In the process of manufacturing seamless pipes, it is generally necessary to cut the seamless pipes to a specified size. Under the existing technical conditions, the cutting of seamless pipes generally uses a sawing machine or flame cutting.Seamless pipe means a pipe with a hollow section and no joints in the middle, which is widely used in various industries such as petrochemical industry.
saw cutting
The main components of the sawing machine are the bottom seat; the bed, the column; the saw beam and the transmission mechanism; the guiding device; the workpiece clamping; the tensioning device; the feeding frame; the hydraulic transmission system; the electrical control system; the lubrication and cooling system;
1.Base
The base is a box-shaped structure made of welded steel plates. The bed and uprights are fixed on it. The inner cavity of the base has a large space. The hydraulic oil tank is equipped with hydraulic pump station and hydraulic pipeline in the cavity. The right side is the cooling cutting fluid tank and water pump.
2.Folding bed
The bed is made of cast iron and fixed on the base. The column is composed of a large and small column. The large column is used as a guide rail for the saw frame to support the up and down movement of the saw beam and ensure accurate guidance.The small cylinder plays an auxiliary role to ensure the normal cutting of the saw blade. In the middle is a clamping vise and a manual feeding mechanism, and the front of the vise is connected with a worktable for accepting finished parts.The clamping device on the left is the clamping screw that passes through the inner hole of the hydraulic clamping cylinder rod, and the left jaw moves left and right by turning the handwheel or pressing the button.
3.Features
Hydraulic control of sawing speed, infinitely adjustable. Cylinder control, stable feeding. Bunching devices can be added as needed. There are semi-automatic and CNC-automatic options available as required. Angled miter saws available.
4.Advantages and disadvantages
The sawing machine has a long history of cutting, has the most equipment, and has the widest application range, but the sawing machine can only be used for simple cutting, with low efficiency and high scrap rate.
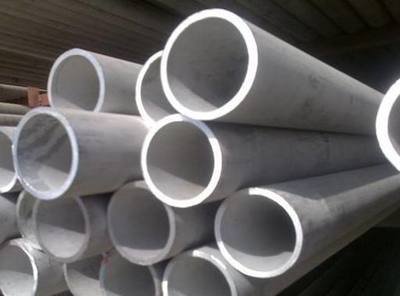
Flame cutting
Flame cutting is to use a preheating flame to heat the cut pipe to the ignition point, and then spray a high-purity, high-speed cutting oxygen flow to the pipe, which causes the pipe to burn violently.At the same time, the combustion products (mainly iron oxide) are blown away by the momentum of the high-speed oxygen flow to form a slit, so as to achieve the purpose of cutting.
1.Torch cutting
The torch is also called the flame gun. The gas used is different, and the structure is also different. The most commonly used is an oxygen-acetylene flame gun. The acetylene pressure is 0.01~0.12MPa, and the oxygen pressure is 0.50~1.0MPa. The two gases are mixed and burned in the flame gun through their respective passages, and the size and nature of the sprayed flame can be adjusted by manually holding the flame gun for cutting.This method is usually used for the cutting of billets and slabs after rolling or for supplementary cutting to remove defects after straightening of steel.
2.Cutting machine cutting
It consists of a cutting torch with a working principle similar to a flame gun, a sizing mechanism and a slit cleaning device. The sizing mechanism includes mechanical, pulsed and photoelectric, which can realize automatic sizing. The kerf cleaning device is specially designed to clean the residue adhering to the kerf so as not to affect the surface quality of the steel during rolling. The cleaning method is to use a scraper to scrape off the sticky slag, and a set of high-speed rotating sharp-angle hammers to knock out the sticky slag and burrs. Flame cutting machines are mostly used as online cutting equipment for billets after continuous casting machines, cutting thick-walled seamless pipes
3.Cutting process
(1) Check whether the workplace meets the safety requirements, whether the cutting torch, oxygen bottle, acetylene bottle (or acetylene generator and flashback preventer) rubber tube, pressure gauge, etc. are normal, and connect the gas cutting equipment according to the operating procedures.
(2)Before cutting, first flatten the steel pipe, and leave a certain gap under the workpiece to facilitate the blowing of iron oxide slag. When cutting, in order to prevent the operator from being burned by the splashing iron oxide slag, a baffle can be added if necessary.
(3)Check the air lines by igniting the flame and adjusting the preheat flame appropriately. Then open the cutting oxygen valve and observe the shape of the cutting oxygen flow (ie the wind line). The wind line should be a straight, clear cylinder and have an appropriate length. In this way, the surface of the workpiece cut can be smooth and clean, and the width and width are consistent. If the air line is irregular, all valves should be closed, and the inner surface of the cutting nozzle should be trimmed with a needle or other tools to make it smooth.
(4)Adjust the oxygen to the desired pressure. For ejector torches, check the torch for ejector capability. The way to check is to first unplug the acetylene intake hose and bend it, then open the acetylene valve and preheat oxygen valve. At this time, put your finger on the acetylene gas inlet pipe joint of the cutting torch. If the finger feels suction and can be adsorbed on the acetylene gas inlet pipe joint, it means that the cutting torch has the ability to shoot and suck and can be used;On the contrary, it means that the cutting torch is abnormal and cannot be used, and should be checked and repaired.
