In industrial settings, accurate measurement of black steel pipes is crucial for quality control and operational efficiency. Various techniques are employed to determine the length or position of these pipes, each offering distinct advantages and applications.
1. Grating ruler measurement
A grating ruler is a tool for measuring the length or position of a black steel pipe. It measures the displacement of an object by using the interference principle of light. It usually consists of a series of parallel lines with spaces between them called "ticks." When light passes through a grating scale, it is divided into a series of "bands", each band corresponding to a scale. By measuring the number of wave bands or the phase difference, we can calculate the displacement of an object.The length of a scale is usually expressed in millimeters or inches. Different scales have different graduation densities, that is, they contain different numbers of graduations per unit length. For example, a grating ruler with a scale density of 10 lines/mm contains 10 scale lines per millimeter.When using a grating ruler to measure black steel pipes, we need to note that its measurement accuracy is affected by many factors, such as the stability of the light source, the placement of the grating ruler, and the accuracy of readings.
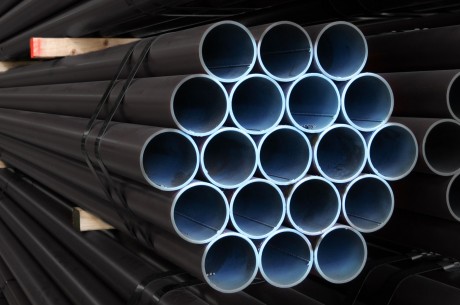
2.Camera measurement
The measurement of the length of a steel pipe using a camera involves optical or digital imaging technology combined with specialized software. The process begins with the camera capturing a digital image of the pipe, followed by calibration to ensure accurate image capture. The software then analyzes the image to detect and localize the steel pipe, employing computer vision techniques for object detection and dimensional analysis. By establishing reference points and analyzing relative dimensions within the image, the system calculates the length of the pipe. Verification methods are incorporated to ensure measurement accuracy , and the final measured length is displayed to the user through a graphical interface or numerical readout. Industries often employ machine vision systems and may utilize laser scanning or 3D imaging technologies for comprehensive dimensional measurements. Overall, camera-based measurement systems offer precise and efficient length measurements for steel pipes, benefiting quality control, inventory management, and various manufacturing and construction processes.
3. Encoder measurement
The working principle of the encoder is based on the measurement of physical movement and timing fundamentals. The technologies they use include photoelectric, magnetoelectric, capacitive and inductive. A rotary encoder consists of a rotating disk and a fixed measuring head, which converts rotational motion into a pulse signal output. Linear encoders support motion along a straight line and are suitable for high-precision measurements and position control applications requiring long stroke measurements.
Install an encoder at the oil cylinder, use the oil cylinder to push the steel pipe to move on the roller table, and install a series of photoelectric switches at equal distances on the other side. When the steel pipe is pushed by the oil cylinder and the end of the pipe touches the photoelectric switch, the recorded encoder readings are converted. Find out the stroke of the oil cylinder, and then you can calculate the length of the black steel pipe.
By leveraging these diverse measurement techniques, industries can effectively address the challenges associated with accurately measuring the length and position of black steel pipes. Whether it’s the interference principle of light, sophisticated digital imaging technology, or fundamental physical movement and timing, each approach plays a vital role in achieving precise measurements essential for quality control, inventory management, and construction processes. As industrial operations continue to evolve, the integration of these measurement methodologies will remain instrumental in ensuring the integrity and accuracy of steel pipe measurements, thereby enhancing overall operational efficiency and product reliability.
1. Grating ruler measurement
A grating ruler is a tool for measuring the length or position of a black steel pipe. It measures the displacement of an object by using the interference principle of light. It usually consists of a series of parallel lines with spaces between them called "ticks." When light passes through a grating scale, it is divided into a series of "bands", each band corresponding to a scale. By measuring the number of wave bands or the phase difference, we can calculate the displacement of an object.The length of a scale is usually expressed in millimeters or inches. Different scales have different graduation densities, that is, they contain different numbers of graduations per unit length. For example, a grating ruler with a scale density of 10 lines/mm contains 10 scale lines per millimeter.When using a grating ruler to measure black steel pipes, we need to note that its measurement accuracy is affected by many factors, such as the stability of the light source, the placement of the grating ruler, and the accuracy of readings.
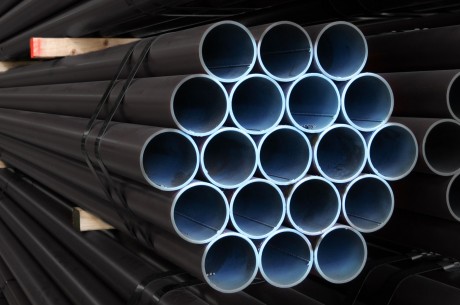
2.Camera measurement
The measurement of the length of a steel pipe using a camera involves optical or digital imaging technology combined with specialized software. The process begins with the camera capturing a digital image of the pipe, followed by calibration to ensure accurate image capture. The software then analyzes the image to detect and localize the steel pipe, employing computer vision techniques for object detection and dimensional analysis. By establishing reference points and analyzing relative dimensions within the image, the system calculates the length of the pipe. Verification methods are incorporated to ensure measurement accuracy , and the final measured length is displayed to the user through a graphical interface or numerical readout. Industries often employ machine vision systems and may utilize laser scanning or 3D imaging technologies for comprehensive dimensional measurements. Overall, camera-based measurement systems offer precise and efficient length measurements for steel pipes, benefiting quality control, inventory management, and various manufacturing and construction processes.
3. Encoder measurement
The working principle of the encoder is based on the measurement of physical movement and timing fundamentals. The technologies they use include photoelectric, magnetoelectric, capacitive and inductive. A rotary encoder consists of a rotating disk and a fixed measuring head, which converts rotational motion into a pulse signal output. Linear encoders support motion along a straight line and are suitable for high-precision measurements and position control applications requiring long stroke measurements.
Install an encoder at the oil cylinder, use the oil cylinder to push the steel pipe to move on the roller table, and install a series of photoelectric switches at equal distances on the other side. When the steel pipe is pushed by the oil cylinder and the end of the pipe touches the photoelectric switch, the recorded encoder readings are converted. Find out the stroke of the oil cylinder, and then you can calculate the length of the black steel pipe.
By leveraging these diverse measurement techniques, industries can effectively address the challenges associated with accurately measuring the length and position of black steel pipes. Whether it’s the interference principle of light, sophisticated digital imaging technology, or fundamental physical movement and timing, each approach plays a vital role in achieving precise measurements essential for quality control, inventory management, and construction processes. As industrial operations continue to evolve, the integration of these measurement methodologies will remain instrumental in ensuring the integrity and accuracy of steel pipe measurements, thereby enhancing overall operational efficiency and product reliability.