Directly buried prefabricated insulated seamless pipe is not a certain type of steel pipe. "Directly buried prefabricated" refers to a type of steel pipe with an insulation layer and anti-corrosion prefabricated in the insulated pipe factory. After being delivered to the project site, it can be directly hoisted into the pipe pit. After welding, it is directly buried underground, eliminating the need for on-site anti-corrosion and insulation of the steel pipe. In this way, factory-prefabricated steel pipes can not only reduce budget costs, but also shorten the project construction cycle.
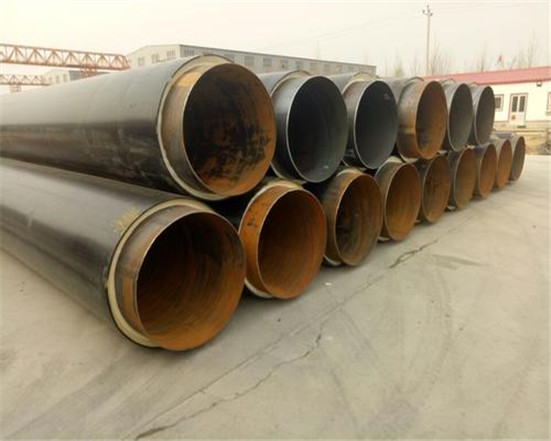
Directly buried prefabricated insulated pipes can generally be divided into two types: polyurethane directly buried prefabricated insulated pipes and steel-sheathed steel directly buried prefabricated insulated pipes. The polyethylene outer sheath pipe, polyurethane insulation layer and inner steel pipe of the polyurethane direct-buried prefabricated insulated seamless pipe are closely connected together. It is required that the transported medium should not have too much vibration. Excessive vibration can easily cause the separation of the insulation layer and the inner steel pipe, reducing the insulation effect. Generally used in municipal engineering, mainly used to transport hot water.
Steel-sheathed steel direct-buried prefabricated insulated seamless pipes are mainly composed of outer steel pipes, built-in brackets, rock wool silicate circuits and other insulation auxiliary materials, and inner steel pipes. The outer steel pipe is generally a spiral steel pipe, which is anti-corrosion and buried underground in direct contact with earth and rock. The built-in bracket can support the inner steel pipe so that the inner steel pipe can move in both directions and offset the vibration of the pipe. Insulation auxiliary materials are generally wrapped around the outside of the inner steel pipe of the directly buried prefabricated insulation pipe. The number of wrapping layers depends on the insulation effect to be achieved. In order to reduce heat loss, a reflective layer must be added between each layer of insulation material. The inner pipe mainly uses seamless steel pipe, because the pressure inside the pipe is still relatively large when transporting steam.
It is worth noting that when installing directly buried prefabricated insulated seamless pipes, it is best to bury them in trenches and not to use the method of drawing pipes. Although pulling the pipe saves costs, it can easily cause damage to the insulation pipe during the pulling process. Once damaged, it is difficult to repair it in a short time.
The following are the construction points of directly buried prefabricated insulated seamless pipes
1. Preparation work before construction
(1) Several professional construction personnel, holding professional certificates to work.
(2) Construction materials should comply with relevant construction standards and specifications, and the quality of materials ensures smooth construction.
(3) Conduct an all-round professional and comprehensive inspection of the patching process. Only after all inspections have passed the inspection can the next construction step be entered.
(4) Integrate, analyze, and output the key parameters that affect the quality of the joint, and improve the errors that may occur during the process.
2. Introduction to construction technology
After the pipeline welding link has passed the inspection, the repair work can be carried out without affecting the construction. First determine the basic parameters and construction procedures of the joint to ensure that there will be no problems with the construction quality. The construction process is suitable to be carried out under conditions above 15C and humidity below 85%.
3. Polyethylene casing installation process
Before installation, pay attention to cleaning the soil and debris around the casing to ensure that the bonding joint is clean. Accurate the docking dimensions of the casing and the outer casing. When docking, ensure that the installation is horizontal and centered to ensure the smooth progress of the docking work.
4. Air tightness test and detection process
(1) Drill a hole in the outer tube first, install the pressure gauge vertically on this part, and fix it with bolts.
(2) Turn on the air compressor, raise the pressure to about 0.02Mpa, and use soapy water to check whether there is air leakage.
(3) If there is air leakage, it should be repaired in time, and then the air tightness test should be carried out. Only when there is no problem can polyurethane foaming be carried out.
5. Basic conditions requirements for construction sites
(1) The polyurethane in prefabricated directly buried thermal insulation pipes cannot be soaked in water for a long time. Therefore, a drainage system must be set up during the construction process to ensure smooth pipeline installation.
(2) The drainage process requires specialized personnel to monitor the drainage process to prevent the pipes from being soaked in water and affecting the construction process.
