Helical (screw) pipe piles, as the name suggests, are pile foundations made using a spiral hole-forming process. Different from traditional concrete pouring piles or steel structure piles, helical pipe piles are made of high-strength materials and made through special processing techniques, which have longer service life.
With the continuous advancement of science and technology, various industries have an increasing demand for support for equipment and towers. Traditional concrete pouring or steel structure support is no longer able to meet the needs of some special places. In this case, a helical pipe pile emerged as a new type of equipment and tower support foundation.
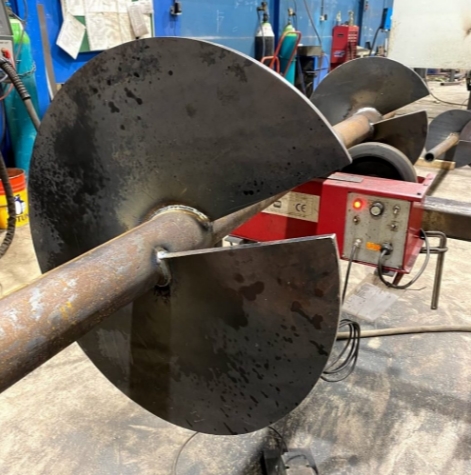
The main features of screw piles are their compact structure, easy installation, strong load-bearing capacity, and wide application range. It can be made of different materials and processing techniques according to different stratigraphic conditions and load-bearing requirements to meet the support needs of various equipment.
In practical applications, screw piles have been widely used in support projects for various equipment and towers. For example, screw piles play an important role in the construction of communication towers, power towers, bridges, highways, and other projects. It can effectively improve the stability and safety of equipment and towers and ensure the smooth progress of the project.
②Good performance
In addition, screw piers also have good seismic resistance and fatigue resistance, which can effectively improve the stability and safety of equipment and towers.
③Easy to install
At the same time, the installation of a helical pipe pile is also very simple. It does not require tedious formwork construction and maintenance work like traditional concrete piles, nor does it require welding and anti-corrosion treatment like steel structure piles. The installation of a helical pipe pile is usually done mechanically or manually. The construction period is short and the installation is simple and quick.
④Durability and environmental protection
In addition to the above characteristics, screw-piles also have good durability and environmental protection. Because helical piles are made of high-strength materials, they generally have a long service life and are less susceptible to corrosion and damage. In addition, the production and installation process of helical pipe piles is relatively environmentally friendly and will not have much impact on the surrounding environment.
Because screw anchors are formed by spiraling them into the soil, their load-bearing capacity may not be as good as other foundation treatments such as reinforced concrete piles. Therefore, in some situations where the geological pressure is high or the building is high, other foundation treatment methods need to be used.
②Subject to soil conditions
Compared with other foundation treatment methods, screw piles have more stringent requirements on soil conditions. For example, when the local soil moisture content is too high, the soil layer is hard, or the load is concentrated, the installation and use of screw piles may be affected.
The cost of helical pilings can vary depending on several factors, including:
Laying out and positioning→Drilling machine and air compressor in place→Drilling machine drilling→Drilling machine shifting→Pile driver in place→Pile feeding→Alignment pile insertion→Verticality correction→Pile drilling→Shifting
②Air compressor drilling method
The pile foundation is formed at one time: when the drilling machine is in place, keep it stable without tilt or displacement, keep the drill pipe vertical, the steel pile is in place, and the pile and pile foundation is fixed on the drill pipe. Mark a 1.5m scale line on the drill pipe to control drilling. The hole depth is below.
Piling: After the pile driver is in place, adjust the verticality of the helical piles and then screw the pile into the ground. Adjust the pile position at any time during the pile driving process to ensure that the position, size, and horizontal height of the pile after driving are within the required dimensional tolerance.
The pile drill itself has a bubble leveling device. After the shift is completed, the operator must level the pile drill horizontally and vertically.Set up a theodolite or line hammer directly in front and to the side of the pile drilling machine to adjust the verticality of the prefabricated piles in the front, rear, left, and right directions.
The bolts should be tightened in place, no gaps visible to the naked eye are allowed, and the depth of penetration into the soil should not exceed ±50mm.With the continuous development of science and technology, the production technology and technology of helical pipe pile are also constantly improved and perfected. In the future, helical piles will be more widely used in supporting projects for various equipment and towers, providing a safer, more reliable, and efficient support solution for engineering construction.
In short, as a new type of equipment and tower support foundation, helical piles have many advantages and advantages. It can effectively improve the stability and safety of equipment and towers and ensure the smooth progress of the project. In the future, with the continuous development of science and technology, screw piles will be more widely used and promoted.o
With the continuous advancement of science and technology, various industries have an increasing demand for support for equipment and towers. Traditional concrete pouring or steel structure support is no longer able to meet the needs of some special places. In this case, a helical pipe pile emerged as a new type of equipment and tower support foundation.
