Cold drawn seamless pipe is a subdivision of seamless pipe. Both are weldless steel pipes, which are directly formed through perforation, rolling and other processes. The only difference is the subsequent processing technology. During the machining process, cold drawn seamless pipes need to pay special attention to some processing details due to their unique processing technology and performance characteristics to ensure processing quality and efficiency. The following are 8 key points that need to be paid attention to during machining of cold drawn seamless pipes:
1. Preheating
Before processing, if there is a large deformation or hardened layer on the surface of the cold drawn seamless pipe, it is recommended to perform preheat treatment. The cold drawing process causes plastic deformation of the surface and internal materials of the steel pipe, which may increase the surface hardness of the pipe. At this time, appropriate annealing or preheating treatment is required to reduce tool wear during processing.
Annealing treatment: If the hardness of the steel pipe is high, annealing treatment can be used to soften the material, improve its processability, and prevent cracks or excessive processing resistance during processing.
Preheating: For some harder cold drawn seamless pipes, proper preheating treatment can avoid excessive thermal stress during processing, which may cause the material to crack or deform.
Carbide tools: For the cutting of cold drawn seamless pipes, carbide tools or high-performance coated tools are usually required. These tools have good wear resistance and heat resistance and can better adapt to the high hardness of steel pipes.
Choose the appropriate tool shape: The shape of the tool needs to be selected according to the processing requirements. Avoid choosing tools that are too sharp or too blunt to avoid affecting the processing quality.
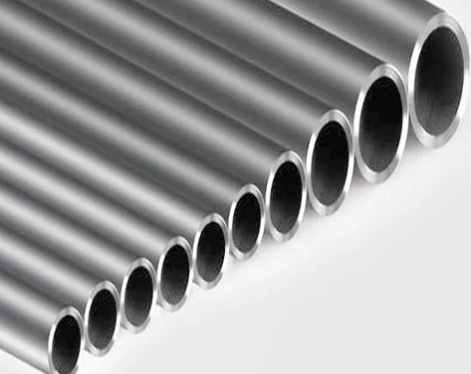
Reasonable cutting speed: It is recommended to adjust the cutting speed according to the material and hardness of the steel pipe. Usually, low cutting speed is suitable for steel pipes with higher hardness.
Appropriate feed speed: The feed speed should be adjusted reasonably according to the processing part and the load of the tool. Excessive feed speed may cause rough surface or poor cutting.
Suitable coolant: Choosing the right coolant helps to maintain a low processing temperature. Water-soluble cutting fluid or emulsion is usually suitable for the processing of cold drawn steel pipes. They can effectively cool the cutting area and reduce thermal stress.
Coolant flow and spray direction: ensure that the coolant can evenly cover the cutting area, maintain a stable temperature in the processing area, and avoid local overheating causing surface defects.
Removing burrs and cleaning the surface: The end face or cutting surface of cold drawn seamless pipes often has burrs, which need to be treated with appropriate mechanical methods (such as polishing, deburring machine) or chemical methods (such as pickling) to ensure the smoothness of the steel pipe surface.
Clean the processing environment regularly: Keep the processing environment clean and avoid unnecessary impurities, which can not only improve the processing accuracy but also extend the service life of the tool.
Dimensional accuracy inspection: Use high-precision measuring tools to regularly check the outer diameter, wall thickness, length and other dimensions of the pipe to ensure that the processing accuracy meets the design requirements.
Dimension correction: If dimensional deviation is found during the processing, it can be corrected by adjusting the processing parameters or taking subsequent process measures.
7. Clamping and supporting of pipes
During the machining process, whether it is turning, milling or drilling, special attention needs to be paid to the clamping and support of the cold drawn seamless pipe. The steel pipe is large in size or may have irregular shapes on the surface. Therefore, it is necessary to avoid deformation of the workpiece due to unstable clamping during processing.
Correctly clamp the workpiece: Use special clamps or flexible clamps to ensure that the steel pipe is stably fixed during processing to avoid deformation caused by unstable clamping during processing.
Support device: For long pipes, support devices are needed to prevent them from bending or deformation, especially when turning or milling, to maintain the straightness and appearance quality of the steel pipe.
Uniform heating and cooling: Avoid sudden heating or cooling to reduce cracks caused by thermal stress. For some materials that are prone to cracking, slow heating and cooling methods are recommended.
Temperature control during the processing: Maintain the stability of the temperature in the processing area to avoid stress concentration, cracks or deformation of the material caused by excessive temperature differences.
Conclusion
In the mechanical processing of cold-drawn seamless steel pipes, it is crucial to correctly select cutting tools, adjust cutting speed, use coolant reasonably, control processing accuracy and ensure clamping stability. Through meticulous process control and appropriate technical measures, the high precision and high quality of the steel pipe can be ensured during the processing, the processing efficiency can be improved, the service life of the tool can be extended, and the final product can be guaranteed to meet the design requirements.
Read more: Cold Drawn Seamless Tube Specificalions
1. Preheating
Before processing, if there is a large deformation or hardened layer on the surface of the cold drawn seamless pipe, it is recommended to perform preheat treatment. The cold drawing process causes plastic deformation of the surface and internal materials of the steel pipe, which may increase the surface hardness of the pipe. At this time, appropriate annealing or preheating treatment is required to reduce tool wear during processing.
Annealing treatment: If the hardness of the steel pipe is high, annealing treatment can be used to soften the material, improve its processability, and prevent cracks or excessive processing resistance during processing.
