High pressure boiler tube is a kind of boiler tube, which belongs to the category of seamless steel tube. The manufacturing method is the same as that of seamless pipes, but there are strict requirements on the steel grades used to manufacture steel pipes. High-pressure boiler tubes are often used in high temperature and high pressure conditions, and the tubes will be oxidized and corroded under the action of high-temperature flue gas and water vapor. The steel pipe is required to have high lasting strength, high oxidation corrosion resistance, and good microstructure stability. High-pressure boiler tubes are mainly used to manufacture superheater tubes, reheater tubes, gas guide tubes, main steam tubes, etc. of high-pressure and ultra-high-pressure boilers.
Manufacturing method of high pressure boiler seamless pipe:
(1) The operating temperature of general boiler tubes is below 450°C, and they are mainly made of carbon-structured steel hot-rolled tubes or cold-drawn tubes.
(2) High-pressure boiler tubes are often exposed to high-temperature and high-pressure conditions when they are used. Under the action of high-temperature flue gas and water vapor, the tubes will be oxidized and corroded. Steel pipes are required to have high durable strength, high resistance to oxidation and corrosion, and good structural stability.
Due to the long-term operation of high-pressure boiler tubes under high temperature and high pressure conditions, the material will undergo creep, the plasticity and toughness will decrease, the original structure will change, and corrosion will occur.
Steel pipes used as boilers should have:
(1) Sufficient lasting strength;
(2) Sufficient plastic deformation capacity;
(3) Minimal aging tendency and hot brittleness;
(4) High anti-oxidation, coal ash resistance, natural gas high temperature corrosion resistance, steam and stress corrosion resistance;
(5) Good tissue stability and good process performance.
The steel grades of high pressure boiler tubes are carbon steel and pearlite, ferritic and austenitic stainless and heat-resistant steels. In order to improve the thermal efficiency of thermal power generating units and reduce fuel consumption, all countries in the world focus on developing large-capacity, high-parameter (high temperature, high pressure) thermal power generating units (above 1000MW). The steam pressure is increased to 31.5-34.3MPa, and the superheated steam temperature is 595-650℃, which develops to the ultra-high pressure critical pressure, which puts forward higher requirements for high-pressure boiler tubes. For this purpose, new steel grades have been developed to meet the needs of high-parameter utility boilers.
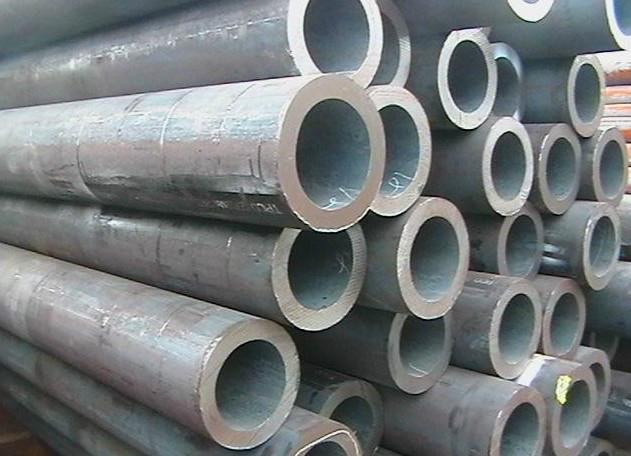
The production process of high-pressure boiler seamless tubes varies with different steel types.
The production process characteristics of high pressure boiler tubes are:
(1) The tube blank should be peeled, and the peeling amount is usually 5mm;
(2) Due to the hard steel, the tube blank is mostly cut or sawed with oxygen;
(3) Since the thermal conductivity of chromium molybdenum vanadium steel is lower than that of carbon steel, the heating speed should be slightly slower, the heating temperature is 1120~1180℃, and the piercing temperature is 1100~1160℃;
(4) This type of steel has good plasticity and low deformation resistance in the range of 1000-1100 °C, so the perforation performance is good, and the deformation parameters can be selected according to medium carbon steel or alloy steel (such as 30CrMnSiA);
(5) After rolling, the steel pipe should be normalized and tempered. The normalizing temperature is 950-980°C, the tempering temperature is 730-750°C, and the holding time is 2-3h;
(6) The dimensional tolerance of the steel pipe is strict to ensure the butt welding; the length of the pipe is as long as possible to reduce the number of welded joints.
The basic method of rust removal of high pressure boiler steel pipe:
(1) cleaning. Use solvents and emulsions to clean the surface of high-pressure boiler steel pipes to remove oil, grease, dust, lubricants and similar organic substances. But it can't remove the rust, scale, welding powder, etc. on the surface of the high-pressure boiler steel pipe, so it is only used as an auxiliary means in anti-corrosion production.
(2) Tool derusting. Mainly use tools such as wire brushes to polish the surface of high-pressure boiler steel pipes, which can remove loose or raised scale, rust, welding slag, etc. Hand tool derusting can reach Sa2 level, and power tool derusting can reach Sa3 level. If the surface of high-pressure boiler steel pipe is attached with firm oxide scale, the derusting effect of the tool is not ideal, and the anchor pattern depth required for anti-corrosion construction cannot be reached.
(3) pickling. Generally, two methods of chemical and electrolytic pickling are used for pickling treatment. Only chemical pickling is used for pipeline anticorrosion, which can remove scale, rust, and old coatings. Sometimes it can be used as retreatment after sandblasting and rust removal. Although chemical cleaning can achieve a certain degree of cleanliness and roughness on the surface, its anchor pattern is shallow and it is easy to pollute the environment.
