Different definitions
1. Manual arc welding
Manual arc welding, for short, is a welding method that uses a manually operated welding rod and the workpiece to be welded as two electrodes, and uses the arc heat between the welding rod and the welding piece to melt the metal.
2. Submerged arc automatic welding
Submerged arc welding, referred to as submerged arc welding, is an arc welding method in which the arc burns under the flux layer, the arc is automatically ignited and controlled mechanically, and the feeding of the welding wire and arc movement are automatically completed. Common submerged arc welded steel tubes include spiral submerged arc welded steel tube (SSAW steel tube) and longitudinal double submerged arc welding steel tube (LASW steel tube)
Different characteristics
1. Manual arc welding
①The equipment is simple.
②Flexible and convenient operation.
③Can perform all-position welding and is suitable for welding a variety of materials.
④The disadvantages are low production efficiency and high labor intensity.
2. Submerged arc automatic welding
①High productivity.
②High quality and beautiful welding seams.
③Improving working conditions. The mechanized operation of the welding process is more convenient, with less smoke and dust, and no arc radiation.
Welding electricity protection measures
1. Before welding work, check whether the welding machine equipment and tools are safe and reliable. For example, whether the shell of the welding machine is grounded, whether the connection points of the welding machine are in good contact, whether the insulation of the welding cable is damaged, etc. It is not allowed to start operations without carrying out safety checks.
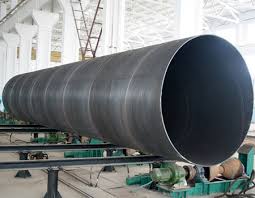
2. The welder's hands and body are not allowed to touch the conductors of the secondary circuit casually, and they are not allowed to rely on the workbench, welding parts, or come into contact with electrified objects such as welding clamps. For welding operations where the no-load voltage of the welding machine is high, and when operating in humid working locations, rubber insulating mats should also be laid on the ground near the operating platform.
3. The following operations should be performed after cutting off the power switch: moving the working location, moving the welding machine; replacing fuses; repairing the welding machine when it fails; changing the welding machine joints; changing the welding parts and modifying the layout of the secondary circuit, etc. When pushing and pulling the switch, insulating gloves must be worn; at the same time, the welder's head should be tilted to prevent arc sparks from burning the face.
4. When welding in metal containers, on metal structures, and other small workplaces, the risk of electric shock is greatest, and special protective measures must be taken. For example, use rubber mats, wear leather gloves, and wear insulated shoes.
5. Welding operators are not allowed to use themselves or the transmission parts of machinery and equipment as welding circuits under any circumstances, and it is strictly prohibited to use the metal structure of the factory, rails (pipes) and other access lines as conductors.
6. The grounding protection device of the welding machine must be complete and effective. At the same time, the welding machine must be equipped with a no-load automatic power-off protection device.
7. There should be no joints in the middle of the welding cable. If it is necessary to use short wires to extend the length, there should be no more than 2 joints. The joints should be made of copper material and ensure good insulation.
8. Strengthen personal protection. Personal protective equipment for welders includes intact work clothes, insulating gloves, overshoes, etc.
9. The installation, inspection and repair of electric welding equipment must be carried out by electricians, and temporary construction sites should be connected to the power supply by electricians.
1. Manual arc welding
Manual arc welding, for short, is a welding method that uses a manually operated welding rod and the workpiece to be welded as two electrodes, and uses the arc heat between the welding rod and the welding piece to melt the metal.
2. Submerged arc automatic welding
Submerged arc welding, referred to as submerged arc welding, is an arc welding method in which the arc burns under the flux layer, the arc is automatically ignited and controlled mechanically, and the feeding of the welding wire and arc movement are automatically completed. Common submerged arc welded steel tubes include spiral submerged arc welded steel tube (SSAW steel tube) and longitudinal double submerged arc welding steel tube (LASW steel tube)
Different characteristics
1. Manual arc welding
①The equipment is simple.
②Flexible and convenient operation.
③Can perform all-position welding and is suitable for welding a variety of materials.
④The disadvantages are low production efficiency and high labor intensity.
2. Submerged arc automatic welding
①High productivity.
②High quality and beautiful welding seams.
③Improving working conditions. The mechanized operation of the welding process is more convenient, with less smoke and dust, and no arc radiation.
Welding electricity protection measures
1. Before welding work, check whether the welding machine equipment and tools are safe and reliable. For example, whether the shell of the welding machine is grounded, whether the connection points of the welding machine are in good contact, whether the insulation of the welding cable is damaged, etc. It is not allowed to start operations without carrying out safety checks.
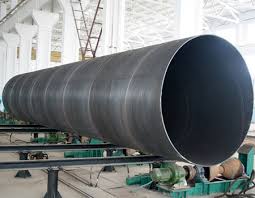
2. The welder's hands and body are not allowed to touch the conductors of the secondary circuit casually, and they are not allowed to rely on the workbench, welding parts, or come into contact with electrified objects such as welding clamps. For welding operations where the no-load voltage of the welding machine is high, and when operating in humid working locations, rubber insulating mats should also be laid on the ground near the operating platform.
3. The following operations should be performed after cutting off the power switch: moving the working location, moving the welding machine; replacing fuses; repairing the welding machine when it fails; changing the welding machine joints; changing the welding parts and modifying the layout of the secondary circuit, etc. When pushing and pulling the switch, insulating gloves must be worn; at the same time, the welder's head should be tilted to prevent arc sparks from burning the face.
4. When welding in metal containers, on metal structures, and other small workplaces, the risk of electric shock is greatest, and special protective measures must be taken. For example, use rubber mats, wear leather gloves, and wear insulated shoes.
5. Welding operators are not allowed to use themselves or the transmission parts of machinery and equipment as welding circuits under any circumstances, and it is strictly prohibited to use the metal structure of the factory, rails (pipes) and other access lines as conductors.
6. The grounding protection device of the welding machine must be complete and effective. At the same time, the welding machine must be equipped with a no-load automatic power-off protection device.
7. There should be no joints in the middle of the welding cable. If it is necessary to use short wires to extend the length, there should be no more than 2 joints. The joints should be made of copper material and ensure good insulation.
8. Strengthen personal protection. Personal protective equipment for welders includes intact work clothes, insulating gloves, overshoes, etc.
9. The installation, inspection and repair of electric welding equipment must be carried out by electricians, and temporary construction sites should be connected to the power supply by electricians.