Submerged arc welding is a welding method in which an arc burns under a layer of flux. Submerged arc welded pipe mainly includes straight seam submerged arc welded pipe (LSAW) and spiral submerged arc welded pipe (SSAW).
1. Undercut
The reason why a single side undercut defect is prone to occur in the submerged arc welded pipe welding process is that the gap between the forming seam changes too much, there are small burrs or small gaps on the edge of the strip, and the forming is wrong. In this case, there is no need to make major adjustments, and the edge of the strip can be processed as smooth as possible and the forming can be kept stable as conditions permit. For the smooth processing of the edge of the strip, the edge milling machine can be used instead of the disc shearing edge to solve it.
In the welding process of submerged arc welded pipes, there will also be a single undercut on both sides. The main reasons for this are uneven wire diameter, rough wire joints, uneven wire feeding caused by uneven wire hardness, and instantaneous short circuit at the nozzle caused by metal burrs. The preventive measures that can be taken in such a situation include: Check the diameter of the welding wire. If the contact tip is a prototype contact tip, the diameter of the contact tip should be appropriately enlarged. The welding wire manufacturer is required to grind the welding wire joint to ensure that the diameter of the joint is consistent and the hardness is consistent. Pay attention to the edge trimming and milling of the board to ensure that there are no burrs, regularly empty the internal flux and perform magnetic screening.
2. The weld reinforcement is too high
The reasons for the excessive weld reinforcement are:
(1) Improper matching of welding specifications, excessive current, low voltage and slow welding speed;
(2) The reclining angle of the welding wire is too large, so that the metal in the molten pool is violently reared;
(3) The distance between the front and back of the welding wire is too small. The wire sticks out too much.
Prevention and control measures include:
(1) Determine reasonable welding specification matching through process test;
(2) Thick-walled steel pipes are welded with open grooves, the extension length of the welding wire is reduced, the spacing of the welding wires is appropriately increased, and the eccentricity of the welding spot is appropriately increased.
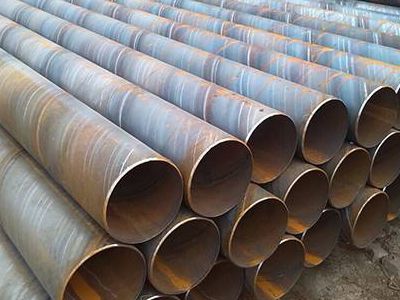
3.Weld pitting and "herringbone" pattern
The causes of weld pitting and "herringbone" pattern are:
(1) The oxidizing atmosphere of welding conditions is too high, that is, the base metal and welding materials have more oil, rust, and oxidized powder, and too many carbon monoxide pores are too late to precipitate, resulting in a large number of pores and surface pitting;
(2) The specificity of the flux is large, the viscosity of the slag is high, the accumulation of the flux is high, or the particle size of the flux is too small, so that the bubble pressure between the metal and the slag is high and pitting occurs.
Prevention and control measures:
(1)Choose sintered flux with light specific gravity and low viscosity, ensure that the flux is dried and cleaned before use, and reduce the accumulation height of flux as much as possible under the premise of unknown arc during use;
(2)Thoroughly remove oil, rust and water on the surface of weldment and welding wire.
4. Weld bias current
Improper solder joint position, too large or too small solder joint off-center or too fast welding speed, incorrect flux feeding position, asymmetric pressure of flux on molten pool, excessive arc voltage will cause weld bias.
Its prevention and control measures mainly include:
(1) Reasonably select the position of the solder joint according to the size of the pipe diameter and the welding specification, and make the molten pool close to the horizontal position to complete the crystallization process as much as possible;
(2) Send the flux in the correct way to reduce the impact of the flux on the molten pool during the flux delivery process. The flux bowl should preferably be made into a shape with a large top and a small bottom to minimize the flow of flux in the front of the molten pool in the flux bowl
(3) Adjust the appropriate arc voltage
5. The transition between the weld and the base metal is not smooth
During welding, the transition angle between the weld and the base metal is generally required to be greater than 110", but the angle is often biased.
Prevention and control measures mainly include:
(1) The thick-walled pipe should increase the breach angle appropriately. Under the condition of ensuring the amount of coincidence, reduce the current of the front wire, increase the voltage of the rear wire, reduce the eccentricity of the welding wire, increase the forward angle of the front wire, and reduce the backward angle of the rear wire.
(2) Reduce the extension length of the welding wire, and make the flux bowl longer, so that the flux enters through the steel pipe and the flux bowl from the direction before welding, so that the flux pushes the liquefied metal to move to the direction after welding. Control the torn mouth and wrong side of the forming seam, and increase the welding wire spacing appropriately.
