1. Galvanized Angle Steel
(1) Definition
Hot-dip galvanized angle steel immerses the rust-removed angle steel in a molten zinc solution at about 500℃, so that a zinc layer adheres to the surface of the angle steel, thereby achieving the purpose of corrosion protection. It is suitable for various strong corrosive environments such as strong acid and alkali mist.
(2) Process flow
The process flow of hot-dip galvanized angle steel: angle steel pickling-water washing-immersion plating solvent-drying preheating-hanging plating-cooling-passivation-cleaning-polishing-hot-dip galvanizing completion. The galvanized layer thickness of hot-dip galvanized angle steel is uniform, up to 30-50um, with good reliability. The galvanized layer and steel are metallurgically bonded and become part of the steel surface. Therefore, the coating durability of hot-dip galvanized angle steel is more reliable.
(3) Main classification
The raw material of hot-dip galvanized angle steel is angle steel, so the classification is the same as angle steel. According to the process classification, it can be divided into hot-dip galvanized hot-rolled angle steel and hot-dip galvanized cold-rolled angle steel. Hot-rolled hot-dip galvanized angle steel is common in the market. Hot-dip galvanized cold-rolled angle steel generally needs to be customized with cold-rolled plates according to user needs. According to the side length, it can be divided into hot-dip galvanized equal-angle steel and hot-dip galvanized unequal-angle steel.
(4) Main advantages
① Low processing cost: The cost of hot-dip galvanizing for rust prevention is lower than that of other paint coatings;② Durable: Hot-dip galvanized angle steel has the characteristics of surface gloss, uniform zinc layer, no missing plating, no dripping, strong adhesion and strong corrosion resistance. In suburban environments, the standard hot-dip galvanizing anti-rust thickness can be maintained for more than 50 years without repair; in urban or offshore areas, the standard hot-dip galvanizing anti-rust layer can be maintained for 20 years without repair;
③ Good reliability: The galvanized layer and the steel are metallurgically bonded and become part of the steel surface, so the durability of the coating is more reliable;
④ Strong toughness of the coating: The galvanized layer forms a special metallurgical structure that can withstand mechanical damage during transportation and use;
⑤ Comprehensive protection: Every part of the plated part can be zinc-plated, even in recessed areas, sharp corners and hidden places, it can be fully protected;
⑥ Save time and effort: The galvanizing process is faster than other coating construction methods and can avoid the time required for painting on the construction site after installation.
(5) Application fields
Galvanized angle steel is widely used in power towers, communication towers, railways, highway protection, street lamp poles, marine components, building steel structure components, substation ancillary facilities, light industry, etc.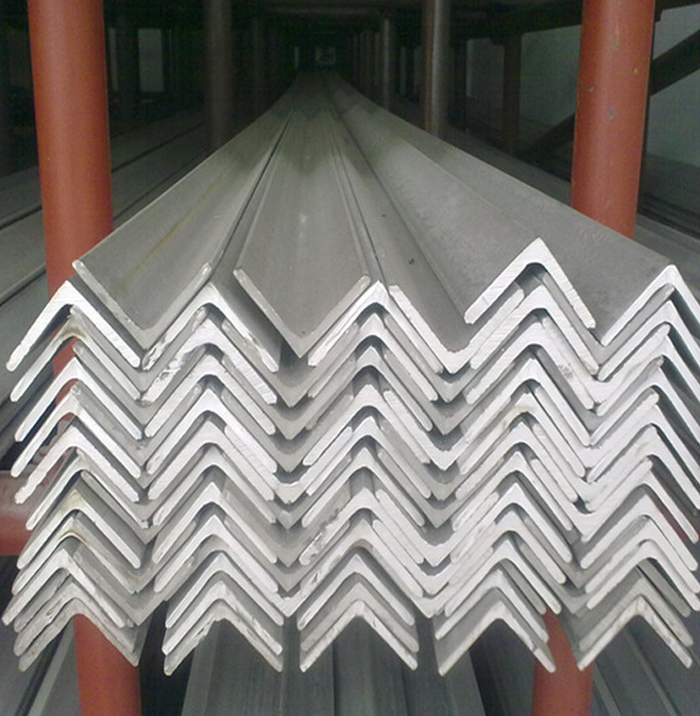
2. Galvanized channel steel
(1) Definition
Hot-dip galvanized channel steel can be divided into hot-dip galvanized channel steel and hot-blown galvanized channel steel according to the different galvanizing processes. The rust-free steel parts are immersed in molten zinc liquid at about 440~460℃ to make the zinc layer adhere to the surface of the steel parts, thereby achieving the purpose of corrosion protection.The main method for surface galvanizing of channel steel is hot-dip galvanizing. Hot-dip galvanizing is developed from the older hot-dip method. Since France applied hot-dip galvanizing to industry in 1836, it has a history of 170 years. However, in the past 30 years, with the rapid development of cold-rolled strip steel, the hot-dip galvanizing industry has developed on a large scale.
