The seamless pipe means a hollow section and is widely used as a pipeline for transporting fluids, such as pipelines for transporting oil, natural gas, gas, water and certain solid materials. Compared with ordinary seamless pipes, stainless steel seamless pipes have higher corrosion resistance, and the finish is better than ordinary seamless steel pipes. But this does not mean that stainless steel seamless pipes will not be corroded.
1. Stress corrosion cracking (SCC): Stress corrosion cracking has a brittle fracture morphology, but it may also occur in materials with high thermal properties. The necessary conditions for stress corrosion cracking to occur are the presence of tensile stress (whether residual stress or applied stress, or both) and a specific corrosive medium. The formation and expansion of the grooves are roughly perpendicular to the direction of the tensile stress. The stress value that causes stress corrosion cracking is much smaller than the stress value required to fracture the material in the absence of corrosive media. At the microscopic level, when stress corrosion cracking propagates to its depth, the material breaks as a normal crack (in ductile materials, usually through the aggregation of fiber defects). Thus, a cross-section of a part that has failed due to stress corrosion cracking will contain characteristic areas of stress corrosion cracking as well as "dimple" regions associated with the aggregation of microdefects.
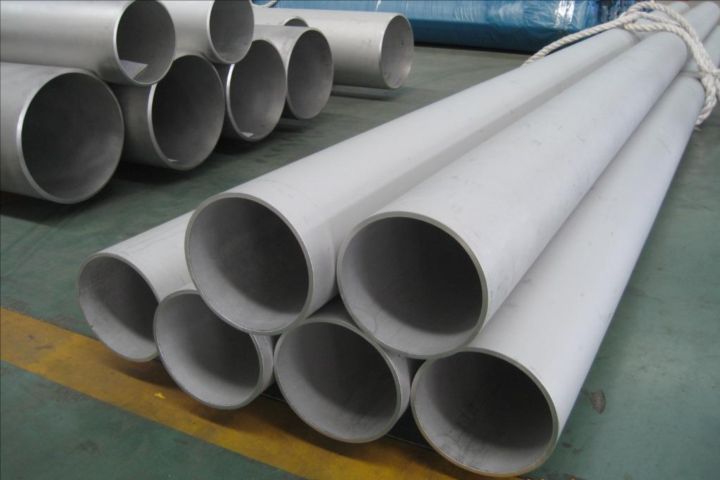
2. Pitting corrosion: Pitting corrosion refers to a high degree of localized corrosion that occurs mostly on the surface of metal materials without corrosion or is slightly corroded.The size of common pits is less than 1.00mm, and the depth is often larger than the surface aperture. Light pits have shallow pits, and even perforations are formed in serious cases.
3. Intergranular corrosion: Crystallization is a favorable area for the segregation of various solute elements in the steel or the precipitation of metal compounds (into carbon compounds). Therefore, in some corrosive media, grain boundaries may be etched first. This type of corrosion is called intergranular corrosion, and most metals and alloys may exhibit intergranular corrosion in certain corrosive media.
4. Crevice corrosion: It is a form of localized corrosion that may occur in crevices where the solution is stagnant or in shielded surfaces. Such gaps can be formed at metal-to-metal or metal-to-nonmetallic junctions, for example, where rivets, bolts, gaskets, valve seats, loose surface deposits, and desired contact with marine organisms are formed.
5. General corrosion: is a term used to describe the corrosion phenomenon that occurs in a relatively uniform manner on the entire surface of the alloy. When general corrosion occurs, the material gradually becomes thinner due to corrosion, and even the material fails due to corrosion. Stainless steel pipes may exhibit general corrosion in strong acids and alkalis. This corrosion can usually be predicted by a simple immersion test.
1. Stress corrosion cracking (SCC): Stress corrosion cracking has a brittle fracture morphology, but it may also occur in materials with high thermal properties. The necessary conditions for stress corrosion cracking to occur are the presence of tensile stress (whether residual stress or applied stress, or both) and a specific corrosive medium. The formation and expansion of the grooves are roughly perpendicular to the direction of the tensile stress. The stress value that causes stress corrosion cracking is much smaller than the stress value required to fracture the material in the absence of corrosive media. At the microscopic level, when stress corrosion cracking propagates to its depth, the material breaks as a normal crack (in ductile materials, usually through the aggregation of fiber defects). Thus, a cross-section of a part that has failed due to stress corrosion cracking will contain characteristic areas of stress corrosion cracking as well as "dimple" regions associated with the aggregation of microdefects.
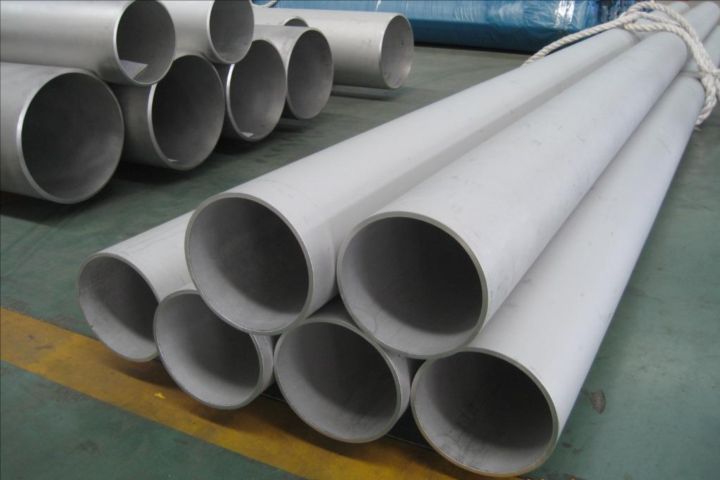
2. Pitting corrosion: Pitting corrosion refers to a high degree of localized corrosion that occurs mostly on the surface of metal materials without corrosion or is slightly corroded.The size of common pits is less than 1.00mm, and the depth is often larger than the surface aperture. Light pits have shallow pits, and even perforations are formed in serious cases.
3. Intergranular corrosion: Crystallization is a favorable area for the segregation of various solute elements in the steel or the precipitation of metal compounds (into carbon compounds). Therefore, in some corrosive media, grain boundaries may be etched first. This type of corrosion is called intergranular corrosion, and most metals and alloys may exhibit intergranular corrosion in certain corrosive media.
4. Crevice corrosion: It is a form of localized corrosion that may occur in crevices where the solution is stagnant or in shielded surfaces. Such gaps can be formed at metal-to-metal or metal-to-nonmetallic junctions, for example, where rivets, bolts, gaskets, valve seats, loose surface deposits, and desired contact with marine organisms are formed.
5. General corrosion: is a term used to describe the corrosion phenomenon that occurs in a relatively uniform manner on the entire surface of the alloy. When general corrosion occurs, the material gradually becomes thinner due to corrosion, and even the material fails due to corrosion. Stainless steel pipes may exhibit general corrosion in strong acids and alkalis. This corrosion can usually be predicted by a simple immersion test.