Preheating: For some harder cold drawn seamless pipes, proper preheating treatment can avoid excessive thermal stress during processing, which may cause the material to crack or deform.
2. Selection of cutting tools
Due to the high hardness and strength of cold drawn seamless pipes, the selection of cutting tools is crucial. The use of unsuitable tools will increase tool wear, reduce processing efficiency, and even damage the workpiece.Carbide tools: For the cutting of cold drawn seamless pipes, carbide tools or high-performance coated tools are usually required. These tools have good wear resistance and heat resistance and can better adapt to the high hardness of steel pipes.
Choose the appropriate tool shape: The shape of the tool needs to be selected according to the processing requirements. Avoid choosing tools that are too sharp or too blunt to avoid affecting the processing quality.
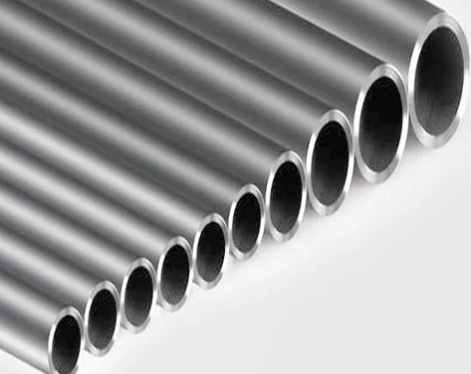
3. Control of cutting speed and feed speed
When processing cold drawn seamless pipes, due to their high hardness and large deformation strength, the reasonable selection of cutting speed and feed speed is very important. If the cutting speed is too fast, it will easily lead to increased tool wear or overheating; If the cutting speed is too slow, the processing efficiency will be low and uneven processing may occur.Reasonable cutting speed: It is recommended to adjust the cutting speed according to the material and hardness of the steel pipe. Usually, low cutting speed is suitable for steel pipes with higher hardness.
Appropriate feed speed: The feed speed should be adjusted reasonably according to the processing part and the load of the tool. Excessive feed speed may cause rough surface or poor cutting.
4. Selection and use of coolant
Coolant is crucial in the machining process, especially when machining cold drawn seamless pipes with higher hardness. Correct use of coolant can not only effectively reduce machining temperature and tool wear, but also improve machining efficiency and surface quality. Suitable coolant: Choosing the right coolant helps to maintain a low processing temperature. Water-soluble cutting fluid or emulsion is usually suitable for the processing of cold drawn steel pipes. They can effectively cool the cutting area and reduce thermal stress.
Coolant flow and spray direction: ensure that the coolant can evenly cover the cutting area, maintain a stable temperature in the processing area, and avoid local overheating causing surface defects.
5. Surface preparation and cleaning
During the mechanical processing of cold drawn seamless pipes, there will often be burrs or other defects on the surface of the steel pipe after cutting, which will affect the accuracy and performance of the pipe. Cleaning the surface residues and burrs is very important to ensure the processing quality.Removing burrs and cleaning the surface: The end face or cutting surface of cold drawn seamless pipes often has burrs, which need to be treated with appropriate mechanical methods (such as polishing, deburring machine) or chemical methods (such as pickling) to ensure the smoothness of the steel pipe surface.
Clean the processing environment regularly: Keep the processing environment clean and avoid unnecessary impurities, which can not only improve the processing accuracy but also extend the service life of the tool.
6. Processing accuracy control
The surface smoothness of cold drawn seamless pipe is relatively high, but due to the plastic deformation during its manufacturing process, there may be certain dimensional tolerances. During processing, special attention should be paid to the size and geometry of the pipe to ensure that the finished product meets the requirements.Dimensional accuracy inspection: Use high-precision measuring tools to regularly check the outer diameter, wall thickness, length and other dimensions of the pipe to ensure that the processing accuracy meets the design requirements.
Dimension correction: If dimensional deviation is found during the processing, it can be corrected by adjusting the processing parameters or taking subsequent process measures.
7. Clamping and supporting of pipes
During the machining process, whether it is turning, milling or drilling, special attention needs to be paid to the clamping and support of the cold drawn seamless pipe. The steel pipe is large in size or may have irregular shapes on the surface. Therefore, it is necessary to avoid deformation of the workpiece due to unstable clamping during processing.
Correctly clamp the workpiece: Use special clamps or flexible clamps to ensure that the steel pipe is stably fixed during processing to avoid deformation caused by unstable clamping during processing.
Support device: For long pipes, support devices are needed to prevent them from bending or deformation, especially when turning or milling, to maintain the straightness and appearance quality of the steel pipe.
8. Avoid cracks or deformation during processing
Cold drawn seamless pipes may crack or deform if not properly controlled during machining, especially when processing high-strength alloy steel pipes.Uniform heating and cooling: Avoid sudden heating or cooling to reduce cracks caused by thermal stress. For some materials that are prone to cracking, slow heating and cooling methods are recommended.
Temperature control during the processing: Maintain the stability of the temperature in the processing area to avoid stress concentration, cracks or deformation of the material caused by excessive temperature differences.
Conclusion
In the mechanical processing of cold-drawn seamless steel pipes, it is crucial to correctly select cutting tools, adjust cutting speed, use coolant reasonably, control processing accuracy and ensure clamping stability. Through meticulous process control and appropriate technical measures, the high precision and high quality of the steel pipe can be ensured during the processing, the processing efficiency can be improved, the service life of the tool can be extended, and the final product can be guaranteed to meet the design requirements.
Read more: Cold Drawn Seamless Tube Specificalions