4.Advantages and disadvantages
The advantage of flame cutting is that the cost is low, a machining process is added when the cutting quality is high, and the market has a large amount.Secondly, the processing speed is slow, and it is only suitable for rough machining.
saw cutting
The main components of the sawing machine are the bottom seat; the bed, the column; the saw beam and the transmission mechanism; the guiding device; the workpiece clamping; the tensioning device; the feeding frame; the hydraulic transmission system; the electrical control system; the lubrication and cooling system;
1.Base
The base is a box-shaped structure made of welded steel plates. The bed and uprights are fixed on it. The inner cavity of the base has a large space. The hydraulic oil tank is equipped with hydraulic pump station and hydraulic pipeline in the cavity. The right side is the cooling cutting fluid tank and water pump.
2.Folding bed
The bed is made of cast iron and fixed on the base. The column is composed of a large and small column. The large column is used as a guide rail for the saw frame to support the up and down movement of the saw beam and ensure accurate guidance.The small cylinder plays an auxiliary role to ensure the normal cutting of the saw blade. In the middle is a clamping vise and a manual feeding mechanism, and the front of the vise is connected with a worktable for accepting finished parts.The clamping device on the left is the clamping screw that passes through the inner hole of the hydraulic clamping cylinder rod, and the left jaw moves left and right by turning the handwheel or pressing the button.
3.Features
Hydraulic control of sawing speed, infinitely adjustable. Cylinder control, stable feeding. Bunching devices can be added as needed. There are semi-automatic and CNC-automatic options available as required. Angled miter saws available.
4.Advantages and disadvantages
The sawing machine has a long history of cutting, has the most equipment, and has the widest application range, but the sawing machine can only be used for simple cutting, with low efficiency and high scrap rate.
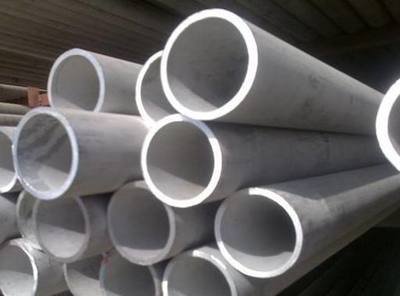
Flame cutting
Flame cutting is to use a preheating flame to heat the cut pipe to the ignition point, and then spray a high-purity, high-speed cutting oxygen flow to the pipe, which causes the pipe to burn violently.At the same time, the combustion products (mainly iron oxide) are blown away by the momentum of the high-speed oxygen flow to form a slit, so as to achieve the purpose of cutting.
1.Torch cutting
The torch is also called the flame gun. The gas used is different, and the structure is also different. The most commonly used is an oxygen-acetylene flame gun. The acetylene pressure is 0.01~0.12MPa, and the oxygen pressure is 0.50~1.0MPa. The two gases are mixed and burned in the flame gun through their respective passages, and the size and nature of the sprayed flame can be adjusted by manually holding the flame gun for cutting.This method is usually used for the cutting of billets and slabs after rolling or for supplementary cutting to remove defects after straightening of steel.
2.Cutting machine cutting
It consists of a cutting torch with a working principle similar to a flame gun, a sizing mechanism and a slit cleaning device. The sizing mechanism includes mechanical, pulsed and photoelectric, which can realize automatic sizing. The kerf cleaning device is specially designed to clean the residue adhering to the kerf so as not to affect the surface quality of the steel during rolling. The cleaning method is to use a scraper to scrape off the sticky slag, and a set of high-speed rotating sharp-angle hammers to knock out the sticky slag and burrs. Flame cutting machines are mostly used as online cutting equipment for billets after continuous casting machines, cutting thick-walled seamless pipes
3.Cutting process
(1) Check whether the workplace meets the safety requirements, whether the cutting torch, oxygen bottle, acetylene bottle (or acetylene generator and flashback preventer) rubber tube, pressure gauge, etc. are normal, and connect the gas cutting equipment according to the operating procedures.
(2)Before cutting, first flatten the steel pipe, and leave a certain gap under the workpiece to facilitate the blowing of iron oxide slag. When cutting, in order to prevent the operator from being burned by the splashing iron oxide slag, a baffle can be added if necessary.
(3)Check the air lines by igniting the flame and adjusting the preheat flame appropriately. Then open the cutting oxygen valve and observe the shape of the cutting oxygen flow (ie the wind line). The wind line should be a straight, clear cylinder and have an appropriate length. In this way, the surface of the workpiece cut can be smooth and clean, and the width and width are consistent. If the air line is irregular, all valves should be closed, and the inner surface of the cutting nozzle should be trimmed with a needle or other tools to make it smooth.
(4)Adjust the oxygen to the desired pressure. For ejector torches, check the torch for ejector capability. The way to check is to first unplug the acetylene intake hose and bend it, then open the acetylene valve and preheat oxygen valve. At this time, put your finger on the acetylene gas inlet pipe joint of the cutting torch. If the finger feels suction and can be adsorbed on the acetylene gas inlet pipe joint, it means that the cutting torch has the ability to shoot and suck and can be used;On the contrary, it means that the cutting torch is abnormal and cannot be used, and should be checked and repaired.
4.Advantages and disadvantages
The advantage of flame cutting is that the cost is low, a machining process is added when the cutting quality is high, and the market has a large amount.Secondly, the processing speed is slow, and it is only suitable for rough machining.
Previous:Prevent cracking of seamless tubes