The cold working of seamless pipe includes cold rolling, cold drawing, cold tension reducing and spinning, etc. It is the main method for producing precision thin-walled and high-strength steel pipes. Among them, cold rolling and cold drawing are commonly used high-efficiency production methods for cold working of seamless pipes.
Compared with hot rolling, cold working has the following advantages:
1) It can produce large-diameter thin-walled pipes;
2) The geometrical dimension of the seamless pipe has high precision;
3) High surface finish;
4) It is helpful for grain refinement, and with the corresponding heat treatment method, higher comprehensive mechanical properties can be obtained;
5) It can produce various special shapes and cross-sections and some materials with narrow thermal processing temperature range, low high temperature toughness and good room temperature plasticity.
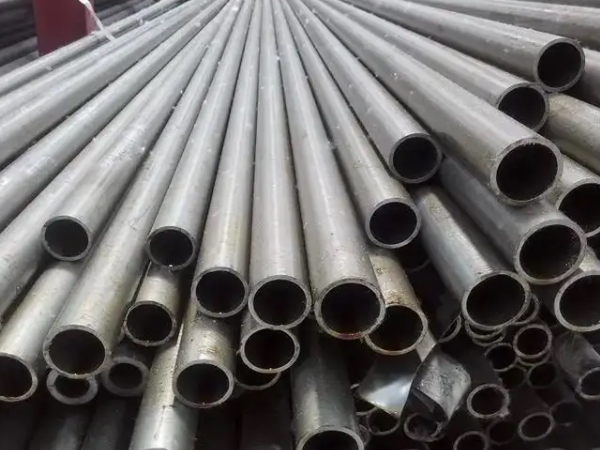
The outstanding advantage of cold rolling is its strong wall reduction ability, which can significantly improve the performance, dimensional accuracy and surface quality of raw materials. The pass reduction rate of cold drawing is lower than that of cold rolling, but the equipment is simpler, the tool cost is less, the production is flexible, and the shape and specification range of the product is also larger. Therefore, it is necessary to reasonably use cold rolling and cold drawing methods on site. In recent years, cold tension reduction, cold processing of welded pipes, and cold drawing of super-long pipes can increase the output of the unit, expand the range of varieties and specifications, improve the quality of welds, and provide suitable pipe materials for cold rolling and cold drawing. In addition, warm processing has been paid more attention in recent years, usually induction heating to 200-400 ° C, to improve the plasticity of the tube blank; the maximum elongation of warm rolling is about 2-3 times that of cold rolling, and the expansion and contraction of the broken blade in warm drawing rate can be increased by 30%. It is also possible to make some metals with low plasticity and high strength to be finished.
Although the specification range, dimensional accuracy, surface quality and microstructure properties of cold-worked seamless pipes are superior to those of hot-rolled pipes, there are four problems in their production: many cycles, long production cycles, large metal consumption, and complex intermediate processing. . Due to their different materials, technical conditions and specifications, various seamless pipes have different production process and process systems, but in general they are composed of the following main processes:
1) Pre-treatment of cold working, including preparation of seamless pipe sizes, shape, microstructure and surface state;
2) Cold working including cold drawing, cold rolling and spinning, etc.;
3) Finishing of finished products, including heat treatment, cutting, straightening and inspection of finished products.
Advantages of seamless pipe cold processing:
1) The forming speed is fast, the output is high, and the coating will not be damaged. It can be made into a variety of cross-section methods to meet the needs of the environment.
2) Cold rolling can cause a large plastic deformation of the steel, thereby increasing the yield point of the steel.
Disadvantages of cold processing of seamless pipes:
1) Although there is no hot plastic shrinkage during the forming process, there are still residual stresses in the section, which will definitely affect the overall and somewhat reluctant properties of the steel;
2) The style of cold-rolled section steel is generally an open section, which makes the rigidity of the free change of the section low. It is easy to change when it is bent, and it is easy to bend and twist when it is compressed, and the torsion resistance is poor.
