Spiral steel pipe (SSAW pipe) is a welded pipe made of strip steel coil as raw material, extruded at regular temperature, and welded by automatic double-wire double-sided submerged arc welding process. The spiral steel pipe sends the strip steel into the welded pipe unit, and after rolling by multiple rollers, the strip steel is gradually rolled up to form a circular tube blank with an opening gap. Adjust the reduction amount of the squeeze roller to control the gap between the weld seams at 1~3mm, and make the two ends of the weld joints flush.
There are two common processing methods for spiral steel pipes.
Thermal expansion method
1. Bulging method. One is to place rubber in the tube and compress it with a punch above to make the tube protrude. Another method is hydraulic bulge forming, in which liquid is filled in the middle of the pipe, and the liquid pressure bulges the pipe into the desired shape. This method is mostly used in the production of corrugated pipes.
2. Forging method Use a swage forging machine to stretch the end or part of the pipe to reduce the outer diameter. Commonly used swage forging machines include rotary type, connecting rod type, and roller type.
3. Bending forming method. There are three methods commonly used, one method is called stretching method, and the other method is called stamping method. The third roller method has 3-4 rollers, two fixed rollers, and one adjustment roller to adjust the distance between the fixed rollers, and the finished pipe fittings are bent.
4. Stamping method Use a tapered core on the punching machine to expand the pipe end to the required size and shape.
5. The rolling method generally does not use a mandrel, and is suitable for the inner round edge of the thick-walled tube.
6. Roller method Place the core in the tube, and push the outer circumference with a roller for round edge processing.
Anti-corrosion method
It is anti-corrosion spiral steel pipe. This processing method refers to coating the surface and inner layer of spiral steel pipe with chemical coating. Common anticorrosion forms include 3pe anticorrosion, epoxy resin anticorrosion, and cement mortar anticorrosion. The biggest purpose of this processing method is to prolong the service life of the pipeline.
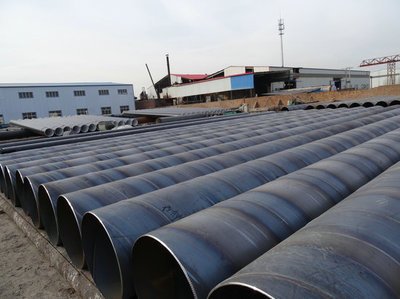
During the processing of spiral welded pipe, the following issues should be paid attention to:
1. Oiling and marking: oiling operation is carried out on the qualified spiral steel pipe to prevent corrosion, and marking is carried out according to the requirements of customers.
2. Leveling and edge milling: use an anvil to level the original curled steel plate, and then use an edge milling machine to mill both edges of the steel plate on both sides to make it meet the required plate width, plate edge parallelism and groove shape.
3. Shear forming: the steel plate is spirally curled into a tubular shape along the outer edge.
4. Butt welding cutting: Pre-welding, inner welding and outer welding are carried out by double-sided submerged arc welding technology. Cut the welded and formed steel pipes to standard lengths using a plasma ruler.
5. Visual inspection: Check some basic parameters by professional technicians.
6. Ultrasonic flaw detection: 100% inspection of the internal and external welds and the base metal on both sides of the weld.
7. X-ray flaw detection: 100% X-ray industrial TV inspection is carried out on the internal and external welds, and the image processing system is used to ensure the sensitivity of flaw detection.
8. Pressure test: The spiral steel pipes are inspected one by one on the hydraulic testing machine to ensure that the steel pipes meet the test pressure required by the standard.
9. Chamfered flat head: Process the pipe end of the thick-walled spiral pipe that has passed the inspection to meet the required bevel size of the pipe end.
10. Final inspection: The spiral steel pipe is subjected to ultrasonic and X-ray flaw detection and magnetic particle inspection at the pipe end again to check whether there are welding problems and pipe end defects.
There are two common processing methods for spiral steel pipes.
Thermal expansion method
1. Bulging method. One is to place rubber in the tube and compress it with a punch above to make the tube protrude. Another method is hydraulic bulge forming, in which liquid is filled in the middle of the pipe, and the liquid pressure bulges the pipe into the desired shape. This method is mostly used in the production of corrugated pipes.
2. Forging method Use a swage forging machine to stretch the end or part of the pipe to reduce the outer diameter. Commonly used swage forging machines include rotary type, connecting rod type, and roller type.
3. Bending forming method. There are three methods commonly used, one method is called stretching method, and the other method is called stamping method. The third roller method has 3-4 rollers, two fixed rollers, and one adjustment roller to adjust the distance between the fixed rollers, and the finished pipe fittings are bent.
4. Stamping method Use a tapered core on the punching machine to expand the pipe end to the required size and shape.
5. The rolling method generally does not use a mandrel, and is suitable for the inner round edge of the thick-walled tube.
6. Roller method Place the core in the tube, and push the outer circumference with a roller for round edge processing.
Anti-corrosion method
It is anti-corrosion spiral steel pipe. This processing method refers to coating the surface and inner layer of spiral steel pipe with chemical coating. Common anticorrosion forms include 3pe anticorrosion, epoxy resin anticorrosion, and cement mortar anticorrosion. The biggest purpose of this processing method is to prolong the service life of the pipeline.
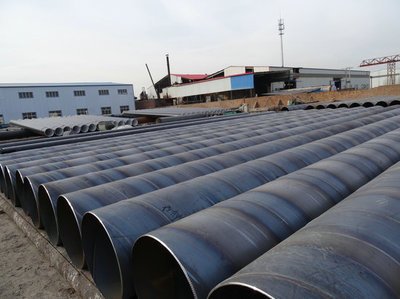
During the processing of spiral welded pipe, the following issues should be paid attention to:
1. Oiling and marking: oiling operation is carried out on the qualified spiral steel pipe to prevent corrosion, and marking is carried out according to the requirements of customers.
2. Leveling and edge milling: use an anvil to level the original curled steel plate, and then use an edge milling machine to mill both edges of the steel plate on both sides to make it meet the required plate width, plate edge parallelism and groove shape.
3. Shear forming: the steel plate is spirally curled into a tubular shape along the outer edge.
4. Butt welding cutting: Pre-welding, inner welding and outer welding are carried out by double-sided submerged arc welding technology. Cut the welded and formed steel pipes to standard lengths using a plasma ruler.
5. Visual inspection: Check some basic parameters by professional technicians.
6. Ultrasonic flaw detection: 100% inspection of the internal and external welds and the base metal on both sides of the weld.
7. X-ray flaw detection: 100% X-ray industrial TV inspection is carried out on the internal and external welds, and the image processing system is used to ensure the sensitivity of flaw detection.
8. Pressure test: The spiral steel pipes are inspected one by one on the hydraulic testing machine to ensure that the steel pipes meet the test pressure required by the standard.
9. Chamfered flat head: Process the pipe end of the thick-walled spiral pipe that has passed the inspection to meet the required bevel size of the pipe end.
10. Final inspection: The spiral steel pipe is subjected to ultrasonic and X-ray flaw detection and magnetic particle inspection at the pipe end again to check whether there are welding problems and pipe end defects.