The manufacturing process of casing pipes involves several steps and specialized techniques to produce high-quality, durable pipes suitable for a wide range of applications. Casing pipes are commonly used in oil and gas exploration, water wells, underground utility installations, and geotechnical drilling. The following comprehensive overview outlines the key stages involved in the manufacturing process of casing pipes.
1. Raw Material Selection:
The first step in manufacturing casing pipes is the careful selection of raw materials. Casing pipes are often constructed from various grades of steel, such as carbon steel, alloy steel, or stainless steel, depending on the specific requirements of the application. The selected steel should meet industry standards for strength, corrosion resistance, and weldability.
2. Pipe Forming
a. Seamless Pipe Production
For seamless casing pipes, the manufacturing process begins with the production of seamless tubes. This process involves piercing a solid steel billet to create a hollow shell, followed by hot rolling and/or cold drawing to achieve the desired dimensions and mechanical properties. Seamless pipes offer high tensile strength and uniform wall thickness, making them ideal for high-pressure and critical applications.
b. Welded Pipe Production
Welded casing pipes are manufactured through the welding of steel strips or plates to form a continuous pipe. The raw steel material is formed into a cylindrical shape and then longitudinally welded using various welding methods such as electric resistance welding (ERW), submerged arc welding (SAW), or high-frequency induction welding (HFI). Welded casing pipes offer cost-effective solutions for various casing and tubing applications.
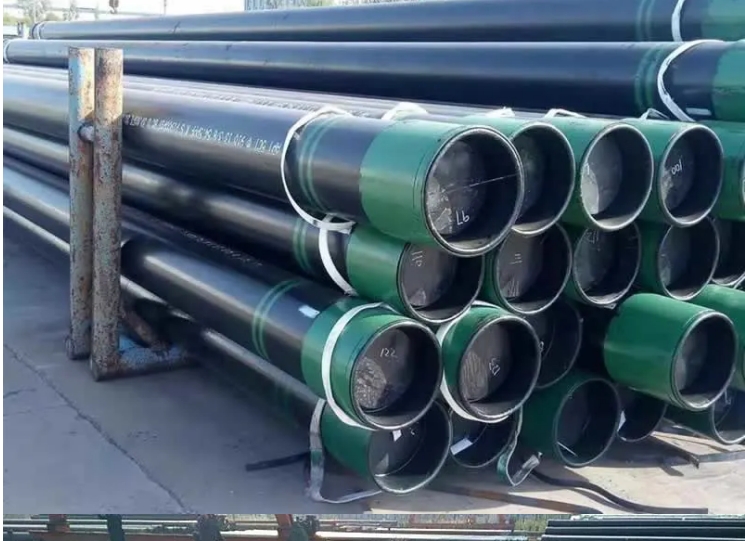
3. Heat Treatment and Conditioning
After the initial forming process, both seamless and welded casing pipes undergo heat treatment to optimize their mechanical properties. Heat treatment methods may include normalizing, quenching and tempering, or stress relieving, depending on the specific steel grade and application requirements. Heat treatment enhances the pipe's hardness, strength, and resistance to deformation, ensuring superior performance under demanding operating conditions.
4. Pipe Sizing and Dimensional Control
Once the pipes have been formed and heat-treated, they undergo precision sizing and dimensional control processes to meet the required specifications. These processes may involve cold sizing, stretching, or straightening to achieve precise outer diameters, wall thicknesses, and lengths. Stringent quality control measures are implemented to ensure dimensional accuracy and compliance with industry standards.
5. Thread Cutting and Connection Installation
Casing pipes intended for well drilling applications require threaded connections to facilitate assembly and installation. Threads are precision-cut onto the pipe ends using specialized threading machines and cutting tools. The threads are then inspected to ensure proper fit and conformance to API or other relevant standards. In some cases, premium connections with enhanced sealing and torque capabilities may be installed to meet specific operational requirements.
6. Surface Treatment and Coating Application
To enhance the longevity and corrosion resistance of casing pipes, various surface treatments and coatings may be applied. Common surface treatments include shot blasting to remove surface oxides and contaminants, while coatings such as epoxy, polyethylene, or zinc-based compounds may be applied to provide additional protection against corrosion in aggressive environments.
7. Quality Inspection and Testing
Quality assurance is a critical aspect of casing pipe manufacturing. Comprehensive inspection and testing procedures are conducted to verify the integrity, mechanical properties, and dimensional accuracy of the finished pipes. Non-destructive testing methods such as ultrasonic testing, magnetic particle inspection, and visual examination are employed to detect defects, ensure weld integrity, and confirm compliance with industry standards.
8. Storage, Packaging, and Transportation
Once the casing pipes have passed rigorous quality inspections, they are carefully stored, packaged, and prepared for transportation to their intended destinations. Protective measures such as end caps, rust inhibitors, and packaging materials are applied to safeguard the pipes during transit and storage, ensuring that they arrive at their final destination in optimal condition.
In conclusion, the manufacturing process of casing pipes encompasses multiple stages, including raw material selection, pipe forming, heat treatment, dimensional control, thread cutting, coating application, quality inspection, and packaging. Each stage is crucial in ensuring the production of high-quality casing pipes that meet the stringent requirements of diverse industries, ranging from oil and gas exploration to water well construction.
