Large-diameter thick-walled steel pipe production process:
The production process of large-diameter thick-walled steel pipe generally includes hot rolling, hot coiling, casting and other production methods. Large-diameter thick-walled steel pipes are mostly produced in double-sided submerged arc welding (SSAW pipe). After bending, jointing, internal welding, external welding, straightening, and flattening, the products meet the standards of the American Petroleum Institute.
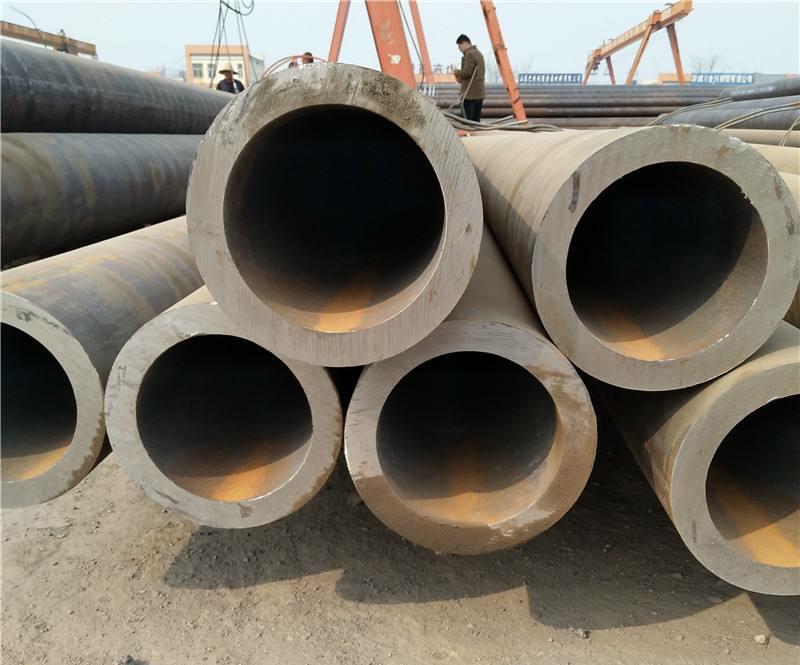
How to cool after the quenching process of large-diameter thick-walled steel pipes?
(1) When quenching, the workpiece must be heated to a higher temperature and cooled at a faster rate, so a large thermal stress will be generated during quenching, especially during quenching and cooling. Temperature changes on the surface and center of a steel ball with a diameter of 26 mm when heated to 700°C and cooled in water.
(2) In the early stage of cooling, the cooling rate of the surface obviously exceeds that of the center, and the temperature difference between the surface and the center increases continuously. When cooling continues, the cooling rate of the surface slows down, while the cooling rate of the core increases relatively. When the cooling rates of the surface and the core are almost equal, the temperature difference between them reaches a large value.
(3) Subsequently, the cooling rate of the core is greater than that of the surface, the surface temperature difference gradually decreases, and the temperature difference disappears completely until the core is completely cooled. The process of generating thermal stress in the event of rapid cooling.
(4) In the initial stage of cooling, the surface layer cools rapidly, and a temperature difference begins to appear between it and the core. Due to the physical characteristics of thermal expansion and contraction, the volume of the surface layer must be reliably contracted, while the high center temperature and large specific volume hinder the free inward contraction of the surface layer, thus forming thermal stress in which the surface layer is pulled and the central part is compressed.
(5) With cooling, the above-mentioned temperature difference continues to increase, and the resulting thermal stress also increases accordingly. When the temperature difference reaches a larger value, the thermal stress is also larger. If the thermal stress at this time is lower than the yield strength of the steel at the corresponding temperature, it will not cause plastic deformation, but only a small amount of elastic deformation.
(6) When further cooling, the surface cooling rate slows down, the core cooling rate increases accordingly, the temperature difference tends to decrease, and the thermal stress also gradually decreases. As the thermal stress decreases, the above elastic deformation decreases accordingly.
Tips: Large-diameter thick-walled steel pipe use:
Large-diameter thick-walled steel pipes are mostly used in large-scale steel structure construction as the main support part (steel pipe pile), such as bridge piling, submarine piling, and high-rise building piling.
