In the field of oil well pipes used in oil drilling, high-frequency resistance welded casing (ERW octg casing for short) has the advantages of high dimensional accuracy, good weld toughness, high extrusion resistance, and low cost compared with seamless casing(seamless steel pipe). It has been widely used abroad and achieved good results.
Technical advantages of ERW octg casing (compared to seamless casing)
(1) High dimensional accuracy
ERW octg casing adopts a mechanical sizing process after forming, so that its dimensional accuracy (outer diameter, wall thickness, roundness, etc.) is improved compared with seamless casing, and its outer diameter deviation generally does not exceed ±0.5%. For example, the standard deviation of the wall thickness of the ф244.5 mm ERW octg casing produced by Japan's Nippon Steel Corporation is <0.10 mm, while the standard deviation of the corresponding seamless casing is 0.41 mm.
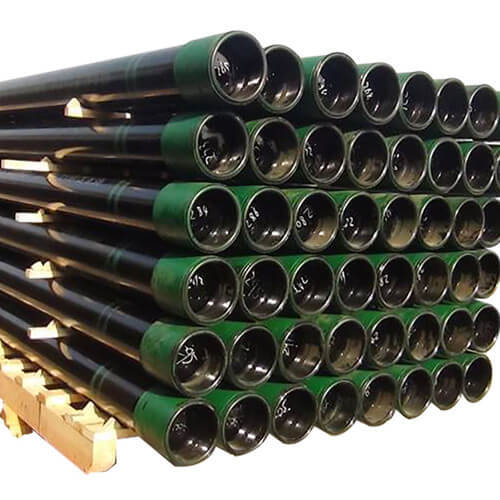
(2) The weld has good toughness
The manufacturing process of ERW octg casing can ensure a high-strength and high-toughness weld. The composition of the weld and the lower content of C, S and P in the base material make the casing more tough than seamless casing.
(3) Good anti-extrusion and anti-explosion properties
Compared with similar API seamless casings, ERW octg casings have 30% to 40% higher extrusion strength and about 50% higher explosion resistance (internal pressure).
(4) Advanced technology and good product quality control
The base material of the ERW octg casing is controlled-rolled coil plate, which is isotropic and can be 100% non-destructively inspected.
(5) Low cost
Compared with similar seamless casing, the cost of ERW octg casing is 5%~10% lower, the production efficiency is high, the degree of mechanization and automation is high, and the production energy consumption is low; the yield rate of ERW octg casing is 93%~98%, while without the yield rate of seamed casing is 85%~90%; the entire project investment of ERW octg casing is also 40% lower than that of seamless casing project.
Technical characteristics of ERW octg casing
(1) Controlled rolling coils are selected as raw materials, and the S and P content and carbon equivalent are strictly controlled. Usually ω (S) ≤ 0.015% and carbon equivalent ≤ 0.25%. And use elements such as Nb, V, Ti and Cu to micro-alloy to improve the toughness of steel and improve its weldability and corrosion resistance.
(2) Thicker coiled plates are milled to reduce local overheating and oxidation caused by burrs during welding.
(3) Spiral loopers are widely used for continuous production, and there are no welding pauses caused by roll-to-roll intermittent production, resulting in product quality defects due to unstable welding current and voltage when welding is restarted.
(4) Advanced hydraulic internal burr removal technology is commonly used, and the internal burr height of the casing is controlled to within 1.14 mm.
(5) Strict welding parameters, including control of power input power, welding V-shaped angle, welding speed, and welding temperature. The welding temperature is controlled by the speed-power closed loop of the high-frequency welding machine, and the fluctuation is controlled to within ±5 °C.
(6) Pay attention to post-weld heat treatment and improve the structure and internal stress of the weld area through post-weld heat treatment.
(7) Using a high-strength sizing unit, the diameter reduction amount is large, and the finished product has good accuracy.
(8) Conduct online or offline non-destructive testing of welds and steel pipes as a whole to detect defects promptly and accurately so that the production process can be adjusted in a timely manner to ensure product quality.
Technical advantages of ERW octg casing (compared to seamless casing)
(1) High dimensional accuracy
ERW octg casing adopts a mechanical sizing process after forming, so that its dimensional accuracy (outer diameter, wall thickness, roundness, etc.) is improved compared with seamless casing, and its outer diameter deviation generally does not exceed ±0.5%. For example, the standard deviation of the wall thickness of the ф244.5 mm ERW octg casing produced by Japan's Nippon Steel Corporation is <0.10 mm, while the standard deviation of the corresponding seamless casing is 0.41 mm.
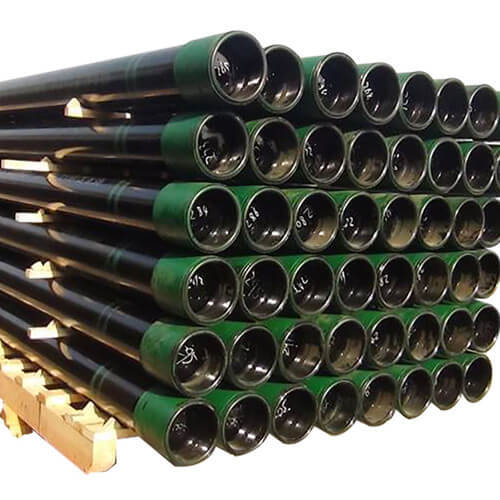
(2) The weld has good toughness
The manufacturing process of ERW octg casing can ensure a high-strength and high-toughness weld. The composition of the weld and the lower content of C, S and P in the base material make the casing more tough than seamless casing.
(3) Good anti-extrusion and anti-explosion properties
Compared with similar API seamless casings, ERW octg casings have 30% to 40% higher extrusion strength and about 50% higher explosion resistance (internal pressure).
(4) Advanced technology and good product quality control
The base material of the ERW octg casing is controlled-rolled coil plate, which is isotropic and can be 100% non-destructively inspected.
(5) Low cost
Compared with similar seamless casing, the cost of ERW octg casing is 5%~10% lower, the production efficiency is high, the degree of mechanization and automation is high, and the production energy consumption is low; the yield rate of ERW octg casing is 93%~98%, while without the yield rate of seamed casing is 85%~90%; the entire project investment of ERW octg casing is also 40% lower than that of seamless casing project.
Technical characteristics of ERW octg casing
(1) Controlled rolling coils are selected as raw materials, and the S and P content and carbon equivalent are strictly controlled. Usually ω (S) ≤ 0.015% and carbon equivalent ≤ 0.25%. And use elements such as Nb, V, Ti and Cu to micro-alloy to improve the toughness of steel and improve its weldability and corrosion resistance.
(2) Thicker coiled plates are milled to reduce local overheating and oxidation caused by burrs during welding.
(3) Spiral loopers are widely used for continuous production, and there are no welding pauses caused by roll-to-roll intermittent production, resulting in product quality defects due to unstable welding current and voltage when welding is restarted.
(4) Advanced hydraulic internal burr removal technology is commonly used, and the internal burr height of the casing is controlled to within 1.14 mm.
(5) Strict welding parameters, including control of power input power, welding V-shaped angle, welding speed, and welding temperature. The welding temperature is controlled by the speed-power closed loop of the high-frequency welding machine, and the fluctuation is controlled to within ±5 °C.
(6) Pay attention to post-weld heat treatment and improve the structure and internal stress of the weld area through post-weld heat treatment.
(7) Using a high-strength sizing unit, the diameter reduction amount is large, and the finished product has good accuracy.
(8) Conduct online or offline non-destructive testing of welds and steel pipes as a whole to detect defects promptly and accurately so that the production process can be adjusted in a timely manner to ensure product quality.