Overall bending is the second step of high frequency welded pipe forming, and its purpose is to bend the pipe as a whole to the curvature of the closed lead-in roller. The traditional overall bending adopts flat/vertical roller alternate empty bending forming.
The typical process of high frequency welded pipe is the same as that of other welded tubes:
Slitting-uncoiling-strip leveling-head and tail shearing-strip butt welding-loop storage-forming-welding-deburring-sizing-flaw detection-fly cutting-initial inspection-steel pipe straightening-pipe section processing- Hydrotesting - flaw detection - printing and coating - finished product.
Advantages and disadvantages of integral forming of high frequency welded pipe
The modern and advanced overall forming process adopts row-roll forming and concentrated empty bending forming, and the FFX forming process adopts involute vertical roller group hollow bending to realize integral forming.
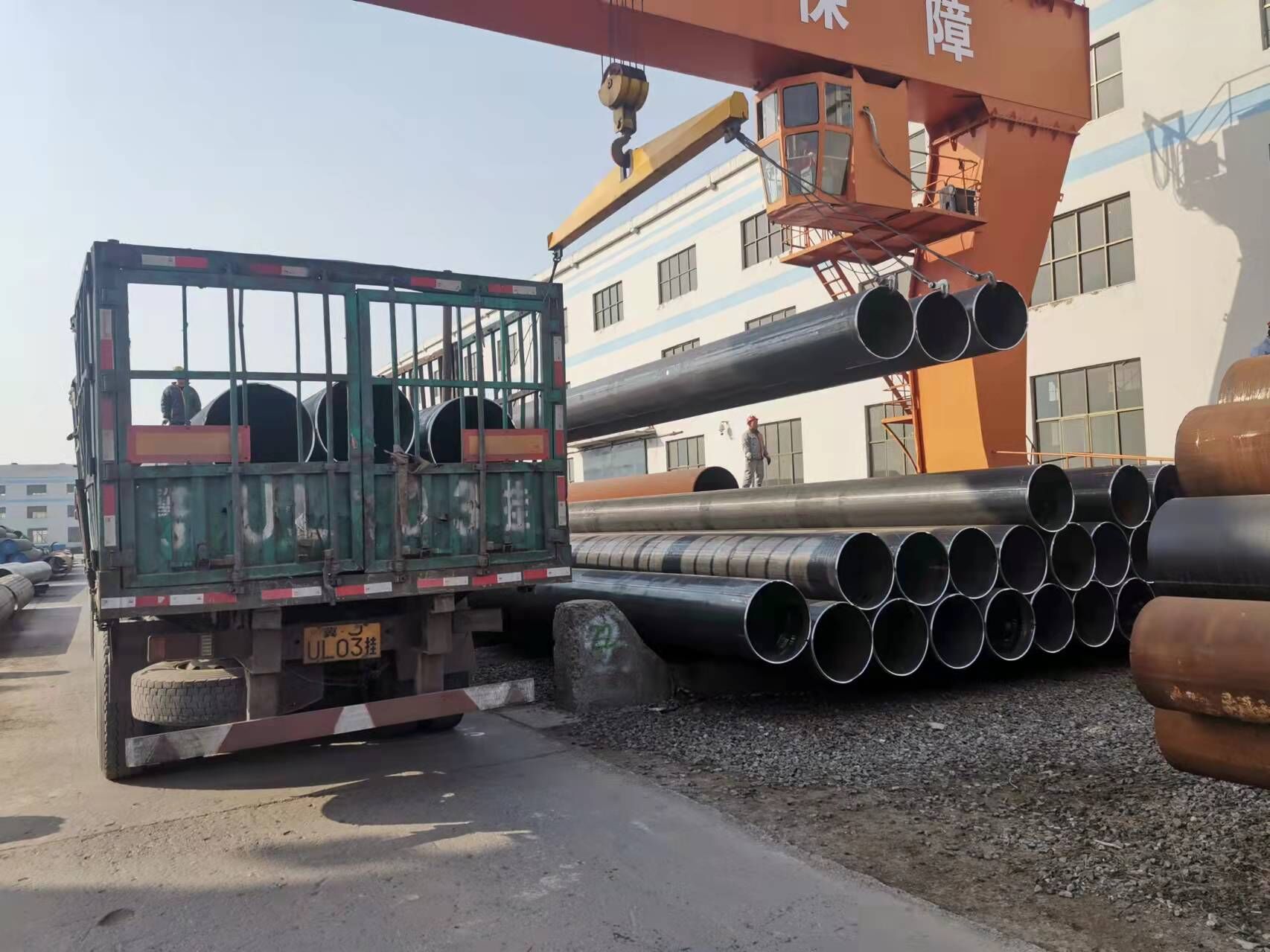
1. Flat/vertical roll forming alternately
The passes and strips formed by flat/vertical rolls alternately are closed empty bends. The flat rolls and vertical rolls are arranged alternately, the flat rolls are the driving rolls, the vertical rolls are the passive rolls, and the flat rolls and vertical rolls perform empty bending one by one.
Advantages: Good formability, uniform and stable forming force distribution, good strip alignment, and not easy to deviate from the rolling center.
2. Forming in row roller group/involute vertical roller group
The pass and strip formed in the row roller group/involute vertical roller group are open empty bends. The strip is continuously concentrated and air-bent by the row roller group or the involute vertical roller group.
Advantages: It is easy for the strip material to enter the hole pattern, the surface is not easily scratched, the forming route is short, and the rolls can be shared well.
shortcoming:
(1) The frame structure is complex and difficult to adjust;
(2) The row roller group/vertical roller group is non-power transmission, and can only be pushed into the pass by external force;
(3) The roller group relies on the retaining roller to prevent the strip material from deviating from the rolling center, which will easily lead to thickening of the strip edge.