(3) In order to ensure the overall quality of the construction, the construction period should be reasonably arranged and each link clearly marked.
(4) Whether necessary supports should be set up in the operation pit should be determined based on the specific depth, loose soil conditions and groundwater level to ensure the safety of construction workers.
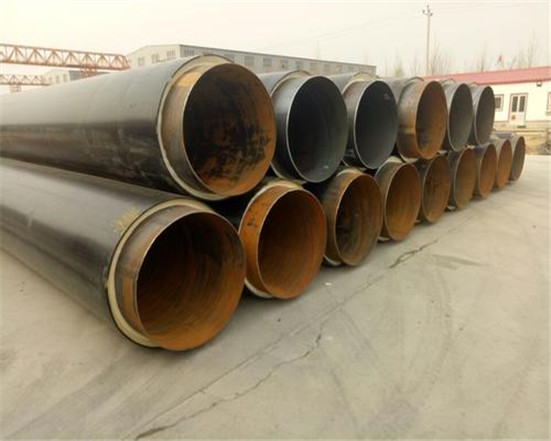
Directly buried prefabricated insulated pipes can generally be divided into two types: polyurethane directly buried prefabricated insulated pipes and steel-sheathed steel directly buried prefabricated insulated pipes. The polyethylene outer sheath pipe, polyurethane insulation layer and inner steel pipe of the polyurethane direct-buried prefabricated insulated seamless pipe are closely connected together. It is required that the transported medium should not have too much vibration. Excessive vibration can easily cause the separation of the insulation layer and the inner steel pipe, reducing the insulation effect. Generally used in municipal engineering, mainly used to transport hot water.
Steel-sheathed steel direct-buried prefabricated insulated seamless pipes are mainly composed of outer steel pipes, built-in brackets, rock wool silicate circuits and other insulation auxiliary materials, and inner steel pipes. The outer steel pipe is generally a spiral steel pipe, which is anti-corrosion and buried underground in direct contact with earth and rock. The built-in bracket can support the inner steel pipe so that the inner steel pipe can move in both directions and offset the vibration of the pipe. Insulation auxiliary materials are generally wrapped around the outside of the inner steel pipe of the directly buried prefabricated insulation pipe. The number of wrapping layers depends on the insulation effect to be achieved. In order to reduce heat loss, a reflective layer must be added between each layer of insulation material. The inner pipe mainly uses seamless steel pipe, because the pressure inside the pipe is still relatively large when transporting steam.
It is worth noting that when installing directly buried prefabricated insulated seamless pipes, it is best to bury them in trenches and not to use the method of drawing pipes. Although pulling the pipe saves costs, it can easily cause damage to the insulation pipe during the pulling process. Once damaged, it is difficult to repair it in a short time.
The following are the construction points of directly buried prefabricated insulated seamless pipes
1. Preparation work before construction
(1) Several professional construction personnel, holding professional certificates to work.
(2) Construction materials should comply with relevant construction standards and specifications, and the quality of materials ensures smooth construction.
(3) Conduct an all-round professional and comprehensive inspection of the patching process. Only after all inspections have passed the inspection can the next construction step be entered.
(4) Integrate, analyze, and output the key parameters that affect the quality of the joint, and improve the errors that may occur during the process.
2. Introduction to construction technology
After the pipeline welding link has passed the inspection, the repair work can be carried out without affecting the construction. First determine the basic parameters and construction procedures of the joint to ensure that there will be no problems with the construction quality. The construction process is suitable to be carried out under conditions above 15C and humidity below 85%.
3. Polyethylene casing installation process
Before installation, pay attention to cleaning the soil and debris around the casing to ensure that the bonding joint is clean. Accurate the docking dimensions of the casing and the outer casing. When docking, ensure that the installation is horizontal and centered to ensure the smooth progress of the docking work.
4. Air tightness test and detection process
(1) Drill a hole in the outer tube first, install the pressure gauge vertically on this part, and fix it with bolts.
(2) Turn on the air compressor, raise the pressure to about 0.02Mpa, and use soapy water to check whether there is air leakage.
(3) If there is air leakage, it should be repaired in time, and then the air tightness test should be carried out. Only when there is no problem can polyurethane foaming be carried out.
5. Basic conditions requirements for construction sites
(1) The polyurethane in prefabricated directly buried thermal insulation pipes cannot be soaked in water for a long time. Therefore, a drainage system must be set up during the construction process to ensure smooth pipeline installation.
(2) The drainage process requires specialized personnel to monitor the drainage process to prevent the pipes from being soaked in water and affecting the construction process.
(3) In order to ensure the overall quality of the construction, the construction period should be reasonably arranged and each link clearly marked.
(4) Whether necessary supports should be set up in the operation pit should be determined based on the specific depth, loose soil conditions and groundwater level to ensure the safety of construction workers.