(4) Spray (throw) to remove rust. Spraying (throwing) rust removal is driven by a high-power motor to rotate the spraying (throwing) blades at high speed. Abrasives such as steel sand, steel shots, iron wire segments, and minerals are sprayed (thrown) on the surface of the steel pipe under the action of centrifugal force. Not only can rust, oxides and dirt be completely removed, but also the high-pressure boiler steel pipe can achieve the required uniform roughness under the action of abrasive impact and friction.
Manufacturing method of high pressure boiler seamless pipe:
(1) The operating temperature of general boiler tubes is below 450°C, and they are mainly made of carbon-structured steel hot-rolled tubes or cold-drawn tubes.
(2) High-pressure boiler tubes are often exposed to high-temperature and high-pressure conditions when they are used. Under the action of high-temperature flue gas and water vapor, the tubes will be oxidized and corroded. Steel pipes are required to have high durable strength, high resistance to oxidation and corrosion, and good structural stability.
Due to the long-term operation of high-pressure boiler tubes under high temperature and high pressure conditions, the material will undergo creep, the plasticity and toughness will decrease, the original structure will change, and corrosion will occur.
Steel pipes used as boilers should have:
(1) Sufficient lasting strength;
(2) Sufficient plastic deformation capacity;
(3) Minimal aging tendency and hot brittleness;
(4) High anti-oxidation, coal ash resistance, natural gas high temperature corrosion resistance, steam and stress corrosion resistance;
(5) Good tissue stability and good process performance.
The steel grades of high pressure boiler tubes are carbon steel and pearlite, ferritic and austenitic stainless and heat-resistant steels. In order to improve the thermal efficiency of thermal power generating units and reduce fuel consumption, all countries in the world focus on developing large-capacity, high-parameter (high temperature, high pressure) thermal power generating units (above 1000MW). The steam pressure is increased to 31.5-34.3MPa, and the superheated steam temperature is 595-650℃, which develops to the ultra-high pressure critical pressure, which puts forward higher requirements for high-pressure boiler tubes. For this purpose, new steel grades have been developed to meet the needs of high-parameter utility boilers.
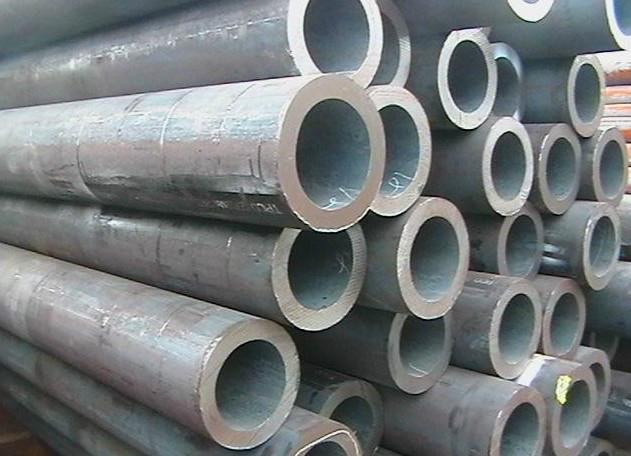
The production process of high-pressure boiler seamless tubes varies with different steel types.
The production process characteristics of high pressure boiler tubes are:
(1) The tube blank should be peeled, and the peeling amount is usually 5mm;
(2) Due to the hard steel, the tube blank is mostly cut or sawed with oxygen;
(3) Since the thermal conductivity of chromium molybdenum vanadium steel is lower than that of carbon steel, the heating speed should be slightly slower, the heating temperature is 1120~1180℃, and the piercing temperature is 1100~1160℃;
(4) This type of steel has good plasticity and low deformation resistance in the range of 1000-1100 °C, so the perforation performance is good, and the deformation parameters can be selected according to medium carbon steel or alloy steel (such as 30CrMnSiA);
(5) After rolling, the steel pipe should be normalized and tempered. The normalizing temperature is 950-980°C, the tempering temperature is 730-750°C, and the holding time is 2-3h;
(6) The dimensional tolerance of the steel pipe is strict to ensure the butt welding; the length of the pipe is as long as possible to reduce the number of welded joints.
The basic method of rust removal of high pressure boiler steel pipe:
(1) cleaning. Use solvents and emulsions to clean the surface of high-pressure boiler steel pipes to remove oil, grease, dust, lubricants and similar organic substances. But it can't remove the rust, scale, welding powder, etc. on the surface of the high-pressure boiler steel pipe, so it is only used as an auxiliary means in anti-corrosion production.
(2) Tool derusting. Mainly use tools such as wire brushes to polish the surface of high-pressure boiler steel pipes, which can remove loose or raised scale, rust, welding slag, etc. Hand tool derusting can reach Sa2 level, and power tool derusting can reach Sa3 level. If the surface of high-pressure boiler steel pipe is attached with firm oxide scale, the derusting effect of the tool is not ideal, and the anchor pattern depth required for anti-corrosion construction cannot be reached.
(3) pickling. Generally, two methods of chemical and electrolytic pickling are used for pickling treatment. Only chemical pickling is used for pipeline anticorrosion, which can remove scale, rust, and old coatings. Sometimes it can be used as retreatment after sandblasting and rust removal. Although chemical cleaning can achieve a certain degree of cleanliness and roughness on the surface, its anchor pattern is shallow and it is easy to pollute the environment.
(4) Spray (throw) to remove rust. Spraying (throwing) rust removal is driven by a high-power motor to rotate the spraying (throwing) blades at high speed. Abrasives such as steel sand, steel shots, iron wire segments, and minerals are sprayed (thrown) on the surface of the steel pipe under the action of centrifugal force. Not only can rust, oxides and dirt be completely removed, but also the high-pressure boiler steel pipe can achieve the required uniform roughness under the action of abrasive impact and friction.