3) The wall thickness of the cold-rolled formed steel is small, and there is no thickening at the corner of the plate connection, so the ability to withstand certain concentrated loads is weak.
Compared with hot rolling, cold working has the following advantages:
1) It can produce large-diameter thin-walled pipes;
2) The geometrical dimension of the seamless pipe has high precision;
3) High surface finish;
4) It is helpful for grain refinement, and with the corresponding heat treatment method, higher comprehensive mechanical properties can be obtained;
5) It can produce various special shapes and cross-sections and some materials with narrow thermal processing temperature range, low high temperature toughness and good room temperature plasticity.
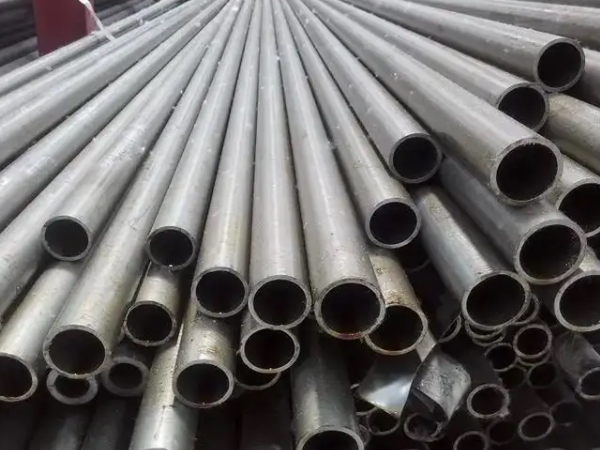
The outstanding advantage of cold rolling is its strong wall reduction ability, which can significantly improve the performance, dimensional accuracy and surface quality of raw materials. The pass reduction rate of cold drawing is lower than that of cold rolling, but the equipment is simpler, the tool cost is less, the production is flexible, and the shape and specification range of the product is also larger. Therefore, it is necessary to reasonably use cold rolling and cold drawing methods on site. In recent years, cold tension reduction, cold processing of welded pipes, and cold drawing of super-long pipes can increase the output of the unit, expand the range of varieties and specifications, improve the quality of welds, and provide suitable pipe materials for cold rolling and cold drawing. In addition, warm processing has been paid more attention in recent years, usually induction heating to 200-400 ° C, to improve the plasticity of the tube blank; the maximum elongation of warm rolling is about 2-3 times that of cold rolling, and the expansion and contraction of the broken blade in warm drawing rate can be increased by 30%. It is also possible to make some metals with low plasticity and high strength to be finished.
Although the specification range, dimensional accuracy, surface quality and microstructure properties of cold-worked seamless pipes are superior to those of hot-rolled pipes, there are four problems in their production: many cycles, long production cycles, large metal consumption, and complex intermediate processing. . Due to their different materials, technical conditions and specifications, various seamless pipes have different production process and process systems, but in general they are composed of the following main processes:
1) Pre-treatment of cold working, including preparation of seamless pipe sizes, shape, microstructure and surface state;
2) Cold working including cold drawing, cold rolling and spinning, etc.;
3) Finishing of finished products, including heat treatment, cutting, straightening and inspection of finished products.
Advantages of seamless pipe cold processing:
1) The forming speed is fast, the output is high, and the coating will not be damaged. It can be made into a variety of cross-section methods to meet the needs of the environment.
2) Cold rolling can cause a large plastic deformation of the steel, thereby increasing the yield point of the steel.
Disadvantages of cold processing of seamless pipes:
1) Although there is no hot plastic shrinkage during the forming process, there are still residual stresses in the section, which will definitely affect the overall and somewhat reluctant properties of the steel;
2) The style of cold-rolled section steel is generally an open section, which makes the rigidity of the free change of the section low. It is easy to change when it is bent, and it is easy to bend and twist when it is compressed, and the torsion resistance is poor.
3) The wall thickness of the cold-rolled formed steel is small, and there is no thickening at the corner of the plate connection, so the ability to withstand certain concentrated loads is weak.