/h.
⑥The finished wire drawing should be checked for defects such as sand holes, groove marks, and skin clips at any time, so as to replace the wire drawing die or adjust the speed at any time.
The basic process of cold drawn tube
① Pipe material supply, the pipe materials used are hot-rolled finished pipes or semi-finished pipes, extruded pipes and welded pipes;
②Pipe material preparation, including inspection, bundling, pickling, cleaning, rinsing, neutralization, drying, lubricating, etc.;
③ cold working (cold rolling or cold drawing);
④Finishing of finished products includes heat treatment of finished products, straightening, sampling, head and tail cutting, inspection (manual inspection and various flaw detection), hydraulic test, oiling, packaging, warehousing, etc. Different products have different finishing contents.
The production feature of the cold-processed pipe unit is that the pipe material usually undergoes multiple cold deformations and produces work hardening from input to processing into finished products. Therefore, the entire production process is composed of multiple preparation processes and deformation processes, and has the characteristics of reciprocating cycles. Therefore, there are many processes, long production cycle, large metal consumption, low production efficiency, and generally small production scale.