The reject rate of seamless pipes caused by the quenching process in the heat treatment process is often high, which is mainly due to the formation of large thermal stress and structural stress during the quenching process. In addition, due to factors such as inherent metallurgical defects, improper material selection, wrong materials, poor structural design, defects formed during cold and hot processing, etc.,they are easily exposed in the quenching and tempering process.
The hardness defects of seamless pipes after quenching mainly include two types: insufficient hardness and uneven hardness.
Insufficient hardness
The reasons for the insufficient hardness of the quenched seamless pipe are as follows.
(1) The heating temperature is too low and the holding time is insufficient. When checking the metallographic structure, undissolved ferrite can be seen in hypoeutectoid steel, and more undissolved carbide can be seen in steel pipe.
(2) Surface decarburization causes insufficient surface hardness. The hardness measured after grinding off the surface layer is higher than that of the surface.
(3) The cooling rate is not enough, and black troostite can be seen distributed along the product boundary in the metallographic structure.
(4) The hardenability of the steel pipe is not enough, and the large cross-section is not hardened.
(5) When interrupted quenching is used, the residence time in water is too short, or after taking it out of water, it stays in air for too long and then transfers it to oil, resulting in a decrease in hardness due to insufficient cooling or self-tempering.
(6) The quenching temperature of the seamless pipe is too high, and the amount of retained austenite is too much, which affects the hardness.
When there is insufficient hardness, the reason should be analyzed and corresponding measures should be taken. Among them, the hardness is insufficient due to the heating temperature being too high or too low. In addition to tempering and reheating and quenching to remedy the defects that have occurred, the furnace temperature measurement and control instruments should be strictly managed, and calibration and maintenance should be carried out regularly according to the metering transmission system.
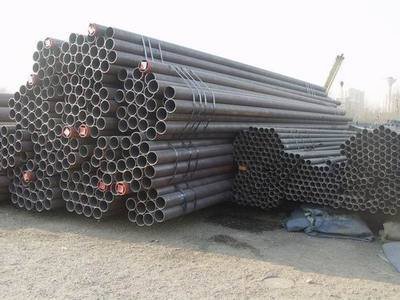
Inhomogeneous hardness
The uneven hardness means that the seamless pipe has soft spots after quenching. The reasons for the quenching soft spots are as follows:
(1) There are scales and dirt on the surface of the seamless pipe:
(2) There are impurities in the quenching medium, such as oil in the water, which will cause soft spots after quenching;
(3) When the seamless pipe is cooled in the quenching medium, the agitation of the cooling medium is not enough, and the groove of the seamless pipe and the bubbles formed at the large cross-section are not promptly driven away to produce soft spots:
(4) The carbon concentration on the surface of carburized parts is not uniform, and the hardness after quenching is not uniform;
(5) The original structure is not uniform before quenching, such as severe carbide segregation, or the original structure is coarse, and the ferrite is distributed in large blocks.
For the first three cases, it can be tempered once, reheated, and quenched under the conditions of appropriate cooling medium and cooling method. For the latter two cases, if there is no further processing after quenching, it will be difficult to remedy once the pitting occurs. For seamless pipes that have not been formed, in order to eliminate carbide segregation or coarseness, forging in different directions can be used to change its distribution and shape. The coarse structure can be annealed or normalized again to refine and homogenize the structure.
The hardness defects of seamless pipes after quenching mainly include two types: insufficient hardness and uneven hardness.
Insufficient hardness
The reasons for the insufficient hardness of the quenched seamless pipe are as follows.
(1) The heating temperature is too low and the holding time is insufficient. When checking the metallographic structure, undissolved ferrite can be seen in hypoeutectoid steel, and more undissolved carbide can be seen in steel pipe.
(2) Surface decarburization causes insufficient surface hardness. The hardness measured after grinding off the surface layer is higher than that of the surface.
(3) The cooling rate is not enough, and black troostite can be seen distributed along the product boundary in the metallographic structure.
(4) The hardenability of the steel pipe is not enough, and the large cross-section is not hardened.
(5) When interrupted quenching is used, the residence time in water is too short, or after taking it out of water, it stays in air for too long and then transfers it to oil, resulting in a decrease in hardness due to insufficient cooling or self-tempering.
(6) The quenching temperature of the seamless pipe is too high, and the amount of retained austenite is too much, which affects the hardness.
When there is insufficient hardness, the reason should be analyzed and corresponding measures should be taken. Among them, the hardness is insufficient due to the heating temperature being too high or too low. In addition to tempering and reheating and quenching to remedy the defects that have occurred, the furnace temperature measurement and control instruments should be strictly managed, and calibration and maintenance should be carried out regularly according to the metering transmission system.
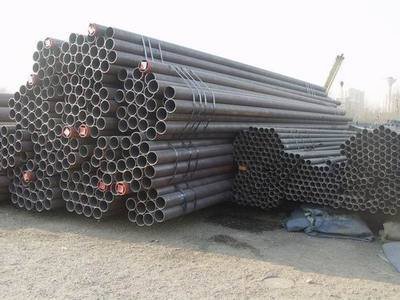
Inhomogeneous hardness
The uneven hardness means that the seamless pipe has soft spots after quenching. The reasons for the quenching soft spots are as follows:
(1) There are scales and dirt on the surface of the seamless pipe:
(2) There are impurities in the quenching medium, such as oil in the water, which will cause soft spots after quenching;
(3) When the seamless pipe is cooled in the quenching medium, the agitation of the cooling medium is not enough, and the groove of the seamless pipe and the bubbles formed at the large cross-section are not promptly driven away to produce soft spots:
(4) The carbon concentration on the surface of carburized parts is not uniform, and the hardness after quenching is not uniform;
(5) The original structure is not uniform before quenching, such as severe carbide segregation, or the original structure is coarse, and the ferrite is distributed in large blocks.
For the first three cases, it can be tempered once, reheated, and quenched under the conditions of appropriate cooling medium and cooling method. For the latter two cases, if there is no further processing after quenching, it will be difficult to remedy once the pitting occurs. For seamless pipes that have not been formed, in order to eliminate carbide segregation or coarseness, forging in different directions can be used to change its distribution and shape. The coarse structure can be annealed or normalized again to refine and homogenize the structure.