Among various coating methods for protecting steel substrates, hot-dip galvanizing is a very good one. It is a process in which zinc is in a liquid state and undergoes quite complex physical and chemical reactions to not only coat the steel with a thicker pure zinc layer, but also generate a zinc-iron alloy layer. This plating method not only has the corrosion resistance of electrogalvanizing, but also has a strong corrosion resistance that cannot be matched by electrogalvanizing due to the zinc-iron alloy layer. Therefore, this plating method is particularly suitable for various strong corrosive environments such as strong acid and alkaline mist.
The hot-dip galvanizing layer is formed by zinc in a high-temperature liquid state in three steps:
①The iron-based surface is dissolved by zinc liquid to form a zinc-iron alloy phase layer;
②The zinc ions in the alloy layer further diffuse into the matrix to form a zinc-iron intersoluble layer;
③The surface of the alloy layer is covered with a zinc layer.
(2) Process flow
The process flow of hot-dip galvanized channel steel: raw material inspection → pickling → cleaning → zinc assist → drying → galvanizing → cooling → passivation → cleaning → finished product inspection → inspection and packaging, etc.
(3) Features
① Hot-dip galvanized channel steel has a thick and dense pure zinc layer covering the steel surface, which can prevent the steel substrate from contacting with any corrosive solution and protect the steel substrate from corrosion. In the general atmosphere, a very thin and dense zinc oxide layer is formed on the surface of the zinc layer, which is difficult to dissolve in water, so it plays a certain protective role on the steel substrate. If zinc oxide generates insoluble zinc salts with other components in the atmosphere, the anti-corrosion effect is more ideal.②It has an iron-zinc alloy layer, which is densely bonded and exhibits unique corrosion resistance in marine salt spray atmosphere and industrial atmosphere;
③Due to the strong bond, zinc and iron are mutually soluble and have strong wear resistance;
④Since zinc has good ductility and its alloy layer is firmly attached to the steel base, hot-dip galvanized parts can be cold-punched, rolled, wire-drawn, bent and other various shapes without damaging the coating;
⑤After hot-dip galvanizing of steel structural parts, it is equivalent to an annealing treatment, which can effectively improve the mechanical properties of the steel base, eliminate the stress during steel forming and welding, and is conducive to turning of steel structural parts.
⑥The surface of the parts after hot-dip galvanizing is bright and beautiful.
⑦The pure zinc layer is the most plastic layer of the galvanized layer in hot-dip galvanizing. Its properties are basically close to pure zinc and have ductility, so it is flexible.
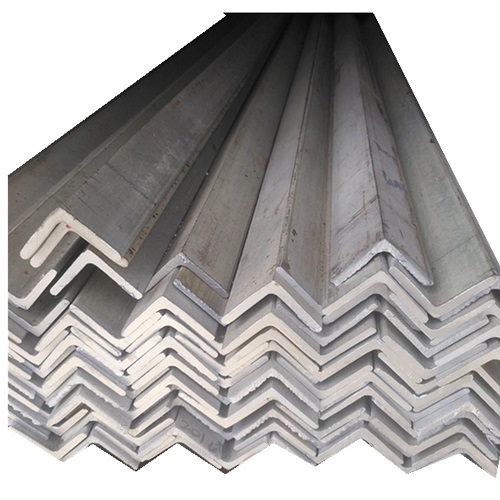