Electric resistance welded (ERW) galvanized pipe is used in construction, piping systems, energy transmission and other fields due to its versatility, durability and corrosion resistance. The following is a brief introduction to ERW gi pipe.
The main method used for surface galvanizing of ERW is hot dip galvanizing.
Hot-dip galvanizing was developed from the older hot-dip method. It has a history of 170 years since France applied hot-dip galvanizing to industry in 1836. However, the hot-dip galvanizing industry has developed on a large scale in the past thirty years with the rapid development of cold-rolled strip steel.
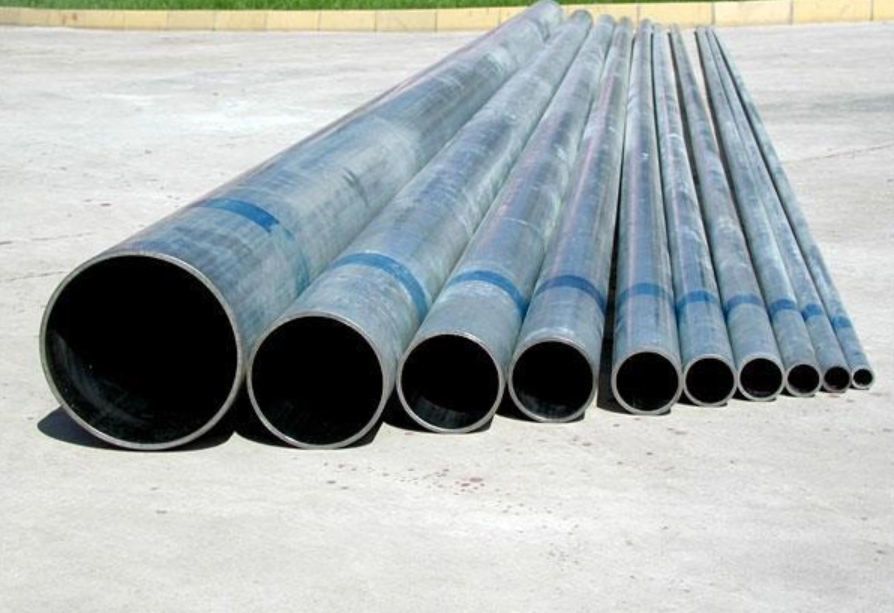
The production process of hot-dip gi steel pipe mainly includes: original pipe preparation → pre-plating treatment → hot dip plating → post-plating treatment → finished product inspection, etc. According to custom, the hot-dip galvanizing process is divided into two categories: off-line annealing and in-line annealing based on different pre-plating treatment methods.
ERW tube also has a galvanizing method called electro-galvanizing. Electro-galvanizing is also called cold galvanizing, which is a process that uses the principle of electrolysis to form a uniform, dense, and well-bonded zinc coating on the surface of the product.
3.Hot-dip galvanized vs electro-galvanized ERW pipe
Electro-galvanizing and hot-dip galvanizing can be distinguished by coating thickness, corrosion resistance, application range, physical properties and cost. The following is a detailed introduction:
In general, hot-dip galvanizing is better than electro-galvanizing in terms of corrosion resistance, corrosion resistance and mechanical properties, while electro-galvanizing is suitable for occasions where the thickness of the zinc layer is not high.
4.Advantages of galvanized ERW tubes
1.ERW steel pipe
ERW means Electric resistance weld tubing, which is a pipe production method that uses the principle of resistance heating to apply electric current at the joints of steel coils to generate heat to locally melt the metal, and then connect the two steel coil heads together.2. ERW pipe galvanizing process
Like sandblasting, pickling and phosphating, galvanizing is also a surface treatment technology for metal pipes.Galvanizing refers to the technology of coating a layer of zinc on the surface of metal, alloy or other materials for aesthetics and rust prevention. The standard electrode potential of zinc is -0.76V. For steel substrates, zinc coating is an anodic coating. It is mainly used to prevent corrosion of steel. Its protective performance is closely related to the thickness of the coating. After the zinc coating is passivated, dyed or coated with gloss protectant, its protective and decorative properties can be significantly improved.The main method used for surface galvanizing of ERW is hot dip galvanizing.
Hot-dip galvanizing was developed from the older hot-dip method. It has a history of 170 years since France applied hot-dip galvanizing to industry in 1836. However, the hot-dip galvanizing industry has developed on a large scale in the past thirty years with the rapid development of cold-rolled strip steel.
