The appearance defects of the welded pipe include long knife bend, wavy bend, gnawing edge, scab, scratch, embossing, uneven head and tail, tower-shaped roll, loose roll, surface oxide skin, etc.
1. Long knife bend
This is the phenomenon of bending to one side on the horizontal surface along the length direction of the hot-rolled strip, or crescent bend, which is caused by the uneven deformation along the width direction of the two sides during the cold-rolling of the hot-rolled strip. The long knife bent welded pipe is very easy to cause lap welding during production and processing, and the direction is deviated or even rotated during forming.
2. Wavy bend
This is the case where the edge part of the hot-rolled strip is continuously bent vertically; it is caused by the uneven deformation of the center and edge along the width direction during the cold-rolling of the hot-rolled strip. The wavy bends cause serious lap welding during forming welding, which cannot be processed, so it is not allowed to appear.
3. Gnaw the edge
This is the appearance of zigzag unevenness on the edge of the hot-rolled strip, which usually occurs on the longitudinally cut hot-rolled strip. The reason is that the disc scissors of the slitting machine are broken, blunt or notched. The welding quality and reliability of hot-rolled strip steel with severe edge gnawing will be endangered during electric welding, because some cracks and gaps will appear.
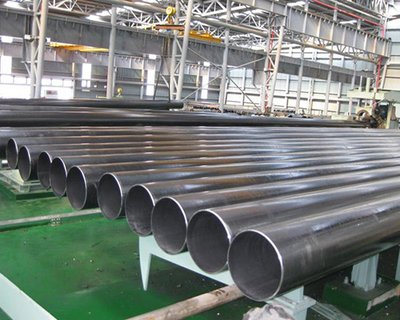
4. Scabs, imprints, scratches, uneven head and tail
Scabbing and embossing are caused by dirt sticking to the roll during cold rolling. Scratches are caused by the scraping of the hot-rolled strip by dirt on the roller table or on the floor during driving, especially when the cold-rolled strip is not oiled. The uneven head and tail is caused by the fact that the hot-rolled strip steel has not been unwound directly after cutting the head and tail after cold rolling. This defect causes the appearance quality of the welded pipe to be unqualified, and must be removed or judged to be scrapped, reducing the yield and compliance rate of the welded pipe.
5. Tower roll
Tower-shaped coil ten hot-rolled steel strip from the inner circle to the outside in a tower-shaped coil to obtain hot-rolled steel strip coils, generally not allowed to exceed 50mm.
6. Loose rolls
Slightly loose rolls can be used after sorting, and serious loose rolls cannot be used because they cannot be sorted out, so they must be cut to a more scattered part, which increases the consumption of metal materials and reduces the yield.
Causes: The packaging is not strong and does not meet the packaging requirements; the operation is not good during the loading and unloading process;
7. Surface air oxide skin
Oxidized scale entering the welding zone between the edges of the hot-rolled strip will cause casting defects. In addition, the compound flakes on the surface of the hot-rolled strip enter the forming opportunity to accelerate the damage of the forming roll. It is necessary to deal with the descaling of the hot-rolled strip with serious scale.
1. Long knife bend
This is the phenomenon of bending to one side on the horizontal surface along the length direction of the hot-rolled strip, or crescent bend, which is caused by the uneven deformation along the width direction of the two sides during the cold-rolling of the hot-rolled strip. The long knife bent welded pipe is very easy to cause lap welding during production and processing, and the direction is deviated or even rotated during forming.
2. Wavy bend
This is the case where the edge part of the hot-rolled strip is continuously bent vertically; it is caused by the uneven deformation of the center and edge along the width direction during the cold-rolling of the hot-rolled strip. The wavy bends cause serious lap welding during forming welding, which cannot be processed, so it is not allowed to appear.
3. Gnaw the edge
This is the appearance of zigzag unevenness on the edge of the hot-rolled strip, which usually occurs on the longitudinally cut hot-rolled strip. The reason is that the disc scissors of the slitting machine are broken, blunt or notched. The welding quality and reliability of hot-rolled strip steel with severe edge gnawing will be endangered during electric welding, because some cracks and gaps will appear.
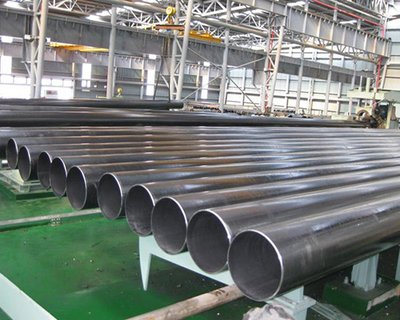
4. Scabs, imprints, scratches, uneven head and tail
Scabbing and embossing are caused by dirt sticking to the roll during cold rolling. Scratches are caused by the scraping of the hot-rolled strip by dirt on the roller table or on the floor during driving, especially when the cold-rolled strip is not oiled. The uneven head and tail is caused by the fact that the hot-rolled strip steel has not been unwound directly after cutting the head and tail after cold rolling. This defect causes the appearance quality of the welded pipe to be unqualified, and must be removed or judged to be scrapped, reducing the yield and compliance rate of the welded pipe.
5. Tower roll
Tower-shaped coil ten hot-rolled steel strip from the inner circle to the outside in a tower-shaped coil to obtain hot-rolled steel strip coils, generally not allowed to exceed 50mm.
6. Loose rolls
Slightly loose rolls can be used after sorting, and serious loose rolls cannot be used because they cannot be sorted out, so they must be cut to a more scattered part, which increases the consumption of metal materials and reduces the yield.
Causes: The packaging is not strong and does not meet the packaging requirements; the operation is not good during the loading and unloading process;
7. Surface air oxide skin
Oxidized scale entering the welding zone between the edges of the hot-rolled strip will cause casting defects. In addition, the compound flakes on the surface of the hot-rolled strip enter the forming opportunity to accelerate the damage of the forming roll. It is necessary to deal with the descaling of the hot-rolled strip with serious scale.