The typical process of high frequency welded pipe is the same as that of other welded tubes:
Slitting-uncoiling-strip leveling-head and tail shearing-strip butt welding-loop storage-forming-welding-deburring-sizing-flaw detection-fly cutting-initial inspection-steel pipe straightening-pipe section processing- Hydrotesting - flaw detection - printing and coating - finished product.
Advantages and disadvantages of integral forming of high frequency welded pipe
The modern and advanced overall forming process adopts row-roll forming and concentrated empty bending forming, and the FFX forming process adopts involute vertical roller group hollow bending to realize integral forming.
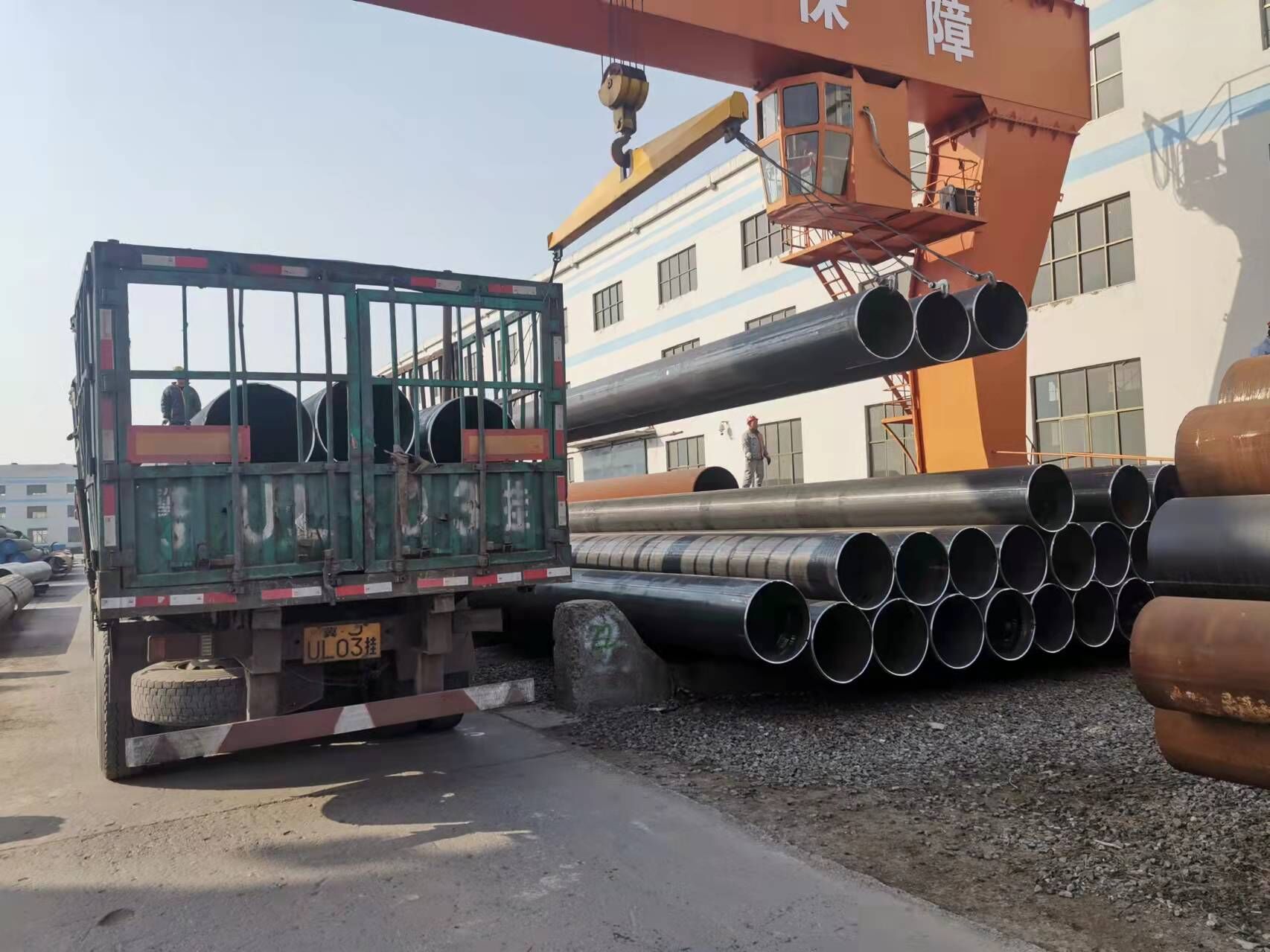
1. Flat/vertical roll forming alternately
The passes and strips formed by flat/vertical rolls alternately are closed empty bends. The flat rolls and vertical rolls are arranged alternately, the flat rolls are the driving rolls, the vertical rolls are the passive rolls, and the flat rolls and vertical rolls perform empty bending one by one.
Advantages: Good formability, uniform and stable forming force distribution, good strip alignment, and not easy to deviate from the rolling center.
2. Forming in row roller group/involute vertical roller group
The pass and strip formed in the row roller group/involute vertical roller group are open empty bends. The strip is continuously concentrated and air-bent by the row roller group or the involute vertical roller group.
Advantages: It is easy for the strip material to enter the hole pattern, the surface is not easily scratched, the forming route is short, and the rolls can be shared well.
shortcoming:
(1) The frame structure is complex and difficult to adjust;
(2) The row roller group/vertical roller group is non-power transmission, and can only be pushed into the pass by external force;
(3) The roller group relies on the retaining roller to prevent the strip material from deviating from the rolling center, which will easily lead to thickening of the strip edge.