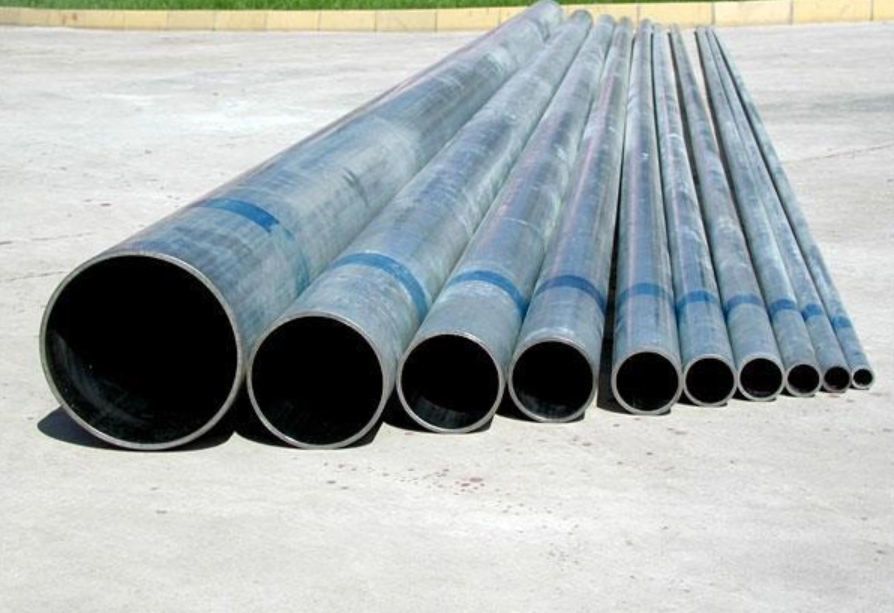
The production process of hot-dip gi steel pipe mainly includes: original pipe preparation → pre-plating treatment → hot dip plating → post-plating treatment → finished product inspection, etc. According to custom, the hot-dip galvanizing process is divided into two categories: off-line annealing and in-line annealing based on different pre-plating treatment methods.
ERW tube also has a galvanizing method called electro-galvanizing. Electro-galvanizing is also called cold galvanizing, which is a process that uses the principle of electrolysis to form a uniform, dense, and well-bonded zinc coating on the surface of the product.
3.Hot-dip galvanized vs electro-galvanized ERW pipe
Electro-galvanizing and hot-dip galvanizing can be distinguished by coating thickness, corrosion resistance, application range, physical properties and cost. The following is a detailed introduction:
(1) Coating thickness
The coating thickness of hot-dip galvanizing is larger, usually 50 to 60 microns, or even up to 600 microns; while the coating thickness of electro-galvanizing is thin, usually 5 to 15 microns.(2) Corrosion resistance
The zinc layer of hot-dip galvanizing is denser and less susceptible to corrosion by oxides and salts in the environment, so it has better corrosion resistance; electro-galvanizing has a thinner coating and is more susceptible to mechanical wear and oxide corrosion.(3) Application scope
Hot-dip galvanizing ERW tubing is suitable for steel structures, automobiles, agricultural machinery, construction and ships, etc., and performs well especially in harsh environments; electro-galvanizing is mostly used for small, delicate products, and works well in mild environments. .(4) Physical properties
The surface of hot-dip galvanized ERW tubes is rough, the zinc layer is thick, showing zinc flowers, and the appearance is bright; the surface of electro-galvanized ERW steel pipes is smooth, and the zinc layer is thin.(5) Costs are different.
Hot-dip galvanizing has a thick zinc layer, good durability, and a relatively high cost, but has a long service life, so it is more economical; electro-galvanizing has a thin zinc layer, a relatively low price, but a short service life.In general, hot-dip galvanizing is better than electro-galvanizing in terms of corrosion resistance, corrosion resistance and mechanical properties, while electro-galvanizing is suitable for occasions where the thickness of the zinc layer is not high.
4.Advantages of galvanized ERW tubes
(1)corrosion resistance and longevity
One of the primary advantages of ERW galvanized steel pipes is their exceptional corrosion resistance and longevity. The zinc coating acts as a sacrificial anode, corroding preferentially to protect the underlying steel from rust and corrosion. This extends the lifespan of the pipes, even in harsh environments where they are exposed to moisture, chemicals, and other corrosive elements. As a result, ERW galvanized pipes are often used in outdoor applications such as fencing, scaffolding, and water distribution systems.(2)Strength and durability
ERW galvanized pipes exhibit excellent structural integrity, making them suitable for high-pressure applications in industries such as oil and gas, construction, and agriculture. The electric resistance welding process produces strong, seamless joints that can withstand the rigors of heavy-duty use. Additionally, the galvanized coating provides an extra layer of protection against physical damage, such as scratches and abrasions, further enhancing the durability of the pipes. This combination of strength and durability makes ERW galvanized pipes an ideal choice for critical infrastructure projects and industrial applications.(3)cost-effectiveness
Despite their superior qualities, ERW galvanized tubes are more economical compared to other piping materials. The relatively simple manufacturing process and abundance of raw materials contribute to their affordability. Additionally, their long lifespan and low maintenance requirements result in cost savings over the lifetime of the pipes. This makes ERW galvanized pipes a cost-effective solution for projects that require reliable, long-lasting piping solutions without breaking the bank.
Previous:Storage of ERW Pipe
Next:ERW rectangular tube