The production process of large-diameter thick-walled steel pipe generally includes hot rolling, hot coiling, casting and other production methods. Large-diameter thick-walled steel pipes are mostly produced in double-sided submerged arc welding (SSAW pipe). After bending, jointing, internal welding, external welding, straightening, and flattening, the products meet the standards of the American Petroleum Institute.
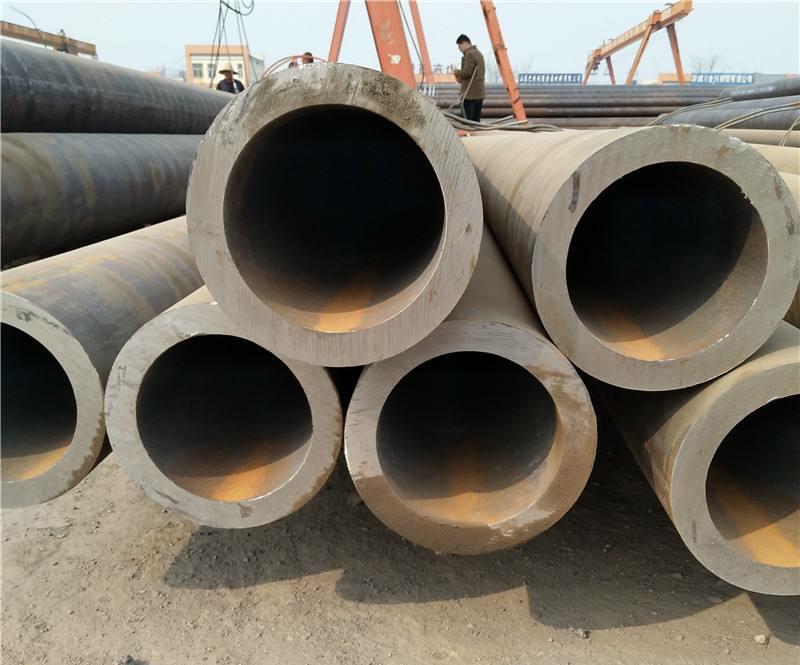
How to cool after the quenching process of large-diameter thick-walled steel pipes?
(1) When quenching, the workpiece must be heated to a higher temperature and cooled at a faster rate, so a large thermal stress will be generated during quenching, especially during quenching and cooling. Temperature changes on the surface and center of a steel ball with a diameter of 26 mm when heated to 700°C and cooled in water.
(2) In the early stage of cooling, the cooling rate of the surface obviously exceeds that of the center, and the temperature difference between the surface and the center increases continuously. When cooling continues, the cooling rate of the surface slows down, while the cooling rate of the core increases relatively. When the cooling rates of the surface and the core are almost equal, the temperature difference between them reaches a large value.
(3) Subsequently, the cooling rate of the core is greater than that of the surface, the surface temperature difference gradually decreases, and the temperature difference disappears completely until the core is completely cooled. The process of generating thermal stress in the event of rapid cooling.
(4) In the initial stage of cooling, the surface layer cools rapidly, and a temperature difference begins to appear between it and the core. Due to the physical characteristics of thermal expansion and contraction, the volume of the surface layer must be reliably contracted, while the high center temperature and large specific volume hinder the free inward contraction of the surface layer, thus forming thermal stress in which the surface layer is pulled and the central part is compressed.
(5) With cooling, the above-mentioned temperature difference continues to increase, and the resulting thermal stress also increases accordingly. When the temperature difference reaches a larger value, the thermal stress is also larger. If the thermal stress at this time is lower than the yield strength of the steel at the corresponding temperature, it will not cause plastic deformation, but only a small amount of elastic deformation.
(6) When further cooling, the surface cooling rate slows down, the core cooling rate increases accordingly, the temperature difference tends to decrease, and the thermal stress also gradually decreases. As the thermal stress decreases, the above elastic deformation decreases accordingly.
Tips: Large-diameter thick-walled steel pipe use:
Large-diameter thick-walled steel pipes are mostly used in large-scale steel structure construction as the main support part (steel pipe pile), such as bridge piling, submarine piling, and high-rise building piling.