1. What are helical piles?
Helical piles, also known as helical cast-in-place piles, refer to piles that use machinery to drill a helical pile drill bit in a spiral shape into broken rock cuttings or soil, and directly combine drilling of the pile body with grouting. Screw piles are galvanized steel pipe piles that can replace cast-in-place piles to provide support for buildings.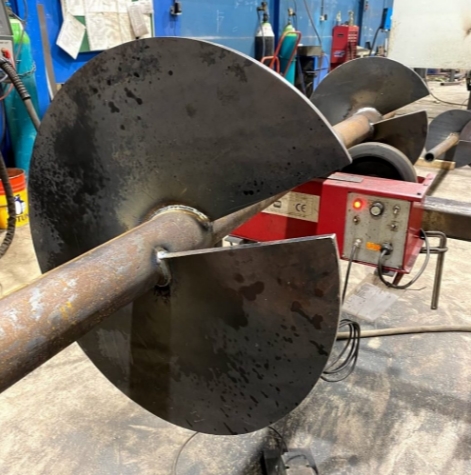
2. What is the purpose of helical piling?
The primary purpose of helical piles is to provide structural support for various types of foundations. They are typically used in construction projects where traditional foundation methods may be impractical or challenging.Helical piling is designed to transfer the load of a structure through the soil to deeper, more stable layers or to provide support in weaker or less predictable soil conditions. They are commonly used in applications such as building foundations, bridges, boardwalks, retaining walls, and other structures requiring reliable and cost-effective foundation solutions.3. What are the advantages and disadvantages of helical piles?
(1)Advantages
①FlexibilityThe main features of screw piles are their compact structure, easy installation, strong load-bearing capacity, and wide application range. It can be made of different materials and processing techniques according to different stratigraphic conditions and load-bearing requirements to meet the support needs of various equipment.
In practical applications, screw piles have been widely used in support projects for various equipment and towers. For example, screw piles play an important role in the construction of communication towers, power towers, bridges, highways, and other projects. It can effectively improve the stability and safety of equipment and towers and ensure the smooth progress of the project.
②Good performance
In addition, screw piers also have good seismic resistance and fatigue resistance, which can effectively improve the stability and safety of equipment and towers.
③Easy to install
At the same time, the installation of a helical pipe pile is also very simple. It does not require tedious formwork construction and maintenance work like traditional concrete piles, nor does it require welding and anti-corrosion treatment like steel structure piles. The installation of a helical pipe pile is usually done mechanically or manually. The construction period is short and the installation is simple and quick.
④Durability and environmental protection
In addition to the above characteristics, screw-piles also have good durability and environmental protection. Because helical piles are made of high-strength materials, they generally have a long service life and are less susceptible to corrosion and damage. In addition, the production and installation process of helical pipe piles is relatively environmentally friendly and will not have much impact on the surrounding environment.
(2)Disadvantages
①Small bearing capacityBecause screw anchors are formed by spiraling them into the soil, their load-bearing capacity may not be as good as other foundation treatments such as reinforced concrete piles. Therefore, in some situations where the geological pressure is high or the building is high, other foundation treatment methods need to be used.
②Subject to soil conditions
Compared with other foundation treatment methods, screw piles have more stringent requirements on soil conditions. For example, when the local soil moisture content is too high, the soil layer is hard, or the load is concentrated, the installation and use of screw piles may be affected.