1. Undercut
The reason why a single side undercut defect is prone to occur in the submerged arc welded pipe welding process is that the gap between the forming seam changes too much, there are small burrs or small gaps on the edge of the strip, and the forming is wrong. In this case, there is no need to make major adjustments, and the edge of the strip can be processed as smooth as possible and the forming can be kept stable as conditions permit. For the smooth processing of the edge of the strip, the edge milling machine can be used instead of the disc shearing edge to solve it.
In the welding process of submerged arc welded pipes, there will also be a single undercut on both sides. The main reasons for this are uneven wire diameter, rough wire joints, uneven wire feeding caused by uneven wire hardness, and instantaneous short circuit at the nozzle caused by metal burrs. The preventive measures that can be taken in such a situation include: Check the diameter of the welding wire. If the contact tip is a prototype contact tip, the diameter of the contact tip should be appropriately enlarged. The welding wire manufacturer is required to grind the welding wire joint to ensure that the diameter of the joint is consistent and the hardness is consistent. Pay attention to the edge trimming and milling of the board to ensure that there are no burrs, regularly empty the internal flux and perform magnetic screening.
2. The weld reinforcement is too high
The reasons for the excessive weld reinforcement are:
(1) Improper matching of welding specifications, excessive current, low voltage and slow welding speed;
(2) The reclining angle of the welding wire is too large, so that the metal in the molten pool is violently reared;
(3) The distance between the front and back of the welding wire is too small. The wire sticks out too much.
Prevention and control measures include:
(1) Determine reasonable welding specification matching through process test;
(2) Thick-walled steel pipes are welded with open grooves, the extension length of the welding wire is reduced, the spacing of the welding wires is appropriately increased, and the eccentricity of the welding spot is appropriately increased.
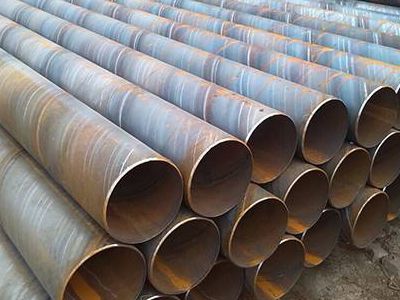
3.Weld pitting and "herringbone" pattern
The causes of weld pitting and "herringbone" pattern are:
(1) The oxidizing atmosphere of welding conditions is too high, that is, the base metal and welding materials have more oil, rust, and oxidized powder, and too many carbon monoxide pores are too late to precipitate, resulting in a large number of pores and surface pitting;
(2) The specificity of the flux is large, the viscosity of the slag is high, the accumulation of the flux is high, or the particle size of the flux is too small, so that the bubble pressure between the metal and the slag is high and pitting occurs.
Prevention and control measures:
(1)Choose sintered flux with light specific gravity and low viscosity, ensure that the flux is dried and cleaned before use, and reduce the accumulation height of flux as much as possible under the premise of unknown arc during use;
(2)Thoroughly remove oil, rust and water on the surface of weldment and welding wire.
4. Weld bias current
Improper solder joint position, too large or too small solder joint off-center or too fast welding speed, incorrect flux feeding position, asymmetric pressure of flux on molten pool, excessive arc voltage will cause weld bias.
Its prevention and control measures mainly include:
(1) Reasonably select the position of the solder joint according to the size of the pipe diameter and the welding specification, and make the molten pool close to the horizontal position to complete the crystallization process as much as possible;
(2) Send the flux in the correct way to reduce the impact of the flux on the molten pool during the flux delivery process. The flux bowl should preferably be made into a shape with a large top and a small bottom to minimize the flow of flux in the front of the molten pool in the flux bowl
(3) Adjust the appropriate arc voltage
5. The transition between the weld and the base metal is not smooth
During welding, the transition angle between the weld and the base metal is generally required to be greater than 110", but the angle is often biased.
Prevention and control measures mainly include:
(1) The thick-walled pipe should increase the breach angle appropriately. Under the condition of ensuring the amount of coincidence, reduce the current of the front wire, increase the voltage of the rear wire, reduce the eccentricity of the welding wire, increase the forward angle of the front wire, and reduce the backward angle of the rear wire.
(2) Reduce the extension length of the welding wire, and make the flux bowl longer, so that the flux enters through the steel pipe and the flux bowl from the direction before welding, so that the flux pushes the liquefied metal to move to the direction after welding. Control the torn mouth and wrong side of the forming seam, and increase the welding wire spacing appropriately.