Non-destructive testing of steel pipes is an inspection technology that detects internal or external defects without damaging the steel pipes. In recent years, it has been widely used by major steel pipe manufacturers. The non-destructive testing technologies used in the production of black carbon steel pipes mainly include ultrasonic flaw detection, magnetic flaw detection, eddy current flaw detection and penetrant flaw detection. Various flaw detection methods have their own scope of use.
What is black carbon steel pipe?
Carbon steel pipes are made of steel ingots or solid round steel perforated into capillary tubes, which are then hot rolled, cold rolled or cold drawn. The color of carbon steel is mainly gray-black, which is due to the high carbon content in its composition. This is also the so-called "black carbon steel pipe".
What is eddy current testing?
Eddy current testing refers to a non-destructive testing method that uses the principle of electromagnetic induction to non-destructively uate certain properties of conductive materials and their workpieces or discover defects by measuring changes in induced eddy currents in the inspected workpiece. In industrial production, eddy current testing is one of the main means to control the quality of various metal materials and a few non-metallic conductive materials such as graphite and carbon fiber composite materials and their products. It occupies an important position in the field of non-destructive testing technology.
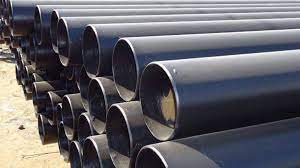
Principles of eddy current testing of black carbon steel pipes
Eddy current testing is a non-destructive testing method based on the principle of electromagnetic induction. It is suitable for conductive materials. When a conductor is placed in an alternating magnetic field, an induced current exists in the conductor, that is, an eddy current is generated. Due to changes in various factors of the conductor itself (such as conductivity, magnetic permeability, shape, size and defects, etc.), changes in eddy currents will occur. The detection method that uses this phenomenon to determine the properties and status of the conductor is called eddy current testing.
Advantages of eddy current testing:
① The detection coil does not need to contact the workpiece, nor does it require a coupling agent. The detection of tubes, rods, and wires is easy to achieve high-speed, high-efficiency automated detection; it can also be used for detection at high temperatures, or for narrow areas of the workpiece and deep hole walls. Wait until the probe can reach a far-reaching place for detection.
② It has high detection sensitivity for defects on the surface and near the surface of the workpiece.
③ Use different signal processing circuits to suppress interference and extract different eddy current influencing factors. Eddy current detection can be used for conductivity measurement, film thickness measurement and metal sheet thickness measurement.
④ Since the detection signal is an electrical signal, the detection results can be digitally processed, then stored, reproduced, and processed and compared.
Limitations of eddy current testing:
① Only suitable for detecting conductive metal materials or non-metallic materials that can induce eddy currents.
② Due to the influence of eddy current penetration effect, it is only suitable for inspecting metal surface and near-surface defects, and cannot inspect deep internal defects of metal materials.
③ There are many factors affecting the eddy current effect, and it is difficult to characterize and quantify defects.
④ Different detection coils have their own shortcomings when inspecting different workpieces.
What is black carbon steel pipe?
Carbon steel pipes are made of steel ingots or solid round steel perforated into capillary tubes, which are then hot rolled, cold rolled or cold drawn. The color of carbon steel is mainly gray-black, which is due to the high carbon content in its composition. This is also the so-called "black carbon steel pipe".
What is eddy current testing?
Eddy current testing refers to a non-destructive testing method that uses the principle of electromagnetic induction to non-destructively uate certain properties of conductive materials and their workpieces or discover defects by measuring changes in induced eddy currents in the inspected workpiece. In industrial production, eddy current testing is one of the main means to control the quality of various metal materials and a few non-metallic conductive materials such as graphite and carbon fiber composite materials and their products. It occupies an important position in the field of non-destructive testing technology.
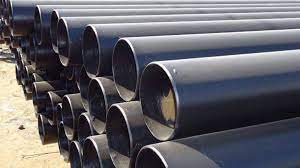
Principles of eddy current testing of black carbon steel pipes
Eddy current testing is a non-destructive testing method based on the principle of electromagnetic induction. It is suitable for conductive materials. When a conductor is placed in an alternating magnetic field, an induced current exists in the conductor, that is, an eddy current is generated. Due to changes in various factors of the conductor itself (such as conductivity, magnetic permeability, shape, size and defects, etc.), changes in eddy currents will occur. The detection method that uses this phenomenon to determine the properties and status of the conductor is called eddy current testing.
Advantages of eddy current testing:
① The detection coil does not need to contact the workpiece, nor does it require a coupling agent. The detection of tubes, rods, and wires is easy to achieve high-speed, high-efficiency automated detection; it can also be used for detection at high temperatures, or for narrow areas of the workpiece and deep hole walls. Wait until the probe can reach a far-reaching place for detection.
② It has high detection sensitivity for defects on the surface and near the surface of the workpiece.
③ Use different signal processing circuits to suppress interference and extract different eddy current influencing factors. Eddy current detection can be used for conductivity measurement, film thickness measurement and metal sheet thickness measurement.
④ Since the detection signal is an electrical signal, the detection results can be digitally processed, then stored, reproduced, and processed and compared.
Limitations of eddy current testing:
① Only suitable for detecting conductive metal materials or non-metallic materials that can induce eddy currents.
② Due to the influence of eddy current penetration effect, it is only suitable for inspecting metal surface and near-surface defects, and cannot inspect deep internal defects of metal materials.
③ There are many factors affecting the eddy current effect, and it is difficult to characterize and quantify defects.
④ Different detection coils have their own shortcomings when inspecting different workpieces.
Previous:Solutions for ERW pipe deburring