4. How much do helical pilings cost?
The cost of helical pilings can vary depending on several factors, including:
(1)Project location
Prices can vary significantly depending on the region or country where the project is located due to differences in labor costs, material availability, and local regulations.(2)Soil conditions
The type and condition of the soil at the project site can impact the cost, as more challenging soil conditions may require specialized equipment or techniques for installation.(3)Load requirements
The load-bearing capacity required for the structure will influence the size and number of helical piles needed, affecting the overall cost.(4)Piling specifications
The size, length, and material of the helical piles will also influence the cost. Larger or longer piles, as well as those made from higher-grade materials, will typically be more expensive.(5)Access and site conditions
Accessibility to the site, ease of installation, and any site-specific challenges can impact the cost of helical piling installation.(6)Contractor rates
The rates charged by contractors or installation companies can vary based on their experience, expertise, and overhead costs.As a rough estimate, helical pilings can range from $30 to $150 per linear foot, but this can vary significantly depending on the factors mentioned above.6. Helical pile construction process
(1) Pay off the line
Firstly, measure and layout according to the confirmed general construction plan provided by the design department, and use measuring instruments including GPS measuring instrument, total station, theodolite, and other measuring instruments. The laying out accuracy needs to be controlled within 7mm;(2) Fixed stakes
According to the setting-out results of the helical piles design drawings, determine the location of each pile that needs to be driven, and mark it with easy-to-find objects such as small flags and wooden strips; surveyors use total stations and RTK to measure and set each helical piles based on the construction control network. The position of the piles should be marked, and the surveyor should review the axis pile positions to ensure that the position of each pile meets the design requirements and that the pile position is correct.(3) The pile driver reaches the pile position
The pile driver uses its traveling function and mast luffing mechanism to enable the drilling rig to quickly reach the pile position;(4) Send piles
Feed the spiral ground pile into the guide rod and adjust the verticality of the helical piles;(5) Pressurization
The power head device of the drilling rig provides torque for the helical pile, and the pressurizing device transmits pressure to the pile through pressurized power until the design elevation is drilled.(6)Adjust the pile driver
The pile driver operation is based on the measured pile position for construction. The crawler pile driver chooses a relatively flat and stable place to position before piling. If the ground slope is steep, use a winch to pull the pile driver. First, adjust the drill head front, back, left, and right. After preliminary adjustment, use a level ruler or line hammer to lift the verticality. After confirmation, proceed to the next step of construction. The pile position deviation is required to be <7mm and the verticality is 90±1°. Install the helical piles after the drilling rig is adjusted.(7) Check pipe piles
Before using the helical piles, the materials should be inspected to see if the size, hole position, blade material, etc. meet the requirements. In particular, check whether the welding of the helical piles steel pipe and the blade is firm. If the requirements are met, the inspection will be carried out according to the inspection batch, and then construction will be carried out.(3)Drill pile
After all preparations are completed, install the helical piles on the pile driver, and then use a magnetic level to correct the horizontality and verticality of the pile driver. Once the requirements are met, start drilling the pile. When drilling a pile, first center it and observe whether there is any deviation in the helical pile when drilling to 1/3 of the depth; if there is any deviation, make adjustments drill to 1/2, and then observe again. If there is no error, drill to the design depth.7. Helical piles construction technology measures
(1) Test pile requirements
Before the piling construction of each square array, two test piles must be tested, and the quality inspection personnel will be notified to stand by during the entire test.(2) Pile drilling method
①Pile drilling process:Laying out and positioning→Drilling machine and air compressor in place→Drilling machine drilling→Drilling machine shifting→Pile driver in place→Pile feeding→Alignment pile insertion→Verticality correction→Pile drilling→Shifting
②Air compressor drilling method
The pile foundation is formed at one time: when the drilling machine is in place, keep it stable without tilt or displacement, keep the drill pipe vertical, the steel pile is in place, and the pile and pile foundation is fixed on the drill pipe. Mark a 1.5m scale line on the drill pipe to control drilling. The hole depth is below.
- Deviation of pile center position: hole depth shall not be greater than 15 mm, and the distance between piles shall not be greater than ±20 mm.
- Side piles shall not be larger than ±20 mm
- Allowable deviation of pile depth: ±50 mm
- Permissible deviation of pile vertical
- Permissible deviation of pile verticality: ≤ 1% pile length
Piling: After the pile driver is in place, adjust the verticality of the helical piles and then screw the pile into the ground. Adjust the pile position at any time during the pile driving process to ensure that the position, size, and horizontal height of the pile after driving are within the required dimensional tolerance.
(3)Vertical control of pile body
Control Method:The pile drill itself has a bubble leveling device. After the shift is completed, the operator must level the pile drill horizontally and vertically.Set up a theodolite or line hammer directly in front and to the side of the pile drilling machine to adjust the verticality of the prefabricated piles in the front, rear, left, and right directions.
(4) Troubleshooting of drilled piles
Keep original records when drilling piles. If any abnormal situation occurs (such as machine damage, etc.), it should be dealt with in time. If an unexpected situation occurs (such as obstacles deep under the pile position, the pile cannot be drilled after reaching the bearing capacity, etc.), Party A should be notified promptly, and effective measures such as pile cutting should be studied together with the design unit.(5) Quality control of ground pile foundations
It is required that the parts are stored in a reasonable location and are not easily damaged or lost;The ground pile surface is clean, and the axis, elevation, and geometric dimensions are accurate. The basic requirements are that the vertical and horizontal length deviation is not more than ±30mm, and the center deviation is not more than 20mm;The bolts should be tightened in place, no gaps visible to the naked eye are allowed, and the depth of penetration into the soil should not exceed ±50mm.With the continuous development of science and technology, the production technology and technology of helical pipe pile are also constantly improved and perfected. In the future, helical piles will be more widely used in supporting projects for various equipment and towers, providing a safer, more reliable, and efficient support solution for engineering construction.
In short, as a new type of equipment and tower support foundation, helical piles have many advantages and advantages. It can effectively improve the stability and safety of equipment and towers and ensure the smooth progress of the project. In the future, with the continuous development of science and technology, screw piles will be more widely used and promoted.o
Previous:Black galvanized pipe
Next:Casing drilling