The medium used for quenching and cooling of seamless steel pipes is called quenching cooling medium (or quenching medium). The ideal quenching medium should have the condition that the steel can be quenched into martensite without causing too much quenching stress.
The commonly used quenching media for quenching and cooling of seamless pipes are water, aqueous solution, mineral oil, molten salt, molten alkali, etc.
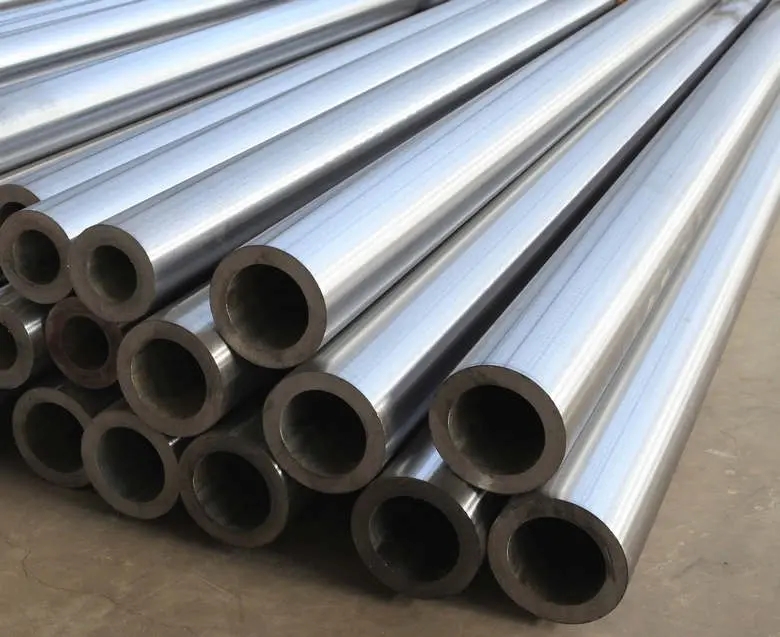
1.Water
Water is a quenching medium with strong cooling capacity. Wide source, low price, stable ingredients and not easy to deteriorate.The disadvantage is that when the C curve is around 500°C, to 600°C, the water is in the steam film stage, and the cooling is not fast enough, which will form a "soft spot"In the martensitic transformation temperature region (300-100℃), the water is in the boiling stage, and the cooling is too fast, which is easy to make the martensite transformation speed too fast and generate great internal stress, resulting in deformation or even cracking of the workpiece.When the water temperature rises, the water contains more gas or insoluble impurities (such as oil, soap, mud, etc.) are mixed in the water, which will significantly reduce its cooling capacity. Therefore, water is suitable for quenching and cooling of steel with small section size and simple shape.
2.Brine and alkaline water
Add an appropriate amount of salt and alkali to the water, after the high-temperature steel is immersed in the cooling medium, the crystals of salt and alkali are precipitated in the steam film stage, the steam film is destroyed, and the oxide scale on the surface of the steel is also destroyed, so that the medium is rapidly cooled in the high-temperature area.In general, the concentration of brine is 10%, and the concentration of caustic soda aqueous solution is 10% to 15%. It can be used as a quenching medium for carbon steel and low-alloy structural steel workpieces. The operating temperature should not exceed 60 °C. After quenching, it should be cleaned and rust-proofed in time.
3.Oil
The cooling medium generally uses mineral oil (mineral oil). Such as engine oil, transformer oil and diesel oil.The new quenching oils currently used mainly include high-speed quenching oil, bright quenching oil and vacuum quenching oil.
High-speed quenching oil is a quenching oil whose cooling rate is increased in a high temperature area. There are two basic ways to obtain high-speed quenching oil. One is to select mineral oils of different types and different viscosities, mix them with each other in an appropriate ratio, and improve the cooling capacity in the high temperature area by increasing the characteristic temperature.The other is to add additives to ordinary quenching oil to form dust-like floats in the oil.Production practice shows that the cooling rate of high-speed quenching oil in the supercooled austenite unstable zone is significantly higher than that of ordinary quenching oil, and the cooling rate of high-speed quenching oil is close to that of ordinary quenching oil in the low-temperature martensitic transformation zone.In this way, high hardenability and hardenability can be obtained, and the deformation is greatly reduced, which is suitable for the quenching of alloy steel workpieces with complex shapes.
Bright quenching oil can keep the workpiece bright surface after quenching. By adding polymer additives of different properties to mineral oil, bright quenching oils with different cooling rates can be obtained.The main component of these additives is the brightener, whose role is to suspend the aging products that are insoluble in the oil, preventing accumulation and precipitation on the workpiece. In addition, bright quenching oil additives also contain antioxidants, surfactants and refrigerants.
Vacuum quenching oil is a cooling medium for vacuum heat treatment quenching. Vacuum quenching oil must have low saturated vapor pressure, high and stable cooling capacity, good brightness and thermal stability, otherwise it will affect the effect of vacuum heat treatment.