1. Raw Material Selection:
The first step in manufacturing casing pipes is the careful selection of raw materials. Casing pipes are often constructed from various grades of steel, such as carbon steel, alloy steel, or stainless steel, depending on the specific requirements of the application. The selected steel should meet industry standards for strength, corrosion resistance, and weldability.
2. Pipe Forming
a. Seamless Pipe Production
For seamless casing pipes, the manufacturing process begins with the production of seamless tubes. This process involves piercing a solid steel billet to create a hollow shell, followed by hot rolling and/or cold drawing to achieve the desired dimensions and mechanical properties. Seamless pipes offer high tensile strength and uniform wall thickness, making them ideal for high-pressure and critical applications.
b. Welded Pipe Production
Welded casing pipes are manufactured through the welding of steel strips or plates to form a continuous pipe. The raw steel material is formed into a cylindrical shape and then longitudinally welded using various welding methods such as electric resistance welding (ERW), submerged arc welding (SAW), or high-frequency induction welding (HFI). Welded casing pipes offer cost-effective solutions for various casing and tubing applications.
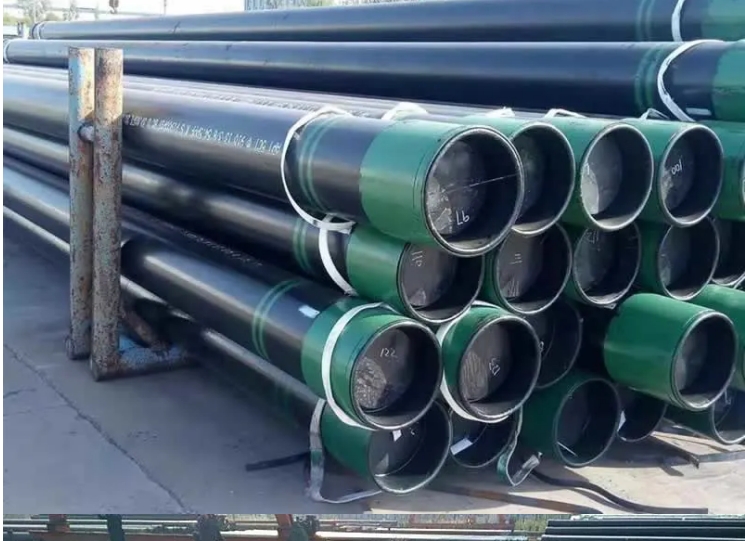
3. Heat Treatment and Conditioning
After the initial forming process, both seamless and welded casing pipes undergo heat treatment to optimize their mechanical properties. Heat treatment methods may include normalizing, quenching and tempering, or stress relieving, depending on the specific steel grade and application requirements. Heat treatment enhances the pipe's hardness, strength, and resistance to deformation, ensuring superior performance under demanding operating conditions.
4. Pipe Sizing and Dimensional Control
Once the pipes have been formed and heat-treated, they undergo precision sizing and dimensional control processes to meet the required specifications. These processes may involve cold sizing, stretching, or straightening to achieve precise outer diameters, wall thicknesses, and lengths. Stringent quality control measures are implemented to ensure dimensional accuracy and compliance with industry standards.
5. Thread Cutting and Connection Installation
Casing pipes intended for well drilling applications require threaded connections to facilitate assembly and installation. Threads are precision-cut onto the pipe ends using specialized threading machines and cutting tools. The threads are then inspected to ensure proper fit and conformance to API or other relevant standards. In some cases, premium connections with enhanced sealing and torque capabilities may be installed to meet specific operational requirements.
6. Surface Treatment and Coating Application
To enhance the longevity and corrosion resistance of casing pipes, various surface treatments and coatings may be applied. Common surface treatments include shot blasting to remove surface oxides and contaminants, while coatings such as epoxy, polyethylene, or zinc-based compounds may be applied to provide additional protection against corrosion in aggressive environments.
7. Quality Inspection and Testing
Quality assurance is a critical aspect of casing pipe manufacturing. Comprehensive inspection and testing procedures are conducted to verify the integrity, mechanical properties, and dimensional accuracy of the finished pipes. Non-destructive testing methods such as ultrasonic testing, magnetic particle inspection, and visual examination are employed to detect defects, ensure weld integrity, and confirm compliance with industry standards.
8. Storage, Packaging, and Transportation
Once the casing pipes have passed rigorous quality inspections, they are carefully stored, packaged, and prepared for transportation to their intended destinations. Protective measures such as end caps, rust inhibitors, and packaging materials are applied to safeguard the pipes during transit and storage, ensuring that they arrive at their final destination in optimal condition.
In conclusion, the manufacturing process of casing pipes encompasses multiple stages, including raw material selection, pipe forming, heat treatment, dimensional control, thread cutting, coating application, quality inspection, and packaging. Each stage is crucial in ensuring the production of high-quality casing pipes that meet the stringent requirements of diverse industries, ranging from oil and gas exploration to water well construction.