The commonly used quenching media for quenching and cooling of seamless pipes are water, aqueous solution, mineral oil, molten salt, molten alkali, etc.
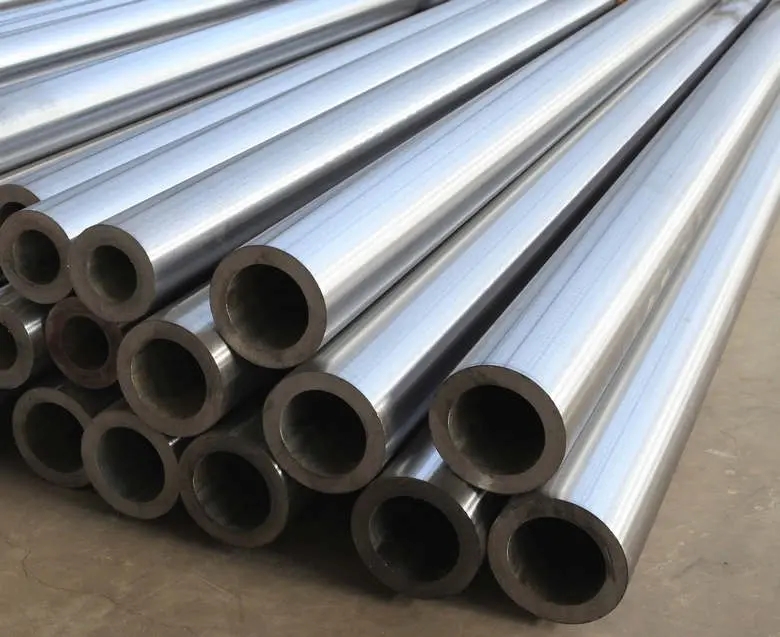
1.Water
Water is a quenching medium with strong cooling capacity. Wide source, low price, stable ingredients and not easy to deteriorate.The disadvantage is that when the C curve is around 500°C, to 600°C, the water is in the steam film stage, and the cooling is not fast enough, which will form a "soft spot"In the martensitic transformation temperature region (300-100℃), the water is in the boiling stage, and the cooling is too fast, which is easy to make the martensite transformation speed too fast and generate great internal stress, resulting in deformation or even cracking of the workpiece.When the water temperature rises, the water contains more gas or insoluble impurities (such as oil, soap, mud, etc.) are mixed in the water, which will significantly reduce its cooling capacity. Therefore, water is suitable for quenching and cooling of steel with small section size and simple shape.
2.Brine and alkaline water
Add an appropriate amount of salt and alkali to the water, after the high-temperature steel is immersed in the cooling medium, the crystals of salt and alkali are precipitated in the steam film stage, the steam film is destroyed, and the oxide scale on the surface of the steel is also destroyed, so that the medium is rapidly cooled in the high-temperature area.In general, the concentration of brine is 10%, and the concentration of caustic soda aqueous solution is 10% to 15%. It can be used as a quenching medium for carbon steel and low-alloy structural steel workpieces. The operating temperature should not exceed 60 °C. After quenching, it should be cleaned and rust-proofed in time.
3.Oil
The cooling medium generally uses mineral oil (mineral oil). Such as engine oil, transformer oil and diesel oil.The new quenching oils currently used mainly include high-speed quenching oil, bright quenching oil and vacuum quenching oil.
High-speed quenching oil is a quenching oil whose cooling rate is increased in a high temperature area. There are two basic ways to obtain high-speed quenching oil. One is to select mineral oils of different types and different viscosities, mix them with each other in an appropriate ratio, and improve the cooling capacity in the high temperature area by increasing the characteristic temperature.The other is to add additives to ordinary quenching oil to form dust-like floats in the oil.Production practice shows that the cooling rate of high-speed quenching oil in the supercooled austenite unstable zone is significantly higher than that of ordinary quenching oil, and the cooling rate of high-speed quenching oil is close to that of ordinary quenching oil in the low-temperature martensitic transformation zone.In this way, high hardenability and hardenability can be obtained, and the deformation is greatly reduced, which is suitable for the quenching of alloy steel workpieces with complex shapes.
Bright quenching oil can keep the workpiece bright surface after quenching. By adding polymer additives of different properties to mineral oil, bright quenching oils with different cooling rates can be obtained.The main component of these additives is the brightener, whose role is to suspend the aging products that are insoluble in the oil, preventing accumulation and precipitation on the workpiece. In addition, bright quenching oil additives also contain antioxidants, surfactants and refrigerants.
Vacuum quenching oil is a cooling medium for vacuum heat treatment quenching. Vacuum quenching oil must have low saturated vapor pressure, high and stable cooling capacity, good brightness and thermal stability, otherwise it will affect the effect of vacuum heat treatment.